High-Pressure Cleaning
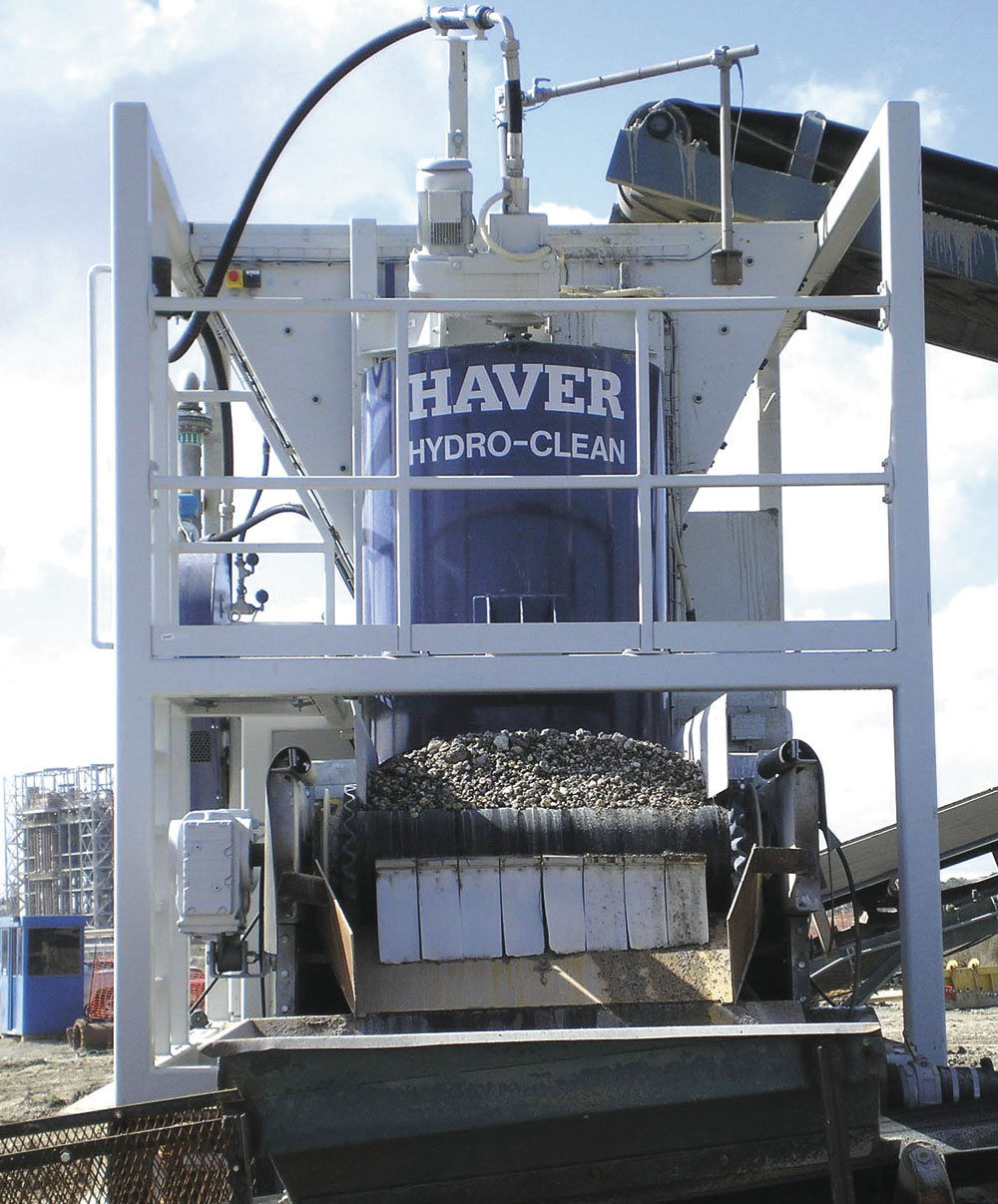
New Hydro-Clean removes contamination with up to 75% less water than standard washing equipment
The new Hydro-Clean washing unit from Ontario-based W.S. Tyler, a member of the Germany-based Haver Screening Group, is said to effectively clean deleterious material from aggregate, industrial minerals and metals while reducing water consumption by up to 75% compared with traditional log-washers.
Accepting a maximum feed material size of up to 6in (150mm) into its vertical drum, the Hydro-Clean employs high-pressure nozzles, rotating at 90 rev/min, to spray up to 90% recycled water on the material at pressures up to 2,900 psi (200 bars). The washing unit removes silt and clay particles as small as 63 microns from mineral mixtures and, with its short retention times, can process up to 400 tonnes/h, depending on the model size and application.
Owing to its compact size and weight, overall operating and structural costs are considerably lower than with traditional washing systems – which also require more equipment and a greater footprint. A traditional washing system can require up to three screens, together with a log-washer or screw. With a Hydro-Clean unit, the producer only needs an additional wash screen for the Hydro-Clean’s discharged material.
The Hydro-Clean is particularly suitable for use in clay-heavy material deposits. The dirty material is fed, via hopper, to a vertical washing drum, where high-pressure nozzles mounted at the top rotate and spray the material with water. The high-pressure water streams spread and wash the material, effectively interacting with it to break up agglomerates and clean the particles of stubborn material. The turbulence within the drum creates additional scrubbing and abrasive forces that enhance the cleaning process as the material travels down the drum cylinder.
Because high-pressure streams of water are injected into areas of the rock (holes, cracks etc) that are difficult to reach with traditional cleaning methods, such as log-washers or screws, the end result is a cleaner product that generates higher selling value. In addition, many producers use this unit to turn material that was once dirty waste into revenue.
During the cleaning process, the washed material works its way down the drum and exits on to a discharge conveyor that leads to a standard wash screen, which removes any remaining dirt or clay still on the stone as it fractionates the material. The resulting dirty water flows through polyurethane screen mesh installed in the sides of the washing drum and is collected by a waste water pipe, which delivers the water to a treatment system for additional fine screening.
The Hydro-Clean consumes little water and power. Water consumption ranges from 27 to 211 gal/min, depending on application and model size, compared with log-washers that can require up to 800 gal/min of water. Power requirements for the Hydro-Clean are no higher than 300hp (225kW) on the largest model. When compared with conventional systems, the Hydro-Clean experiences little wear and features a maintenance-friendly design that allows for easy exchange of the few standard components that are subject to wear.
Moreover, the distance between the washing rotor and the material bed in the Hydro-Clean is variable and allows the system to adapt to various material types. Level sensors located at the material feed inlet provide exact data to the PLC control unit, ensuring a consistent material flow into the system. The Hydro-Clean is available in four model sizes that can produce from 20 to 400 tonnes/h, depending on the application.
For more information visit www.wstyler.ca