Sixty years of the Roto-Packer
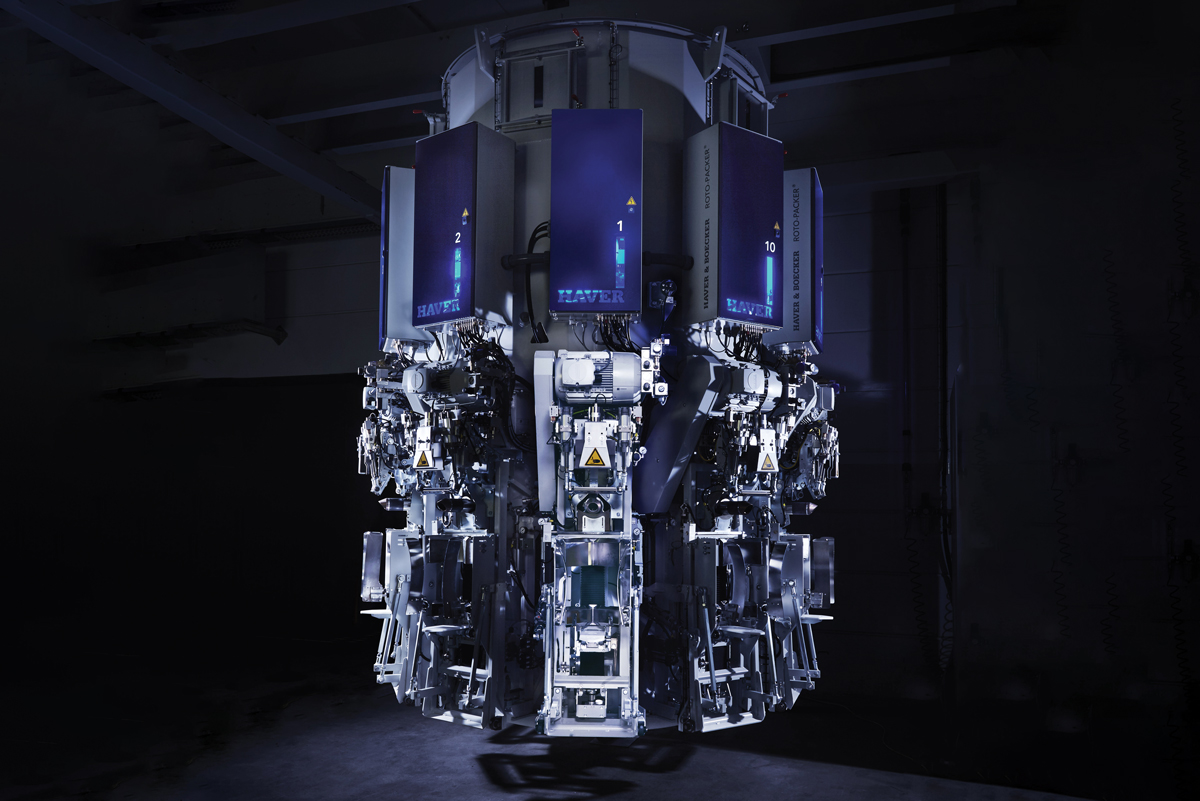
First published in the September 2020 issue of Quarry Management
Haver & Boecker celebrate the world’s most famous round packer, which heralded a new era in bag packing when the prototype went into operation in 1960
Back in 1960, like today, the Roto-Packer was unique in its future-oriented design and in its ability to meet the market demands with precision. As ‘the original’, the Roto-Packer has actively shaped the cement industry and supported growth in the building materials sector.
Many developments of the Roto-Packer have been shaped by increasing customer demands. At the outset, Rudolf Haver and designer Paul Schwake reacted to a suggestion made by the Phoenix cement plant in Beckum, Germany, which needed a more powerful system than the previous in-line packers, so Mr Schwake combined the rotating system of a round packer with the unique Haver & Boecker filling technology, which was able to efficiently fill the paper bags that, at the time, were emerging on the market. He implemented a machine that could meet the changes of the future and could be expanded by adding further spouts, laying the cornerstone for a success story that would last decades.
Many things have changed in mechanical engineering over the past 60 years. Whilst the first Roto-Packer was purely mechanical, except for the drive motors, today it is a detailed and well-balanced combination of mechanics, electronics and pneumatics. The filling of paper bags instead of jute bags was a major milestone. Another milestone is currently being experienced in the filling of PE bags. As is the case today, over the decades further developments of the Roto-Packer fulfilled the requirements of tomorrow’s market. The Roto-Packer has been continuously expanded in seven major development steps, bringing customers important new advantages in the cement, building materials and many other industries:
- The first Roto-Packer impresses with new filling technology and expandability. It fills more bags than comparable systems and does so with the newly developed paper bags.
- Additional correction weighers improve weight accuracy.
- The automatic bag applicator, in the form of a swivel arm, increases speed, cleanliness and employee safety.
- Further machine optimization using the latest technology leads to a doubling of speed.
- The overall height of the Roto-Packer is reduced, depending on the model. The smaller size allows subsequent installation in existing, normal-height production halls.
- The patented and low-maintenance Roto-Lock dosing unit and SEAL technology for sealing valve bags increase cleanliness immensely and leads to greater employee safety and environmental protection. The Adams technology for filling PE bags expands the range of products to include sustainable and environmentally friendly packing technology.
- Digitization takes hold. The Roto-Packer becomes the central control of an entire packing line and can be monitored by the QUAT2RO system at any time and from anywhere in the world.
Roto-Packer sets the pace
In its six decades of development, the Roto-Packer became the heart of countless packing lines worldwide. In combination with other units such as the Radimat automatic bag applicator, a palletizer or a truck loader, the Roto-Packer ensures a perfect flow of filled products and continuous output. Today, there are four expandable standard versions of the Roto-Packer with different filling systems: the Adams version for filling powdery bulk materials into environmentally friendly PE bags; the SEAL version for packing mixed products into sealable paper or PP valve bags; and the advanced and basic versions. With the expandability of the Roto-Packer and other modular solutions for the entire process, from storage to filling to loading, Haver & Boecker are able to meet all market requirements.
Roto-Lock and SEAL
In 2016 Haver & Boecker introduced the patented, low-maintenance Roto-Lock dosing device. This replaces the sliding plates connecting the filling chamber and the filling spout, thus removing a primary source of product loss in rotating systems. The rotating rising chamber completely eliminates product spillage during the dosing process and requires almost no maintenance. The Roto-Lock can be retrofitted to all original Haver & Boecker Roto-Packers built from 2000 onwards. SEAL technology can also be retrofitted to these units, whereby at the beginning of the filling process, a sleeve inflates in the specially designed filling spout and seals the valve bag so that no product can escape. After dust-free filling, the bag valve is ultrasonically welded shut. The compact and completely closed bag provides for a clean working environment for improved health standards for all plant employees as well as clean handling during the entire logistics chain and at the end customer.
Clean filling by Roto-Lock and SEAL increases process reliability and reduces wear and tear and production downtime due to cleaning, maintenance and repairs. The clean bags and attractive appearance also create a positive effect on company and product image, allowing the product to stand out at the point of sale and protecting the environment. Loss-free and clean filling means no product is wasted and resources are conserved.
Adams technology for PE bags
With Adams technology, Haver & Boecker have made it possible to fill powdery, bulk products into tight FFS film bags made of PE. The RST Adams version is a stand-alone system with two, four or six to 12 filling spouts. It combines the rotating process with the unique Adams technology for the compact filling of PE bags. Powdery products are compacted by special internal and bottom vibrators to such an extent that almost no air remains inside the bag.
The customer benefits from high weight accuracy, environmentally friendly packing and tight easily stackable bags. The Adams version of the Roto-Packer is also suitable for filling micro-granulates in package sizes from 5kg to 50kg, which means it can be used efficiently in the cement and building materials industry.
Radimat for perfect flow
As an optional module, the Radimat automatic bag applicator automates the packing of products into valve bags on rotating packing lines. All common rotating packing machines on the market – including those of other manufacturers – can be retrofitted to operate with the Radimat, thus optimizing the entire packing process. With a shot rate of up to 99.7%, the Radimat shoots the bags in the packing machine’s work cycle. The empty valve bags are automatically drawn from a magazine or from a roll. This makes the entire packing process independent of the work quality of the machine operator, who is now free to perform more important and safer tasks.
The Radimat is suitable for systems for packing a wide range of loose materials in bulk and can be installed in existing plants or for scaling down new plants. Components such as rotary tables, elevating systems and different magazine arrangements allow installation variants to be adapted to the available space.
QUAT2RO system monitoring
With optional intelligent LED diagnostic lighting, the operator can view the system’s status from a distance at a glance (blue = in operation, red = malfunction, white = open doors) and thus react without delay. Moreover, the entire packing process can be observed and analysed with Haver & Boecker QUAT2RO system monitoring, which can be retrofitted to all systems. With QUAT2RO, companies can take effective precautions against lengthy periods of downtime and high maintenance costs. Real-time production and maintenance information can be called up at any time on a computer, tablet or smartphone. The responsible personnel are thus able to access the plant’s progress and visualized performance data at any time and from anywhere in the world via an encrypted connection, allowing the causes of possible deviations to be identified more quickly and maintenance to be planned at an early stage.
For more information, visit: www.haverboecker.com
- Subscribe to Quarry Management, the monthly journal for the mineral products industry, to read articles before they appear on Agg-Net.com