Hassell At Needingworth
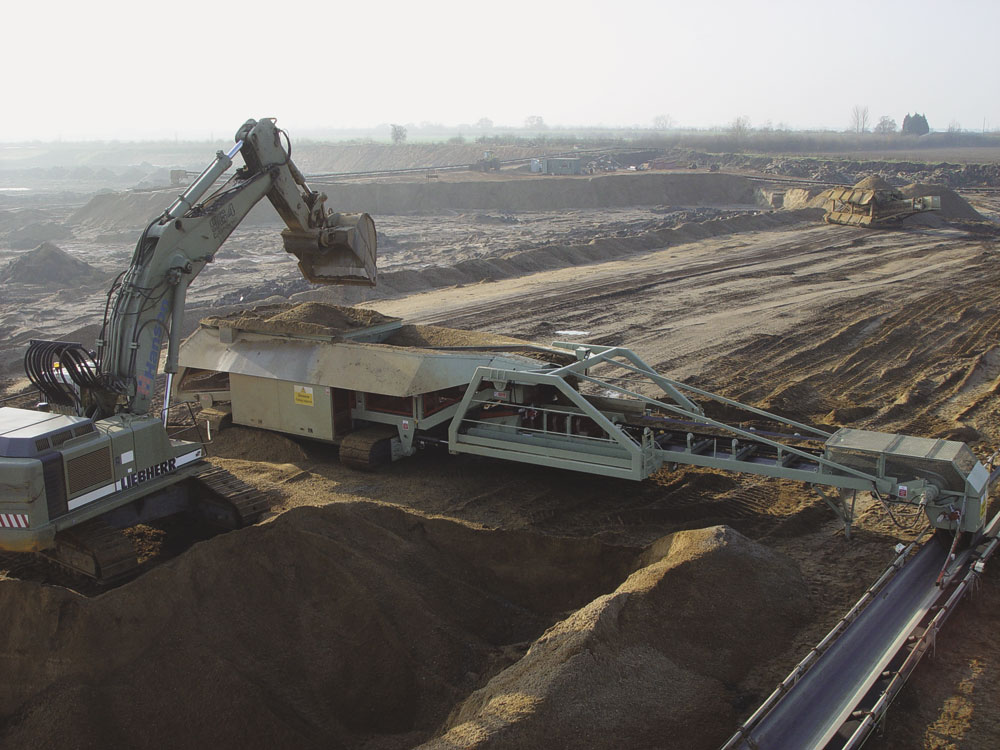
Hanson take delivery of bespoke hopper feeder
E.H. Hassell have delivered an DF 1200L heavy-duty tracked hopper feeder to Hanson Aggregates’ Needingworth Quarry in Cambridgeshire. The first bespoke feeder of this type was delivered to Hanson’s Bulls Lodge Quarry two years ago where so far it has handled around two million tonnes of material at a rate of 650–700 tonnes/h. A second machine with a throughput of 200–250 tonnes/h and featuring an integrated Finedoor grizzly screen has also been installed at RMC Aggregates’ quarry at East Leake in Nottinghamshire.
Initial discussions between Hassell and Needingworth Quarry started two years ago, but began in earnest 10 months ago, with final order to delivery taking just six months. Hassell always work in collaboration with their customers to build high-specification units using high-quality components. At Needingworth, Hanson management, engineers and site staff were all included in the consultation process.
The new HDF 1200L tracked hopper feeder was designed and built at Hassell’s factory in Stoke-on-Trent. It replaces a skid-mounted feeder that, on a good day, took around 20min to move into position as the face progressed. Three separate items of equipment had to be moved using chains attached to an excavator and as two or three moves were required each day, this resulted in increased downtime as well as a number of health and safety issues. The new track-mounted feeder comprises just one piece of equipment and is fully remote controlled, propelling itself in seconds and allowing it to be moved into a new position in less than 5min. This has improved health and safety on site, increased throughput and so improved the payback on Hanson’s investment.
Commissioned in early October, the hopper feeder was transported to the site in two pieces. It was then assembled and moved to the face in just half a day. Three site operatives have been trained to operate the unit, which runs 9h a day on a 9.5h shift.
Designed to process 1 million tonnes a year for 30 years, the HDF 1200L has a feed rate of 650 tonnes/h, weighs approximately 50 tonnes and has a travelling speed of 0–3km/h. The 900mm wide tracks, supplied by Strickland, provide the unit with low ground pressure, essential for this type of terrain.
A 8.8m3 capacity feed hopper discharges material on to a 1,200mm wide drag-out conveyor fitted with a Westweigh belt weigher. This inturn discharges on to a 1,000mm wide secondary conveyor and finally on to the 1.5 mile long field conveyor. The second conveyor is mounted on an independent swinging gantry that allows it to be moved up and down for correct positioning over the field conveyor to avoid any spillage. It is also fitted with a Rotech belt-speed sensor that instantly shuts down the entire machine if the field conveyor stops. Both conveyors are fitted with Hosch belt scrapers and Interroll rollers. The hopper is lined with abrasion-resistant plates and has a radio-controlled tilting grid that rejects any oversize material over the back end.
Due to Needingworth’s remote location a totally hydraulic drive system was specified. A Cummins diesel engine provides 155hp at 2,200 rev/min for the hydraulic power pack that drives the track motors, conveyors and reject grid. With a 1,000-litre capacity fuel tank, refuelling takes place once a week. A 1,000-litre capacity hydraulic reservoir provides cooling, assisted by twin cooling fans. The hopper feeder also incorporates an integrated 24V PLC control system.
The cut at Needingworth is currently 600m long and 3m deep. The hopper feeder at 20m long provides a 30m wide cut and is moved, on average, three times a day. Controlling material spillage was another key factor in the design of the unit, which is just 3m high. This helps to reduce the amount of spillage when material is loaded into the hopper by a Liebherr 964 Litronic excavator, which is fitted with a 4m3 (8-tonne) bucket. This low-level design also means that the excavator can be positioned further back from the feeder to give the required cut width.
The hopper feeder features an auto-lube system that is refilled once a week. Servicing is carried out by Hassell engineers who take oil samples, change hydraulic fluids, and service the hydraulic drives, engine, track motors etc. An initial service was carried out after 250h with subsequent service intervals taking place every 500h.
There is good all-round ground-level access, removing the use of portable ladders. The hopper feeder is fully guarded and is quieter than the excavator that feeds it. Hanson specified the fitting of a bbs-tek ‘shh shh’ alarm to alert site operatives when the hopper feeder is being moved and at conveyor start-up.
Management and staff at Needingworth Quarry are very impressed with the overall performance of the hopper feeder, the ease with which it can be moved around the site and the back-up service provided by Hassell. One of the site crew joked: ‘We now argue over who is going to move it.’