Eagle Iron Works Wash Plant for US Sand and Gravel Operator
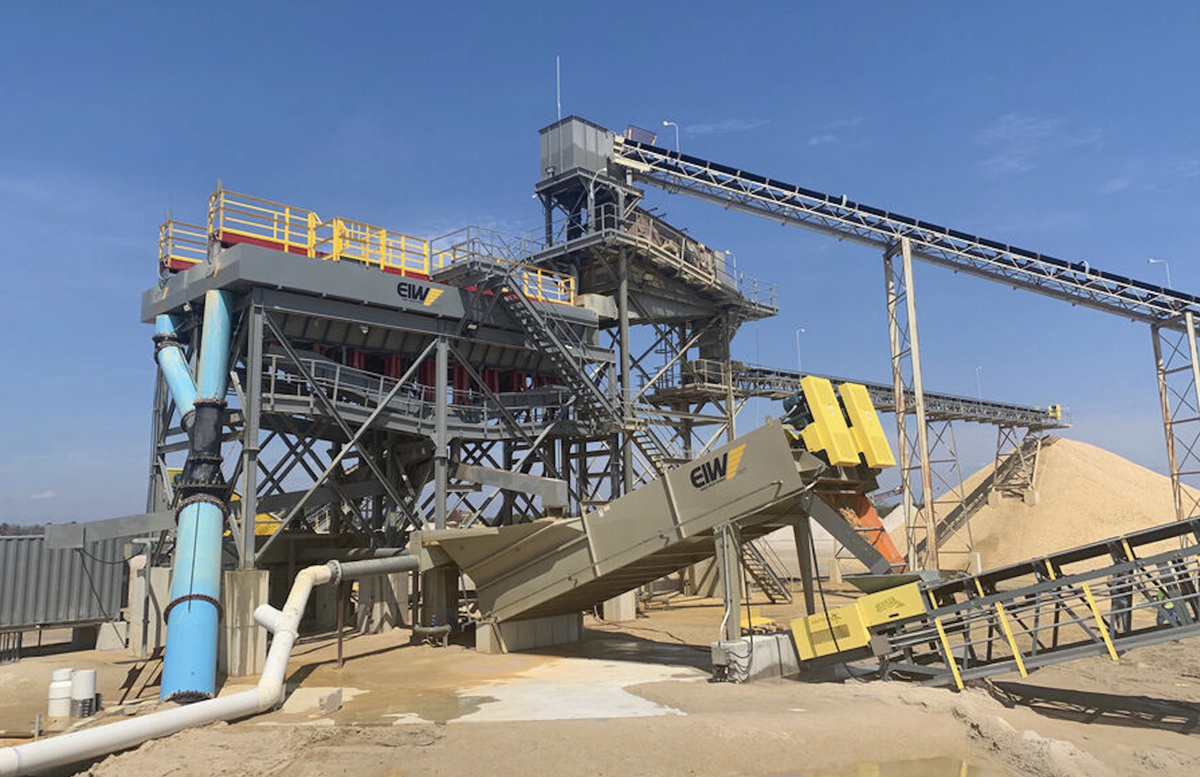
First published in the August 2020 issue of Quarry Management as Tuckahoe Achieve their Goal
New Jersey sand and gravel operator triples production with new Eagle Iron Works wash plant
At their location in southern New Jersey, Tuckahoe Sand and Gravel produce numerous aggregate materials, including concrete sand, various types of golf course sand, and gravels used for drainage and landscaping. Known up and down the US East Coast for their quality and consistency, sand and gravel products produced at Tuckahoe are used in Department of Transportation projects, on construction and residential job sites, and at numerous golf courses.
Because the sand and gravel market is so competitive, Tuckahoe need to produce high-quality material at prices their customers can afford, and in order to accomplish these goals, they have to make as much material as they can, as fast as they can. However, with two small, aging plants, they were not able to meet the required productivity goals and sales were suffering as a result.
‘Production was the problem,’ said Tuckahoe plant manager Ron Sutton Jr. ‘We just weren’t able to increase inventory and maintain production to supply our customers.’
Tuckahoe did not have belt scales on their old plant, but Mr Sutton estimated production was less than 100 tons/h at times. ‘The writing was on the wall that we had to increase our production,’ he explained. ‘We proved the sales were there to support the purchase of a new dredge and a new plant.’
Familiarity with Eagle Iron Works (EIW) equipment and support from their local dealer, Dibble Equipment, influenced Tuckahoe’s decision to upgrade their old wash plant with new equipment from EIW.
‘My employees are familiar with Eagle products, so there was no learning curve,’ explained Mr Sutton. ‘They knew how to maintain the Eagle product and, in my tenure here at Tuckahoe, we’ve always been satisfied in the quality and reliability of the Eagle product.’
Tuckahoe’s new wash plant includes two 10ft x 40ft EIW classifying tanks, for separating and blending pre-screened material into three different products, and two 54in x 34in double-screw fine material washers for washing, classifying and dewatering those products before stockpiling.
EIW classifying tanks are well suited to dredge operations like Tuckahoe’s because they remove large volumes of excess water from feed materials, smooth out feed fluctuations and produce a consistent, reliable in-spec product. They make it easy for Tuckahoe to produce secondary and tertiary products, such as golf course sand.
‘The Eagle Iron Works classifying tanks allow us to fine-tune the products that we’re producing,’ said Mr Sutton. ‘If one of those products becomes too coarse, we can then put that extra material to the third product to keep an eye on it and maintain the quality we’re looking for.’
Material discharged from the classifying tanks is sent to one of three EIW fine material washers, one of which has been in operation at Tuckahoe since 1999. These machines remove deleterious coatings and fine material from the sand products. They also dewater the product as it is conveyed up the screw shaft for discharge. ‘It’s important to use the EIW screws to produce a drier product faster. Our customers do not want to pay for water. They want to buy sand,’ said Mr Sutton.
To maintain the high-quality products for which Tuckahoe are known, the Eagle Iron Works wash plant is key. ‘The equipment is very important, and familiarity with the equipment is important,’ explained Mr Sutton. ‘It was important for us to have a product that our employees were familiar with. We didn’t really want to change. We didn’t want there to be a learning curve with the new plant. We wanted to hit the ground running and be able to transition from the old equipment we had to the new equipment, and staying with EIW allowed us to do that smoothly.’
Since their installation, Tuckahoe have found the EIW classifying tanks and fine material washers to be both very reliable and user-friendly – something they also found from their past experience with Eagle Iron Works equipment.
Moreover, with their new Eagle Iron Works wash plant, Tuckahoe have tripled their production to 300 tons/h, and as they continue to familiarize themselves with the new plant and optimize their process, they plan to produce even more. ‘We’re very satisfied,’ said Mr Sutton. ‘We feel as though our plan has come together. You always have a plan and goal on paper, but to feel as though you’ve reached that goal is rewarding.’
- Subscribe to Quarry Management, the monthly journal for the mineral products industry, to read articles before they appear on Agg-Net.com