The Invisible Belt Destroyers
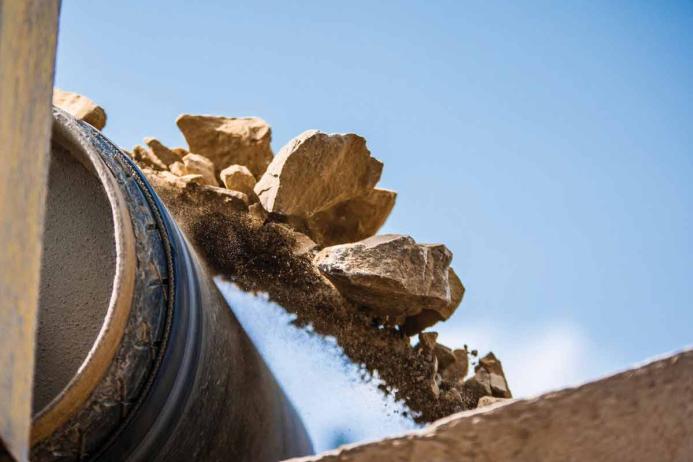
First published in the March 2024 issue of Quarry Management
How ozone and ultraviolet light dramatically shorten the working life of conveyor belts
No matter what price you pay, the reliability and longevity of your conveyor belts will ultimately dictate their true cost. There are many factors that determine the length of that working lifetime, including abrasion, cutting, gouging, impact, ripping, and tearing.
However, what is not so well known is that two unavoidable factors, ozone (O3) and ultraviolet light (UV), also have a hugely detrimental influence on the operational lifetime of conveyor belts. The damage is extensive and certainly not limited to higher altitudes or sunny climates. Nearly all rubber used in conveyor belts is synthetic and can easily be made resistant to their effects. Despite this, more than 90% of all conveyor belts sold in Europe are not ozone and UV resistant. In this article, application engineer Rob van Oijen explains the ozone and ultraviolet phenomenon and how to avoid the damage it causes.
Ozone and ultraviolet damage – Causes and effects
Ground-level ozone (O3), also known as surface-level ozone and tropospheric ozone, is a trace gas in the troposphere (the lowest level of the Earth’s atmosphere). It is created by the photolysis of nitrogen dioxide (NO2) from sources such as automobile exhaust and industrial discharges. Scientifically, this is known as ozonolysis, which is the reaction that occurs between the molecular structure (double bonds) and ozone. The immediate result is formation of an ozonide, which then decomposes rapidly so that the double-bond molecule is split.
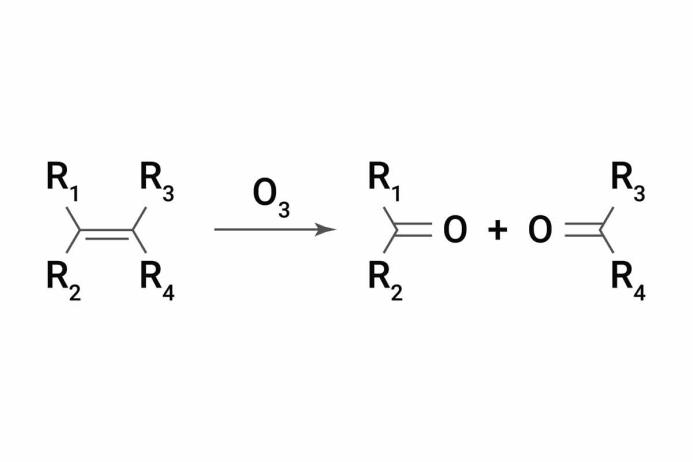
The critical step in the breakdown of molecular chains is when rubber polymers are attacked. By splitting the chain, the molecular weight drops rapidly. There comes a point when very little strength remains in the rubber and cracks start to form. Further attacks occur inside the freshly exposed cracks, which continue to grow steadily until they complete a ‘circuit’ and the product separates or fails.
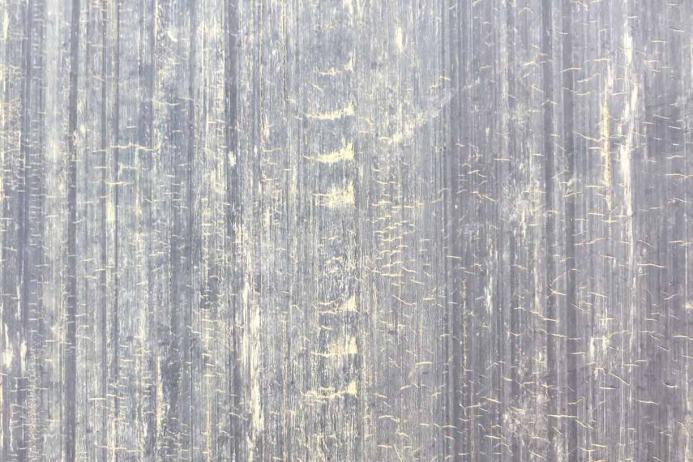
Exposure is unavoidable because even tiny traces of ozone in the air will attack the molecular structure of rubber. It increases the acidity of carbon black surfaces with natural rubber, polybutadiene, styrene-butadiene rubber, and nitrile rubber being the most sensitive to degradation. The first visible sign of a problem is when cracks start to appear in the surface of the rubber. Unless an adequate level of ozone resistance has been built into the rubber compound, the process of ozonolysis effectively begins when the conveyor belt leaves the production line.
Although the variability of weather, airflow patterns, seasonal changes, the level of emissions and climatic conditions do mean that ozone concentrations can differ from one location to another, the fact is that ground-level ozone pollution is ever-present and, therefore, its effects should never be underestimated.
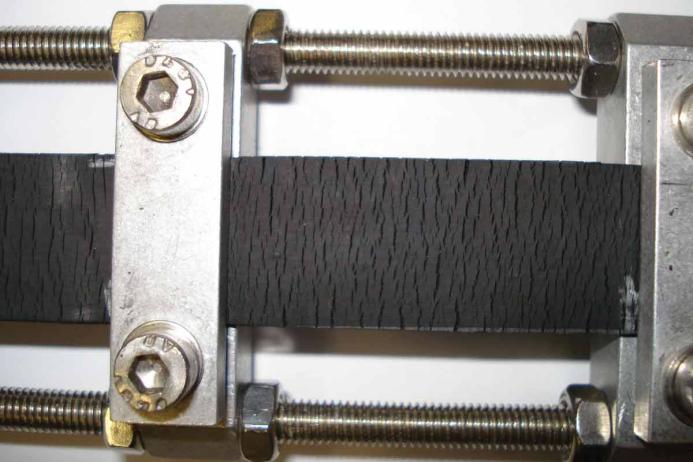
Hidden effects
Ozone cracks form in rubber that is under tension. This is sometimes referred as ‘dry rotting’. It is important to bear in mind that the amount of tension (critical strain) needed is extremely small. Even a belt that has not yet been fitted has a certain amount of intrinsic tension. The cracks are always oriented at right angles to the strain axis. The dynamic stress that a conveyor belt undergoes while in operation is considerable. Ozone attack occurs at the points where the strain is greatest.
The repeated action of the mechanical stress of the conveyor belt and the frictional process from the idlers means that the rubber molecular chain will break to form what scientists refer to as a ‘free radical’. This triggers the oxidative chain reaction that forms a chemical process which mechanically breaks the molecular chain and activates the oxidation process, which magnifies a whole range of more obvious problems and weaknesses, including the ability to resist abrasion.
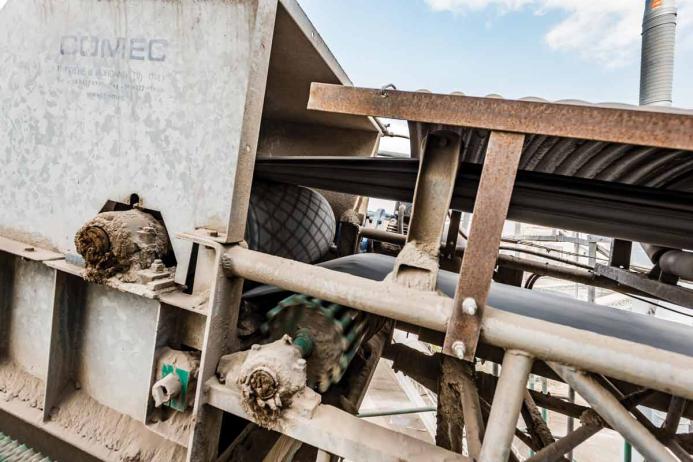
Stress magnification
At first glance, having small cracks in the surface rubber may not seem to be significant, but over a surprisingly short time, the rubber becomes increasingly brittle. As just mentioned, transversal cracks deepen under the repeated stress of passing over the pulleys and drums. The ozone continues to attack so the cracks will steadily grow until catastrophic failure occurs. Cracks often present other potential risks such as scrapers catching on them and tearing off parts of the cover. Splice repairs can also become increasingly difficult over time as the adhesion properties of the rubber diminish.
Yet another ‘hidden’ problem is that moisture seeps into the cracks. This penetrates down to the actual carcass of the belt. In multi-ply belts, the synthetic fibres of the weft strands of the plies expand as they absorb moisture, which, in turn, causes sections of the carcass to contract (shorten) as the weft strands pull on the warp strands of the ply. This can lead to tracking problems that can be very difficult to pinpoint, and which no amount of steering idler adjustment can compensate for. There can also be significant environmental and health and safety consequences because fine particles of dust penetrate the cracks and are then discharged (shaken out) on the return (underside) run of the belt.
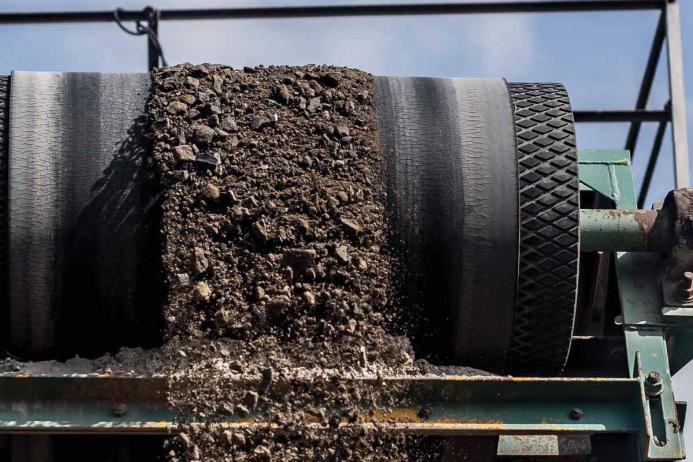
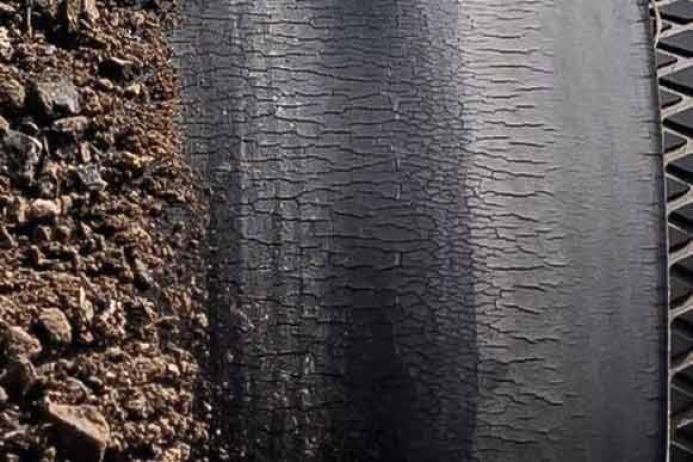
A partner in crime
To make matters worse, ‘bad’ ozone has a partner in crime that also has a seriously detrimental effect on rubber. Ultraviolet light from sunlight and artificial (fluorescent) lighting accelerates rubber deterioration because it produces photochemical reactions that promote the oxidation of the rubber surface, resulting in a loss in mechanical strength. This is known as ‘UV degradation’.
Ironically, the decline in the ozone layer in the upper atmosphere over the past several decades is allowing an increasing level of UV radiation to reach the earth’s surface. As you would expect, the problem is worse in sunnier, hot climates, but even in the most moderate of environments the problem is ever-present and, as with ozone, it would be foolish to underestimate the damage it causes.

Entirely preventable
As touched on earlier, damage caused by ozone and ultraviolet is almost entirely preventable thanks to the use of modern technology. Several years ago, Fenner Dunlop were among the first to make use of new technology that allowed the effects of ozone on rubber to be tested and measured. We equipped our laboratory with the very latest ozone testing equipment and introduced mandatory testing to EN ISO 1431 international standards for all of our rubber products.
As a result, special additives that act as highly efficient anti-ozonants and protect against the damaging effects of ozone and ultraviolet became a compulsory ingredient of all our rubber compound recipes, without exception. The same testing regime was applied to samples of belts made by other manufacturers.
Unfortunately for end-users, most belt manufacturers do not use anti-oxidant additives. This is because so much of the market is dominated by those trying to undercut their competitors on price. Anti-ozonants are not cheap. Consequently, in the pursuit of a price advantage, they are simply not used. A more sinister aspect of their non-use is that for many belt manufacturers and traders, anything that prolongs the working life of conveyor belts is not good for business.
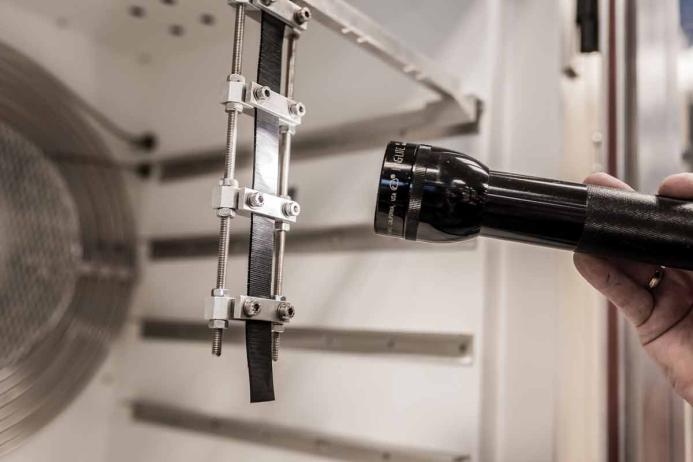
EN ISO 1431 testing
The EN ISO 1431 test method is used to scientifically measure resistance to ozone. Samples are placed under tension (eg 20% elongation) inside an ozone testing cabinet and exposed to highly concentrated levels of ozone for a period of up to 96h (@ 40°C, 50pphm and 20% strain).
Samples are closely examined for evidence of cracking at two-hourly intervals and the results carefully measured and recorded. Experience has determined that in order for the rubber to be regarded as adequately resistant, the pass criteria is that the rubber sample does not show any signs of cracking within the 96h period.
As mentioned earlier, more than 90% of belts tested in Europe fail the EN ISO 1431 test. Worse still, in the majority of cases, the cracks start to appear as early as 6–8h within the target time of 96h. In fact, it is not uncommon to see rubber samples completely disintegrate within a few hours.
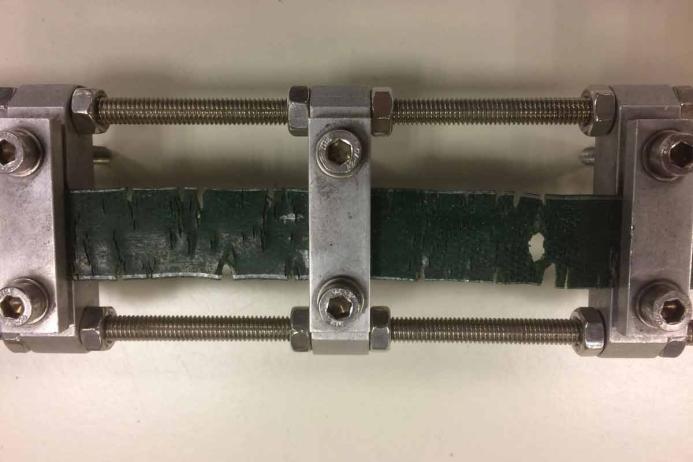
Swept under the carpet
Despite its crucial importance, ozone and UV resistance is very rarely, if ever, mentioned by belt manufacturers and suppliers and remains a subject that is swept under the carpet.
Because of the sheer size of industrial conveyor belts, it is common practice amongst manufacturers and distributors to store rolls of belting in the open air. Belts can often be held in stock for long periods, sometimes for years, before they are eventually put to use. During that time, they are vulnerable to the ever-present effects of ozone and UV radiation. A number of conveyor belt users have reported that surface cracking could be seen at the time of delivery.
No hiding place
Ozone can be found everywhere. There is no hiding place. The importance of having conveyor belts that are resistant to the damage caused by ozone and ultraviolet can no longer be ignored. Unless conveyor operators start insisting on having belts that are ozone and UV resistant, the vast majority of belt manufacturers and suppliers will continue to ignore the issue and supply belts that will start to deteriorate from the moment they are created.
For all buyers of rubber conveyor belts, an absolute prerequisite when buying any type of belt is that it is fully resistant to the effects of ozone and ultraviolet. Always insist on certification that confirms that the belt you are being offered is fully resistant to ozone and UV in accordance with the EN ISO 1431 test method, because without this essential property the belt will almost certainly need to be replaced far sooner than it should be.
About the author
Rob van Oijen, application engineering manager for Fenner Dunlop Conveyor Belting in The Netherlands, is one of the most highly respected application engineers in the industry. He has specialized in conveyors for more than 15 years, supporting businesses throughout Europe, Africa, the Middle East, and South America.
Subscribe to Quarry Management, the monthly journal for the mineral products industry, to read articles before they appear on Agg-Net.com