Operational Functionality of New Rolling Bearings
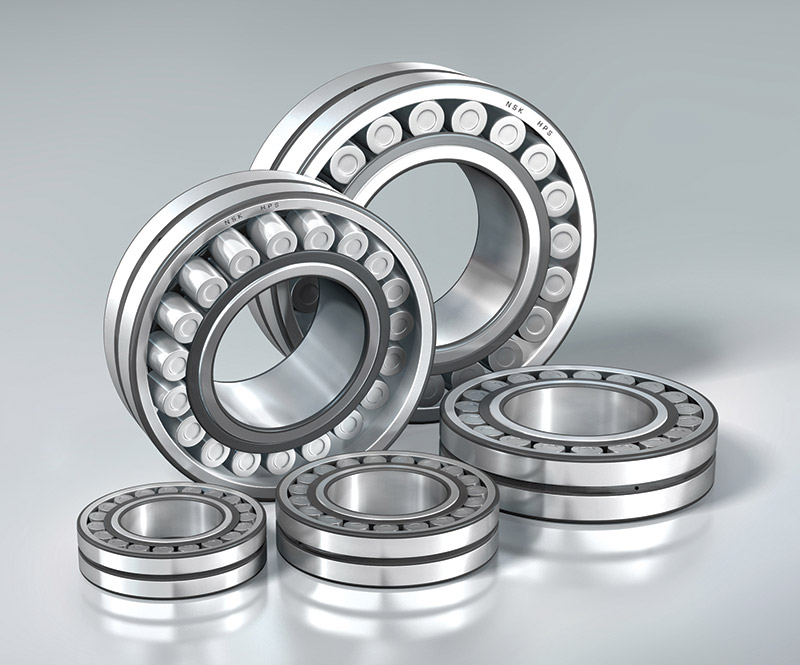
First published in the September 2014 issue of Quarry Management as Handle with Care
Malcolm Watson of Brammer and Tony Synnott of NSK discuss best practice in mounting, handling and checking the operational functionality of new rolling bearings
When mounting, checking or handling a bearing, the process needs due care and consideration in order to ensure the product’s longevity and effectiveness. If they are not handled correctly, bearings can be prone to failure quickly and unexpectedly, but some basic checks will help avoid some of the common problems associated with their handling and usage.
As rolling bearings are high-precision machine parts, they must be handled carefully. Even high-quality bearings will not deliver the desired service life and performance quality if they are not handled and maintained correctly.
However, observing a few basic precautions will help negate the possibility of premature failure. First, the bearing and its surroundings must be kept clean. The presence of any dust and dirt – even particles not visible to the human eye - is one of the key causes of bearing failure.
Bearings must also be protected from corrosion. Perspiration on the hands and a variety of other contaminants may cause corrosion, so hands should be clean and dry before handling bearings, with gloves worn if possible.
Care should also be taken when handling the bearing itself. Heavy shocks can scratch or cause other damage to the bearing, while physical impact may result in brinelling, breaking or cracking.
Proper tools should always be used for any work involving bearings – general-purpose tools wherever possible should be avoided. The manufacturer’s instructions are generally the best place to start for a guide on handling bearings.
Mounting
The mounting process is key to the bearing’s running accuracy, life and performance, so the manufacturer’s mounting instructions should be followed precisely. Failure to do so could result not just in premature failure, but in damage to other components, unscheduled downtime and invalidation of the product warranty.
In the first instance, the bearing and any surrounding components should be thoroughly cleaned and dried, with the dimensions and finish conditions of related parts subsequently checked. The mounting procedure should then be followed.
Since most bearings rotate with the shaft, the bearing mounting method is often an interference (tight) fit for the inner ring and shaft, with a clearance (loose) fit for the outer ring and housing.
The correct type and quantity of lubricant should be applied. After mounting the bearing, an operating test should be undertaken to verify that the mounting has been carried out correctly.
Checks and common faults
On small machines that are operated manually, the bearing should be turned by hand. Checks should be made for stick-slip as these will be manifested in the form of debris, cracks and dents. Uneven rotating torque indicates faulty mounting, while excessive torque again shows either a mounting error or insufficient radial internal clearance.
Once these checks have been completed, the machine should be turned on and operated at a low speed without a load, gradually increasing the speed and load till the typical rating is reached. Checks should be made at this stage for irregular noise, bearing temperature rise, lubricant leakage and lubricant discoloration.
Several types of noise may be heard. A loud metallic sound can be caused by abnormal load, incorrect mounting, insufficient or incorrect lubricant, or contact with rotating parts. A loud regular sound can be the result of brinelling/flaws, corrosion, scratches or flaking on the raceways. Meanwhile, an irregular sound will be heard in the event of excessive clearance, penetration of foreign particles or flaws/flaking on balls.
An abnormal temperature rise is frequently the result of lubrication issues – either too much or too little, or the wrong type. However, it can also be caused by abnormal load, incorrect mounting, ‘creep’ on the fitted surface, or excessive seal friction.
Brinelling, flaking, incorrect mounting and foreign particle penetration can all contribute to excessive vibration or axial runout. Lubricant leakage or discoloration is usually the result of overzealous application or the ingress of foreign matter and abrasion chips.
In the event of any of these occurring the appropriate remedial action should be taken immediately. Failure to do so will almost inevitably result in failure of the bearing, with the likelihood of associated damage to other components.
Once the bearing has passed all these checks and is fully operational, it is best practice to check the bearings on a regular basis with the aim of identifying any damaged or failing components as early as possible.
For further details visit www.brammeruk.com or www.nskeurope.com
- Subscribe to Quarry Management, the monthly journal for the mineral products industry, to read articles before they appear on Agg-Net