Training And Competence
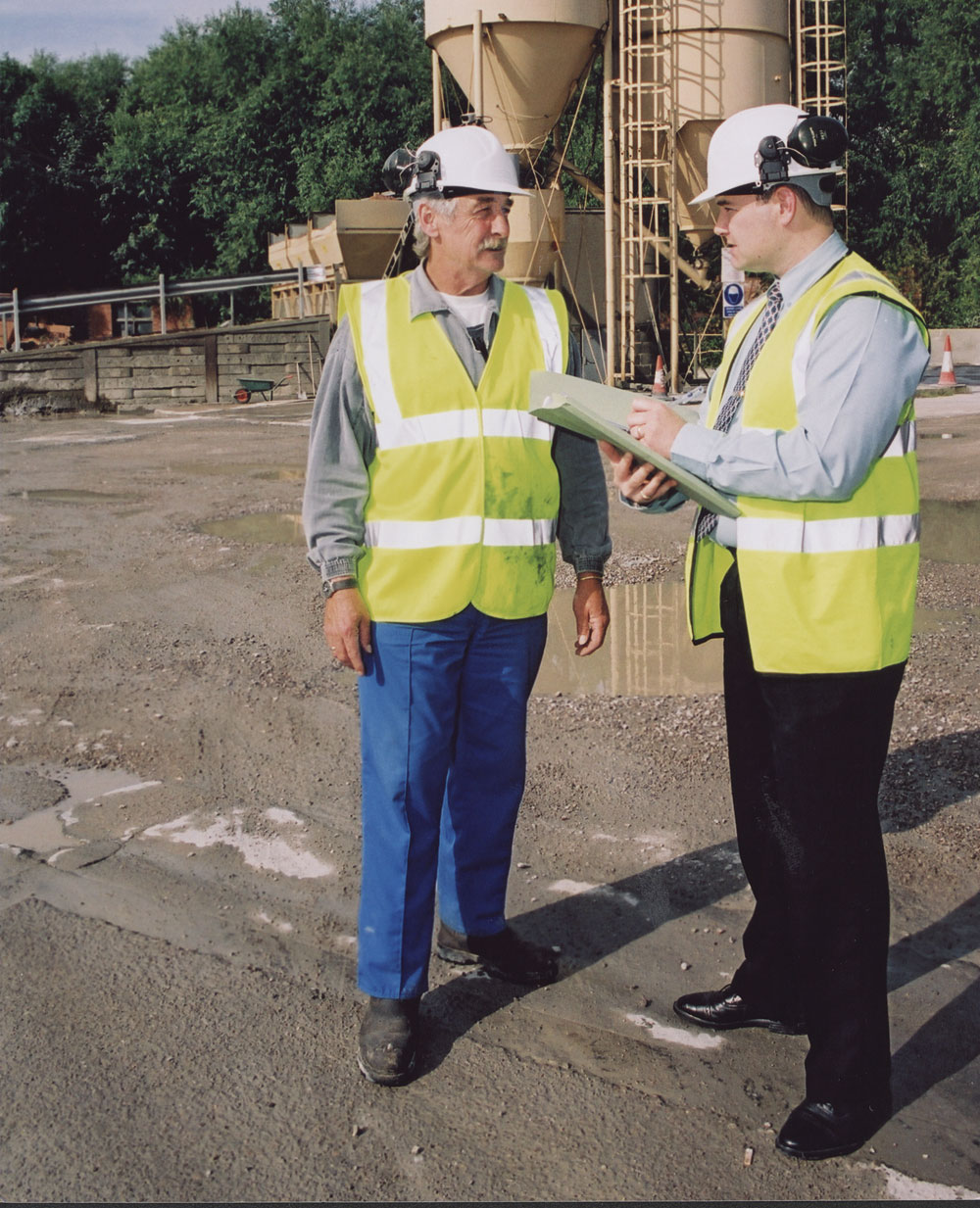
Improving skills to maintain a safe and environmentally acceptable workplace
A highly skilled management and workforce are vital to a company’s competitiveness and business success. All employees need to have relevant and current skills and the knowledge and ability to apply them if companies are to be able to respond to market changes, increasing customer demands, and, particularly in the extractive and minerals processing industries, maintain a safe and environmentally acceptable workplace.
The sector has a poor safety record, arguably the worst in UK industry. While workplace safety has always been a high priority for most operators, the last few years have seen a burgeoning awareness among the industry’s major stakeholders of the need to increase the effort and the resources applied to improving this unacceptable safety record. These have primarily been applied to the introduction of improved working practices, new technology, better safety-management systems, and the development of a positive safety culture in which all employees, whether directly or indirectly employed, make a vital and essential personal contribution to improving workplace safety.
The Health and Safety Commission (HSC) introduced the Hard Target Initiative in 2000 as a positive and innovative effort to bring the major stakeholders together to tackle the problem of the industry’s safety performance. The stakeholders include: employers, Health and Safety Executive (HSE), trade associations, training organizations and academic institutions. Those stakeholders committing to the Hard Target Initiative have pledged to reduce the level of major accidents by 50% by 2005.
EPIC is party to the Hard Target Initiative, and this paper discusses some of the contributions it has made in the fields of training and competence.
The benefits of having well trained, competent staff have always been recognized. However, some three or four years ago the impending introduction of the Quarries Regulations 1999, with their specific requirements for competent staff at quarries, caused the sector’s stakeholders to determine the most appropriate means of assuring competence through accredited assessment and certification.
EPIC began to explore the options for competence assurance and this led to the introduction of National Vocational Qualifications to the sector. EPIC established itself as an Awarding Body that is operated separately from its training arm, and EPIC Awarding Body began the task of developing, or steering the development of, sector-specific awards.
In June 1999, the employer members of the EPIC Council committed formally to an N/SVQ programme whereby 50% of the workforce would achieve a level 2 award, or its equivalent, by 2004 and a further 20% would achieve a level 4 award, or its equivalent, within the same timescale. Although pre-dating the Hard Target Initiative, this commitment to N/SVQs has become a key feature of the drive to reduce accident rates for those companies involved.
The background to the introduction of N/SVQs and the progress to date is discussed in this paper.
Competence assurance
Some three or four years ago, EPIC, on behalf of the sector, began to investigate and to inform and advise the sector on the topic of competence assurance. The initial emphasis was on the operation of mobile plant and processing plant. This was because transport activities were responsible for a major proportion of incidents resulting in fatalities, injury and damage to plant, equipment and property, and the operatives form by far the largest occupational group in the sector.
The route indicated was competence assurance through vocational qualifications. National Vocational Qualifications (NVQs) in England, Wales and Northern Ireland and Scottish Vocational Qualifications (SVQs) in Scotland became the preferred schemes, at least for the major employers in the sector. Sector-specific awards were introduced for mobile plant operatives, road-surfacing operatives, process plant operatives and drillers at level 2, and for shotfirers at level 3.
The HSE are supportive of N/SVQs as a means of assuring competence and this is evidenced by the inclusion of the NVQ definition of competence in the Quarries Regulations 1999 (Approved Code of Practice, Guidance Note 72).
While not all companies in the sector are able or wish to commit to an N/SVQ programme, the level of interest and commitment generated since their introduction for operatives has stimulated interest in the development of sector-specific awards in Health, Safety and Environmental Management in Quarries at levels 3, 4 and 5, sponsored by The Institute of Quarrying. These awards are now available and companies are preparing to register candidates when the requisite infrastructure is established.
This commitment to competence assurance is now, of course, part of the Hard Target Initiative, a larger and more comprehensive drive to improve the sector’s safety record.
Defining competence: What is it?
Competence in employment can be defined in a number of ways, but a useful starting point would be a simple one, such as: ‘the ability of an individual to perform activities within an occupation to required standards set in employment’.
To be competent in this respect, an individual employee must have the necessary underpinning knowledge, understanding and skills, and the ability to apply them consistently in his/her job. Competence is therefore directly related to performance in the workplace, and not to attendance on training courses or the achievement of academic qualifications, although these are important tools for developing competence.
Competence derives from a number of factors, in particular, training, experience, knowledge and skills, and such other qualities that a person may require to achieve effective performance in a job role.
The model for competence for the sector is the statutory definition found in the Quarries Regulations 1999, Regulation 2, which defines competence as: ‘competent in relation to a person means a person with sufficient training, experience, knowledge and other qualities to enable him properly to undertake the duties assigned to him’.
There is, therefore, a clear statutory definition of competence as it applies to health and safety at quarries, but this could and should be used as the definition for all activities in the sector.
In determining whether a person is competent, an employer should, therefore, take into account all the elements defined in Regulation 2 in terms of: training received, through an examination of training records; experience gained, through a review of job history and testimonials; and knowledge, through questioning and observation, and also through examination of training records. The need to determine an employee’s ‘other qualities’ depends on the job role.
Further guidance on the definition of competence, to aid employers to select the competence assurance route, is given in Regulation 9 of the Quarries Regulations, where Guidance 72 of the Approved Code of Practice (ACOP) quotes the NVQ definition of competence as: ‘the ability to apply knowledge, understanding, practical and thinking skills to achieve effective performance to the standards required in employment. This involves solving problems and being sufficiently flexible to meet the changing demands’.
The inclusion of this definition in the regulations has been interpreted as a confirmation of the suitability of the adoption of N/SVQs as a means of competence assurance of employees and, as stated previously, this and other factors led to the decision of the EPIC Council to formally commit to the N/SVQ system.
Competence assurance is the means by which competence of individuals can be verified, and is based on defining job performance standards and measuring the competence of employees against these standards.
N/SVQs are assessed and awarded within a competence assurance framework involving the Regulatory Body, the Awarding Body and the Approved Centre. The Qualifications and Curriculum Authority (QCA) is the regulatory body for England, Wales and Northern Ireland, while the Scottish Qualifications Authority is the counterpart organization for Scotland.
EPIC Awarding Body is the awarding body for the sector and its role is to assure the competence assessment process through external verification, give guidance to approved centres, process claims for certification and issue certificates. Approved Centres are the organizations that register candidates and carry out assessments. They can be set up within a company, provided by a commercial external provider, or by a college. Competence assurance within the Approved Centre is conducted internally by an internal verifier. Most of the major employers have registered as Approved Assessment Centres using their own staff to carry out assessments.
N/SVQs are based on National Occupational Standards, and those for the sector-specific awards listed earlier have been developed by EPIC through industry consultation.
In very simple terms, National Occupational Standards:
- define individual competence in performance terms
- deal with what individuals can do and not just what they know
- define the skills required
- define the underpinning knowledge required
- require that the individual demonstrates an understanding of the knowledge requirements
- promote best industry practice.
Effective training is crucial in developing the competence of individuals. As with assessment, training should be designed and delivered to a specification or standard and, where they exist, this should be the National Occupational Standard. The training method must be appropriate to the individual being developed, within the context and environment in which the competence is deployed. The timing and frequency of the training input is also important so that the employee is properly prepared for assessment and supported thereafter.
The occupational profile of the sector
In March 2001, EPIC published its Skills Foresight Strategy for the extractive and mineral processing industries, for the period 2001/2 to 2003/4, to identify and disseminate the skill needs for the sector. The report summarizes the sector’s skill needs, both nationally and regionally, and highlights priority areas for EPIC to engage with key stakeholders. Data available to EPIC from the EPIC Employer Survey completed in 1999, updated research and cross-referencing with other surveys were used to compile the report.
All three parts of the sector (quarrying and quarry products, kaolin and ball clay production, and coal mining) are heavily concentrated in terms of employer size. The five largest quarrying and quarry products’ employers account for 77% of employees in the four categories of: quarrying stone for construction; operation of sand and gravel pits; quarrying of limestone, gypsum and chalk; and quarrying of slate. They also account for 34% of the total number of employees in the sector overall. The occupational structure in the sector is shown in table 1.
Employers in the EPIC Employer Survey were also asked to provide information about the qualifications held by their employees. The data, shown in table 2, suggest that the density of qualifications was very high among senior management and professionals; high among middle and unit management and, with the exception of laboratory and engineering staff, very low within all other occupations.
Sector-specific N/SVQs
Information collected in the 1999 EPIC Employer Survey about the types of sector-specific N/SVQs showed that the numbers of employees holding, or working towards, these awards were concentrated in the larger employers in the sector, ie those with 200 or more employees — this is still currently the case. The sector-specific N/SVQs available and the position, as reported in the EPIC Skills Foresight Strategy for 2001/2 to 2003/4 Report, is shown in table 3.
Since the survey, several awards have been withdrawn — Mobile plant operations, level 1 (MP1); Mobile plant operations, level 2 (MP2); and Roadbuilding, level 1 (RB1). Level 2 awards for mobile and process plant operatives have replaced these, with many candidates registering for them. Other new awards in Health, Safety and Environmental Management at levels 3, 4 and 5 have recently been accredited and are available to the sector.
The take-up of sector-specific N/SVQs has increased as a consequence of the sector’s commitment to the level 2 targets. The situation at the end of January 2002 is illustrated in figure 1.
Competence assurance through EPIC
Many of the larger employers in the sector have taken up N/SVQs as the main means of assuring the competence of their staff. There are, however, other options where N/SVQs are not appropriate. This can be particularly important for smaller businesses, where the resources may not be available for an N/SVQ programme, or where other factors militate against its adoption. EPIC can offer alternatives and these are described, together with the N/SVQ suite of qualifications, below.
N/SVQs
Industry-specific awards available are: Specialized mobile plant operations, level 2; Process operations, level 2; Drilling operations, level 2; Shotfiring, level 3; Health, safety and environmental management in quarries, levels 3, 4 and 5.
In addition, EPIC jointly offers, with another awarding body, Laboratory and associated technical activities, level 3.
EPIC Mobile Plant Operator Competence Assessment Scheme (EMPOCAS)
This is an accredited scheme using EPIC-licensed external assessors, engaged through EPIC, or in-company licensed assessors to conduct assessments of operatives on specific items of plant. Not as exhaustive, nor as comprehensive as an N/SVQ, it nevertheless provides competence assurance against a standard which takes into account relevant parts of the National Occupational Standard. It is useful as a machine-specific assessment and can be used in conjunction with related training, such as health and safety, undertaken by the operative. Where an operative has achieved an N/SVQ, EPIC recommend that this assessment is repeated at periodic intervals, to reconfirm competence, or whenever new plant is being introduced.
Training for competence
Experience gained from the fairly rapid adoption of N/SVQs, and the resultant increasing assessment activity, showed that the previous training and experience and prior competence of candidates varied quite significantly. Assessors often found shortcomings in candidates’ competence, and so training interventions were required. Thus the assessment process became a useful tool to identify training needs. The underlying reasons for the variations can be attributed to prior training being delivered and assessments being made against standards which were not based on the National Occupational Standards that the new sector-specific N/SVQs use. This information is useful for training providers who can use the National Occupational Standards in the design of training programmes that prepare candidates for N/SVQ assessment.
Figure 2 is a simple illustration of the process that training providers should follow to ensure that training is focused and related to the standard of competence that the trainee is working towards.
The training cycle is based on the Training and Development Lead Body’s (TDLB) standards and it is in the planning and design stages that reference to the National Occupational Standards is important, both in terms of content and type of training, as the training provider has to take into account the environment in which the candidates are working.
Types of training
There are essentially four types of training that are used by companies in the sector:
- in-house training
- on-the-job training
- externally provided
- toolbox talks.
In-house training is provided by a company’s own staff and has the potential benefit of being relatively low in cost. This, however, is not always the case, as companies continue to downsize and resources need to be directed at core activities, in which case external training provision may be a more economic option than in-house training.
On-the-job training is particularly important in the quarrying industry where the trainee is often trained in the working environment. It usually involves working under the instruction and supervision of a competent person and is the type of training referred to in Regulation 9 of the Quarries Regulations 1999. A typical example of where on-the-job training is used is in the training of shotfirers.
External training is provided by outside training providers through public or in-company courses. The latter can be standard courses customized to meet a company’s particular requirements or bespoke courses. EPIC Training Organization delivers external training through its own staff in the case of instructional techniques and in a number of seminars, and through third-party providers as listed in the EPIC directory of training programmes.
Toolbox talks are widely used in the sector and are a very useful means of imparting knowledge on a wide range of topics and issues, many of which can be company, site or even occupation specific. Managers and supervisors often deliver them and they can, therefore, be a way for management to gather very valuable feedback from the workforce.
Meeting training needs through EPIC
Some 12 months ago EPIC reviewed its policy for meeting the training needs of the sector. In addition to feedback from the industry there were some valuable lessons learned from the increased take up of N/SVQs and a growing demand for accredited courses that include assessment of course-member performance and/or learning.
As a result of this review, it was decided that EPIC was well placed to meet the needs of employers by providing effective training through approved third-party providers, delivering courses on their behalf. EPIC has, as a consequence, built up its capability to deliver a wide range of health and safety training courses that are either bespoke, adapted to a particular company’s requirements, or standard accredited courses from external bodies such as IOSH.
In parallel with this approach, EPIC also developed its previous accreditation protocol so that employers requiring EPIC accreditation can request that a training provider submits a course to this process, which is essentially one of due diligence on the provider and quality assurance of the course design and delivery.
Training providers also have the option of pre-empting an employer’s request by proactively submitting a request for accreditation.
The accreditation process recognizes two types of courses:
- EPIC-accredited courses leading to a Certificate of Achievement awarded after assessment
- EPIC-approved courses with no mandatory assessment criteria and which lead to a Certificate of Attendance.
A third strand of EPIC’s approach is to identify appropriate training courses and providers and to make this information available to members. An EPIC Training Information Bank is being compiled which will provide a comprehensive guide to EPIC training courses, accredited training courses and approved training providers. Eventually this will be available in a hard-copy format and on EPIC’s website.
EPIC as training provider
All EPIC courses have been developed through consultation with employers and the range of topics and activities and workgroups addressed is expanding, thus providing a comprehensive training and learning resource for the sector.
One area of training, ie mobile plant operator training, requires special mention because of the experience gained from the N/SVQ programme. This demonstrated that the extent and quality of training varied widely, not only from company to company, but with different operators in the same company. As a result of this, EPIC has updated and improved its mobile plant operator training scheme and guidelines.
Employers should have a training policy in place for basic mobile plant operator training that provides a statement covering:
- pattern of operator training to be adopted
- where training is to take place
- allocation of plant and resources to basic training
- commitment to safety-awareness training and to basic-skills training in machine operations prior to working machine under production conditions
- procedures for recording training achievement and operator-competence assessment.
The recommendations are for an initial basic-training programme to be carried out away from the active working areas, followed by a period of improvement when the trainee operator implements the training and gains experience in a fully operational environment. The guidelines recommend a period of initial training of three days, followed by 150 machine hours experience. This would be followed by assessment, and, if competence is demonstrated, the issue of a Certificate of Competence, which is valid for five years. The model in figure 3 illustrates this process.
Where the employer exercises the option of registering the operator as a candidate for N/SVQ in SPMO 2, the EMPOCS certificate would be accepted by the assessor as supplementary evidence to support competence and may, therefore, shorten the assessment period.
EPIC training products
In addition to training courses and assessment services, EPIC has a number of products to support employers in the effort to reduce accidents.
Toolbox talks
A range of talks covering health and safety issues are available, as well as optional training packages to develop skills in writing, evaluating and presenting toolbox talks. These are to be reviewed through consultation with employers to determine any new requirements in terms of topic and mode of delivery.
Quarries’ health and safety checklists
This is a new management tool developed by EPIC on behalf of the HSE and is shortly due for release on CD-ROM. The checklists cover the requirements of the Quarries Regulations 1999 and other health and safety legislation, such as PUWER and LOLER. The checklists can be used to carry out safety audits, benchmark safety-management systems, as well as being used for a comprehensive and extensive range of physical standards inspections. Every question in the checklists has a reference to the legislation so that users can check basic legal compliance. Ideal for SMEs, the checklists can be adapted to suit a company’s individual circumstances. The checklists can also constitute part of the health and safety document required to be kept at a quarry by virtue of Regulation 7 of the Quarries Regulations 1999. The checklists have been endorsed by a number of organizations including the Quarries National Joint Advisory Committee (QNJAC).
Conclusion
There are almost 40,000 employees in the extractive and mineral processing sector, not including those engaged in deep mining. Over one third of those employed are operatives who are, or should be, competent to N/SVQ level 2 or equivalent. Many of them work in a hazardous environment, in an industry with a poor safety record, but which senior management are committed to improving. In addition to the need to improve safety, the commercial pressures on the sector require a competent, highly motivated workforce to meet the many challenges it faces, while maintaining its competitiveness.
Effective training, based on clearly defined standards, followed by competence assessment of individuals, is essential if companies are to maximize their contribution and secure the commitment of the workforce.
The introduction of the new Health, Safety and Environmental Management in Quarries N/SVQ is an important event for the sector, providing options are provided for employers to assure the competence of responsible management or supervision of quarries and quarrying activities and personnel. Furthermore, by exposing managers and supervisors to the N/SVQ process, which hitherto has been confined to operatives, employers will be taking another step towards achieving the positive safety culture they are pursuing by promoting the safety-biased N/SVQ ethos and engaging the decision-makers and leaders in another process to improve safety performance in the workplace.
Options of competence assurance are available for those companies that have not committed to N/SVQs. The NVQ definition of competence, nevertheless, provides a useful guide for employers to use in providing training for, or selecting the means of assuring, the competence of employees.
Early indications based on the accident statistics for 2000–2001 are that the Hard Target Initiative is working and safety performance is improving at the target rate. The means of achieving the Hard Targets are many and varied, but every committed stakeholder is making a valuable contribution.
Finally, training and the development of competence of management and the workforce are not, of course, the only means of meeting the industry’s Hard Target challenge.
Strong leadership of sound organizations with robust systems and stringent controls and suitable plant, machinery and equipment are also necessary. Where competence is assured and all the other ingredients for success are present, the final requirements are for the right attitudes, positive constructive behaviours and total commitment from everyone. This should ensure a positive business culture where safety is paramount and which involves all employees whatever their role.
The author, David Allan, is senior training advisor with EPIC Training Ltd