Effective Dust-Suppression in Quarries
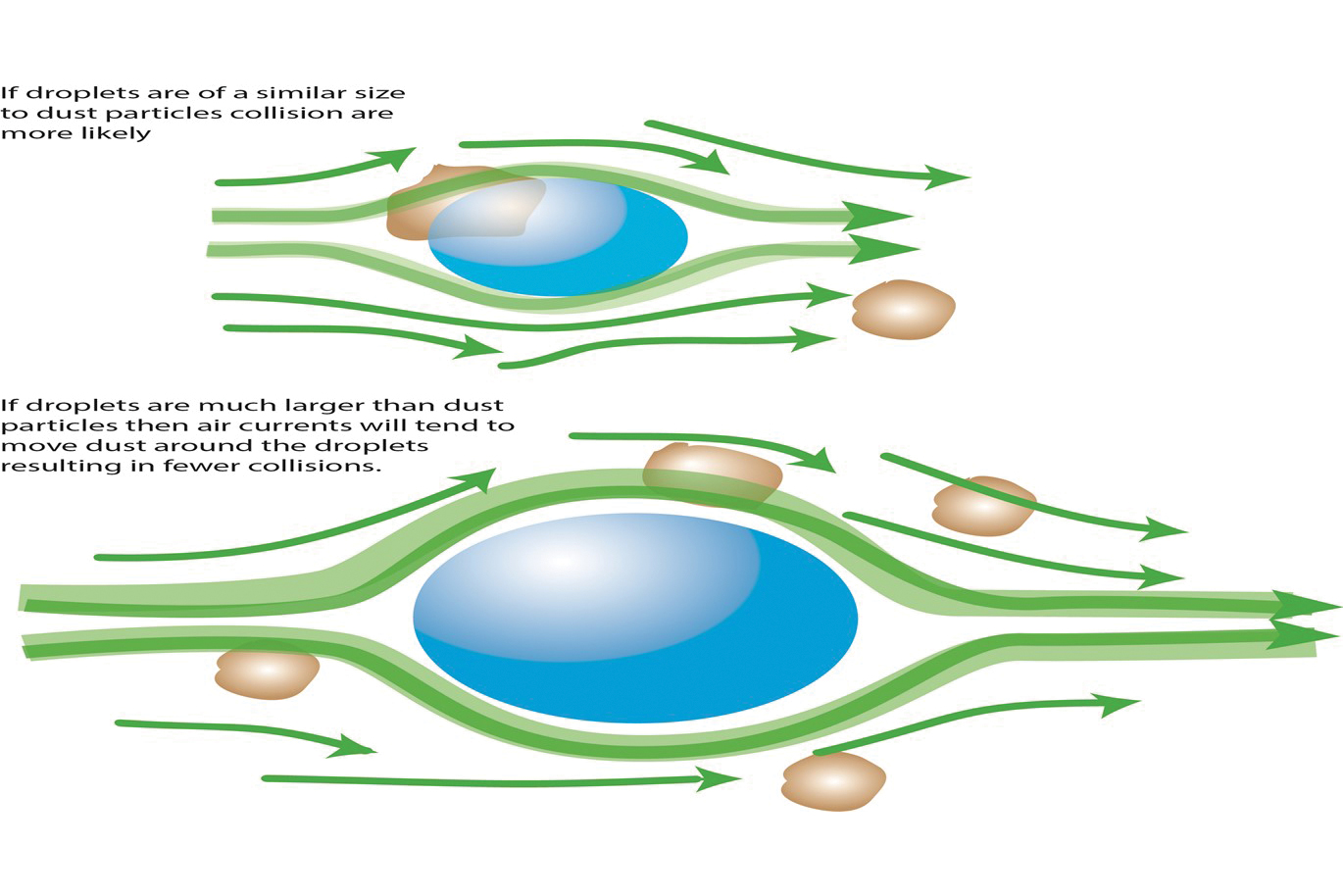
First published in the December 2017 issue of Quarry Management as The Dust Factor
Brigitte Pennington from Conflow looks at the importance of effective dust-suppression systems in quarries
One of the greatest threats to health and safety in quarries is the dust known as respirable crystalline silica (RCS). Crystalline silica is found in varying proportions in rocks, sands and clays, and exposure to RCS can, over time, cause hardening of the lung tissue, leading to impairment of lung function. This is known as silicosis and is characterized by a severe shortness of breath, meaning sufferers can find it difficult to walk even short distances. The condition is so debilitating that it continues to worsen even after exposure has stopped – and it is irreversible. A link has also been proven between exposure to silica and the occurrence of lung cancer. Anyone with silicosis also has an increased risk of contracting a range of other diseases, including kidney inflammation, tuberculosis and arthritis. Quarries in the UK and around the world have a responsibility to their staff and to those living close by, and need to protect them, as far as possible, from the impact of RCS.
Different types of stone contain different amounts of silica – ranging from sandstone, where the quartz (silica) content may be 70% or more, to limestone and chalk at around 2%. In the UK, the workplace exposure limit (WEL) for RCS is 0.1mg/m3 – which is expressed as an 8-hour time-weighted average (TWA). UK quarries also need to operate within the requirements of the Control of Substances Hazardous to Health (COSHH) Regulations 2002. The WEL applies only to the respirable fraction of the silica dust, ie the portion of dust that reaches the deepest parts of the lungs – which is said to be around 10–20% of the total inhalable dust. In limestone quarries, where the silica content is low, exposure to RCS may well be below the WEL. Nevertheless, such quarries still need to ensure that the amount of inhalable dust does not exceed 10mg/m3 over an 8-hour period and exposure to respirable dust should not exceed 4mg/m3.
Anyone operating or managing a quarry is required, under Health and Safety Executive (HSE) guidance, to reduce the exposure of staff, contractors and those living near a plant to silica dust generated by their operations. Exposure to RCS is governed by factors including the proportion of silica in the material, the mechanical work involved in breaking up or processing the material, and the work patterns influencing when and how individuals may be exposed. Risk assessments should be carried out for each job or range of tasks. This will include identifying the potential for exposure to RCS, measuring the effectiveness of existing dust-control systems, ensuring the use of respiratory protective equipment, and maintaining and regularly inspecting any control systems in place to ensure effective operation. Regulation 7 of COSHH requires that employers have a duty of care to prevent employee exposure to RCS, or to ensure this is adequately controlled.
Dust particle size is typically 50–70 microns. There are, of course, dust particles that are larger than this (which tend to settle in the immediate vicinity of whatever is generating the dust), and particles that are smaller than this. It has been shown that dust particles of 20 microns or less can remain airborne for a very long time and can find their way on to and into machinery, into lungs, and also into areas outside the quarry itself. Dust particles less than 10 microns in size are invisible to the naked eye and can remain suspended in the air indefinitely. Generally, the smaller the particle size, the more hazardous it is to health and equipment. Also, the smaller the particle size the harder it is to remove from the atmosphere.
There are three main methods of dust control: suppression, collection and containment. One of the most effective methods of reducing RCS risks is dust suppression, where the aim is to prevent dust escaping from its source. This is usually achieved through spray mechanisms. Conflow’s dust-suppression systems use water sprayed on to the source of the dust emission – usually at point of extraction or crushing. This ensures that the respirable sized particles are wetted and entrapped by the water droplets. Alternative forms are chemical suppression and solenoid valve dust suppression. Chemical dust suppression can be expensive and the dosage of chemical must be accurate at all times to be effective. Solenoid valve dust-suppression systems require a power source and often require regular maintenance. Conflow’s water-based dust-suppression system, which is mechanical in operation and requires no power, is inexpensive to run as well as being low maintenance and very efficient.
The principle behind the Conflow dust-suppression range is that the dust agglomerates with the water, causing it to fall under gravity. However, it is not simply a matter of providing a water spray. If the water droplets are too large, the airborne dust particles are simply moved around in the resulting air currents and very little dust is removed from the air. Too much water also results a very wet working environment and may cause issues at later stages in the processing operation. For the dust to be removed from the air, the water droplets need to be of a similar size to the dust particles, which makes collision between the two more likely (see fig.1). The design of spray head is, therefore, of paramount importance in ensuring the delivery of the correct volume and size of water droplets.
Conflow’s engineers continue to work with quarries and equipment manufacturers to improve and develop new products to protect equipment and personnel from the harmful effects of airborne dust. Dust-suppression systems can be retrofitted to any existing installation and, assuming an adequate supply of water, such a system can be operational in a matter of hours. Such systems can be installed in a variety of areas where dust suppression is required, eg primary and secondary crushers, conveyors, hauls roads etc, particularly during dry weather. For a dust-suppression programme to be successful, however, careful selection of appropriate equipment is required. Operators also need to be trained in the correct use of the equipment, and Regulation 9 of COSHH requires that measures be put in place to ensure the equipment in an effective state of repair and regularly maintained.
Effective dust suppression makes sense from both a production and a health and safety point of view. It is an issue that no quarry can afford to ignore and is essential in being a responsible operator, reducing risks and remaining compliant. For more information visit: www.conflow.com
- Subscribe to Quarry Management, the monthly journal for the mineral products industry, to read articles before they appear on Agg-Net.com