From Razors And Lingerie To Excavators
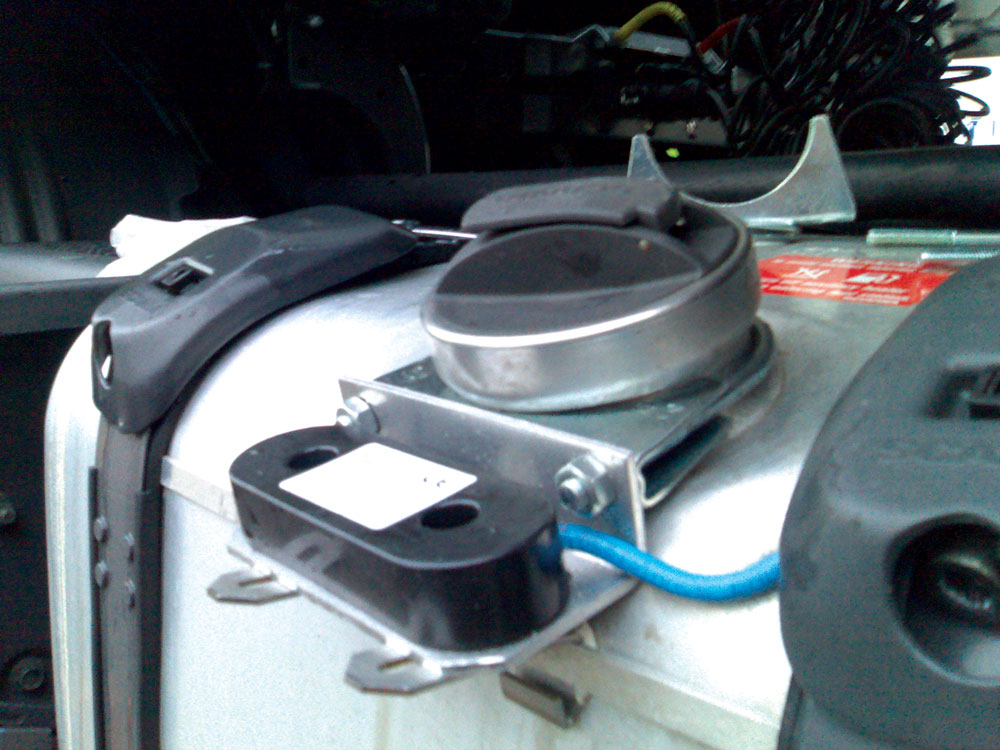
The use of RFID technology in fuel-management best practice
By Kevin Taylor, managing director of Liquid Management Solutions Ltd
The Stern Report listed ‘mining and quarrying’ and ‘concrete’ among the 25 most energy-intensive sectors out of a total of 123 UK sectors. Therefore, when a business seeks to invest a large sum of cash in an item of mobile plant there are several important factors that the company will potentially want to consider, such as how versatile, cost-effective and mobile the machine is, not to mention maintenance requirements, comfort, power and, of course, fuel-efficiency.
Future duty pressures vs fuel-management KPIs
When asked, most companies will know how much they spend on gas-oil per month, but when really quizzed about accurate key fuel-performance indicators on their plant fleets, they often go a little quiet. Since July 1997 the duty on red diesel has risen by 150% and is set to take another dramatic leap of 25% in April 2008 when the Government enforces another rate increase. The need to gain 100% accurate information on fuel usage has, therefore, never been so business critical, but the recognized difficulty for any company buying a wheel loader, excavator or dumptruck is the means by which to gain this vital fuel KPI information.
Do we really believe some of the claims from manufacturers’ fuel trials? Do we really trust what the on-board computer is telling us, and would we ever challenge it? The problem begins when we need to truly establish accurate fuel-efficiency figures, with the global manufacturers battling it out with claims of 5–20% fuel savings by procuring their respective brands. There has been a noticeable move by the manufacturers to introduce a number of performance-enhancing engines to produce power and torque, all supposedly meeting Tier 3 emission requirements. Further costly extras, including load-sensing hydraulics, idle-management software and simultaneous lift and tilt features, have all been added too.
However, with the unsympathetic rises in fuel duty, surely the key question must be: what evaluation is being performed regarding the installation of more efficient fuel-monitoring facilities to ensure operators can independently capture fundamental KPI information at site level?
Refuelling technology advances with demands on accuracy
A recent statement of intent by the Quarry Products Association acknowledges that greater focus is required on helping the quarrying sector to reduce its carbon emissions. But if this is not monitored; how can it be managed?
A large proportion of UK quarries are in desperate need of assistance and guidance on ways to introduce fuel-management best practice, reviewing everything from fuel stockholding, wet-stock reconciliation, speed of refuelling and overall security of this ‘liquid gold’ commodity.
A variety of static fuel-monitoring systems have been used to monitor red diesel’s road-going counterpart, Derv, in transport yards across the country for many years. However, because quarries are often located in remote, rugged landscapes, no UK manufacturers have ventured into this environment, and any mention of bringing a large item of plant to refuel at a static fuelling facility would be regarded as a logistical nightmare by most quarry managers.
RFID – a true mobile solution
Hectronic, the Swiss-owned global manufacturers of fuel-management hardware, designed a ‘shockproof’ mobile fuel-monitoring solution some years ago to accurately monitor fuel usage in mines throughout South Africa. The company has now forged an alliance with UK industry refuelling experts Liquid Management Solutions (LMS) to bring this proven radio-frequency identification (RFID)-based technology to the UK quarrying industry.
RFID has been adopted across many different business applications from the tagging of Gillette razors and Marks & Spencer’s lingerie, and now for monitoring the 100% secure refuelling of mobile plant. LMS say the RFID-based solution is very simple, secure and robust, making it well suited to harsh quarry environments. Individually programmed RFID tags are typically installed in close proximity to the fuel tank filler neck. All the operator has to do is put the nozzle in the tank and squeeze the trigger.
As well as eliminating any unauthorized refuelling, this solution also brings about environmental benefits, as a ‘nozzle-out’ function switches off the fuel pump immediately if the RFID signal is broken during the refuelling process, reducing the risk of fuel spillage.
Knowing that fuel has been 100% securely deposited into the vehicle is important, but automatically capturing the engine hours is the key. By recording this data automatically at the point of each fuelling from a simple non-engine management interface, the company is armed with 100% accurate fuel key performance indicators.
With this armoury, the operator can truly assess the effects of positive or negative fuel returns against the unit’s whole-life cost, aiding future plant procurement decisions and increasing bottom-line profitability.
For further information contact Kevin Taylor at Liquid Management Solutions on tel: (0845) 450 7373.