Bruce Engineering supply modular sand washing plant to Russian aggregate producer
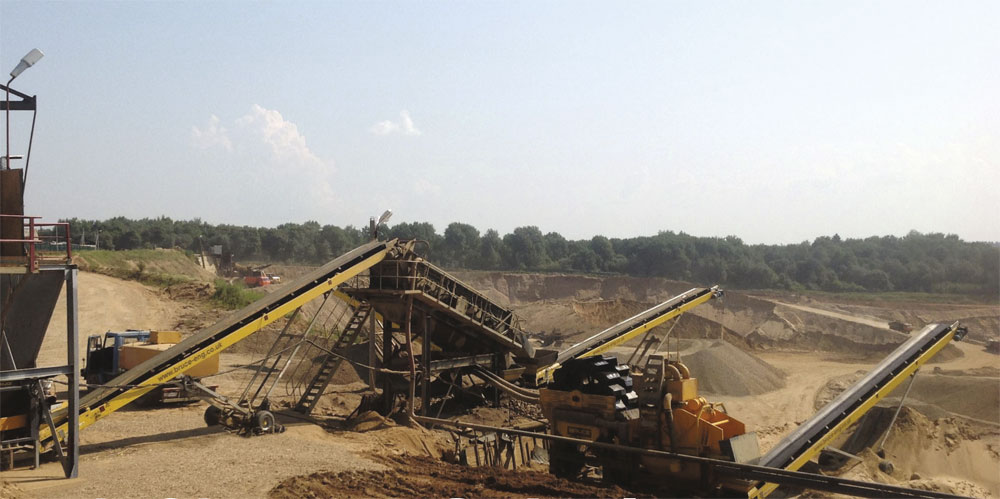
First published in the August 2013 issue of Quarry Management as A Clearer Solution
Bruce Engineering washing plant working 24h a day, seven days a week in Russia
With more than 50 years’ experience in materials processing and numerous modular washing plants in operation throughout Russia, Bruce Engineering were the first choice for one Russian customer seeking a cost-effective solution to the problem of washing a high silt content aggregate material.
Bruce were approached on behalf of the customer by their exclusive distributor in Russia, GT Holdings Ltd, and given a remit to provide a highly productive, low-maintenance solution capable of running round the clock, seven days a week, to deliver a much demanded and profitable product to sell to the construction market in Russia.
Following a site visit and analysis of the feed material by Bruce’s washing team, the Northern Ireland-based company proposed a simple modular washing plant. The feed material comprises 0–100mm aggregate with a high silt content, which is difficult for conventional dewatering equipment to deal with.
The plant supplied by Bruce is fed via a free-standing hopper equipped with a belt feeder. From here the material is conveyed to a 6m x 2m double-deck washing screen that produces two finished products (+30mm and –30mm +3mm) for stockpiling. As around 80% of the feed consists of –6mm material, a Bruce BWSRB120 unit provides an efficient, cost-effective and user-friendly solution for sand recovery.
All –3mm slurry from the bottom deck of the washing screen is fed, via a simple sump and pipe system, to the Bruce BWSRB120, which comprises a double bucket wheel, centrifugal slurry pump, twin hydrocyclones, collection tank and dewatering screens all mounted on one chassis. Capable of throughputs up to 120 tonnes/h, this machine delivers a highly desirable clean sand while ensuring less wear on the cyclones and providing a drier end product.
According to the customer, the new plant has exceeded all expectations. They say it is very efficient, easy to run and capable of producing material 24h a day, seven days a week. It also suits the country’s extreme weather conditions, which can range from –18°C to +30°C.
A spokesperson for GT Holdings Ltd added: ‘Bruce’s specialized team specified the correct plant to process this material and offered a simple solution that our customer could run efficiently and cost-effectively.’
Bruce Engineering say that, if required, they can also supply a silt-recovery system for a complete turnkey solution that can be adapted to suit or complement any existing plant.
To find out more about the company’s bespoke washing systems, email: caroline@bruce-eng.co.uk; or visit: www.bruceeng.co.uk
- Subscribe to Quarry Management, the monthly journal for the mineral products industry, to read articles before they appear on Agg-Net