New Levels of Product Development for JCB
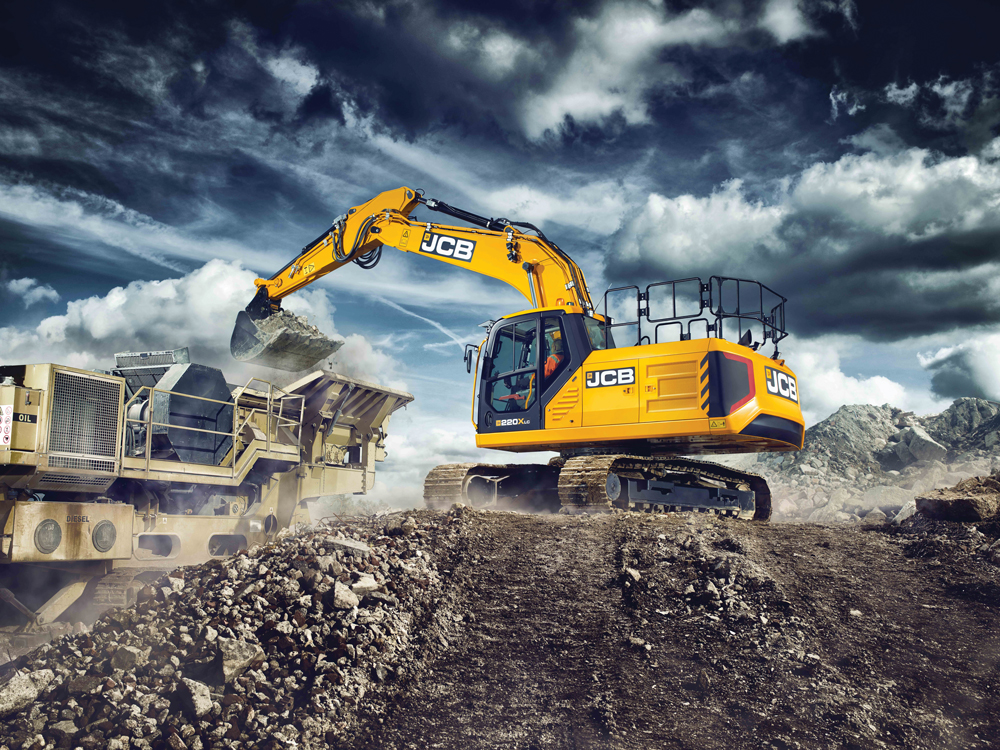
First published in the November 2018 issue of Quarry Management as Creature Comforts
Operator comfort — the design priority behind JCB’s new X-series excavator range
JCB have developed advanced new 220X crawler excavators, the first models in the next generation of JCB tracked machines for the global construction market. Over a four-year development period, JCB have employed a programme of intensive component and product testing to achieve increased levels of build quality and reliability for customers.
The new machines feature:
- 15% larger global cab with integral ROPS structure, offering reduced noise levels
- 200mm wider upper-structure delivering improved packaging
- Central main boom mounting for increased digging accuracy and durability
- Intuitive, ergonomically designed cab with simple user interface
- Stronger side doors for greater strength and increased protection.
JCB’s chief innovation and growth officer, Tim Burnhope, said: ‘With the next-generation 220X, JCB have moved to a totally new level of product development and machine assembly that will benefit all of our excavator customers in the field.
‘Every detail of these excavators has been examined and perfected to provide maximum durability and reliability in operation. But more than that, we have made it easier for the operator and for the service technician, reducing downtime for the customer and boosting profitability. The 220X heralds the arrival of a new generation of JCB excavators that will provide many years of faithful service across the world.’
Operator environment
There has been a total focus on the operator environment and the cab is a completely new structure, which will be used across the X-series range. It is 100mm longer and a full 1m wide, making it 15% larger overall than on previous machines. The cab incorporates the ROPS frame within the structure and has flat glazing all round. Most impressively, the 220X boasts an exceptionally low 68dB(A) noise level inside the operator’s cab, down from 73dB(A) on the previous generation.
The wiper motor is mounted to the bottom left-hand side of the front windscreen, to maximize visibility, whilst three all-new seat options – developed with suppliers Grammer –provide maximum comfort, with heating and ventilation among the options. The servo levers are mounted from the seat frames and therefore move with the operator, whilst the cab now sits on four new cab mounts for improved isolation.
The flat floor of the cab is easy to keep clean and even the rubber mat has been redesigned to assist with sweeping out. JCB have also provided an additional hour meter that can be seen from ground level outside the cab.
This attention to detail continues inside, as all of the controls have been ergonomically designed to be 100% operator-focused. To the right-hand side of the operator is an all-new command pod, bringing together all switches and controls into a single seat-mounted unit. A 7in tilt-adjustable monitor has been provided with intuitive menus and functionality. The monitor is accessed through an automotive-style rotary controller.
By combining the benefits of the screen and the command pod, which has a button for every regularly used function, tests have shown that an operator can carry out regular operations faster. The foot pedals, foot rests and tracking levers have also been redesigned to provide increased comfort, while the machines can be supplied factory-prepared for GPS excavation guidance, tilt-rotator and autolube, if required.
Durable design
The new 20-tonne class excavators herald a robust, purposeful new appearance that will be carried throughout the range. Designed and built to work efficiently and profitably, with durability and reliability built in throughout, the excavators have an upper-structure that is now a full 2.7m wide, 200mm broader than their predecessors.
The additional space has allowed JCB’s designers to mount the main boom in the centre of the machine, rather than at an offset, which reduces stress on the slew bearing and also permits the use of larger buckets without impacting the tracks.
To the right of the machine the handrail has been mounted inboard of the structure to prevent damage. However, if handrails are caught, they are now bolted in place, so can easily be replaced. The service doors are made from pressed double-skin steel with sturdy handles and a welded framework for added rigidity.
A pronounced skirt circles the upper-structure, providing a strong yet easily repairable profile to protect the new doors. All tanks are now mounted inside the bodywork, to further reduce the risk of damage, and even the counterweight has been designed to prevent knocks. There is easy access to a large tool box with integral refuelling pump with filter, while the AdBlue tank is positioned under a separate cover to prevent cross-contamination and to make it easier to refill.
On the left-hand side of the body there is an air inlet in just one access door, cutting external noise levels. A large cooling pack with standard wide-core radiators as standard comes with a removable fly-screen that is easy to keep clean. There is a storage area above the batteries and the machines benefit from a new consolidated IP69 fuse board located within the service door behind the cab. There is also ground-level access to the heating and ventilation system filter behind the cab door, and the machines can be supplied with optional LED lights inside the service compartments.
Increased efficiency
While much of the last decade has, for all manufacturers, put engine development at the centre of the engineers’ brief, the stability of Tier 4 Final and Stage IV legislation has allowed the JCB team to expand its remit for the new models. The company has stayed with proven Kawasaki hydraulic pumps and Kayaba valves, but has opted for larger spools and a latest-generation valve block for reduced hydraulic losses. The diameter of the main hydraulic hose to and from the main hydraulic valve has increased in diameter from 19mm to 25mm, giving greater flow without increasing the speed of the oil. Maintaining the speed of the oil in increased diameter hoses results in less wear and tear and, therefore, increases hose life.
Although the boom and arm are unchanged, JCB will offer the option of boom float with two modes to make grading easier and to reduce stress when operating a hydraulic breaker. The bucket ram will be available with an optional hose burst check valve and the grease points in the boom and arm have been grouped together to reduce service time.
Research and development
JCB say they have undertaken the design and engineering of the new 20-tonne machines with quality and durability at the heart of every operation. The company benchmarked all leading competitors and collected more than 1,000 requirements from customers around the world. The team has spent four years honing the excavators, to make them both simple to operate and simple to service.
Perhaps not surprisingly, the excavators were designed using computer-aided engineering (CAE), however the team at JCB also used CAE to virtually build the excavators. Before any parts were ordered from suppliers, the production line knew exactly how to assemble the components, thanks in part to contributions from the staff on the assembly line.
A vast amount of endurance testing has been carried out, with every door opened and slammed shut more than 10,000 times to assess durability. In addition, electronic test rigs have been used to test every electrical component and, for the first time, JCB have put the entire 20-tonne excavator on an automotive-style shaker rig.
JCB say customers will also notice higher-quality paint finishes, as the designers have eliminated any sharp edges in the steelwork. The hot test that all machines undergo at the end of the assembly line has also been increased to fully test the machines. Even the way that the excavators are built has been changed, with 42% of the machine now constructed as sub-assemblies off the main line – double the previous amount. This allows for additional quality inspections and reliability checks, while simplifying the main line. For further information visit: www.jcb.com
- Subscribe to Quarry Management, the monthly journal for the mineral products industry, to read articles before they appear on Agg-Net.com