Gas Oil – Are You Seeing Red?
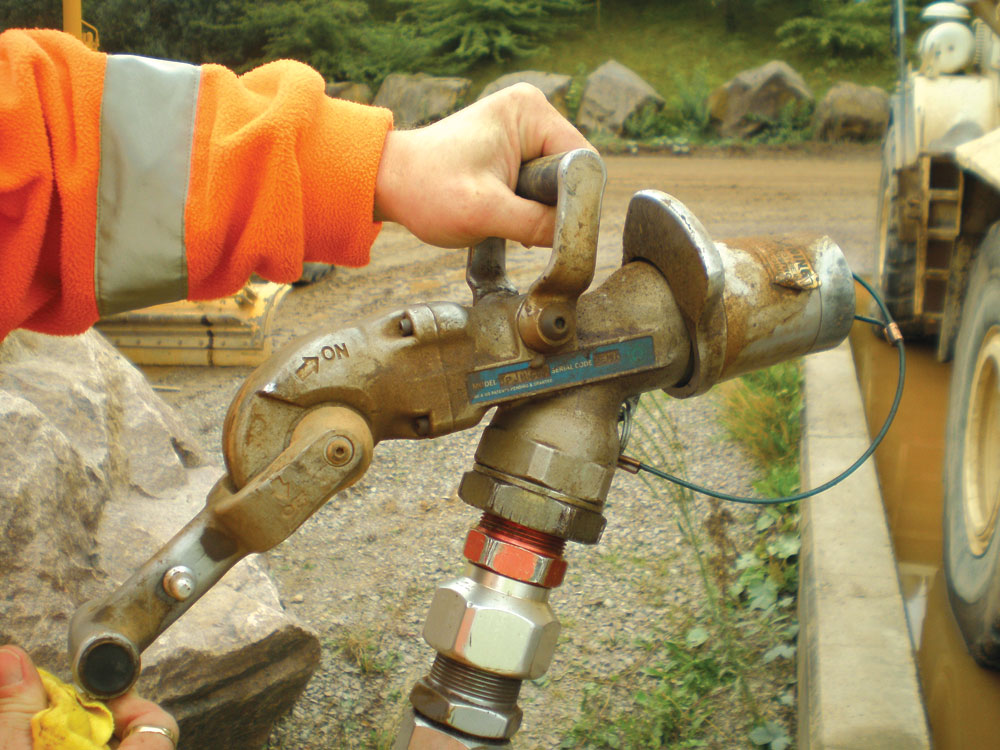
No one has remained untouched by the recent increases in energy prices, be it gas, electricity or general forecourt products. Many of the major investment traders, such as Goldman Sachs, have already raised their oil price forecasts for this year, warning that crude oil could soar to $200 a barrel.
So, what are the cost ramifications for the quarry manager?
The average cost of red diesel across the UK is currently around 65p per litre, depending on delivery order volumes. A year ago the average price was 38p per litre, and in 2002 the majority of quarry operators would have paid as little as 17p per litre. The big question is, with cost increases of well over 150% being applied to red diesel prices, what additional resource or investment is being applied to effectively measure and manage this cost?
In a relatively short space of time quarry managers have moved away from rudimentary pen and paper to PC-based software applications that assist with the production of various operational key performance indicators. However, red diesel stock control and fuel management have largely been overlooked, with tanks being dipped with a stick and no form of access control in place to monitor fuel use per item of plant.
With such unsophisticated control mechanisms in place, the industry needs to take prompt action and focus attention on improving the way fuel usage levels are collated. Midlands-based fuel-efficiency experts Liquid Management Solutions see the improvement of this base data and the minimization of carbon emissions as key challenges to be addressed by the industry in association with its stakeholders.
One of the most significant aspects of legislation ever to hit the industry, the Climate Change Bill, contains provisions that will set a legally binding target for reducing UK carbon dioxide emissions by at least 26% by 2020, and by at least 60% by 2050, compared to 1990 levels. This all sounds extremely challenging, and it is, but without any form of base data from control mechanisms, many industry operators will simply not be in a position to gauge and plot their usage levels per item of plant.
High fuel prices have triggered a wave of thefts of low-tax red diesel across the UK. Like rural farms, quarries are an obvious target for the light-fingered criminal fraternity, as they are often situated in outlying locations and generally have a low level of security around their fuel-storage facilities. So, what can be done to implement some control?
Automatic tank gauging
Getting rid of the ‘stick’ and investing in automatic tank gauging is one of the easiest and most cost-effective ways of implementing fuel-management control.
Various types of automatic tank gauging is used by the industry for other specialist fluid-related products, but typically fuel tends to be overlooked. A cost-conscious quarry manager needs to know, via a PC screen, exactly what fuel stocks he holds at any point in time, but, more importantly, he must be able to ensure that what has been ordered, has been delivered, exactly.
Automatic tank gauging typically comprises a modular item of equipment, which means it can be purchased initially or after the investment in a fuel-management system, but if integrated successfully it serves as an accurate eye.
Fuel management solutions
For many years, a variety of static fuel-monitoring systems has been used to monitor red diesel’s road going counterpart, Derv, in transport yards across the country. But, because quarries are often in harsh and remote locations, many UK manufacturers have struggled to engineer a fuel-management solution for this particular application.
However, proven ‘shock-proof’ fuel-monitoring solutions capable of working with static or mobile bowsers are now readily available using future-proof radio-frequency identification (RFID)-based technology.
RF fuel monitoring is particularly suited to quarrying applications, as the components are essentially very simple, yet secure and robust enough to suit the harsh quarry environment. Plant items are fitted with individually programmed RF tags in close proximity to the filler point. The fuel nozzle, whether high-speed or standard, performs the secure connection with the item of plant; the only manual intervention required by the operator is squeezing of the trigger.
This solution also provides environmental benefits, as a ‘nozzle-out’ function switches the fuel pump off immediately if the RF signal is broken during the refuelling process, thereby reducing the risk of fuel spillage.
Since launching this technology at Hillhead 2007, Liquid Management Solutions have been steadily implementing unique fuel-management solutions for a variety of cost-conscious quarry operators.
For further information or guidance on any fuel-management related issue, contact Kevin Taylor, managing director of Liquid Management Solutions, on (0845) 450 7373.