Hazemag VARIOwobbler impresses in France
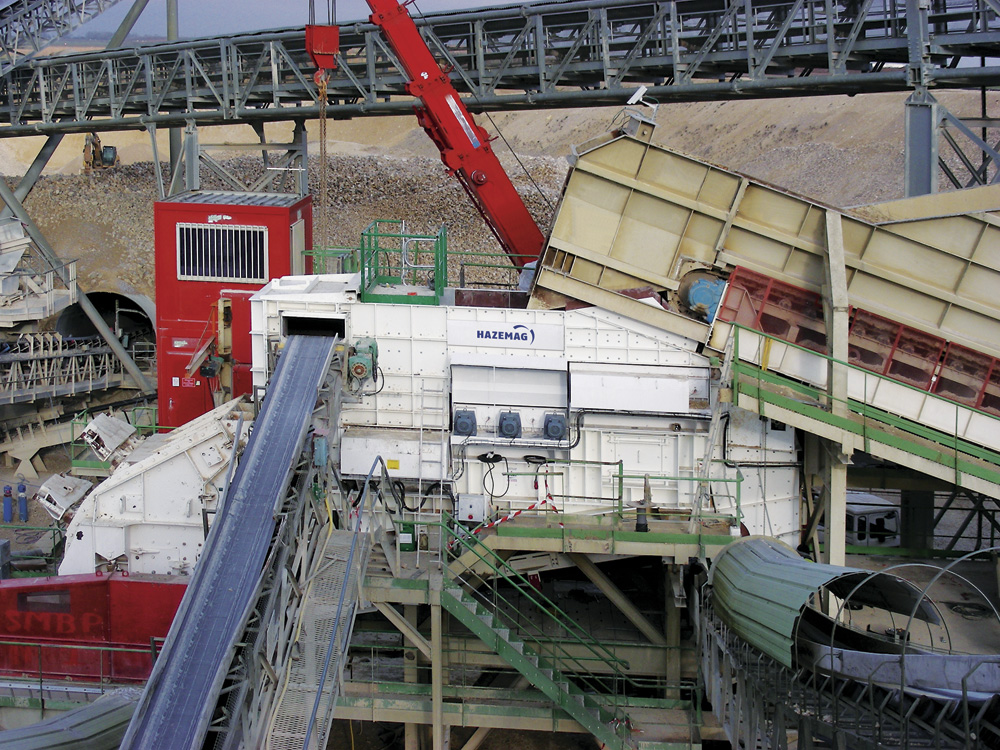
SMBP invest in VARIOwobbler roller screen to improve production at their limestone quarry near Chatres
A key feature of the three-stage VARIOwobbler installed at SMBP’s limestone quarry in Prasville, near Chatres, is that it can vary the granular size of screened product at the touch of a button. As a consequence, the plant operator is able to achieve a consistent quality of screened feed to the crusher, despite changes in the characteristics and properties of the initial feed material. The end result is a significant increase in process plant performance, with production levels now reaching 7,000 tonnes per day as opposed to the previous 5,000 tonnes. Further significant benefits include reduced wear in the downstream impact crusher and reduced water usage in the washing process.
Owing to seasonal climatic fluctuations in the region, the characteristics of the quarried limestone vary greatly; from dry in summer to very moist and sticky in winter. Pre-crushed material 0–300mm in size, as well as uncrushed material 0–2,000mm in size, is fed to the crushing plant. A high clay-loam content of 10–12% (with peaks up to 40%) and a high level of clay-content fines is also prevalent, particularly in the winter. This had created major problems with operation of the vibrating screen previously employed for pre-screening. Severe clogging occurred on a regular basis and a mini-excavator had to be used to clear the screen. This, in turn, caused contamination of the finished product and significantly affected system performance, reducing output to 300 tonnes/h.
Christian Laye, head of SMBP, said: ’The situation had become totally unacceptable and so we decided to replace the existing vibrating feeder with a new Hazemag VARIOwobbler roller screen.’
Hazemag engineers designed the VARIOwobbler as a three-stage system in order to bridge the vertical space previously occupied by the vibrating screen, and to fit exactly between the apron feeder and the impact crusher. The system design also provides the advantage of turning the material at each stage, resulting in improved screening and cleaner crusher feed.
The screening surface of the VARIOwobbler consists of a series of rotating shafts fitted with special triple triangular disks. Material is conveyed horizontally and fines pass between the shafts. The hydro-mechanical control system allows the gap between individual shafts to be infinitely varied at the touch of a button. At SMBP, the separation distance in the first two stages is constantly fixed at 80mm, but in the third stage the gap can be adjusted between 80mm and 120mm.
The overall objective of the screening process at SMBP is to provide a consistent quality and flow of feed material to the crusher, with acceptable levels of loam and clay content, while achieving trouble-free operation and reduced wear rates in the impact crusher. The flexibility provided by the VARIOwobbler means that these objectives can be met whatever the climatic conditions.
In the summer, when the material is clean and dry, all three stages are operated with the minimum gap setting of 80mm. This means that only a relatively small amount of material requires washing – saving considerably on water usage. In the winter, when the material is wet and sticky, with extensive adhering contamination, the separation distance on the third stage is adjusted to 100mm or, if necessary, 120mm. Although this results in more material being sent to the washing system, it is less than was formerly the case with the vibrating screen, which had a 150mm mesh. According to SMBP, the improvement in quality and consistency of feed to the impact crusher is in marked contrast to that previously achieved using the vibrating screen. Also, the problems of contaminated feed, such as loam and clay entering the crusher, caused by frequent un-clogging of the screen by the mini-excavator, have now been totally eradicated.
The effectiveness of the VARIOwobbler was clearly demonstrated during commissioning, which was carried out in severe winter conditions. It snowed during this period and the feed material, which had already been stored for a significant time in the bunker, was especially sticky. Christian Laye was very anxious to see how the VARIOwobbler would function under these conditions. In the event, the machine did not clog and its trouble-free operation proved that he had made a sound decision. And with plant performance now reaching 600–800 tonnes/h, SMBP say they are looking forward to a rapid return on their investment.
For further information visit: www.hazemaguk.com