Hazemag at Stancombe Quarry
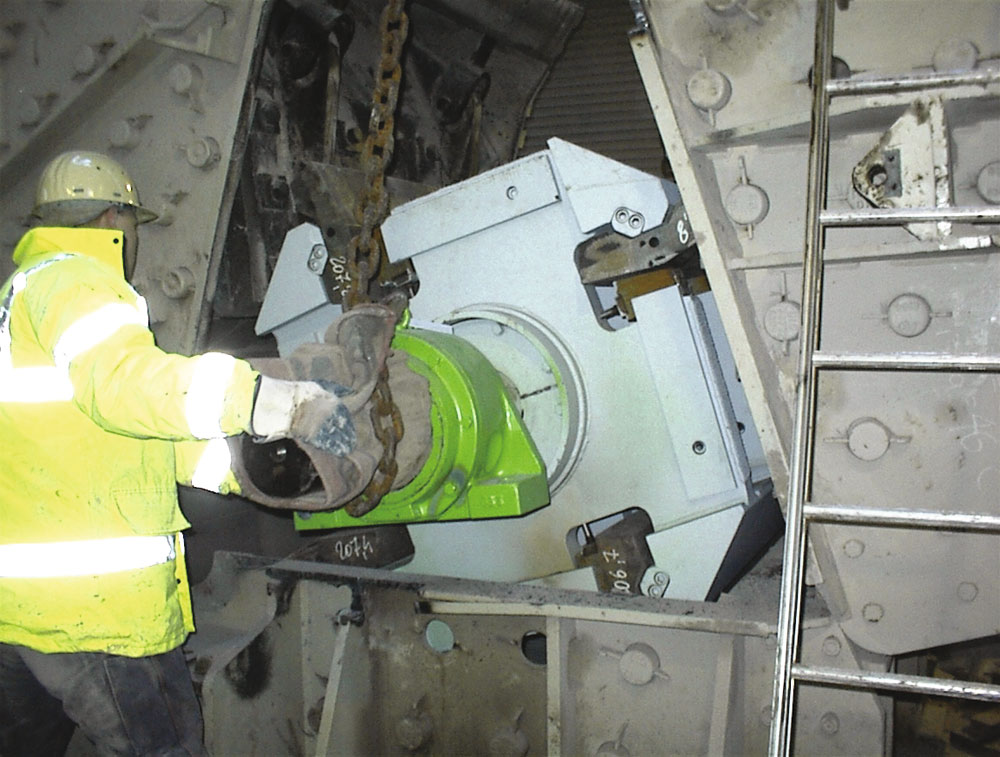
New Hazemag SQ-type secondary rotor improves product shape and comminution efficiency with less wear
By Stefan Koch, Hazemag & EPR GmbH
For the past two years Tarmac Southern Ltd’s Stancombe Quarry, near Bristol, has operated a Hazemag AP5 BR primary impact crusher fitted with a relatively new rotor design — the GSK-type rotor. Using this new rotor, which features special blow-bar geometry, the life of the blow-bars has been increased by around 20% compared with conventional S-type blow-bars.
As a result of this and other successful operations involving the GSK-type rotor, Hazemag decided to utilize their experience and knowledge of rotors of all types to introduce a completely new design of rotor for secondary crushing applications, the result being the SQ-type rotor.
In January 2003 the rotor on Stancombe’s secondary impactor, a Hazemag AP-K 1615, was replaced with the newly developed SQ-type model (figs 1& 2). This machine processes the primary crushed material (after it has passed through a screening unit), reducing it from –200mm+40mm to less than 40mm in a closed-circuit arrangement at a rate of up to 250 tonnes/h.
Rotor design
The rotor is the most severely-tested component of any impact crusher and plays a vital role in the comminution process. Consequently, throughout their near 60 years of business, Hazemag have striven to optimize the design and development of their rotors to suit all possible applications. The new SQ-type rotor, which is the result of this experience and knowledge, features blow bars that combine the comminution advantages of S-type blow-bars with the benefits of Q-type blow-bars, in terms of their degree of utilization; the blow-bars can be turned once, whereby an overall utilization rate of more than 50% can be achieved.
As with almost all secondary rotors, the new SQ-rotor is an open-disc type, with the rear retaining beam mounted in appropriate recesses. The blow-bars are tightly fixed in position using the well-proven wedge-type retainers of the Hazemag QB-type (rubble crusher) rotor. This securing method permits use with blow-bars of various material qualities, making the SQ-type rotor well suited to a wide range of secondary comminution applications, including hard rock crushing. Attached to the sides of the rotor discs are reversible and replaceable protective wear plates that also serve as retaining wedge guides. Depending on the crusher model selected, the blow-bars can be extracted laterally either by means of the wedges or over the retaining beams; this is achieved by dismantling the side locking device and loosening the retaining wedges.
In conjunction with the introduction of the new rotors at Stancombe, an inspection contract covering the Hazemag impactors was agreed with Tarmac. This provides for the periodic examination of the machines based on the prevailing operating conditions. According to Hazemag, preventive and necessary maintenance carried out by trained specialists militates against the development of any potentially serious problems, while early recognition of any problems that do arise ensures that downtime and production shortfalls are kept to a minimum and allows servicing and maintenance schedules to be drawn up well in advance.
Results
During the latest inspection of the impactors at Stancombe in September 2003, Stefan Koch and Graham Mansfield of Hazemag & EPR GmbH and Hazemag UK Ltd, respectively, examined the condition of the new SQ-type rotor and looked at the results achieved (figs 3&4). With the ‘old’ rotor the blow-bars had to be turned after approximately 350,000 tonnes (ie around 700,000 tonnes per set of blow-bars), however, at the time of the inspection, some 205,000 tonnes of material had already been processed using the new rotor without any noticeable wear.
Up to now the new rotor has fulfilled all the demands placed on it and has even exceeded expectations in certain respects. According to Stancombe Quarry’s unit manager, Paul O’Neill, and workshop manger, Peter Hicks, since the new rotor was installed the proportion of oversize generated has been reduced by half and at the same time the shape of the product has visibly improved.
In addition, the blow-bar wear rate determined so far suggests that the life of the blow-bars has been tripled (although a doubling of the blow-bar life had already been anticipated, as the weight of the new set of blow-bars is twice that of the old set). Moreover, not only was there little sign of wear to the rotor body, but impact plate wear had also clearly been reduced.
Hazemag say the use of original spare parts has contributed greatly to these results, but add that the service life of such components is just one consideration; the choice of material and the component configuration are also greatly influenced by machine utilization and the operating conditions as part of an integrated unit. Awareness of the correlation between machine availability and the utilization of original replacement parts is of key importance in this respect, Hazemag say.
This new-generation rotor improves both the shape of the product and the comminution efficiency of the crusher and at the same time reduces wear rates and optimizes maintenance requirements. According to Hazemag, the deployment of the first SQ-type rotor has demonstrated its potential and underlined its competitive advantages.