Watergel or Emulsion: Which is the better bulk explosive?
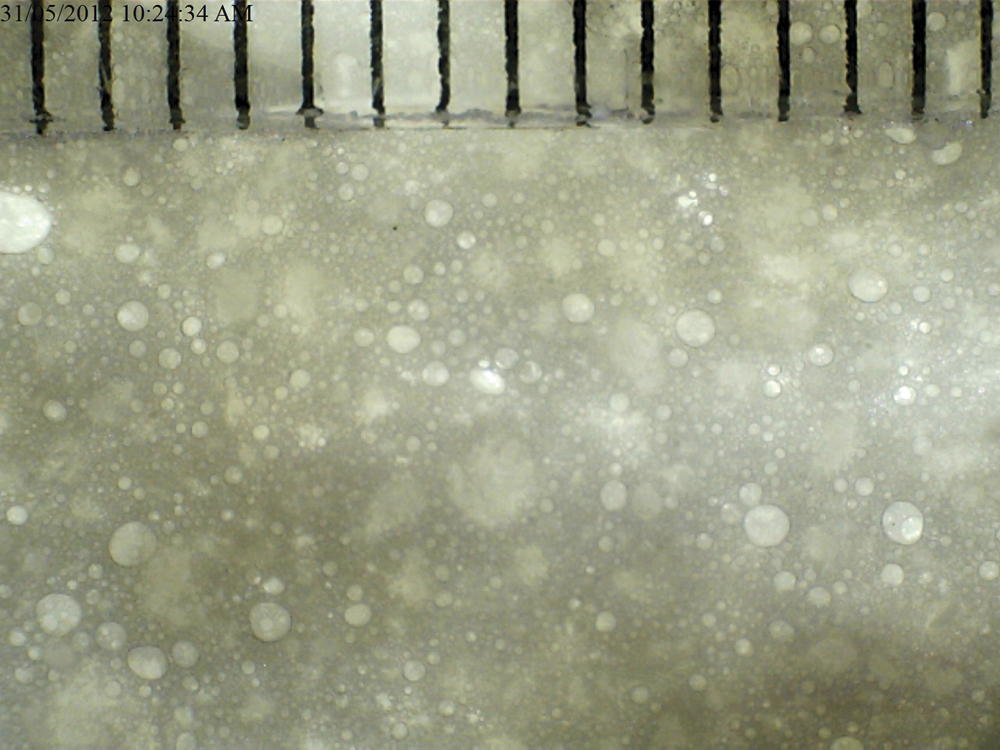
In the contest between watergels and emulsions for the perfect bulk explosive, Brent Buffham, technical manager with Maxam, explains why the company’s Rioflex variable-density product is arguably the best compromise
The history of commercial explosives is relatively short. Only 140 years ago the world was restricted to black powder and nitro-glycerine-based explosives. In today’s world of resource extraction, there is an explosive for the majority of situations and applications, but what does this mean for the user? It means choice, and with choice comes compromise – between explosive performance and cost. Is there a ‘perfect’ explosive for your needs?
The explosive supply and manufacturing industry is the same as any other commercial entity that provides something for sale. The saleability of a product is based on raw material costs, availability, the technology available, manufacturing and transport costs versus the possible returns from the sale of the product. Consider if the price of corn was raised to the same value as that of gold; consumers would see corn flakes disappear from the supermarket shelves overnight. The cost of manufacturing corn flakes would negate the returns achievable. The same is true for explosives, as is the adage of ‘getting what you pay for’. Everyone wants a bargain, but at what cost? With explosives, that cost is available useable energy.
Many companies in the explosives industry tailor their products to suit their resources and their market. Traditionally, Maxam supply quarries and smaller mines and Rioflex produces exceptional results for these consumers. Thanks to this robust and reliable product, Maxam have seen their quarry market share grow.
Rioflex, Maxam’s bulk variable-density product, is placed in the category of an ammonium nitrate suspension gel. This essentially means that Rioflex is a watergel in the traditional sense. However, the watergels of yesteryear are not the same as the Rioflex matrixes of today. Emulsions, when they first arrived on the market were hailed as the ‘future of explosives’, and statements and papers were produced to support the technology change. The use of electron microscopes to show the intimacy between oxidizer and fuel produced undeniably great imagery. The measurements of oxidizers in a 100% emulsion phase were compared to the size of oxidizers in slurries (watergels) from the 1990s. Various companies used this as evidence that the product would have a higher velocity of detonation (VoD) and, therefore, be a better and more advanced technology.
However, the situation in the early days of emulsion development is probably not as relevant to how emulsions are made in today’s market. Cost, as mentioned before, is the driving force in how products are made and marketed. Emulsions are traditionally aimed at large-diameter blasthole markets in large-scale mines where single blasts can consume in excess of 500 tonnes of bulk explosives. Although clients now want the best deal, they remain oblivious to the rising cost of production and development of blasting products. Thus, the key for an emulsion supplier is to make the emulsion-based explosive cheaper, which is likely the reverse of the reason for their development in the first place. To do this water may be added, resulting in less energy.
Slurries or watergels get their name from being partially composed of water and containing long carbon-chain molecules that are cross-linked to a gelled, semi-solid state. Thus, the name ‘watergel’. Emulsions were derived to take the energy thief – namely water – out of the gel. With the expanding oil market, copious oil derivatives were produced and emulsions became cheaper to manufacture. Then the emulsion phase needed the addition of explosive-grade ammonium nitrate prill (PPAN); this process is called doping. The most common and cheapest water-resistant bulk explosive is a 70% emulsion with a 30% ammonium nitrate dope. What the explosives suppliers realized is that emulsions needed to be made with water as well to make them more cost-effective, as water is a low-cost additive. The gain of liquidizing the oxidizers for intimacy is soon reduced by the addition of ammonium nitrate prill and the introduction of water to the emulsion phase. The ultimate energy thief for an explosive is water. Therefore, to make high-energy explosives, water content must be reduced. Water provides no energy to the bulk explosive when detonated. Water’s vaporization essentially steals energy. In order to heat 1kg of water to vaporization, 2,256 kilojoules per kilogram of energy is required.
So, if water gels have water and emulsions have water, how is one better than the other? Rioflex is not a typical watergel. It is made with high-grade and refined short carbon-chain fuels. This fuel is nitrated and normalized and, along with this, ammonium nitrate is dissolved into the solution making the base suspension media of the matrix. Contrary to popular articles on watergels, water content amounts to less than 13% of the final mix. The suspension media has more ammonium nitrate prill (either high-density prill or porous explosive grade) added, though not before it has been crushed and made angular. This crushing process takes the previously round ammonium nitrate and increases the surface-to-mass ratio, thereby significantly increasing the reaction speed and, in turn, the VoD of the bulk product. At this point, a very small percentage of water has been added, so where does this watergel get its name? Perhaps it is the same as when horses and carts used to travel the streets? They were not called streets, they were called carriageways. Today we have dual carriageways but no horses and carts; and we have watergels with less water than emulsions.
This is where the water plays its part in protecting and stabilizing the product. The carbon chains used in gelling are long and all ravelled up into a little ball. They require a medium to be suspended in so that they can unravel, through hydration. In order to do this, Maxam use a small amount of water to suspend the fuel and oxidizer, and that is it. Of all the explosive phases or matrixes on the Australian explosives market, Rioflex has the least water content. Other manufacturers in the market may add up to 23% water to the emulsion phases of their bulk products.
It is important to understand that emulsions of any type, explosives or not, use a chemical (emulsifier) to blend two or more immiscible (unblendable) liquids together. As emulsions (in terms of explosives) are waxes, oils and oxidizers in water, they have to be over-fuelled, in general terms, to reduce noxious fumes of nitrous oxide when doped with ammonium nitrate. Rioflex is perfectly formulated to ensure a near-neutral oxygen-fuel balance that, together with the intimate encapsulation of highly angular ammonium nitrate, produces the optimal base matrix.
The gain that the industry achieves with emulsion phase explosives creates a false economy, robbing Peter (energy) to pay Paul (procurement). Many explosives users understand that what you spend on drilling and blasting results in improved production in the quarry as well as through the crushers or mills, in orders of magnitudes. So, to answer the question that was posed earlier: ‘Is there a perfect explosive for your needs?’ The answer is yes.
This article first appeared in the August 2012 edition of Quarry, the official journal of the Institute of Quarrying Australia, and is reproduced here by kind permission.