Committed To Service
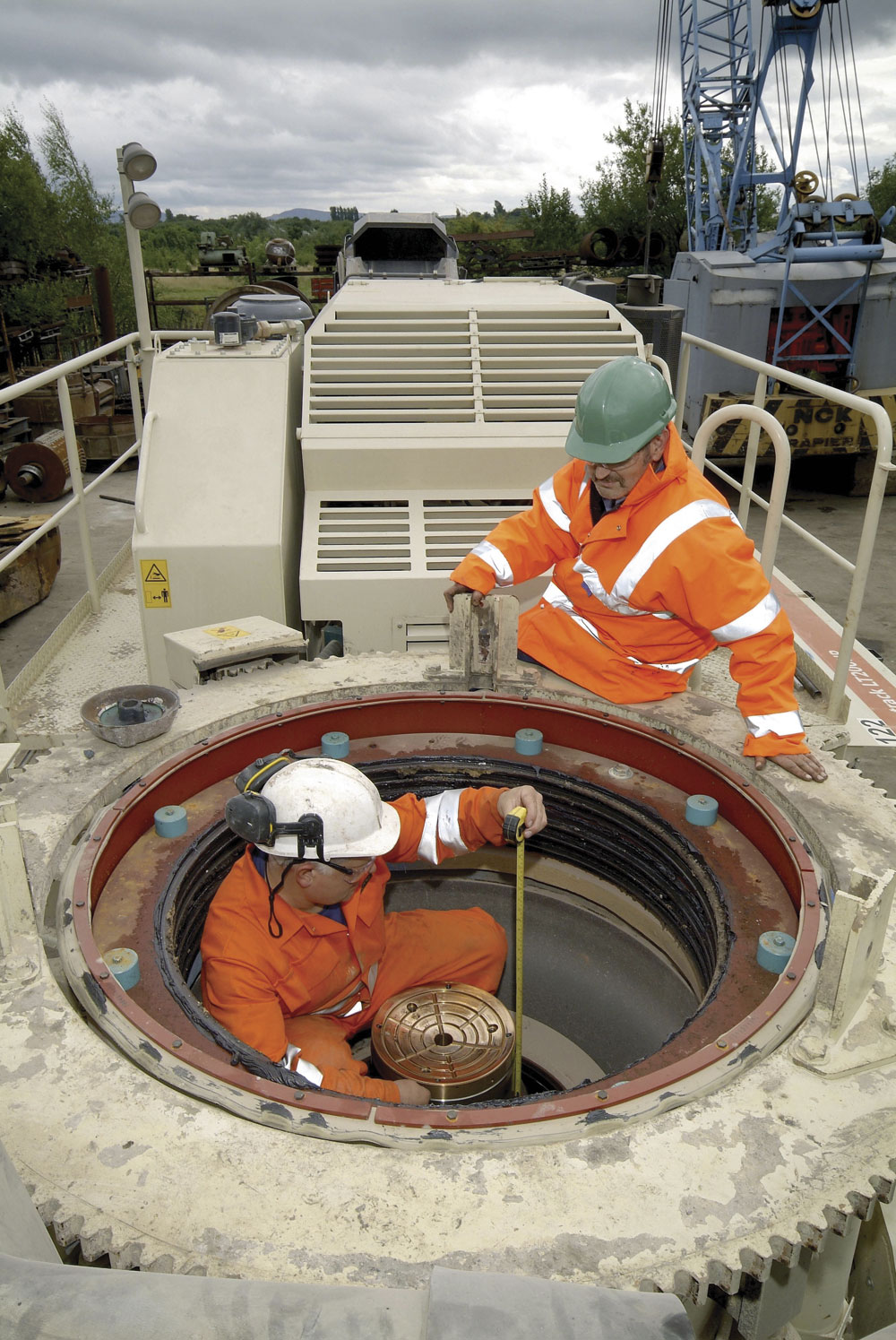
Metso Minerals offer an expanded range of differentiated support services tailored to individual customer requirements
In recent years there has been a growing trend for quarry operators to transfer responsibility for key tasks such as plant optimization, maintenance and repairs to their plant and equipment suppliers. This trend is set to continue as new equipment becomes steadily more complex and customers look for an increasing return from their business investments.
Metso Minerals’ after-sales support services already cover the entire life cycle of the machines in their extensive product line, but to meet the changing needs of their customers the range and scope of these services has steadily increased in recent years as customers have demanded ever more effective equipment-management solutions that allow them to optimize the performance and reliability of their equipment, while lowering their operating costs.
By offering a broader range of differentiated customer support services, ranging from advice on system selection and acquisition to a full line of equipment-management services that can be tailored to individual customer requirements, Metso Minerals say they are demonstrating a commitment to ‘operational excellence’. The extended range of services now available includes:
Process optimization: This begins with a survey of a customer’s existing operation to identify areas with the greatest potential for process improvement. Metso then combine their process expertise with the use of plant simulation tools to devise a solution. In many cases a plant can be optimized by making minor changes to the process while incorporating existing equipment, while older plants may benefit from the installation of new, more technologically advanced equipment.
Inspection service: This helps improve equipment availability and reduce operating costs by identifying faults or unusual wear patterns. Experienced Metso engineers conduct an inspection and condition analysis of the equipment and supply a detailed report on the condition of key components and wear parts together with projections of when they will have to be replaced. The service is available on a one-off basis or as part of comprehensive preventative-maintenance agreement.
Maintenance and repair service: To increase plant availability and life, Metso offer a range of maintenance and repair programmes tailored to individual customer needs. These include routine servicing and maintenance work through to comprehensive repair and maintenance agreements covering all aspects of equipment servicing and maintenance, including the planned repair/replacement of worn or unreliable parts and components.
Certified repair and rebuild services: This newly introduced service provides a cost-effective solution for UK and Irish customers looking to extend the life of their crushing equipment. A major feature of this service is that all the products are repaired or rebuilt to agreed specifications using original engineering drawings and Metso-certified parts (see box 1)
Wear parts replacement service: This all-inclusive service allows customers to optimize the performance and life of their wear parts by planning for their replacement. This is achieved through regular inspections by Metso Minerals engineers who recommend how and when replacement should take place.
The wear parts are then delivered to site and replaced at a time to suit the customer.
Customer training service: Tailored customer training packages covering the operation and/or maintenance of Metso equipment are available to suit specific customer requirements. Topics range from basic equipment maintenance through to total plant optimization.
Equipment protection plan: This new initiative is incorporated in the original sales agreement and covers a wide range of components in Metso crushing and screening machines. Periods of extended cover ranging from three years or 6,000h up to five years or 10,000h are available (see box 2).
Performance-based service: This service allows customers to transfer responsibility for plant optimization, maintenance and repairs to Metso Minerals, providing a complete operation and maintenance package to ensure that required production and availability targets are achieved over an agreed contract period. Backed by availability and production guarantees, the service is offered on either a cost-per-hour or cost-per-tonne basis.
Commenting on their expanded range of customer support services, Metso Minerals (UK) Ltd’s managing director, David Moon, said: ‘More and more quarrying companies are looking to outsource the non-core aspects of their business; they want to share and transfer responsibility for service, maintenance and repair. Metso Minerals are committed to providing customers in the rock and minerals-processing industries with total solutions to their business requirements. We are demonstrating our commitment to ‘operational excellence’ by offering an expanded range of differentiated support services that can be tailored to individual customer needs and cover the whole life cycle of their machines.’