Dust In The Workplace – An Explosive Subject
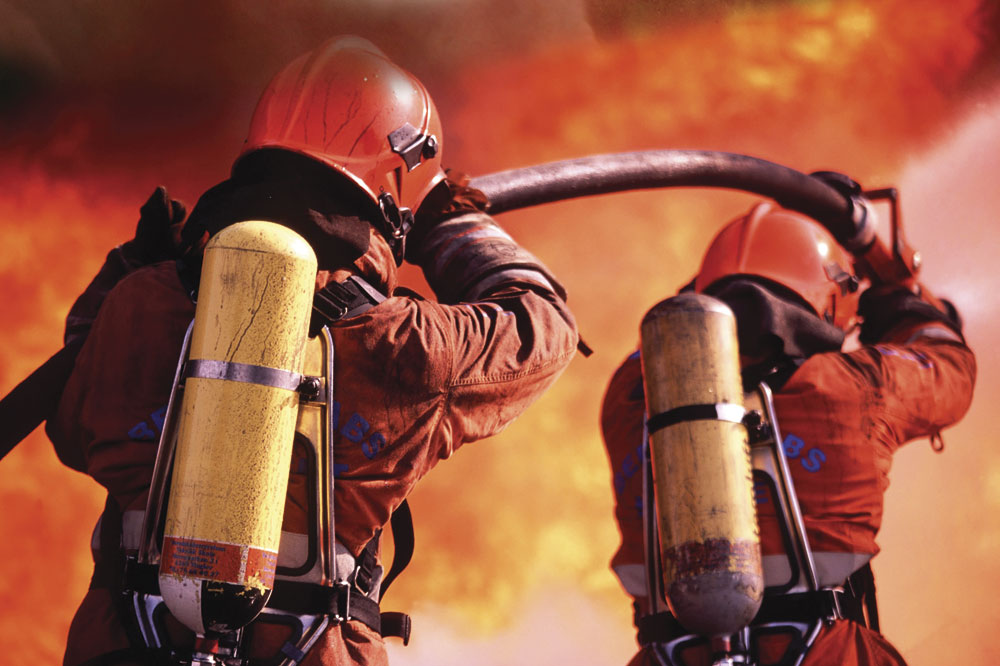
Graham Doran, sales & marketing director at Cooper Crouse-Hinds (UK) Ltd, discusses how companies can reduce the risk of dust explosions occurring in the workplace and the current standards relating to explosion-proof electrical equipment installed in these areas
The risk of a dust explosion occurring in the workplace is not as remote a possibility as people might think. A dust explosion requires only three things: air, combustible dust and a source of ignition, such as an electrical spark or hot surface.
Indeed, many companies are potentially at risk. Why? Because combustible dusts are present in many process manufacturing environments. Problem arise when these combustible dusts are left to gather on hot surfaces in a workplace, such as on an overheated electric motor or fan. This can cause smouldering fires to occur, or can cause an explosion when the dust is kicked up, for example, by a person opening a nearby window.
Dust explosions can have catastrophic consequences because the initial shockwave resulting from the explosion kicks up more dust, which triggers a chain reaction through the plant, often resulting in mass destruction of equipment and buildings, as well as causing possible death or injury to employees.
Therefore, as potential sources of ignition, all electrical equipment installed in these areas, including mixers, filling hoppers, conveyor systems, mills, silos, dust-extraction plant, kilns and drying systems, need to be adequately protected and designed to operate under these conditions. Directors, company owners, plant managers and maintenance engineers – indeed anyone who is responsible for the health and safety of employees or for sourcing electrical equipment for hazardous areas – needs to be fully aware of the risks of dust explosions, the European Directives and standards relating to electrical equipment installed in hazardous areas, and the measures that can be taken to eliminate the risk of dust explosions occurring.
Owners of new equipment are governed by the compulsory European directive 1999/92/EC, implemented in the UK as the ‘Dangerous Substances and Explosive Atmospheres Regulations 2002’ (DSEAR). Since 2006, this directive has also included ‘old’ as well as ‘new’ equipment. In summary, owners are required to: identify the risks of explosion; implement explosion protection measures, such as avoiding sources of ignition (secondary explosion protection); define zones in areas at risk from dust explosions; create an explosion protection document; use suitable production equipment; and create a test plan.
For electrical equipment in areas at risk from dust explosions, a new stricter series of standards, EN61241-... was introduced on 1 October 2008, superceding the existing standard EN 50 281. Within this new series of standards, one of the main protection types for production equipment at risk from dust explosions, in accordance with ATEX Directive 94/9/EC, is protection by enclosure type ‘tD’. This protection type is where the electrical production equipment is equipped with an enclosure to prevent dust penetration and where measures to limit the surface temperature have been implemented.
The main changes to this standard concern the following areas: impact energy – high demand on impact energy as in Zone 1; electrostatics – electrostatic conductance of the enclosure; and ageing resistance – high demand on the ageing resistance of the plastic enclosure. Owners need to be aware of these changes when sourcing or upgrading electrical equipment for hazardous dust areas.
Hazardous areas for explosive dust atmospheres are classified into three Zones: 20, 21 and 22. Zone 20 is an area in which an explosive atmosphere, in the form of a cloud of combustible dust in the air, is present continuously, or for long periods or frequently.
Zone 21 is an area in which an explosive atmosphere, in the form of a cloud of combustible dust in the air, is likely to occur in normal operation occasionally.
Zone 22 is an area in which an explosive atmosphere, in the form of a cloud made up of combustible dust in the air, is unlikely to occur in normal operation but, if it does occur, will persist for a short period only.
In addition, on the 6 April 2008, the Corporate Manslaughter and Corporate Homicide Act 2007 came into force in the UK, which means companies cannot afford to cut corners or delay the implementation of appropriately protected electrical equipment. If they do, these firms could face severe fines or even imprisonment should a dust explosion occur.
The statistics show that companies need to act now without delay, as around 2,000 dust explosions occur in Europe every year and all types of companies are affected.
One recent example of how costly – both in terms of lives lost and damage to plant – dust explosions can be, occurred in February 2008 at the Dixie Crystal Refinery, part of the Imperial Sugar Co. and one of the leading sugar manufacturers in the US. A massive sugar dust explosion killed at least six people and injured more than 60, some seriously, who had to be rushed by helicopter to a special hospital for burns victims. The sugar silos of the filling plant had exploded during the night shift, setting fire to most of the plant. This is just one of many dust explosions that occur around the world. It is estimated that more than 300 dust explosions in grain silos, sugar plants and food companies in the last 30 years in the US alone have cost the lives of more than 120 people.
When can dust explode?
Combustible dust-air mixtures have different ignition temperatures. The surface temperature of the equipment in areas where there is a risk of dust explosions is allowed to reach two-thirds of the minimum ignition temperature of the surrounding dust-air mixture. With a 5mm thick layer of dust, this surface temperature must be at least 75°K below the minimum ignition temperature of the dust (glow temperature).
It is, therefore, the equipment owner’s responsibility to ensure that the cleaning and maintenance intervals of installed equipment with a dust explosion risk are scheduled so that no dust layers thicker than 5mm are allowed to form. With thicker dust deposits, the minimum ignition (glow) temperature of the dust is reduced significantly.
The goal of the current European directives is to protect operating plants from dust explosions and to prevent damage or personal injury. The explosion protection measures are divided into ‘Owner’ and ‘Manufacturer’ directives. Again, the objective is to implement all necessary measures to ensure that explosion-protected products can only be operated if they do not pose any danger to health and safety and provided that they are correctly assembled, installed, maintained and used for their intended purpose.
For owner operators who need technical advice and guidance on explosion-protected electrical installations and the relevant EU directives and standards, Cooper Crouse-Hinds offer a comprehensive range of explosion-protected electrical equipment, including fluorescent light fittings, emergency lighting, switches, terminal boxes, control stations, portable lamps, connectors and plugs. For more information or for a free copy of the company’s new full-range dust catalogue, entitled ‘Catalogue Dust-Ex 712: dust explosion-protected luminaries and apparatus’, contact Cooper Crouse-Hinds’ UK sales office on tel: (024) 7630 8930; or email: sales@ceag-crouse-hinds.co.uk