Emission Control
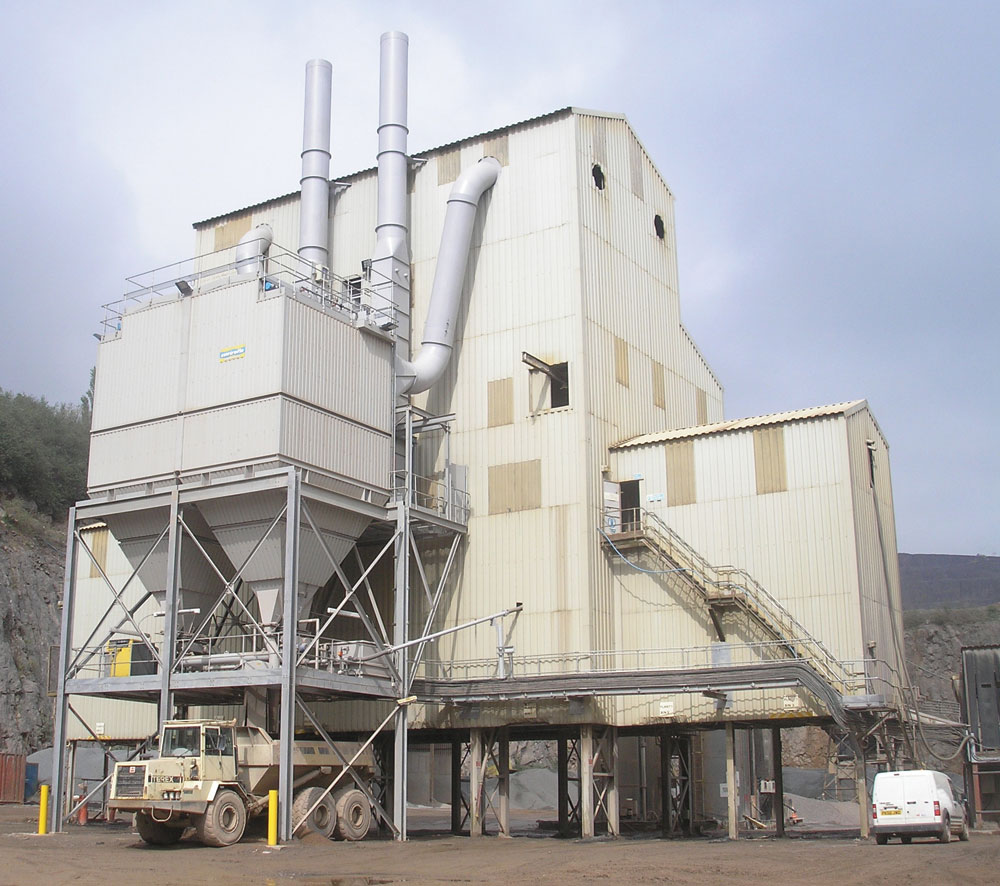
Recent progress in dust control in the quarrying/asphalt industry – a personal view on best practice by Harold Wylie, managing director of Enviroflo Engineering Ltd
Dust control in the quarrying industry has moved forward considerably during the past 20–30 years. In particular, stack emissions from asphalt plants and crushing and screening plants have reduced from in excess of 200mg/m3 down to an average of 15–20mg/m3. And while dust emissions from crushing and screening plants without extraction and collection equipment have shown a lesser reduction, and dust from haul roads and bench roads can still cause problems in dry, windy weather, plant areas and main roads serving quarries and coating plants are now usually treated using a combination of water sprinklers and wheel-washing facilities. As a result, these areas are now showing a considerable reduction in dust emissions when exposed to wind and traffic movement. The application of both existing equipment and new equipment design has been one of the main driving forces behind these improvements.
Best practice for stack emissions
The bag filter has superseded a variety of wet collectors and Venturi scrubbers as the terminal filter of choice. Two main types of bag filter are now commonly used: reverse-air filters – without compressed air cleaning; and pulse jet filters – with compressed air cleaning.
Pulse jet filters were used some 30 years ago, mainly on crushing and screening plants, but were also applied in their early days to asphalt and coating plants. However, their engineering was suspect and pulse jet filters often did not clean down satisfactorily. Reverse air filters soon took over from pulse jet filters and the market, in general, would not consider an alternative. This was based on the premise that reverse air filters used less energy, were easier to maintain and performed better than pulse jet filters. However, despite their continued use, reverse air filters do have a number of significant problems.
Waste/reclaimed oil has grown in use since the mid-1970s. Such oil originally had a low sulphur content and a low chlorine content, but by the early 1990s these values had increased. By inducing atmospheric air into the cleaning system, the reverse air filter has the effect of cooling of the main gas flow through the filter by up to 20°C. This can reduce the temperature of the exhaust gases to below acid dew point resulting in the occurrence of a condensate of sulphuric acid and hydrochloric acid, mainly in the top section of the bag house, which in turn leads to high levels of corrosion, ie on the clean air outlet section.
Another major difficulty with the reverse air filter is that when the filter is not being cleaned, the rotating plenum configuration is set in the ‘parked’ position to ensure minimum leakage of atmospheric air into the filter. Often, however, the plenum is allowed to remain stationary outside the ‘parked’ position, and in many cases this creates a considerable leakage volume, which in turn reduces the performance capability of the rotary dryer. Another problem can occur when the filter starts to clean and the air induced from atmosphere robs the main process air, reducing the production capacity of the dryer or extraction from exhaust and collecting systems.
The argument regarding energy reduction when using reverse air filters is often false owing to the fact that most filters leak atmospheric air into the cleaning system and operate at high temperature losses. The fan absorbs more power at lower temperatures and as the leakage air increases. When the filter is cleaning, additional air enters the filter and fan and this too pushes up fan motor amps.
With the industry taking steps to save energy and reduce its carbon footprint, one of the areas selected for energy saving is the exhaust fan on bag filter installations. The most common way of achieving savings in this area is to fit a frequency inverter, which reduces the fan speed when full extraction is not required. However, this reduction in fan speed reduces the vacuum on the inlet side of the filter and can impair the cleaning efficiency (which is a function of the vacuum available within the filter to induce adequate air into the cleaning system).
In the author’s opinion the industry has lived with these problems for too long and it is probably the case that the vast majority of reverse air filters in use today restrict the overall output of asphalt plants, owing to the leakage and filter cleaning difficulties mentioned above, as well as reducing the extraction volume on crushing and screening applications.
For these reasons it is now becoming clear that pulse jet filters can eliminate most of the disadvantages of the reverse air filter. Pulse jet filters are cleaned by external compressed air, which means that, using modern technology, the overall exhaust volume of the process can be maintained and the temperature loss between inlet and outlet is only some 2–3°C. Dew point condensation is therefore less likely in this type of filter, resulting in a longer life expectancy when handling reclaimed oil.
A range of devices can be applied to the pulse jet filter controller, such as burst bag location, failed diaphragm valve location, stack monitoring, differential pressure control etc. All of these parameters can be logged on the main plant PLC.
Frequency inverters are well suited to this type of filter and, together with differential pressure control, which only cleans the filter when required, represent a big energy saver and, according to the author, a huge leap forward compared to the reverse air filter.
Best practice for crushing and screening applications
The addition of moisture for dust control purposes into minerals being processed has been carried out for many years and it is a fact that the addition of water/absorbed moisture can considerably reduce nuisance dust during handling. In the past water has been added to the process mainly through the use of atomized sprays. On the better engineered systems, this water can be automatically shut off to parts of the plant that are not operating through the use of process signals and solenoid valves. Often, however, the minerals being handled repel water and it is sometimes difficult using water-only systems for the water to become absorbed into the finer fraction of the product, which is the main contributory mechanism to dust release. This may be overcome by adding more water, up to 3–5% of product mass flow, although this amount of water often cannot be tolerated. To help overcome this difficulty, surfactants can be used to reduce the surface tension of the water, making it easier to coat the mineral being processed and thus reduce the amount water used. Surfactants can reduce water consumption down to 0.5–2%. Undoubtedly, ‘wet’ dust-suppression systems do have their uses if applied properly. They are economical to purchase and operate and the cost of chemicals, if used, is relatively low. However, they do not, as a rule, control dust as efficiently as foam systems and tend to use more water in the process.
[img_assist|nid=12264|title=Dry foam|desc=|link=none|align=left|width=393|height=200]In instances where there is a shortage of water or where there is a limit to the amount of moisture that can be added if the product is to be fine screened, eg where the minimum mesh size is below 4mm, high moisture contents can cause blinding of the screens resulting in seriously impaired screening efficiency. There are a number of other mineral products where it is important to keep the added moisture content down, eg coal feed to boilers and aggregate feed to asphalt plants, where ‘free flow’ characteristics are important, as are thermal costs related to driving off moisture. Once again, this limits the amount of water that can be added for dust-suppression purposes.
To overcome most of these problems and to improve the degree of dust control achieved, special foaming agents have been developed. The foam is produced at source by the controlled introduction of water and compressed air into a foaming chamber to create micro-bubbles. These can be applied to strategic parts of the process where the majority of the dust is generated. The micro-bubbles are required to have a high degree of stability, ie they should not break up when sprayed on to the materials being handled. They should also maintain their shape until they enter crusher chamber, transfer point etc, whereupon they ‘burst’ causing the moisture and chemicals they contain to be integrated into the product.
Many foams are available today, but in the author’s opinion US company Nalco make the best product, identified mainly by its micro-bubble stability. Nalco’s patented products are known as DustFoam and DustFoam Plus. Enviroflo Engineering Ltd, who have the sole rights to design DustFoam systems in the UK and Ireland and other designated areas of the world, say cheaper foams are available but that these normally require more foaming agent to produce a similar effect, which can be more costly overall. In addition, the application of DustFoam to one process application can have a considerable advantageous ‘carry-over’ effect to other downstream parts of the process.
As a general rule 0.6 litres of Nalco DustFoam mixed with 99 litres of water will produce approximately 5,000 litres of foam that can be added directly to the process. Normally 0.15% moisture is added to the product. The system may also be run below the above values but this can only be decided on site during commissioning, depending on the mineral being handled, the locations of application points, degree of sealing etc.
The use of DustFoam suppression systems allows considerably smaller volumes of water to be used than the conventional water or water/surfactant systems. Moreover DustFoam is a totally inert organic material and has no detrimental effects on watercourses, cement manufacturing processes, bitumen coating processes etc.
The Enviroflo/Nalco DustFoam system has already been successfully applied on a number of crusher applications in the UK and Ireland, including: three impact crushers at CEMEX’s Halkyn limestone quarry in North Wales; three cone crushers handling granite at Aggregate Industries’ Glensanda Quarry in Scotland; and the primary gyratory crusher, secondary cone, tertiary cone and Barmac crushers at Roadstone Dublin’s (part of the CRH Group) Belgard Quarry in Ireland.
After careful evaluation of the original dust-extraction system serving the crushers, screen and conveyor transfer areas at Glensanda, it was decided (for a number of reasons related to maintenance, abrasion, power consumption etc) to replace this system with an Enviroflo/Nalco ‘dry’ foam system. A special foaming agent was used containing a ‘tackifier’. This foam, known as Nalco DustFoam Plus, encapsulates the dust more efficiently than the standard DustFoam. The presence of the tackifier increases the retention time of the treatment for up to 28 days, which significantly reduces dust generation during ship loading and also reduces emissions when the aggregate is subsequently offloaded.
Generally, the DustFoam equipment is containerized within a standard shipping container, which is pre-piped, pre-wired and supplied complete with heating and lighting if appropriate. If the clients’ compressed air supply is insufficient, an air compressor can be installed in the container, and should the clients’ water supply not be of adequate capacity or pressure (around 6 bar), a tank and pump set can also be included.
The use of DustFoam significantly reduces capital cost but revenue cost moves up to reflect the chemical expenditure. On average, this equates to 2–3p per tonne. The product can solve many problems on crushing and screening plant and its carry-over effect in subsequent handling processes is a bonus, especially with DustFoam Plus. However, as with moisture-addition systems, DustFoam is not suitable for applications where the removal of dust from fine fractions is required. Nevertheless, there are a multitude of plants where DustFoam could be very successfully applied and, in the author’s opinion, the product represents a significant leap forward in dust control in the aggregates and minerals handling industry.
Dust control on haul roads, bench roads, plant areas, main running roads and stockpiles
Best practice for this type of application is to add water to the appropriate surface either by fixed sprinklers or by bowser spraying. Where there is a plentiful supply of water this method is generally satisfactory. Fixed sprinklers are usually more economic to operate than bowsers as they require little manpower and are normally lower in capital cost. Sprinkler systems can be set to work periodically on a 0–24h timer and zoned to reduce pump size.
Where an ample water supply is a problem, a range of chemicals have been developed that can be added to unmade-up roads to help reduce water consumption. When mixed with water, these chemicals bind the dust together and on to the larger aggregate sizes.
Once again, Nalco offer a range of dust-control chemicals for this purpose:
- Haulage DC: is added to water and is claimed to reduce water consumption by 50%.
- Haul-EZ: a more expensive solution but one that will reduce dust for up to six weeks per application. However, rainwater does dilute the chemical and it tends to be used with the greatest success in dry countries on haul roads in the mining industry.
- DustBind: an encrusting agent which, when added to water, is used to reduce dust erosion from non-active fines stockpiles. As its name suggests, DustBind forms a crust on the surface of the stockpile and is not normally influenced by rainwater. It must be emphasized, however, that DustBind should only be used on stockpiles that are not in active use and the pile must not be walked on or the ‘crust’ damaged in any manner, otherwise the wind will find any weakness on the surface and may start breaking up the remaining crust, making the pile, once again, vulnerable to wind erosion and hence dust emissions.
Excess dust
Excess dust from coating plants and dust-extraction and collection plants on crushing and screening applications can present the industry with a big problem, which will be further exaggerated by EU regulations regarding the use of virgin limestone filler in place of reclaimed fines. Current best practice is to use reclaimed fines wherever possible in other industrial processes and the industry should follow this quest with vigour. It is also best practice to use as much fines content as possible in a mix, thus reducing the surplus, as this is better than disposal.
Reducing excess fines in the –5mm fraction is also worthy of close examination. Modifications to the crushing/screening process can reduce the –63 micron fraction. It is worth remembering, this excess dust is blasted, hauled to the crushing plant, heated in the dryer to an average of 170°C, carried in ducted and filter systems, causing increased abrasion, and then dumped. If a use cannot be found for this excess dust, the alternative is disposal by means of a dust-conditioning system. This adds some 10–15% water to the surplus dust, which is mixed to form a ‘pug’. This can then be dumped in a suitable area of the quarry or, in the case of urban coating plants, removed from site. Owing to contamination with fuel or partly burnt fuel, pug is often regarded as a controlled waste and, therefore, requires a licensed tip for safe disposal, adding considerable expense to the disposal process.
Hot dust from coating plants often repels water particularly when hydro- carbons are present. This will adversely affect the dust/water mix and often dust-conditioning equipment cannot be totally successful in eliminating dust during off-loading and handling. Adding a suitable surfactant can break down the surface tension of the water, thus improving mixing. Disposal at the quarry is not always the best solution and care is needed to prevent coating plant dust from washing into local watercourses causing contamination.
For more information, contact Enviroflo Engineering Ltd on tel: (01902) 784848; email: harold.wylie@envirofloeng.com