Safety In Sight
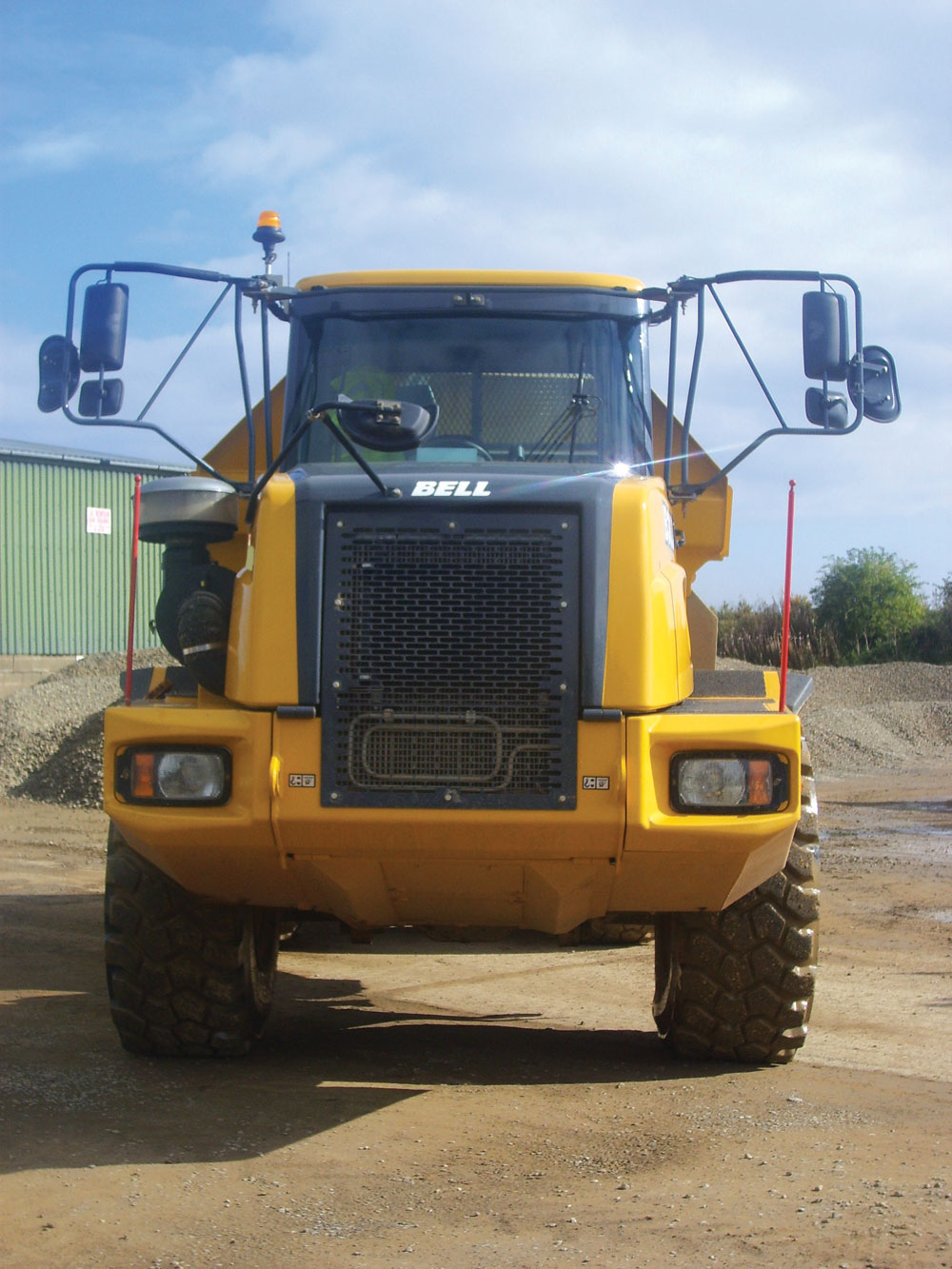
With substantial plant operating on open-plan worksites, and aggravating factors such as noise and dust, the quarry industry needs to be especially rigorous in managing the risks of reversing plant and vehicles. Julian Athawes, a plant specialist and managing director of Allfett Vehicle CCTV and Allfett Automatic Lubrication Systems, looks at the issues
Quarrying remains one of the most dangerous industries for workers. Since 2000, over 2,700 quarry workers have suffered an injury reportable to the HSE, 21 of these being fatal.
Across all industries, vehicles account for 25% of fatal accidents, rising to 60% in quarrying. Vehicle accidents in quarries and opencast sites account for, on average, 50% of all quarry deaths, many of these while reversing.
In terms of vehicle safety, size does make a difference. The quarry industry may boast some of the biggest mobile plant, but these super-size vehicles also pose some of the biggest problems in terms of the driver’s field of vision.
Owing to their size, large wheel loaders, faceshovels, excavators and dumptrucks can suffer from poor visibility from the cab. Views can be hampered to the side or front of the vehicle, as well as to the rear.
Unsighted manoeuvres by large dumptrucks pose a risk to other smaller service vehicles. A Land Rover, for example, stands little chance against a fully loaded truck weighing 50 tonnes or more.
Payloads can also hamper visibility: drivers of lift trucks and compact dumper vehicles may have difficulty with forward visibility when moving large loads.
Indeed, varying degrees of difficulty exist regarding visibility when operating other quarry vehicles, such as bulldozers, excavators, faceshovels, scrapers, graders, fork-lift trucks, lorries etc.
Responsibilities
Today, of course, the industry is more aware than ever of its responsibilities and duty of care.
During the past 10 years, a raft of health and safety guidance, initiatives and updated legislation – and no small amount of effort by quarry owners and operators themselves – has driven up standards in the safe operation of vehicles and plant.
Since the launch of the HSE’s Hard Target Initiative in 2000, the quarry sector has achieved a 55% reduction in accidents (up to the year 2006/07), and it continues to make strides towards its target of achieving zero reportable accidents by 2015.
A first step to reducing the risk of an accident caused by a reversing vehicle is simply to eliminate the need to reverse wherever possible.
If this is not possible, the risk assessment should consider if there is enough room to reverse, whether people can be excluded from the area, and whether vehicles are using the most suitable route for reversing.
Managing traffic routes, using a one-way system and segregating vehicles during operation are other ways of reducing the need to reverse and the risk of collision caused by such manoeuvres.
Where it is difficult to implement rules on vehicle movements, some control can be effected through physical measures, eg gates, barriers, and flow plates or control spikes that can only be crossed in one direction
Visibility
When every step has been taken to reduce the need to reverse, ensuring excellent visibility for drivers when performing reversing manoeuvres becomes the key.
According to the HSE, in every quarry accident involving moving vehicles, the lack of all-round visibility for the operator has played a significant part.
The need for good visibility is highlighted in core legislation – the Quarries Regulations 1999 – with reference to PUWER (Provision and Use of Work Equipment Regulations 1998). Regulation 28 in PUWER requires that ‘where the driver’s direct field of vision is inadequate to ensure safety, there are adequate devices for improving his vision so far as is reasonably practicable….’
The importance of 360° visibility cannot be over-emphasized, as the HSE states in its ‘Let drivers see and be safe’ advice document. This states: ‘It is difficult to envisage any operation of a vehicle which does not have all-round driver visibility, where proper risk assessment would fail to identify the need for all-round visibility aids’.
The 1.0m stick test is the accepted method of assessing visibility from the cab. This requires that a driver must be able to see the top of a stick both 1.0m from the vehicle and 1.0m above ground level at all times without the need to look over his or her shoulder.
Based on this, the health and safety manager can then work out what supplementary visual aids may be needed to comply.
Machines themselves should also be visible, through the use of bright paintwork; visibility stripes on the rear of the machine; roof beacons; warning signs; and good lighting, including roof lights and high-intensity reversing lights. Vehicles and equipment should also be cleaned regularly.
Reversing aids
The market has seen huge growth in reversing aids – from convex mirrors and reversing alarms to radar sensors and vehicle CCTV – to enhance reversing safety as well as to achieve the 1.0m golden rule.
When it comes to ‘real sight’ rather than sensor technology, vehicle CCTV, together with convex mirrors, are becoming a staple health and safety equipment specification for quarry plant and vehicles.
In ‘Mobile Plant Reversing & Visibility Aids’, published in 2006 by the British Cement Association (BCA), the use of reversing cameras is recommended to comply with the 1.0m stick test. It says: ‘To achieve compliance…, the following equipment should be considered as part of the overall risk assessment and usually fitted as a minimum: closed-circuit television (CCTV), convex internal rear-view mirror, convex segment wing mirrors on each side’.
Like the BCA, the HSE promotes a ‘belt-and-braces’ approach to the provision of visual aids. In ‘Let drivers see and be safe’, it states: ‘Fit curved convex mirrors as well as normal reversing mirrors and you will be able to see right and left and to the front of the machine. Fit closed-circuit television (CCTV) or radar as well and you will have the all-round visibility you need’.
In its advice document, ‘Vehicles at Work - Safe Manoeuvring’, the HSE also states: ‘CCTV can cover most blind spots. The cost of fitting CCTV systems has fallen since the technology was first developed, and the systems are more reliable. Companies who have fitted CCTV have found that it can reduce the number of reversing accidents, so the systems usually pay for themselves in a few years’.
Sophisticated CCTV
Specifications for modern reversing camera technology are becoming more and more sophisticated to meet even the most demanding needs, such as the huge trucks and harsh environments of heavy construction and quarrying.
High-resolution colour monitors are now widely available, generously sized – typically 5in and 7in – and with full adjustment of contrast, brightness and resolution for overcast or bright conditions. A hood may also be provided to shield the screen from glare.
A reputable supplier will carry out a visibility assessment and advise on the ideal camera system specification, configuration and positioning, as well as installing and commissioning it.
The styling and ergonomics of in-cab monitors continues to be updated, with many now having an integrated controller with fewer and more accessible components for easier installation and servicing.
Multiple cameras can be of benefit to large vehicles, as can wireless picture transmission where the location of the camera makes it difficult to wire back to the in-cab monitor.
Bromfield Sand & Gravel
Wayne Clent is the quarry manager for Bromfield Sand & Gravel, in Ludlow, an independent company that also manufactures concrete blocks, resulting in additional traffic including lorries making bulk cement deliveries and articulated trucks collecting blocks.
Previously with a large quarry group, Mr Clent has helped Bromfield make great strides with health and safety since he joined the company in September 2006.
‘We don’t have ready-made guidelines on vehicle health and safety like the big groups, so we have had to work hard to establish procedures that work for the particular operational needs of our site,’ he explained.
Deposit is hauled by dumptruck to a field hopper half a mile away, then conveyed to the process plant and stockpile area, which is accessible by the public, further complicating health and safety provision.
The stockpile site operates two loading shovels, an articulated dumptruck, a stock lorry, a telehandler, a forklift and two on-highway delivery trucks.
Bromfield have invested in the latest reversing safety equipment, as Mr Clent explained: ‘We use a combination of radar, colour reversing cameras and convex mirrors. The articulated dumptruck has extra convex mirrors to comply with the 1.0m rule, and we are currently looking at a new generation of the radar braking system as an additional measure.
‘We eliminate reversing operations wherever we can. Stockpiles have been set to make them more accessible and the need for reversing is minimal. The site also operates a one-way system. When vehicles are parked, we ensure that the next time they are used, the first movement is in a forward direction.’
One-way
The one-way system is integral to Bromfield’s rigorous safety provision for members of the general public, who can buy materials direct from site.
‘Obviously, our domestic customers are unaware of the health and safety risks of the quarry site, so we have implemented strict controls to safeguard them when visiting,’ said Mr Clent.
‘Drivers are banned from getting out of their vehicle in areas beyond the weighbridge unless they are wearing high-visibility clothing, a hard hat and have been authorized to do so. There is also a strict speed limit on site.
‘We now pre-bag materials for our retail customers so they are not dismounting from their vehicles to hand shovel their own materials from the stockpiles,’ he added.
To help maintain good visibility, stockpile areas as well as all roads at the site, right up to the main highway, are irrigated to suppress dust.
Segregation
Task segregation is also helping to reduce the risks from mobile plant, as Mr Clent explained: ‘We have implemented an operational hierarchy giving priority to the movement of certain machines.
‘For example, when the loading shovel is in use, operators and other machines are not allowed to enter its working zone. This eliminates the need for it to negotiate other plant or people, removing the associated hazards, minimizing disruption and supporting greater efficiency.’
Health and safety theory is no good without personnel instruction and awareness, so training is a continuous focus at Bromfield.
‘Plant and vehicle safety is always a key part of our health and safety meetings,’ said Mr Clent. ‘Our operators are EPIC certified in terms of plant operation and we also have regular toolbox talks on maintaining the vehicles themselves in a safe condition, checking brakes, keeping them clean and so on.
‘Daily inspections must be carried out by each operator at the start of the shift or when a machine is first used. The inspections are recorded and any faults must be reported.’
The signs are that legislative requirements and standards will only get tougher in relation to risk assessment, safe working practice and mandatory equipment to improve the safety of mobile quarry plant, especially when reversing.
Although manufacturers continue to push the envelope towards ‘zero-risk’ reversing technology, sound training and supervision will remain paramount in reducing the risks from reversing in the quarry industry.
For further information, contact Allfett Ltd on tel: (0870) 161 1058; or visit: www.allfett.co.uk
Quarrying remains one of the most dangerous industries for workers. Since 2000, over 2,700 quarry workers have suffered an injury reportable to the HSE, 21 of these being fatal.
Across all industries, vehicles account for 25% of fatal accidents, rising to 60% in quarrying. Vehicle accidents in quarries and opencast sites account for, on average, 50% of all quarry deaths, many of these while reversing.
In terms of vehicle safety, size does make a difference. The quarry industry may boast some of the biggest mobile plant, but these super-size vehicles also pose some of the biggest problems in terms of the driver’s field of vision.
Owing to their size, large wheel loaders, faceshovels, excavators and dumptrucks can suffer from poor visibility from the cab. Views can be hampered to the side or front of the vehicle, as well as to the rear.
Unsighted manoeuvres by large dumptrucks pose a risk to other smaller service vehicles. A Land Rover, for example, stands little chance against a fully loaded truck weighing 50 tonnes or more.
Payloads can also hamper visibility: drivers of lift trucks and compact dumper vehicles may have difficulty with forward visibility when moving large loads.
Indeed, varying degrees of difficulty exist regarding visibility when operating other quarry vehicles, such as bulldozers, excavators, faceshovels, scrapers, graders, fork-lift trucks, lorries etc.
Responsibilities
Today, of course, the industry is more aware than ever of its responsibilities and duty of care.
During the past 10 years, a raft of health and safety guidance, initiatives and updated legislation – and no small amount of effort by quarry owners and operators themselves – has driven up standards in the safe operation of vehicles and plant.
Since the launch of the HSE’s Hard Target Initiative in 2000, the quarry sector has achieved a 55% reduction in accidents (up to the year 2006/07), and it continues to make strides towards its target of achieving zero reportable accidents by 2015.
A first step to reducing the risk of an accident caused by a reversing vehicle is simply to eliminate the need to reverse wherever possible.
If this is not possible, the risk assessment should consider if there is enough room to reverse, whether people can be excluded from the area, and whether vehicles are using the most suitable route for reversing.
Managing traffic routes, using a one-way system and segregating vehicles during operation are other ways of reducing the need to reverse and the risk of collision caused by such manoeuvres.
Where it is difficult to implement rules on vehicle movements, some control can be effected through physical measures, eg gates, barriers, and flow plates or control spikes that can only be crossed in one direction
Visibility
When every step has been taken to reduce the need to reverse, ensuring excellent visibility for drivers when performing reversing manoeuvres becomes the key.
According to the HSE, in every quarry accident involving moving vehicles, the lack of all-round visibility for the operator has played a significant part.
The need for good visibility is highlighted in core legislation – the Quarries Regulations 1999 – with reference to PUWER (Provision and Use of Work Equipment Regulations 1998). Regulation 28 in PUWER requires that ‘where the driver’s direct field of vision is inadequate to ensure safety, there are adequate devices for improving his vision so far as is reasonably practicable….’
The importance of 360° visibility cannot be over-emphasized, as the HSE states in its ‘Let drivers see and be safe’ advice document. This states: ‘It is difficult to envisage any operation of a vehicle which does not have all-round driver visibility, where proper risk assessment would fail to identify the need for all-round visibility aids’.
The 1.0m stick test is the accepted method of assessing visibility from the cab. This requires that a driver must be able to see the top of a stick both 1.0m from the vehicle and 1.0m above ground level at all times without the need to look over his or her shoulder.
Based on this, the health and safety manager can then work out what supplementary visual aids may be needed to comply.
Machines themselves should also be visible, through the use of bright paintwork; visibility stripes on the rear of the machine; roof beacons; warning signs; and good lighting, including roof lights and high-intensity reversing lights. Vehicles and equipment should also be cleaned regularly.
Reversing aids
The market has seen huge growth in reversing aids – from convex mirrors and reversing alarms to radar sensors and vehicle CCTV – to enhance reversing safety as well as to achieve the 1.0m golden rule.
When it comes to ‘real sight’ rather than sensor technology, vehicle CCTV, together with convex mirrors, are becoming a staple health and safety equipment specification for quarry plant and vehicles.
In ‘Mobile Plant Reversing & Visibility Aids’, published in 2006 by the British Cement Association (BCA), the use of reversing cameras is recommended to comply with the 1.0m stick test. It says: ‘To achieve compliance…, the following equipment should be considered as part of the overall risk assessment and usually fitted as a minimum: closed-circuit television (CCTV), convex internal rear-view mirror, convex segment wing mirrors on each side’.
Like the BCA, the HSE promotes a ‘belt-and-braces’ approach to the provision of visual aids. In ‘Let drivers see and be safe’, it states: ‘Fit curved convex mirrors as well as normal reversing mirrors and you will be able to see right and left and to the front of the machine. Fit closed-circuit television (CCTV) or radar as well and you will have the all-round visibility you need’.
In its advice document, ‘Vehicles at Work - Safe Manoeuvring’, the HSE also states: ‘CCTV can cover most blind spots. The cost of fitting CCTV systems has fallen since the technology was first developed, and the systems are more reliable. Companies who have fitted CCTV have found that it can reduce the number of reversing accidents, so the systems usually pay for themselves in a few years’.
Sophisticated CCTV
Specifications for modern reversing camera technology are becoming more and more sophisticated to meet even the most demanding needs, such as the huge trucks and harsh environments of heavy construction and quarrying.
High-resolution colour monitors are now widely available, generously sized – typically 5in and 7in – and with full adjustment of contrast, brightness and resolution for overcast or bright conditions. A hood may also be provided to shield the screen from glare.
A reputable supplier will carry out a visibility assessment and advise on the ideal camera system specification, configuration and positioning, as well as installing and commissioning it.
The styling and ergonomics of in-cab monitors continues to be updated, with many now having an integrated controller with fewer and more accessible components for easier installation and servicing.
Multiple cameras can be of benefit to large vehicles, as can wireless picture transmission where the location of the camera makes it difficult to wire back to the in-cab monitor.
Bromfield Sand & Gravel
Wayne Clent is the quarry manager for Bromfield Sand & Gravel, in Ludlow, an independent company that also manufactures concrete blocks, resulting in additional traffic including lorries making bulk cement deliveries and articulated trucks collecting blocks.
Previously with a large quarry group, Mr Clent has helped Bromfield make great strides with health and safety since he joined the company in September 2006.
‘We don’t have ready-made guidelines on vehicle health and safety like the big groups, so we have had to work hard to establish procedures that work for the particular operational needs of our site,’ he explained.
Deposit is hauled by dumptruck to a field hopper half a mile away, then conveyed to the process plant and stockpile area, which is accessible by the public, further complicating health and safety provision.
The stockpile site operates two loading shovels, an articulated dumptruck, a stock lorry, a telehandler, a forklift and two on-highway delivery trucks.
Bromfield have invested in the latest reversing safety equipment, as Mr Clent explained: ‘We use a combination of radar, colour reversing cameras and convex mirrors. The articulated dumptruck has extra convex mirrors to comply with the 1.0m rule, and we are currently looking at a new generation of the radar braking system as an additional measure.
‘We eliminate reversing operations wherever we can. Stockpiles have been set to make them more accessible and the need for reversing is minimal. The site also operates a one-way system. When vehicles are parked, we ensure that the next time they are used, the first movement is in a forward direction.’
One-way
The one-way system is integral to Bromfield’s rigorous safety provision for members of the general public, who can buy materials direct from site.
‘Obviously, our domestic customers are unaware of the health and safety risks of the quarry site, so we have implemented strict controls to safeguard them when visiting,’ said Mr Clent.
‘Drivers are banned from getting out of their vehicle in areas beyond the weighbridge unless they are wearing high-visibility clothing, a hard hat and have been authorized to do so. There is also a strict speed limit on site.
‘We now pre-bag materials for our retail customers so they are not dismounting from their vehicles to hand shovel their own materials from the stockpiles,’ he added.
To help maintain good visibility, stockpile areas as well as all roads at the site, right up to the main highway, are irrigated to suppress dust.
Segregation
Task segregation is also helping to reduce the risks from mobile plant, as Mr Clent explained: ‘We have implemented an operational hierarchy giving priority to the movement of certain machines.
‘For example, when the loading shovel is in use, operators and other machines are not allowed to enter its working zone. This eliminates the need for it to negotiate other plant or people, removing the associated hazards, minimizing disruption and supporting greater efficiency.’
Health and safety theory is no good without personnel instruction and awareness, so training is a continuous focus at Bromfield.
‘Plant and vehicle safety is always a key part of our health and safety meetings,’ said Mr Clent. ‘Our operators are EPIC certified in terms of plant operation and we also have regular toolbox talks on maintaining the vehicles themselves in a safe condition, checking brakes, keeping them clean and so on.
‘Daily inspections must be carried out by each operator at the start of the shift or when a machine is first used. The inspections are recorded and any faults must be reported.’
The signs are that legislative requirements and standards will only get tougher in relation to risk assessment, safe working practice and mandatory equipment to improve the safety of mobile quarry plant, especially when reversing.
Although manufacturers continue to push the envelope towards ‘zero-risk’ reversing technology, sound training and supervision will remain paramount in reducing the risks from reversing in the quarry industry.
For further information, contact Allfett Ltd on tel: (0870) 161 1058; or visit: www.allfett.co.uk