Condition Monitoring
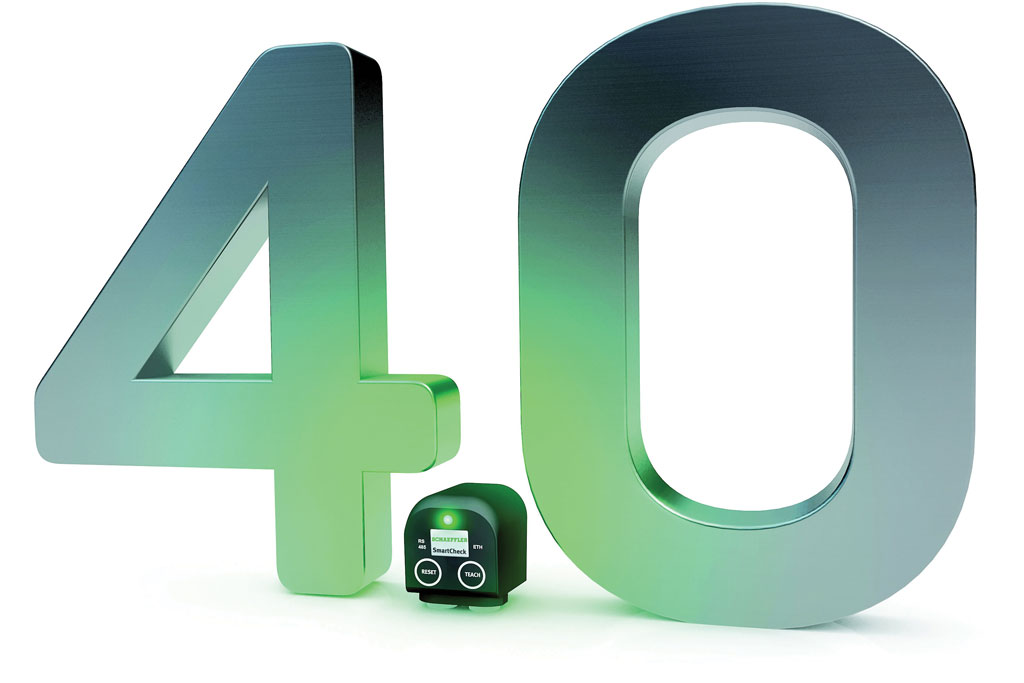
First published in the March 2019 issue of Quarry Management
A key part of Industry 4.0 and the ‘Dark Factory’ - While condition-monitoring (CM) systems are continuing to prove their value in industrial applications, many companies are still unsure how CM should fit into their Industry 4.0 strategy and the automated ‘lights-out’ factory, says Ian Pledger, service engineer at Schaeffler UK.
In the UK, most process industry sectors have now implemented some sort of condition monitoring (CM) strategy or CM systems within their process plant, even if it is just CM for process-critical rotating equipment and machines. The sectors that seem to be adapting best to CM are those that cannot afford the high costs associated with production downtime, perhaps due to an unforeseen machine breakdown. These sectors include mining, quarrying and cement.
Outside of the process industries, discrete manufacturers in the automotive, aerospace, wind power and rail industries are also benefiting from the implementation of CM systems. In fact, any business that utilizes electric motors, gearboxes, air compressors, fans, conveyors and pumps can benefit from CM services.
Measuring vibration is one of the most widely used CM techniques for detecting and diagnosing equipment faults. Vibration-monitoring systems are one of the most reliable methods of monitoring the condition of rolling bearings and for detecting the early onset of damage to bearings and other machine components. Schaeffler have many years of experience as a manufacturer of bearings, and as a provider of CM systems and vibration-analysis expertise.
Most CM systems to date have been used as local systems, collecting vibration data from machines and using analysis algorithms and a rolling bearing database to check for signs of wear, defects or other unusual behaviour. While this works very well for many companies, it is now possible to share and compare local machine condition data, via the cloud, with other similar items of equipment across a plant, or better still, with other equipment at multiple plants within a business, wherever they are located globally.
Minimal skills, knowledge and experience required
The latest Cloud-capable CM systems from Schaeffler, such as Smart QB and SmartCheck, offer a suitable platform for managing and processing ‘Big Data’. These CM systems are quick and easy to install and set up, with the user requiring no specific skills or knowledge of vibration diagnosis.
With the Smart QB fixed online monitoring system, when changes occur in the condition of the equipment, the system automatically generates plain text messages on a display, providing the user with clear instructions for action, allowing any corrective maintenance work to be undertaken and any replacement parts to be ordered if required. These ‘automatic fault-assessment’ CM systems are groundbreaking, as they do not require specifically trained vibration experts to analyse the data.
With ready-to-use, preset measurement configurations, these CM systems are helping users identify the main causes of faults, eg bearing damage, imbalance and temperature increases. For general changes in vibration patterns that cannot be clearly attributed to one of the above, the CM system can request, via the Cloud, additional analyses from a specialist.
The advantages are that analysis can now be carried out anywhere at any time, with the expert being located anywhere in the world within a company or external. Similar equipment can be compared across global manufacturing plants, to compare and/or develop trends.
Digitalized Industry 4.0 technologies
Schaeffler’s components, such as bearings, are used in important parts of plant and machines that produce critical information about conditions and movements. Schaeffler are continuing to invest heavily in research and development and have incorporated sensors, actuators and control units with embedded software into their products, including rolling bearings and linear guidance systems. With these new, digitalized Industry 4.0 technologies, it is now possible for these products to collect and process valuable data on the condition of a machine or process and then convert this data into added-value services.
Schaeffler’s Cloud-capable SmartCheck CM device, for example, allows a simple and flexible point of entry into the digitalization of machines and equipment based on vibration monitoring.
Enablers for digital services
Components equipped with sensors are central to the drive systems used in machines and equipment – they record data and are the fundamental ‘enablers’ for these digital services. Schaeffler’s aim is to continuously transform conventional mechanical products such as bearings and integrate these into the digital world. This represents an important step towards a future in which not only complex systems, but also simple assemblies and machines will have easy access to digitalization and the Internet of Things (IoT).
The recorded vibration data from bearings can now be transferred, via a flexible Schaeffler Gateway, to the Schaeffler Cloud, where Schaeffler’s rolling bearing domain expertise is made usable in the form of digital services. For example, automated rolling bearing diagnosis and ‘remaining useful life calculations’ can be used to provide precise information on the condition of the bearing and, therefore, of the machine or process being monitored, which, in turn, allows specific actions to be recommended. It will even be possible to use actual load data to make adjustments to operational machine processes in real time.
But what are the implications on the workforce? Over the next decade, engineers will spend less time diagnosing faults on machines and process plant, as this data will be collected and reported on automatically using smart CM systems. Collected CM data can be provided in a format suitable for whoever needs to see the data within the business or global group. Different process engineers, maintenance staff, machine operators and senior plant managers will cherry pick the information they need from this pool of machine and process data and use it as they see fit to make improvements to processes, machine efficiencies and, ultimately, business profit.
Where is the catch?
There are some drawbacks to implementing modern CM systems, but these should not prevent companies investing in CM. The cost of the CM system itself and its implementation can appear relatively high at first. However, the cost of implementation is likely to decrease over the coming years as these systems become easier and faster to install, as well as less costly to develop in the first place. As CM technologies mature, the price of CM systems will decrease. Small, affordable CM devices such as the Schaeffler SmartCheck are already making investment payback periods significantly shorter.
The Dark ‘lights-out’ Factory
Eventually, a ‘Dark Factory’ situation may emerge, whereby machines, automated plant and robots carry out all their work in an energy efficient, ‘lights-out’ scenario, where there is little or no human intervention required, except when a CM alarm limit on a machine or process is reached, new raw material is required for the process, or a machine breakdown occurs.
Condition monitoring will continue to remain at the forefront of fault diagnosis and Industry 4.0 and the IoT will continue to drive the way CM technologies are developed.
For more information, visit: www.schaeffler.com
- Subscribe to Quarry Management, the monthly journal for the mineral products industry, to read articles before they appear on Agg-Net.com