Large-capacity hoist installations
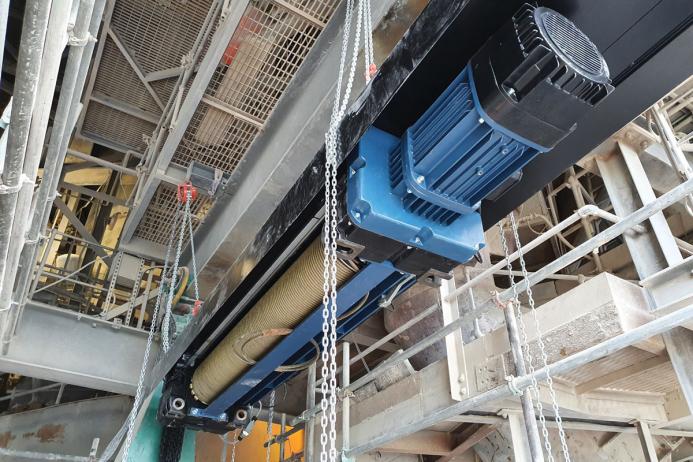
First published in the September 2023 issue of Quarry Management as Making Safety and Reliability Count
Hoist & Winch Ltd continue to raise the bar in challenging, large-capacity hoist installations
Supplying, installing, load testing, and LOLER (Lifting Operations and Lifting Equipment Regulations) certifying a wide range of manual and powered hoist units, Hoist & Winch have extensive experience and expertise in all kinds of industrial lifting operations.
However, certain projects require special know-how, such as the installation of large-capacity, electric-powered wire-rope hoists in challenging and restricted access applications. And yet even in these situations, Hoist & Winch have a proven methodology to ensure a high-performance, efficient, safety-certified outcome for customers.
Every hoist installation is different and most generally present some level of challenge to overcome, typically relating to the dimensional clearances of the hoist unit or the logistics of general access conditions.
When the hoist unit’s dimensional clearances are particularly critical, Hoist & Winch tend to carry out a detailed survey prior to manufacture, ensuring that the complete installation can perform the required tasks with sufficient operating clearance.
On some occasions, a pre-installation survey is required to check site/work area access conditions. Hoist & Winch will subsequently submit their Risk Assessment and Method Statement (RAMS) for approval by the customer prior to starting work.
These documents detail the installation procedure, the equipment intended for use, and the hazards and risks associated with the various tasks. In addition, the documents will set out how it is possible to minimize or negate these risks.
A recent cement plant project involving challenging installation access conditions highlights how the capability and knowledge of Hoist & Winch proved extremely useful in delivering a successful outcome for customers.

This complex project involved replacing an obsolete, 10-tonne SWL (safe working load), electric-powered wire-rope hoist unit with 60m lifting height. The task was required ahead of the cement production facility carrying out extensive modification work to its pre-heater tower.
The pre-heater tower is 100m high and the existing hoist unit was located at the 60m level on a monorail beam that cantilevers out of the building for approximately 8m. Both the obsolete hoist unit and monorail beam had been dormant for many years, which meant that Hoist & Winch’s scope of supply included the load testing and thorough examination of not just the new wire-rope hoist unit, but also the monorail beam.
Among the first tasks was removal of the existing wire-rope hoist unit, which weighed 3 tonnes. Hoist & Winch decided to cut this down in sections using gas-burning equipment, as many of the hoist parts were badly seized and not easy to dismantle in the conventional way.
Initially, the company removed these sections to a specially constructed scaffold work platform located below the hoist installation area. Each piece of the obsolete hoist was then lowered further to the nearest adjacent floor level, 16m below, using manual chain blocks, for movement to the goods lift access located on that level.
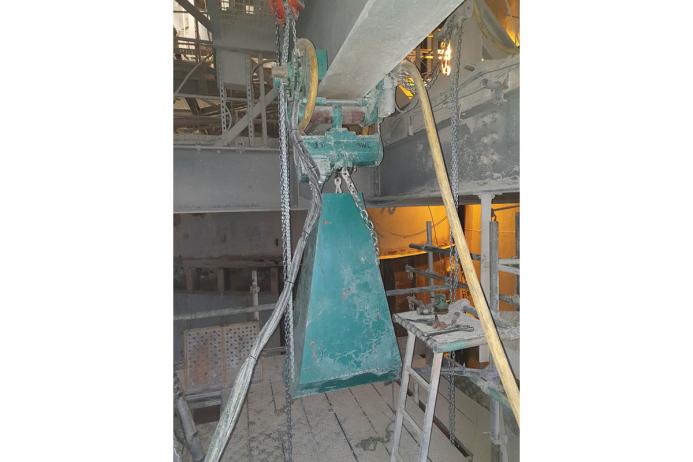
Next, Hoist & Winch had to install the new hoist (weighing 2.2 tonnes) in part-dismantled form. The company eased the difficulty of this task by installing a temporary 3-tonne SWL motor-trolley-mounted, air-powered chain-hoist unit on the monorail beam and raising the new hoist unit to the required 60m from the outdoor groundfloor work area.
Hoist & Winch took great care with the preparation of the chain-hoist unit to ensure reliability during the operation as any breakdown during the critical 60m lift would require special access equipment to help resolve any issues. The lifting equipment specialists also carried out meticulous checks on the quality, volume, and pressure of the air supply.
The next task was to raise the completely new hoist unit to the 60m installation level. From there, Hoist & Winch used the 3-tonne SWL motor-trolley-mounted, air-powered chain-hoist unit to transport the new hoist into the building and over the temporary scaffold work platform.
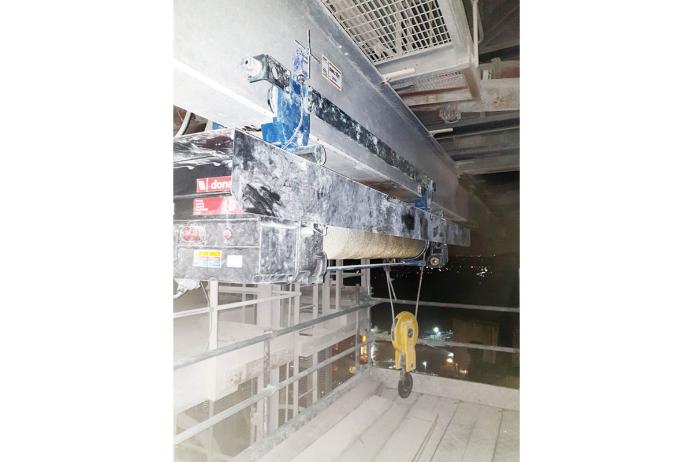
From this position – after first opening up the hoist unit trolley wheels wider than the monorail beam width – the company lifted the wire-rope hoist unit into position. To facilitate this task, the company deployed four 1-tonne SWL manual chain blocks suspended from each end of two specially fabricated lifting frames clipped into position on the top flange of the monorail beam.
The final tasks included electrical commissioning, assembling the hoist on to the monorail beam and the removal of all temporary lifting equipment. Hoist & Winch later performed dynamic load testing of the new wire-rope hoist unit and monorail beam, using a skid-mounted, certified 10-tonne test load prior to a LOLER Thorough Examination report.
As part of the dynamic load testing procedure, the outdoor cantilever section of the monorail beam was deflection tested in accordance with BS2853 using a special long-range, outdoor-operation Leica laser system mounted on a stable and adjustable tripod.
‘Manufacturing and process plants tend to evolve over time, often compromising general access to existing hoist installations,’ commented Andy Allen, director of Hoist & Winch. ‘In other instances, legacy hoists fall into disuse and become obsolete.
‘We’ve seen this on many occasions over the years, but with our in-house design, engineering and manufacturing skills, there is nothing we cannot overcome. If you are in this situation and could benefit from the input of an expert partner, please contact us for a no-obligation discussion about the potential solutions.’
For further information visit: www.hoistandwinch.co.uk
Subscribe to Quarry Management, the monthly journal for the mineral products industry, to read articles before they appear on Agg-Net.com