The Five Factors of Fuel Efficiency for Earthmoving Plant
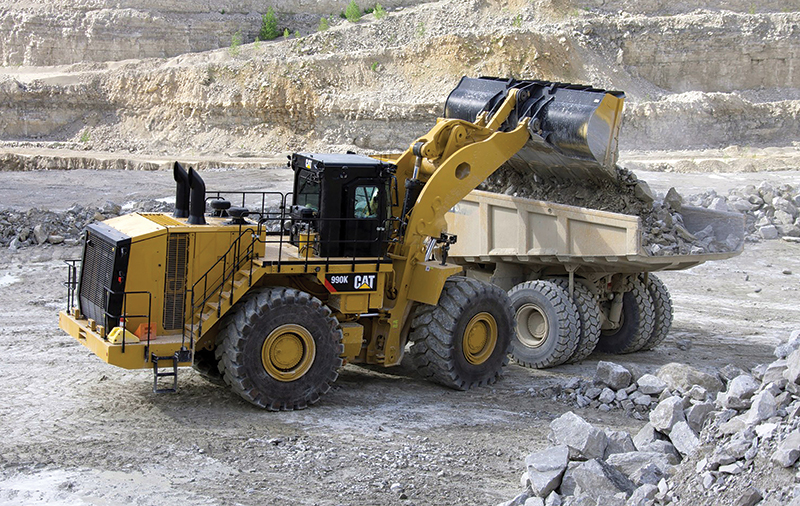
First published in the November 2015 issue of Quarry Management
Fuel expense accounts form a significant proportion of the total machine operating cost in earthmoving plant and equipment. Jason R. Hurdis describes the five factors that can determine fuel efficiency and outlines the steps aggregate producers can follow to reduce their fuel consumption.
Fuel expense in owning and operating aggregates equipment is a constant and will account for about 50% of total machine operating costs. Fuel prices have recently been on the decline, but based on history this trend will soon reverse. The International Energy Agency recently warned that steadily falling oil prices ‘could deter investment in production, which will eventually hurt supply’.
With the unpredictable nature of fuel prices and the absolute necessity of fuel for business operations, most aggregate producers have simply looked at how much fuel they are burning and paid the bill. Recently, technology has changed. Now, with the addition of production data, producers can look at their fuel efficiency (how they are using fuel) and know its impact on the bottom line.
Fuel efficiency incorporates the amount of fuel burned, but its final value is dependent on several factors. These factors, or fuel-efficiency influencers (see fig. 1), can be categorized as follows:
- Idle time
- Operator technique
- Quarry site set-up
- Equipment selection and configuration
- Technology
This article explores each of these influencers in detail, explaining the parameters and the overall interaction on fuel efficiency.
FUEL EFFICIENCY
Fuel efficiency is defined as material moved (work) in a time period divided by the amount of fuel consumed to move the material in the same time period. The fuel-efficiency formula for aggregates equipment is:
Fuel efficiency = Material moved per unit of time ÷ Fuel consumed per unit of time
To put this formula into plain terms from an application point of view, material moved, also known as productivity, is measured in tonnes or cubic metres; fuel consumed is measured in litres (or gallons) used to move the material; and the unit of time for fuel efficiency is an hourly measurement, which results in units of tonnes per litre or cubic metres per litre.
Based on this, improvements in fuel efficiency are achieved by either increasing the productivity while retaining the same amount of fuel consumed, or reducing the fuel consumed while retaining the same productivity level.
Idle time
Equipment idle time is one of the largest and generally most misunderstood influences on fuel efficiency. Idle time is defined as fuel being consumed with no work or productivity.
Idle time in aggregates applications is impossible to avoid because of equipment warm-up and shutdown requirements. Industry studies show equipment idle time can be as much as 40–50% of total operation time. Idle time results in a direct expense to companies’ profit margins. Table 1 shows a simple example of idle time cost.
It is obvious idle time has a direct impact on fuel consumption. Indeed, when idle time is reduced, hourly fuel consumption is actually increased. This relationship is often confusing to users, because the general thought is if the equipment is idling less, the hourly fuel consumption should decrease, not increase. This phenomenon is best explained by understanding the relationship between idle time, working time, productivity, fuel consumption and fuel efficiency (see table 2).
While some equipment idle time is unavoidable, it can still be controlled or minimized. The following are effective methods to reduce idle time:
Education: Reviewing fuel-consumption data and fuel costs with employees helps educate them on idling effects on the equipment, overall operation, environmental stewardship and company profits.
Limit warm-up time: Equipment warm-up time at start of shift varies with ambient conditions, but a rule of thumb from the US Environmental Protection Agency (EPA) indicates warm-up times can be limited to between three and five minutes.
Implement a 5min idle rule: If equipment idles for more than 5min, shut it down to save fuel. Restarting equipment uses less fuel than idling, considering most aggregates equipment consumes an average of almost 4 litres/h at idle. Most aggregates equipment manufacturers offer, as standard or as optional equipment, shutdown timers that automatically shut off machines after 5min or other user-defined time periods.
Limit cool-down time: Equipment should be idled at end of shift to allow turbochargers and emission systems to cool and purge. As another general rule, idling for 2min at the end of the shift will allow most equipment to reach optimum shutdown temperatures. Newer aggregates equipment has automatic shutdown features that control this time and process for the user.
Idle-management systems: Some equipment comes with ‘auto-idle’ or ‘engine idle management’ systems. These systems monitor equipment parameters and automatically reduce engine revolutions per minute (rev/min) to idle rev/min or below normal machine idle rev/min. Using these systems can reduce idle fuel consumption to almost 4 litres/h.
Breaks and lunch: Studies and observations indicate equipment is left idling over breaks or lunch periods. The most frequent reason stated by equipment operators for doing this is to keep the cab environment at temperature, whether warm or cool. Systems such as engine-off cab heaters and coolers can reduce the ‘need’ to idle over breaks and lunch. Operator education and layout of break/lunch areas to production areas can be helpful too.
Monitoring asset utilization: Best practice today includes using telematics for monitoring equipment and utilization, to benchmark and identify opportunities to reduce idling time and enhance the fleet utilization.
Operator technique
The equipment operator’s experience, operating technique and application knowledge all equally influence fuel consumption, productivity and resulting fuel efficiency. One study indicates efficiency can vary by up to 40% between different operators on the same equipment in the same application. Caterpillar recently conducted a study using eight operators of various experience and skill levels on the same machine in the same application. A summary of the test results appears in table 3.
Table 4 shows results from studies conducted with various operator experience and skill levels with different-sized wheel loaders and track-type machines in the same application. The variables in these studies are derived from material engagement with loading device, equipment movement, interaction with equipment controls and engine/transmission/traction management, and experience with particular machine platforms.
As shown in these studies, fuel efficiency can also be dramatically affected by an operator’s experience, skill level and familiarity with a specific piece of equipment. Time frames for an operator to become comfortable with a particular piece of equipment can vary from a few hours to several weeks, based on experience and skill levels with similar types of aggregates equipment.
While operator proficiency levels vary, the impact on fuel efficiency can be reduced with aggregates equipment in any application. The following methods can be used to improve operator technique and achieve fuel-efficiency improvements:
Training: Operator training can be separated into two basic types: first, on-the-job training; and secondly, training simulators.
One method of on-the-job training is mentoring, using an experienced operator to train a less-skilled or inexperienced operator. Mentoring allows training on site with site machines and under site conditions while maintaining production, even if at a reduced level, during the mentoring period. A potential risk of mentoring is the progression of ‘bad habits’ from the trainer to the trainee.
Another method of on-the-job training is using equipment manufacturer training services. Equipment manufacturer training can be completed either in a controlled event, ie at a demonstration and training centre, or at the customer’s site on machines in the customer’s applications. Like mentoring, this type of training allows the trainee operator to experience environmental conditions, job site conditions such as gradients, manoeuvring restrictions and other equipment interactions he or she may encounter during daily work periods.
Either method of on-the-job training requires an investment in time and expense, but rewards can be quickly realized via improved production, equipment care and fuel efficiency.
The use of training simulators allows operators to develop basic control familiarity in a controlled environment without fear of mistakes, equipment hour accumulation, production interruption or fuel consumption. However, equipment simulators lack the feel, stability, visibility and environmental conditions that a real machine in a real application can provide.
Nonetheless, simulators can be valuable in new operator or continuous training programmes. The training duration and resulting fuel-efficiency improvements of either on-the-job or simulator training will vary based on the operator’s initial experience and skill level, commitment to improve and ability to retain techniques learnt during training.
Equipment features: Some equipment has built-in features and systems that automate control systems, traction-aid devices, transmission shift points and engine-hydraulic interactions, all of which the operator can select to enhance their performance and improve fuel efficiency. Recent features added to equipment include performance modes that adjust engine horsepower, hydraulic power, hydraulic speed and rimpull to improve fuel efficiency. As mentioned previously, systems such as auto-idle, engine idle management and others are rendered useless if an operator does not know how to engage or effectively use them.
Quarry site set-up
How the quarry is planned and set up is another fuel-efficiency influencer. Typically, it is planned far in advance, taking into consideration land acquisition, rights of way, material deposits, permitting and the production volumes required to make the site profitable. If there is not an effective and systematic approach to the initial job site planning, cost overruns, time delays and manpower expenses mount rapidly.
Quarry site fuel-efficiency influencers include the following:
Material location: This has the largest fuel and operational efficiency impact. Improper stockpile location requires load-out equipment to traverse the site to load customer trucks, which results in additional fuel consumption, additional equipment wear and operator fatigue. Safety issues such as blind spots can also arise from poorly planned stockpile placement.
Inadequate space: Where space is limited on site, stockpiled materials can blend together, which causes additional equipment cycling times and increased fuel consumption. Space constraints can also increase equipment transport distances, or ‘roading’, which consumes additional fuel and limits productivity.
Site roads: These can significantly affect aggregates equipment fuel consumption, productivity and fuel efficiency.
Equipment selection
Equipment selection is simply defined as having the right machine for the right application at the right time. If the machine is too large for the application, fuel efficiency can be reduced because the machine can potentially exceed production requirements, which may lead to additional material re-handling, extended idle time and operator inefficiency. If the machine is too small for the application, fuel efficiency is impacted because the machine will consume more fuel while trying to achieve production requirements.
To ensure the right equipment is selected for the application, the following should be taken into consideration:
Work tools: The work tool size and type affects digging or excavating performance, stability, cycle times and fuel consumption. If the work tool is too large for the machine, additional engine rev/min, hydraulic power, digging times and digging forces will result in higher fuel consumption. If the work tool is too small, productivity will suffer and, as such, additional cycles and fuel will be required to meet production requirements.
As a subset of work tools, ground-engaging tools are an important selection. Using the incorrect edge or tooth configuration can affect production, cycle times, operator technique, fuel consumption and fuel efficiency.
Application: Machines are designed for specific applications, such as loose-material truck loading, load and carry, face-material truck loading, below-ground excavation or utility work. While a single machine may be able to complete each of these applications, additional job set-up or support machines might be required.
Tyre selection: Studies conducted by tyre manufacturers indicate radial tyres result in up to 10% less fuel consumption. Tyre pressures also play an important part in fuel efficiency. Under-inflated tyres increase rolling resistance, which increases fuel consumption and can also affect stability, which affects productivity. Overinflated tyres can change the ride characteristics of a machine, affecting fuel efficiency via production losses from lost material during transport.
Machine features: Most equipment manufacturers offer fuel-saving and production-improving features such as variable work modes, fuel-management systems, traction aids, lock-up clutch torque convertors, load-sensing hydraulic systems and on-demand fans. These features can be adjusted/applied either by the operator or automatically based on application and environmental conditions.
Fleet or system match: Load and haul units need to be sized correctly to be the most fuel-efficient systems. As a rule of thumb, loading units should be able to load hauling units within four to six passes. Equipment dealers are a valuable resource and should be consulted to assist in machine selection.
Technology
Technology can also influence fuel efficiency. In this article, technology encompasses both telematics and equipment technologies. Each is equally important to equipment fuel efficiency.
Telematics: Such systems can be broken down into off-board telematics and on-board telematics.
Off-board telematics are equipment manufacturer or third-party services that provide individual machine or fleet information to site personnel. They provide site personnel with fuel information without additional labour to obtain the data via on-site measurement. This information allows site personnel to better understand their operations and analyse individual machines, operators and quarry site set-up to improve and sustain fuel efficiency.
On-board or on-machine telematics are machine-monitoring systems and displays providing the operator with real-time information such as productivity, fuel consumption, idle time and fuel efficiency. This information allows the operator to make adjustments to the operating technique or machine, to improve fuel efficiency in real time. The operator can also use this information with site management to assist in site improvements or to identify issues that may be affecting fuel efficiency.
Machine technology: Advances in equipment design and development have been rapid in the past five years. Several engines and machine platforms are now designed to deliver full power at lower rev/min, which reduces fuel consumption and emission packages.
Advanced technologies: Common in the automotive market, advanced technologies such as hybrids, electric drive, hydrostatic or continuously variable transmissions have been introduced in recent years. These machine technologies are creating double-digit fuel-consumption reductions with productivity levels equal to or greater than standard configured models in the same size and machine class. Several of these technologies also improve operator technique by automatically adjusting performance or transmission settings.
‘Add-on’ technologies: Technologies such as grade technologies and payload technologies can improve fuel efficiency. Grade technologies improve operator efficiencies and reduce unnecessary idle and fuel consumption. Payload control systems improve production, reduce idle time, reduce fuel consumption and improve operator efficiencies.
CONCLUSION
Idle time, operator technique, quarry site set-up, equipment selection and configuration, and technology all influence fuel efficiency. While one may be more visible or easier to control than another, all five must be understood, investigated and acted upon jointly to maximize fuel efficiency.
The author, Jason R. Hurdis, is senior market professional for the quarry and aggregate industry, on behalf of Caterpillar. First published in Aggregates Manager in July 2015 and reproduced in Quarry in Sept 2015, his article is reproduced here by kind permission.
- Subscribe to Quarry Management, the monthly journal for the mineral products industry, to read articles before they appear on Agg-Net.com