Dust Control In The Aggregates Industry
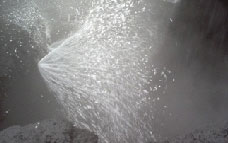
Latest development in foam suppression
By Harold Wylie, Enviroflo Engineering Ltd
Despite the fact that the industry is currently in a commercial downturn, dust control in quarry processes cannot be ignored. Indeed, it may form part of the conditions of a planning consent or statutory regulations. Two main issues drive dust control requirements: the first is environmental dust pollution in the area surrounding the quarry operations, which can have an adverse effect on the neighbouring community; and the second is the health of personnel who work in close proximity to high levels of dust emissions and, in particular, hazardous dust sources such as silica oxide from granite/quartz.
Two main methods are used to control dust in the aggregates production process; one is dust extraction and collection and the other is foam suppression. Dust extraction/collection and foam suppression can both be used in a single crushing and screening application – extraction being applied to remove a proportion of excess particles from single size aggregates should the –63 micron content in the 0–5mm range be higher than normal (12–14% or above).
Foam suppression, however, is often the preferred option on a crushing plant owing to its low capital cost, simplicity in operation and reduced maintenance requirements. The intimate mix of foam and breaking aggregate within each crusher is often adequate to control dust throughout the entire production process.
The foam is produced at source by the controlled introduction of water and compressed air. These are passed to a foaming device to create micro-bubbles, which are required to have a high degree of stability, ie they should not breakdown when sprayed on to the aggregate being handled. They should also retain their shape until they enter the crushing chamber or transfer point, whereupon they ‘burst’ causing the moisture and chemicals they contain to be integrated into the product.
For the greatest effect, a special foaming agent containing a tackifier can be used, such as NALCO DustFoam Plus. This foam encapsulates the dust more efficiently than the standard NALCO DustFoam product. The presence of the tackifier increases the active retention time of treatment up to 28 days and, significantly, reduces dust generation during ship or truck loading from large stocks (and also reduces dust emission when the aggregate is subsequently offloaded).
Care should be taken when selecting from the many foaming agents now available, as it has been reported that several foam applications have had an adverse influence on the strength of concrete mixes. Foaming agents should only be used if they are ‘certified’ by a recognized independent testing laboratory. These tests should confirm that the crushing strength of the concrete is not impaired due to the use of a particular foaming agent. Tests should be carried out with 50–100% excess foaming agent compared to the normal quantity used in the process. This is recommended to evaluate the effects of overdosing.
NALCO DustFoam products were certified 10 years ago and have been re-certified in the past 12 months, making them well suited to dust control in many applications, including crushing, screening and the handling of aggregates.
One of the advantages of DustFoam suppression is that it uses a small amount of water –1.5 litres per tonne of aggregate processed. No screen blinding should occur if the foam system is controlled in parallel with the aggregate process, although a DustFoam suppression system does require an intimate knowledge of the process it is being applied to otherwise it is likely to fail. Appropriate enclosures are usually required around the inlet and especially on the outlet side of each crusher to be treated. These are fitted to reduce entrained air from passing through the crusher and dragging out dust during its passage.
Generally, the DustFoam equipment is containerized within a standard shipping container and is pre-piped and pre-wired. The container can also house an air compressor and water tank if these items are not already available on site.
If extraction and collection is the preferred dust-control option, this involves an extended run of ducting from each crusher and normally each transfer point. The ducting passes into the inlet side of a bag filter. Enviroflo Engineering Ltd bag filters can be of the pulse-jet or reverse-air design. The pulse-jet filter is cleaned by electronically controlled compressed air for optimum performance, while the less sophisticated reverse-air filter requires minimal maintenance. Instead of compressed air, this type of filter relies on the periodic introduction of atmospheric air to clean the bags. Normally, the bag filter is mounted above a storage hopper of 20–30 tonnes capacity. The bag filter can also be ground mounted and fitted with a pneumatic conveying system to blow the collected dust into a remote silo. The dust from either type of storage can be offloaded via a road tanker or passed through a dust-conditioning mixer, where approximately 10–20% of water is added to turn the dry dust into a water-based mix that can be discharged and handled with minimum dust nuisance.
If the 0–5mm aggregate can accept the predominantly –63 micron particles collected by the bag filter, the bag filter can be located at high level to coincide with the top of the 0–5mm aggregate bunker. The collected dust can be transferred from the filter hopper into the ‘dust bin’, leaving no surplus dust to be disposed of.
Enviroflo Engineering Ltd (EEL) – now a NALCO-owned company – have been involved in the quarrying, aggregates and coated-stone industry for more than 30 years. For the past five years EEL have acted as engineering agents for NALCO and have co-operated on a number of schemes in the UK, including CEMEX’s Halkyn and Taff’s Well quarries, and Aggregate Industries’ Glensanda operation.
In addition to dust-foaming agents, NALCO also offer a range of dust-control chemicals, including: dust binders for rail wagons, haul roads and stockpile stabilization; dust tackifiers; surfactants; humectants; anti-foaming agents etc.
For further information, contact: Enviroflo Engineering Ltd on tel: (01902) 784848;
email: sales@envirofloeng.com; or visit: www.envirofloeng.com