The Latest Silo-Protection Technology from Hycontrol
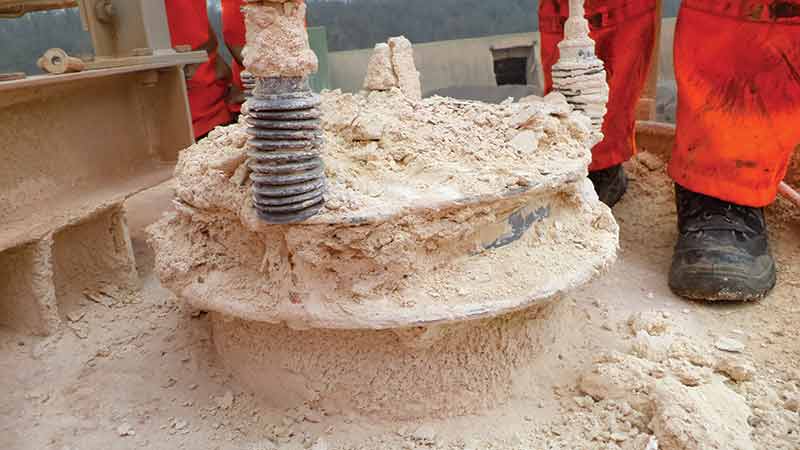
First published in the August 2015 issue of Quarry Management as A Disaster Waiting to Happen?
The latest silo-protection technology provides much more than a safety system to prevent overfilling and over-pressurization of powder storage silos
Having designed specialist silo-protection systems for more than 20 years, level-measurement specialists Hycontrol have extensive experience of the potential problems that exist on sites, especially in the cement, quarrying and bitumen sectors. And according to managing director Nigel Allen, many powder storage silos are disasters waiting to happen, putting lives at risk and posing serious threats to the environment.
‘Our findings are worrying to say the least, and the photos taken by our installation engineers speak for themselves,’ said Mr Allen. ‘Companies just don’t seem to understand the consequences of poorly maintained protection systems. It’s quite frightening that operators accept pressure blowouts via the pressure-relief valve (PRV), erroneously thinking that ‘It’s OK – the PRV is doing its job’. This couldn’t be further from the truth – PRVs are there as a last resort.
‘If the silo-protection system is working correctly and is fitted with an automatic shut-off feature to prevent overfilling, the PRV should never be used. If a PRV blows then there’s an inherent problem with the system or the filling protocol and corrective action must be taken.
‘Material in and around a PRV is a telltale sign that there’s something wrong and a catastrophic blowout is waiting to happen,’ he continued. ‘The material blown out from the silos will almost certainly solidify over time and this will, at best, prevent the PRV from working correctly, and at worst, completely clog it up. Unfortunately, many maintenance engineers just don’t realize the potential dangers that lurk beneath. They often think that simply cleaning off the material on and around the PRV is good enough. They don’t realize that if the PRV doesn’t lift next time an ‘event’ occurs, the over-pressure could easily rupture the silo or eject the filter housing from the top. On an ATEX-rated silo the over-pressure could be sufficient to simulate an explosion and open the protective blast panels, resulting in costly loss of product and silo contents being left open to the elements.’
With regard to filter housings, Hycontrol engineers say they have witnessed another worrying practice at a number of sites where companies fit chains to prevent the housing being blown off the top of the silo, almost accepting blowouts as an inevitability.
What causes over-pressurization problems?
Silo-protection systems are designed to prevent the damaging and potentially dangerous consequences of silo overfilling or over-pressurization when powdered material is being transferred pneumatically from road tankers to silos. Unfortunately, perched on the top of silos, such protection systems are all too often ‘out of sight, out of mind’ – until a major problem occurs.
Problems during the filling process usually arise through an inherent problem with the silo-protection system or with the air-filtration system on top of the silo. Problems can also occur through tanker driver/operator error. Delivery tankers are pressure-tested vessels, typically capable of withstanding up to 2 bar (29 lb/in2) pressure. Storage silos, on the other hand, are only designed to withstand the weight of material stored in them and can rupture at pressures as low as 1–2 lb/in2 above atmospheric pressure.
The possible consequences of overfilling or over-pressurization include:
- Serious or fatal injury to workers and the public
- Catastrophic silo damage
- Loss of material and production
- Harmful environmental pollution
- Damage to company reputation.
A key issue with many silo-protection systems is that without adequate ground-level testing capabilities, operators do not know if they will work when needed. Working at height restrictions limit silo-top inspections and maintenance, especially in adverse weather conditions. The main problem, however, is what can engineers actually do when they are at the top of the silo? How can they physically test a relief valve or pressure transmitter unless they remove them?
Even if the protection system does do its intended job and prevents a major incident, companies rarely investigate the root cause of the problem so that remedial work can be carried out to prevent the situation reoccurring. Important near-miss events such as PRV (pressure-relief valve) lifts, high level events and high-pressure events are routinely not recorded and often conveniently dismissed. Hycontrol have clear evidence that, in practice, there are more near-misses than realized and the situation is a ticking time bomb.
Filter housings on top of silos are designed to vent the silo during filling, while preventing dust escaping into the atmosphere. Normally, these are fitted with some form of self-cleaning system to keep the filters clear, typically mechanical shakers or reverse-jet systems. Although filter manufacturers give recommended check routines and filter replacement schedules, in practice it would appear that these guidelines are regularly ignored. Faulty operation can be caused by a range of issues, including blockages and the fitting of unsuitable or wrongly sized filters. Most powders form hard compounds when mixed with water from the atmosphere, further exacerbating the problems at the top of the silo.
The Mineral Products Association publishes comprehensive guidelines for silo-protection systems in quarries and cement works, but even with guidelines in place the benchmark for the effectiveness of any silo safety protection system can only relate to the last time all the components were fully tested.
Optimum solution
The only effective solution is to take an integrated approach to silo-protection design whereby the PRV, pressure sensor and high level alarm can be tested at ground level, prior to each fill. Only when all these safety devices have passed the checks should the safety interlock allow the silo inlet valve to open and the delivery to commence.
As an added benefit, an effective protection system can serve as a powerful predictive maintenance diagnostic tool by recording critical near-miss events that occur during the filling process. This information allows managers to carry out effective predictive maintenance by means of a logical step-by-step root-cause analysis (RCA) process to understand why the problems are arising. For example, high-pressure and PRV-lift events may be due to filter problems, prompting questions such as:
- Are the filters the correct size?
- Is the filter cleaning regime fully operational?
- Have the filter bags/cartridges been changed in line with manufacturers’ recommendations?
In parallel, the logs will also indicate if the tanker drivers are routinely over-pressurizing during the fill process.
In summary, the optimized silo-protection system should incorporate:
- Pressure sensor, high level alarm sensor and PRV testing (essential)
- Simple one-button press to test all components
- Silo-filling auto shut-off control
- Pneumatic cleaning of pressure sensor
- Recording of the number of incidents of over-pressure (time/date stamp)
- Recording of the number of events of PRV lift and opening (time/date stamp)
- Recording of the number of events of high level probe activation (time/date stamp)
- Filter ON/OFF output option to check filter status
- Filter air supply monitoring alarm option.
There is strong empirical evidence that many silos are disasters waiting to happen. The practical reality is that powder storage silos can split or rupture at pressures as low as 1 or 2 lb/in2 above atmospheric pressure. Malfunctioning filter housings can and have been ejected at similar pressures.
Simply relying on cursory visual inspections of silo-protection equipment is woefully inadequate. It is imperative, therefore, that any installed safety system must be capable of providing reliable protection that can be easily verified by testing critical components before each and every delivery – without having to climb to the top of the silo. This approach will provide total silo safety; protecting assets, the environment and, most importantly, site personnel and the public.
- Subscribe to Quarry Management, the monthly journal for the mineral products industry, to read articles before they appear on Agg-Net.com