Dry Engineered Sand Solutions
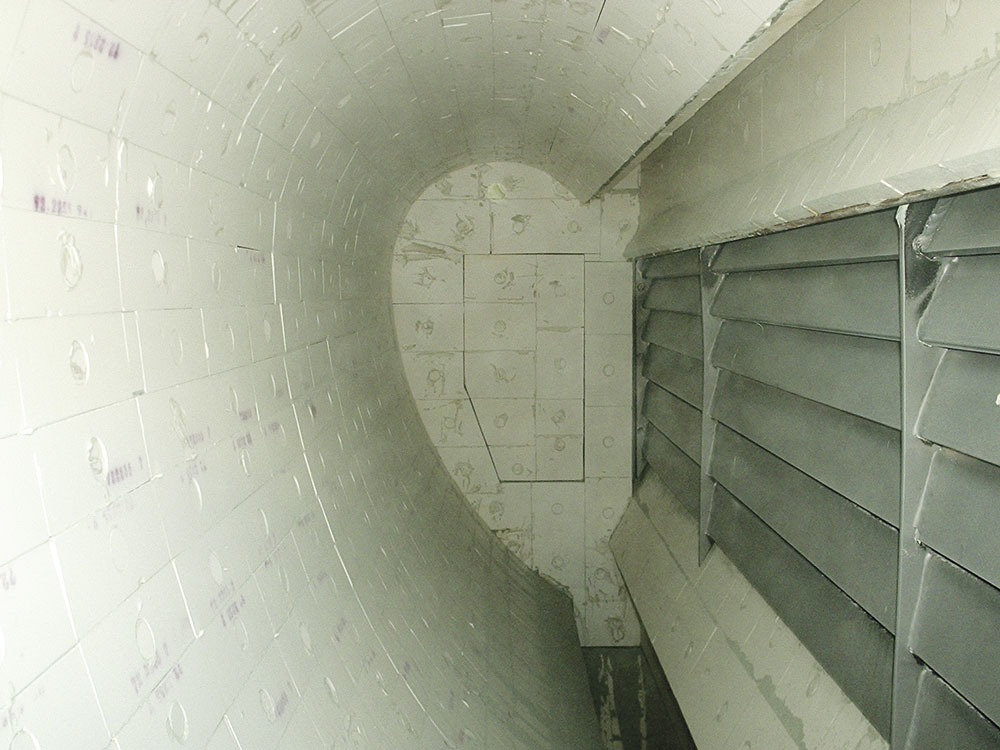
An overview of Luck Stone Corporation’s investigations, experiences and advances in the production of quality engineered sands from quarried rock
More than 20 years ago Luck Stone Corp., one of the largest family-owned and operated aggregates companies in the US, embarked on a sequenced investigation to satisfy demand for a dry asphalt sand product that would avoid the environmental concerns inherent in wet systems. The solution to dry asphalt sand processing also led them to applications for the production of their own design of dry engineered concrete sand.
Requirement for a dry solution
In 1989, Luck Stone’s northern Virginia sales staff requested a manufactured sand product to supply to their asphalt customers. Engineered sand specifications for concrete in the US are controlled by the American Society for Testing and Materials (ASTM) through C33 and are significantly different to those in most other countries. Manufactured sand for use in asphalt in Virginia – Luck Stone’s primary market – is generally considered to be material passing a 6.3mm (1/4in) screen. However, the real asphalt issue was, and is, the excess –75 micron component, which needed to be less than 7% passing 200 mesh.
Because most ‘screenings’ have significantly more material passing 200 mesh, Luck Stone had routinely employed a wet process to remove the excess, but concerns regarding space and the environmental aspects of this process pointed to the desirability of a dry processing system. As a result, in 1990 the company began an investigation into ‘dry’ alternatives to dewatering with a classifying screw.
The search begins
As with many aggregate producers, Luck Stone were faced with a dilemma. How could they produce asphalt sand without the associated problems of a wet process? They did not want to sacrifice aggregate stockpile space to locate dewatering ponds, nor did they want to process or produce wet material during freezing weather. Also, they did not want the environmental concerns that are inherent with ponds, eg wet fines containment and water or slimes disposal.
The challenge of finding a dry solution was given to Luck Stone’s chief engineer at the time, Bob Stansell (since deceased), who considered and tested several options.
Dry fine screening
Luck Stone began their investigation on a suggestion from their Leesburg plant manager. He proposed that they investigate a multi-deck screen that had previously been demonstrated to him. The desired result with this type of screen would be realized if it could remove a sufficient amount of –75 micron material by either screening or air sweeping to meet a gradation of less than 5% passing 200 mesh.
After several days of testing and evaluation, Luck Stone concluded that this particular screening unit would not be suited to dry separation at a cut point below 300 microns (50 mesh), nor would it be effective in the production of a final product due to its sensitivity to moisture and the company’s inability to control the weather.
Fluid-bed dryer
Luck Stone then investigated a fluid-bed style dryer. This process would have the advantage of being able to remove moisture at the same time the ultrafines were being removed. The equipment included a slightly inclined vibrating pan with many small holes throughout – an arrangement that allowed heated air to pass through the material both drying and removing the ultrafines.
This process offered excellent control regarding the cut point and eliminated the moisture problem associated with damp feed. The results were favorable with good levels of control and predicted consistency.
However, even though this equipment provided excellent results, Luck Stone determined that the capital required to install such a system would be excessive. Their concern also extended to the higher maintenance considerations of this process due to abrasion and complex burner requirements. The added processing cost to provide the necessary energy for drying was another consideration. Their final concern was the ability of such a system to operate safely unattended with the balance of the automated circuit.
Therefore, although the fluid-bed dryer was superior in providing a good, clean and consistent product, Luck Stone decided to continue their search for a better process.
A new direction
During a market lull, with decreased demand for an asphalt sand, the intensity of this investigation abated as Luck Stone turned to other pressing issues. During this time the company began a serious study of the moisture content in process screenings. This was conducted over a six-month period and found an average moisture content level of 1.5%, due primarily to water added at the crusher for dust control.
Also noteworthy during this period was the installation of dust collectors on the circuit, minimizing the need for water addition at the crushers. These results encouraged Bob Stansell to investigate a type of air classifier he had installed some 20 years earlier. He had not seriously considered this air classifier, as his previous experience had shown it to wear rapidly, even in limestone. Other concerns were sensitivity to feed moisture, similar to other fine-separation equipment.
However, continuing his investigation, Mr Stansell discovered that the company responsible for this particular classifier – the gravitational inertial classifier – was actively marketing this process for dry engineered sands. He also discovered that the company had overcome his concerns regarding wear through the utilization of ceramic liners.
Metso static classifier solutions
The technology that Luck Stone investigated has recently been purchased by Metso. It is one of three separate static classifier types offered dependant upon the separation required by the process.
Gravitational classifiers produce 0.15–1.65mm (12/100 mesh) separations and are suitable for coarse industrial mineral solutions, while centrifugal classifiers exploit centrifugal forces to produce very fine separations – 0.02–0.15mm (100/600 mesh) – and are suitable for industrial mineral, mining, fly ash and cement applications.
Gravitational inertial classifiers produce 0.063–0.3mm (50/230 mesh) separations and are highly suitable for precise engineered sand applications. An adjustable air flow controls the amount of ultrafines retained as product and recirculating air scrubs the coarse product before it exits.
The gravitational inertial classifier’s main applications are in the production of quality engineered sands from quarried rock. The classifier utilizes air flow, gravity and directional changes to achieve very accurate and adjustable material separations.
The ultrafine retention is controlled by adjustment of the primary to secondary air ratio. Tailoring the amount of ultrafines in the product offers quality sand production with minimum waste.
Static yet accurate
The gravitational inertial classifier offers a versatile option that can fit into multiple quarrying solutions. It is highly accurate and adjustable, and has the ability to remove only the ultrafines that need to be removed, which maximizes both productivity and sand quality.
Moreover, these classifiers have exceptionally low operating costs as they have no moving parts and ceramic lining throughout. This means that no adjustment for wear is required and abrasive feeds have little influence on operating costs, with ceramic liners lasting for years even in highly abrasive applications.
The intelligent design of the classifier also effectively utilizes the air movement, which minimizes the power requirement.
Luck Stone’s experience at Leesburg
Luck Stone submitted test samples for evaluation with the gravitational inertial classifier in the autumn of 1992. Based on the initial tests, as well as an on-site visit of the testing facilities, a design process was initiated to include a gravitational inertial classifier at Luck Stone’s Leesburg plant, in Virginia.
During the design process a structure to support a dual AC22.5GI was built. A single unit, installed in 1993, absorbed the existing 60 tons/h of 2mm (10 mesh) screenings produced by a Nordberg 51/2ft shorthead cone. With the addition of a new HP300 to the circuit in 1994, the increased feed tonnages required the installation of the second AC22.5GI unit to give a combined throughput of 120 tons/h.
A single conveyor from the circuit feeds both units by use of a splitter at the head pulley discharge. After passing through the classifiers, the finished asphalt sand product falls through a mixer where water is added both for dust control and to maintain product homogeneity. This air-scrubbed sand product is then conveyed to a stacker for outside storage.
The sand plant fines (SPF), ie the –75 micron component (200 mesh) removed from the classifiers and separated from the air by the dust collector, are stored in a 350-ton silo. Draft for both the dust collector and the dual AC22.5GI classifiers is provided by a single 75kW (100hp) system fan. The system operates under negative pressure, thereby eliminating the problem of fugitive dust.
Product characteristics and uses
The final classifier product (air-scrubbed screenings) provides a more desirable material for the asphalt producer. Limiting the moisture in this dry process reduces the amount of energy required by the asphalt producer to dry the material, thereby resulting in cost savings. Removing water leads to added savings because the asphalt plants become more productive as they retain stone for less time, thus allowing the full design tonnage/h to run through the plant.
An important question Luck Stone considered when evaluating this process was what could be done with the ultrafines that are generated. They determined that these could be blended back into the base product without any detrimental effects, so a handling system to achieve this was designed into the plant layout. Although these fines range over 90% passing 75 microns, their impact upon the base quality is limited due to the differences in comparative volumes. And because these fines are easy to handle, a system for loading them directly into trucks was also included in the design.
A new challenge – engineered concrete sand
Today Luck Stone employ air-classification technology at the majority of their plants and have also adapted its use to make engineered concrete sand.
Several years after the successful production of asphalt sand with their air classifiers, Luck Stone began to investigate a replacement crushed-stone product for natural sand in the ready-mixed concrete market. After more than a decade of effort, this pursuit has resulted in the production of high-performance crushed fine aggregate for use in concrete.
Production of engineered concrete sand is much more difficult in the US compared with other parts of the world due to the tight ASTM regulatory specifications. The ASTM C33 specifications are designed for natural sands with little accommodation for manufactured sands within the envelope. For this reason, achieving specification with engineered concrete sand in the US is a difficult task. It is also the case that most concrete customers in the US only have experience in the use of natural sands and are thus very resistant to engineered concrete sand technologies.
Research based approach
Luck Stone started their research into this area with the International Center for Aggregates Research (ICAR), a joint operation of The University of Texas, Austin, and Texas A&M University, which is dedicated to aggregate research. The goal of one of ICAR’s projects was to prove that engineered sands can, and do, compete technically with natural sands, and to demonstrate that high percentages of –75 micron (200 mesh) are feasible in Portland Cement Concrete (PCC).
The results from this research proved that higher percentages of –75 micron are not detrimental to the quality of engineered sand, which does, in fact, have advantages over natural sand. The results showed that processing with a Barmac VSI produced excellent texture and shape in the engineered sand.
From research to reality
Luck Stone carried out multiple trials of local natural sands against those produced in each of their quarry sites. The best engineered sand results were from crushing diabase (trap rock) at their Goose Creek site. The company purchased a Barmac B9100 VSI for Goose Creek in 1998 as it could foresee increasing demand for shaped aggregate and the possibility of producing quality engineered sand from this site. After installation of the Barmac, the site produced a ‘high fines’ engineered sand with 14% passing 75 microns (200 mesh). The company also commissioned the Aggregates Research Institute (ARI) to help establish the quality of the engineered sand.
During this period Luck Stone branded the engineered concrete sand as Advanta. However, owing to Advanta’s higher than ASTM C33-allowed –75 micron content compared with natural sand, it proved difficult for the product to gain acceptance with customers. To try to encourage acceptance of Advanta, Luck Stone decided that blending with natural sand to decrease the –200 mesh would allow their customers to gain confidence in the new sand.
Blends were produced by mixing Advanta with natural sand from Luck Stone’s Caroline pit, but customers still proved resistant to the new sand. To further help encourage the use of Advanta, Luck Stone specified the product’s use on a major construction project at their Goose Creek plant. As a result of this work and the performance of the concrete during finishing, customers began to use the material in mixes for low-risk uses. The blended sand was eventually accepted by customers but blending costs proved to be high due to the cost of transportation of natural sand.
Controlling the ultrafines to produce 100% engineered concrete sand
Luck Stone decided that they needed to reduce the amount of –75 micron present in Advanta concrete sand in order for customers to accept a 100% engineered sand. A dual AC22.5GI air classifier was installed at Goose Creek in 2005 to control the –75 micron content, creating an improved Advanta concrete sand to meet their customers’ requirements.
After several years Luck Stone determined to advance the concrete sand strategy to other production plants where markets were present. To do this, they decided the best solution was to conduct large-scale testing using a portable Barmac B6100 VSI, a screen and a transportable gravitational inertial air classifier, in order to prove the viability of the product to customers.
By changing the Barmac VSI’s rotor speed Luck Stone were able to adapt different stone mineralogies to perform in a similar fashion to natural sands from the local area. The portable plant was installed at Luck Stone’s quarry sites and then fed with sufficient material to produce 1,000–1,500 tons of Advanta concrete sand for specific customers to test at full production through their ready-mix plants, providing a means to determine real-time production benefits outside a laboratory setting. Following completion of the experimentation, this transportable test plant is now producing Advanta concrete sand consistently at one of Luck Stone’s plants.
With the success of the trials, a decision was made to establish Advanta concrete sand production at Goose Creek, in Virginia. This decision was based on both market demand and location geology. Installed in 2005, the dual AC22.5GI is fed with crushed sand from a Barmac B9100. The dual AC22.5GI air classifier processes up to 100 tons/h of sand to produce both Advanta as well as mineral filler supplement (used in hot-mix asphalts, specifically SMAs) from the –200 mesh.
Conclusion
Today, several of Luck Stone’s plants are producing Advanta concrete sand and the strategy is to continue introducing this product to the company’s concrete customers. This is testament to Luck Stone’s tenacity and foresight in introducing Advanta in spite of the difficulties due to both customer resistance to change and unfavourable ASTM specifications.
Meanwhile, in 2010, Metso purchased the Buell air-classification technology from Fisher-Klosterman Inc. Metso intend to build on the success that this long-established air-classification technology has had in the US. It is being offered along with existing Metso technologies to create highly efficient and adjustable solutions to engineered sand production globally.