Dynamic Stimulation
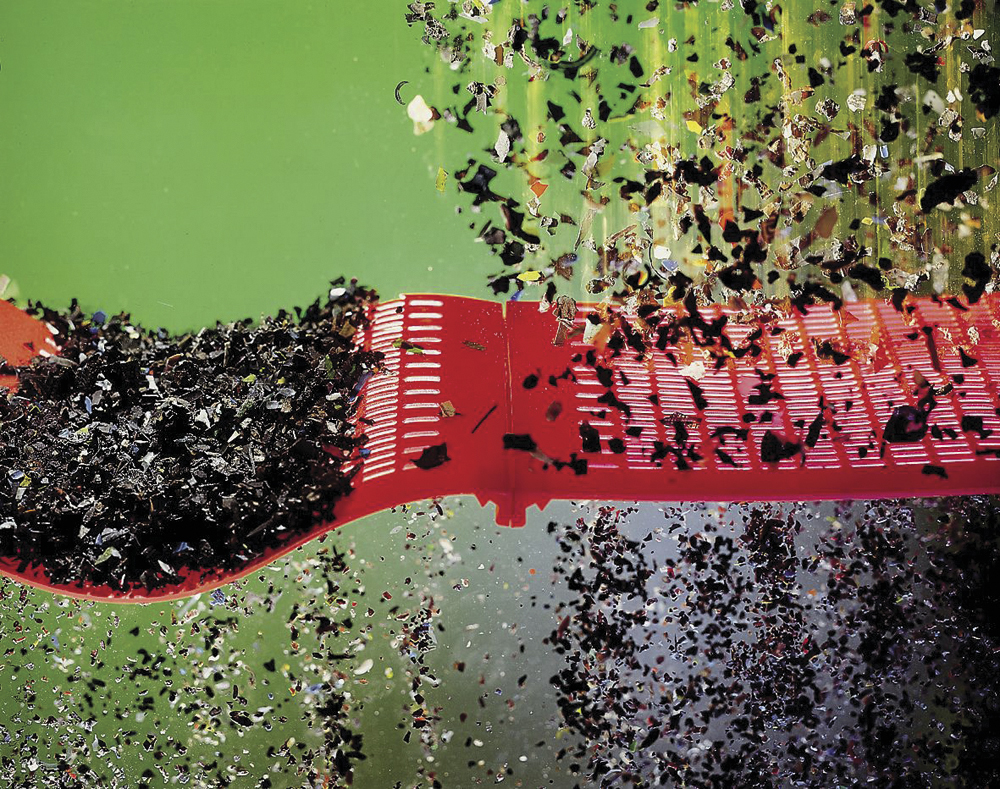
High-efficiency screening of difficult materials using Bivitec technology
By Ronan Ghosh, RG Recycling Ltd, and Christoph Baier, Binder+Co AG
Increasing demand for screening technology solutions that can deal with difficult-to screen-materials has created numerous new task assignments for the well-proven Bivitec range of screening machines from Binder+Co AG. The most common applications include: ‘filler removal’ and fines screening with moist crushed stone fines; screening of mixed construction waste; pre-screening of moist material; and wet screening of fine sands in the 0.3–1mm separation cut range.
Difficult to screen feed materials
There are three main problems when using ‘conventional’ screening machines, eg circular vibrating screens, linear vibrating screens or resonant screens, for material classification:
- High levels of surface moisture in the feed material can cause blinding in the screen cloth, particularly in combination with silt, clay or other impurities.
- Columnar and leaved feed materials can encourage the formation of clogging grains.
- Fibrous, matted particles in the feed material can entwine themselves around the ties in the screen cloth.
In all three cases mentioned above, the separation cut falls within a very short time to an unacceptable level in terms of screened product quality. This can continue until eventually no more screening can take place due to a clogged screen cloth. Some of the most difficult to screen feed materials include:
- argillaceous sand
- moist crushed stone fines
- moist pre-screening material
- coal and coal intermediates with commensurate surface moisture
- peat
- building rubble and mixed construction waste.
‘Filler removal’ involves the use of screening technology to separate the finest fines from moist crushed stone fines (0–2mm, 0–3mm or 0–5mm sizes) without resorting to elaborate measures such as airstream separation, drying, or spraying/water management. With crushed stone fines, the first quality characteristic is the content of oversized grains in percentage terms, followed by the grain size distribution of a particular crushed stone fine in the fines range. Depending on the reduction and classification technique used, and especially on the raw material’s natural fracture characteristics, a greater or lesser content of fines is generated (eg content less than 63μm) for each respective crushed stone fines product. It is then imperative to separate out the finest fines in order to attain the quality of higher-class products.
Mode of operation and relevant characteristics for special screening machine versions
With Bivitec screening machines, every second cross beam is rigidly connected to the screenbox (oscillating mass one) and, in this way, performs the same basic circular or linear vibration (fig. 1a). In between these cross beams are positioned freely oscillating beams (oscillating mass two) that are connected to the screenbox via thrust rubber spring elements (fig. 1b). These freely oscillating beams make up a single oscillating frame together with the longitudinal beams. Thus, a relative movement is generated between both beam systems or individual oscillating masses (fig. 1c). The screen mats are fastened without bolts between the rigid and moving cross beams. The relative movement between the beams causes the screen cloth to tauten and buckle alternately (see lead photo). When the screen cloth is tautened, high acceleration values of up to 500m/s2 occur (corresponding to about 50 times the acceleration due to gravity ‘g’). The screenbox itself is subjected to only very minor acceleration values somewhere in the range 2–3g.
The material being screened is loosened to a great extent by the high acceleration that is imparted by the dynamic stimulation of the screen cloth. The screen mats themselves are stretched in the tautening stage and then released in a whiplash effect, such that any material clinging to them is loosened and any clogging grains are ejected. The basic oscillation of the machine together with the Bivitec effect facilitates adequate material advancement, even at machine inclinations of 5° to 10°, and allows for a corresponding reduction in machine height in comparison with other systems.
The characteristics of Bivitec screening machines, ie the oscillation amplitude of the cross beams, can be easily and rapidly adjusted and optimized to cope with possible changes in parameters by:
- changing the basic oscillation by adjusting the unbalanced masses
- altering the spring constant by changing the number of thrust rubbers
- changing the stimulation speed.
When utilizing special screening machines, two relevant characteristics must be borne in mind with regard to outsize grains and wear:
- ‘Ox horn’ version: Binder+Co have developed a side seal that prevents wear between the screen cloth and screen flange by preventing outsized grains from discharging into the lower part of the screen.
- Fastening system without bolts: a system with completely smooth screen decks, free from fastening elements such as bolts, guide rails etc, is used for fastening the screen mats. Fastening the screen cloth without bolts eliminates wear on the diverse fastening elements and allows the screen cloths to be mounted or removed simply and quickly.
Several different Bivitec versions are possibile. Screens are differentiated into two groups according to the basic oscillation (circular or linear vibration), while another classification is made according to the number of screen decks: single, double, two-and-a-half, triple and four decks. With double- and two-and-a-half-deck systems, it is only possible to utilize the Bivitec system in the lower deck. Traditional composite screen cloths or wire mesh can be used in the upper deck (fig. 2). Effective screen widths range from 800mm to 3,000mm, while effective screen lengths cover the range from 3m up to 12m, giving a screening surface area from 2.4m2 up to 36m2 per screen deck.
Bivitec ‘banana’
These screening machines combine the well-known advantages of current commercially available ‘banana screens’ with those of Bivitec or flip/flop screening machines. This so-called banana version generates greater area-related throughput rates, more convenient layer heights, and a longer retention period for the screened material in the screen deck area on the discharge side (fig. 3). Consequently, and particularly with feed material with high fine grain content (ie high proportion less than the required separation cut), smaller machines can be employed while maintaining an equally clear separation effect. This means that correspondingly higher plant performance is possible even with limited space availability. For new plant installations, making use of a smaller machine has a positive effect on peripheral costs, such as screening machine supports, underflow hopper and feed conveyor.
If two separation cuts are to be carried out on one screen deck (eg single deck with two separation cuts or upper deck in two-and-a-half-deck machines), a banana version boasts significant benefits. On the feed side of the screen deck, where the screen mat has been installed with appropriately smaller hole diameters, there is a large amount of material to be screened. Here, the greater deck inclination causes better layer heights and, as a consequence, higher screening performance and clear separation effects. On the discharge side, a coarser separation cut takes place by means of relatively larger hole dimensions with a reduced amount of screening material on the deck. At the same time, the reduced screen deck inclination slows down the material, achieving the best layer height for the coarse separation cut as well as increasing screening material retention time on the deck.
Applications for Bivitec screening machines
Figure 4 shows a single-deck Bivitec banana KRL/ED 2200 x 7m – R45 machine for screening crushed gravel at 150 tonnes/h. The 0–4mm, 4–11mm and 11–20mm products are generated by means of two separation cuts on one screen deck. Among others features, this version offers the advantage of a low construction height as well as the possibility to quickly convert the separation cut from 4mm to 2mm without any great effort simply by changing the screen mats.
Figure 5 shows two double-deck Bivitec KRL/DD 3000 x 8m screening machines employed to pre-screen 0–120mm sand and gravel at 700 tonnes/h, with separation cuts at 63mm and 2mm. The machines are currently being operated without a spraying device as extraction is being carried out ‘dry’ using wheel loaders. This method will eventually be complemented by a suction dredger and two further identical Bivitec screening machines have already been delivered and will be set up to wet screen the dredged product.
To enhance the value of raw materials in a deposit, Binder+Co recommend the use of a Bivitec screening machine for the classification of pre-screening material (0–40mm). Separation cuts can vary from 8mm to 15mm, depending on deposit quality, offering the customer the possibility of controlling material flow according to rock quality and, thereby, attaining optimal exploitation of the deposit. Figure 6 shows this type of screening operation at a plant in Spain.
In the UK, RG Recycling Ltd have partnered with Binder+Co to supply screening equipment to plant operators. For example, the McCloskey B200 mobile tracked screening machine (fig. 7) utilizes Bivitec technology to produce quality products even in the most demanding conditions.
For further information visit: www.rgrecycling.co.uk