Managed Maintenance Of Clean Air
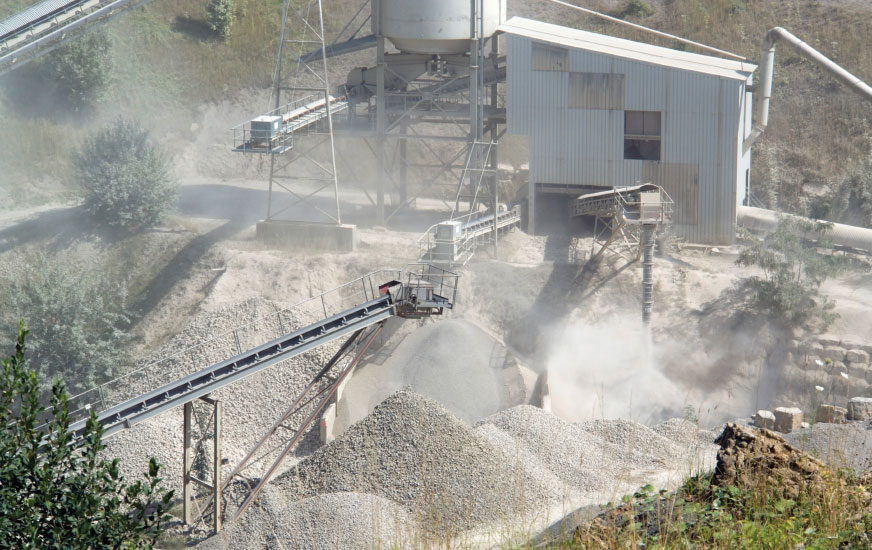
Over the last decade, air filtration requirements in the quarrying and asphalt industry have become ever more demanding, which means operators have to constantly review both the health and safety as well as environmental aspects of their business. Stuart Ainsworth of Tyne Tees Filtration takes a look at the latest developments in baghouse filter design
Stone crushing and screening in quarrying and asphalt operations create two types of dust problems for operators – heavy dust and respirable dust. Heavy dust comprises particles down to 50 microns in size that can become airborne and, because they fall at around 200mm/s, are unlikely to make it beyond the perimeters of the quarry site. To the naked eye, heavy dust is readily seen as a cloud.
Respirable dust, ie anything below 50 microns in size, can stay in the air for in excess of 30min and is easily breathed into the lungs. This type of dust, therefore, causes the greater problem for quarry and asphalt operations, not least because it can also travel beyond the quarry/plant boundary. Even at this size, when present in large enough quantities, it can be visible as a dust cloud.
Respirable dust is, however, most commonly seen as a fine coating when it settles on machinery or other surfaces within the quarry or asphalt operation, as well as on leaf surfaces beyond the site boundary. It is a real problem for many operations because wind can agitate the dust once it has settled, causing it to become airborne again. Through this process, it can travel relatively long distances from the quarry site, posing a serious issue for the surrounding environment. As well as creating issues from a health and safety and environmental point of view, a substantial amount of material can be lost through the formation of dust.
There are various ways of tackling airborne dust, including water spray droplets, ideally in the form of a fine mist that will agglomerate dust at the size of the water droplet. However, once the dust agglomeration falls to the ground, it will dry out and once again become a potential source of windblown dust.
Baghouse filters offer a more reliable solution to this problem than water sprays and, more importantly, remove dust as close to its source as possible to achieve maximum filtration levels, thus helping operators meet their legal requirements. Under legislation introduced in October 2007, which sets out new limits for workers’ exposure to dust, owners, operators and employers now have to keep exposure levels below agreed limits. Since the introduction of this new legislation, bag filters made from aramid felt have been in strong demand from quarry and asphalt operators looking for improved filtration levels in both dust and wet filtration applications.
Aramids in asphalt operations
Nomex, which is a trademark of DuPont, was the original meta-aramid and, as such, is still the industry standard and recognized, technically, as the best. More recently, other aramids, such as Conex, have become available along with a number of new generic products. In terms of performance, aramid is highly suited to bag filters, especially for asphalt flue gas situations, as its temperature resistance is good (up to 220°C for short periods in dry conditions). However, in common with other fibres, such as polyester and P84, aramids are susceptible to hydrolysis.
This means that in hot or moist environments, eg bitumen mixing, water can break down the chemicals from which the fibres were made. This greatly reduces the strength of the filter bag and, ultimately, turns the fibres to powder. Some chemical treatments can delay the onset of degradation; in particular, strong fluorocarbon treatments, such as CR1, protect the fibres from moisture, though they cannot actually prevent hydrolysis.
In common with many bag filters, aramid needlefelts can incorporate conductive fibres to reduce the problems associated with the build-up of static electricity, which is a common problem in stone-crushing operations. These can take the form of Checkstatic conductive scrims or conductive fibres, or a combination of the two. With aramid products, it is normal to use stainless steel fibres due to the temperature and chemical conditions that are frequently encountered within the filter. Tyne Tees Filtration have recently manufactured many aramid bag filters using proprietary FiberLox technology because of the benefits it offers to asphalt operations.
FiberLox removes the scrim from the process, allowing the weight of the scrim to be replaced with fibres. The finished bag filter is, therefore, 100% fibre and it is these fibres that act as the filtration medium, rather than fibre and scrim, where the scrim acts as a barrier to filtration. For many asphalt operators, FiberLox has become a compelling option because, in addition to providing superior filtration levels, weight-for-weight it is more cost-effective than scrim-supported filters. In addition, the removal of scrim and addition of fibres reduces fabrication costs and improves filtration efficiency.
It is generally recommended that the aramid felts used to make bag filters should be heat stabilized, followed by press singing, because this reduces the harshness of the singe traditionally found with aramid felts. The bag filters can also be impregnated with fluorocarbon treatments to enhance their resistance to hydrolysis and to improve cake management with certain dusts.
The cost-effectiveness and efficiency of bag filters made from self-supporting non-woven media, such as FiberLox, means these are proving an economical solution for many difficult baghouse applications in the asphalt industry. In addition, they provide higher burst strengths compared with standard scrim-supported needlefelt filters, which means that, in certain situations, longer bag-filter life can be achieved. The FiberLox technology is available in polyester, polypropylene, polyimide, PPS and meta-aramid materials, which means it can be used for most dust requirements within a plant.
In addition to incorporating FiberLox technology, the fibres used to make the bag filters can have various surface finishes to suit specific applications, such as a glazed dust-collection surface to improve the dust-release properties in either reverse-air or pulse-jet units. The many base materials available that incorporate self-supporting technology, mean that bag filters can be chosen to suit particular applications, such as attack from acidic and alkaline atmospheres.
Managed maintenance
With the ever-tightening environmental legislation, many customers now prefer to use maintenance programmes to meet the required standards. This gives the plant operator confidence that their operation is continually monitored to ensure compliance, eg with the stack test requirements. It is also an effective way to reduce costs, as problems can be identified before they escalate and laboratory test facilities can be used to recommend ways of improving bag life.
As part of their Managed Maintenance Programme, Tyne Tees Filtration offer isokinetic stack testing and certification from an MCERT- and UKAS-accredited company. This programme offers timely planning of filter-unit assessment and repairs, prior to the regular stack emission test. This helps ensure that the plant is ready, performing efficiently and to standard, thereby reducing costly unplanned downtime and failures.
Offering a maintenance programme to complement Tyne Tees’ bag-filter manufacturing facilities helps customers to achieve their clean-air objectives. Achieving improved levels of filtration makes both the plant and surrounding areas cleaner and safer. The environmental focus on all operations that produce dust looks set to become ever tighter, which means owners and managers are under constant pressure to reduce target emission levels even further. This is driving them to constantly review their anti-pollution and de-dusting processes to ensure compliance. With legislators having the authority to stop an operation that does not meet air quality standards, it is vitally important that quarry and asphalt operations have access to the right products to achieve the latest targets.
The goal at Tyne Tees Filtration is to develop even more efficient methods of helping operators comply with legislation, a key part of which is the company’s maintenance programme, which ensures continual monitoring of the operation. Suppliers who can offer this combination are able to offer enhanced filtration levels, providing quarry and asphalt operations with a complete ‘clean-air’ solution.