Michelin On Front Line At Back Lane
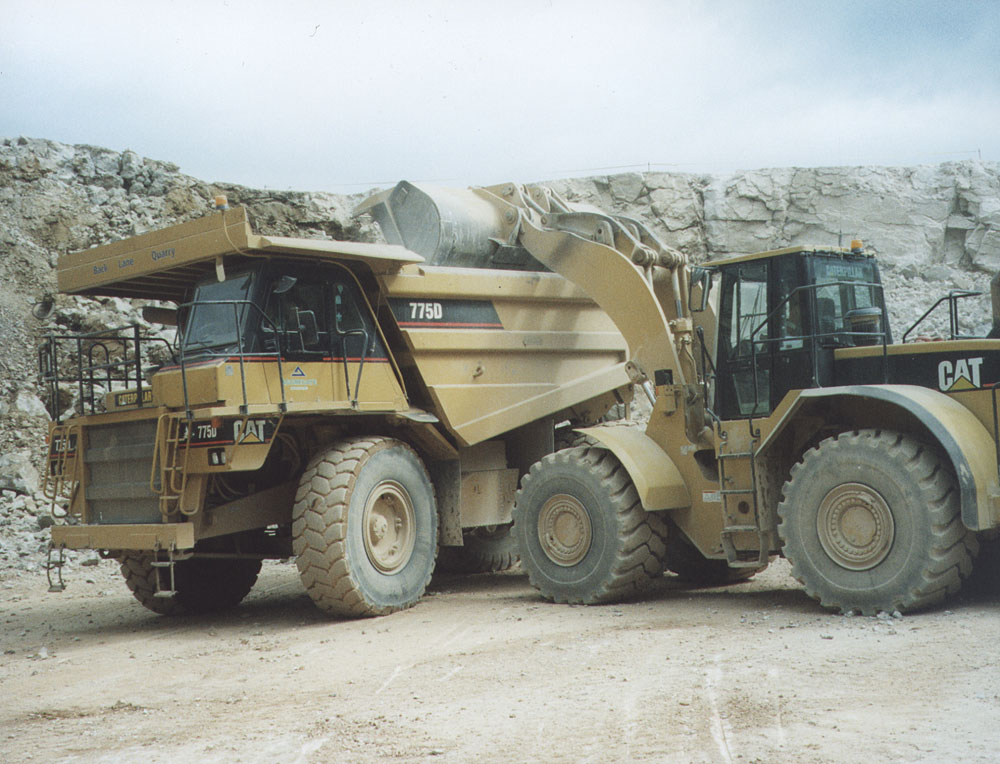
Bardon Aggregates introduce tyre management good practice
When Mark Morfoot took over as unit manager at Bardon Aggregates’ Back Lane Quarry near Carnforth in 1997, he inherited a mobile plant fleet shod with tyres from a variety of manufacturers, some of which were clearly in need of remedial action.
To eliminate the frequent and premature failures Mr Morfoot set about progressively changing and upgrading all the tyres to a carefully selected premium specification, and introduced a regime of good practice in tyre management. ‘It is nothing more than good housekeeping really,’ he says. ‘Planning ahead, monitoring and recording progress with routine checks, and instilling an awareness at all levels of both the importance of good tyre management and a sense of individual responsibility.’
He also firmly believes that buying cheap tyres is a false economy, as the short-term gain of saving on expenditure by buying the cheapest available can cost unaccountable thousands of pounds extra in the long run — in terms of disruption, lost production and an unpredictable maintenance budget.
In this area of management Mark Morfoot has a distinct advantage, as he came up through the ranks from a service/engineering background with hands-on experience of keeping quarry plant in operation.
One of the first problems he had to tackle at Back Lane was in the prime production area of the haulers. The 750,000-tonnes-a-year quarry uses two 50/60-tonne capacity Cat dumptrucks hauling from the face (a 773B and a 775D), with a third 773B on yard duties. It was apparent that the tyres were achieving an average life of only 4,500h.
Taking into consideration the working conditions in the hard limestone material and on the relatively long hauls of up to 1,200m each way, the tyres need to be resistant to impact and cutting damage, and have the durability to run the long uphill grades fully loaded. Traction and ride were other issues taken into account for the long-term running of the fleet.
With guidance from Michelin’s earthmover technical department, Michelin XDT dumptruck tyres with ‘A4’ hard rubber compound were chosen — a decision that has since been borne out in practice. ‘We have not only virtually eliminated punctures and the consequent troublesome daily emergencies, but we have practically trebled the tyre life to 12,000–13,000h. That equates to a cost of less than 30p per tyre per hour,’ says Mr Morfoot.
Other factors which he regards as important are the regular visits from Robin McAuslan, Michelin’s regional sales manager, and the three-monthly tyre inspections which help keep the records up to date and help spot minor problems before they become major ones.
A similar policy applies to the other mobile equipment at the quarry. For example, the Cat 980G wheel loader which works in the yard and at the quarry face (backing up a Cat 5080 hydraulic shovel) is fitted with Michelin XLD-D2 tyres which achieve a life of 8,500h in a fairly aggressive application before being changed. Another Cat loader, a 966F which carries out general truck loading and stockpiling in easier conditions, is running on Michelin XRD1s which have clocked up some 16,000h.
‘The evidence speaks for itself,’ says Mr Morfoot. ‘For some quarries perpetual tyre problems can be a nightmare, but we have proved that with careful selection and proper management the tyres can give the service you would expect, reduce risk and actually save money.’