Stemming Plugs
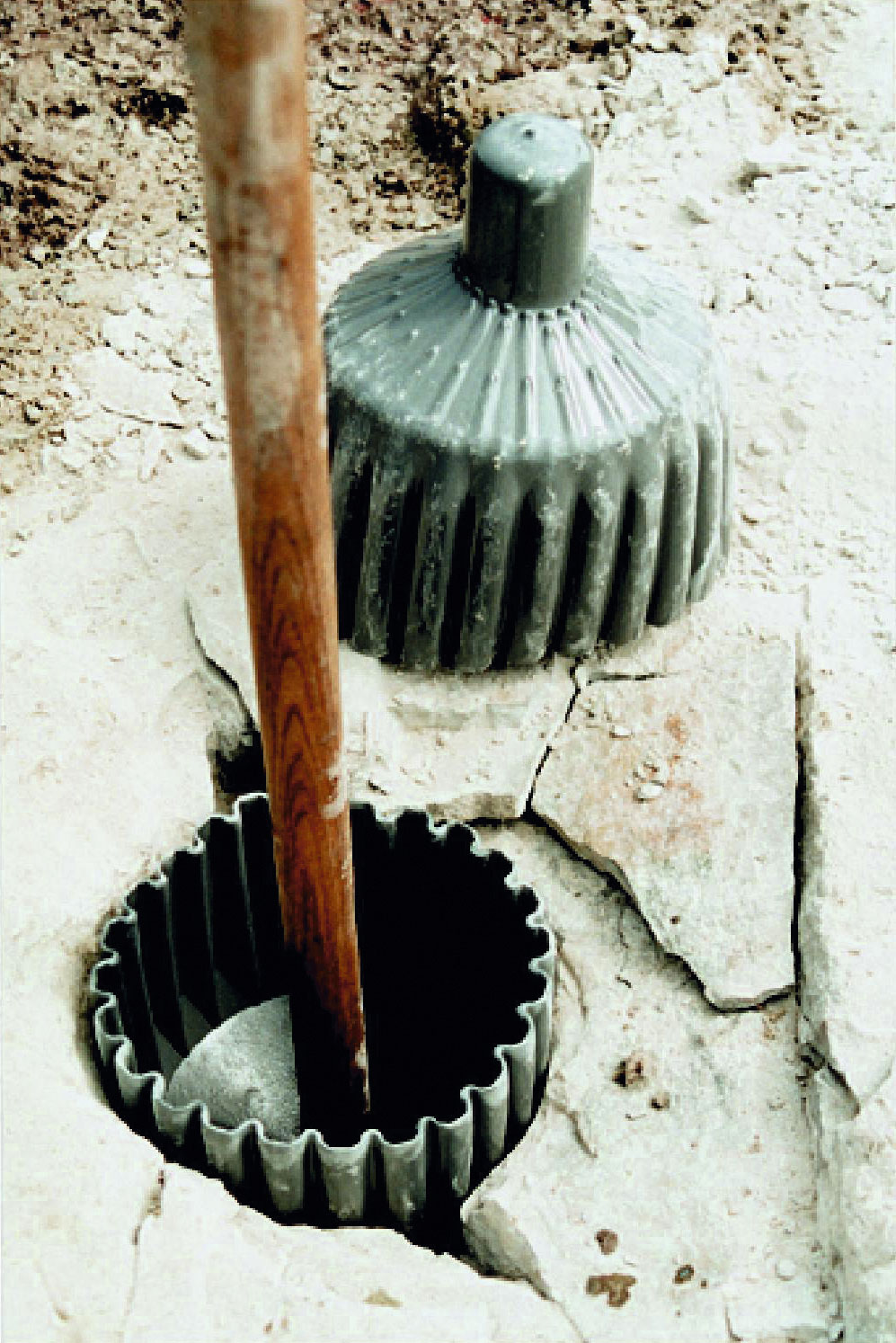
Can they improve blasting and productivity?
by Douglas A. Bartley, president of US-based DBA Consulting, Inc.
Of the various products introduced to improve blast performance, flyrock control and productivity, stemming plugs have been looked upon with some disbelief and uncertainty.
Typically, the loss of explosive energy through stemming ejection reduces the performance of the blast. The fundamental theory promoting the use of blast-improvement and containment plugs is that they could improve the effectiveness of stemming material in the blasthole. As a result, this would better contain the explosives energy within the rock mass and yield a more controlled and efficient blast.
The three keys to efficient blasting are:
- Energy level — the amount of available energy in the explosive product.
- Energy distribution — the optimized linear distribution of the explosives in the rock mass.
- Energy confinement — the optimized burden to energy ratio.
The optimum stemming column height is determined to provide proper energy confinement while still allowing for maximum explosive energy distribution in the blasthole. The measure of the effectiveness of the available explosive energy to both break and displace the rock mass is proportional to the effective burden that energy must overcome. This relationship is a crucial element in basic blast design.
Testing procedures were conducted at Better Materials’ Rich Hill Quarry in Connellsville, Pennsylvania, (now a subsidiary of Hanson Building Materials America, Inc.) to provide data to quantify the performance of Vari-Stem stemming plugs within the parameters of rock fragmentation, crusher throughput and blast control. The site was selected because the company had already achieved a high level of blast optimization through their drilling and blasting practices.
A series of five production blasts were monitored. The first two blasts were initiated without plugs to establish baseline data and the last three blasts were detonated using Vari-Stem plugs. A high level of field control was maintained during the drilling, blasting and data-collection processes in order to ensure the integrity and accuracy of the data throughout the testing procedure.
The blasts were symmetrical to one another in terms of their geometry and loading parameters and were all timed using Daveytronic programmable electronic detonators. The use of electronic detonators to eliminate timing scatter significantly increased the reliability of the study’s findings.
Several of the blasts were filmed using a Redlake high-speed digital video recorder at a frame rate of 500 frames per second. The camera zoomed in to the surface of the bench directly above the first hole to be detonated in the face row of the blast. A surface electronic signal detonator was programmed with the same firing time as the in-hole detonators of the explosive column below.
The purpose of this test was to determine the amount of time elapsed (Dt) between the explosive detonation and the vertical heave and gas venting above the blasthole. Any increase in the Dt would indicate a higher level of energy containment. This would allow the expanding gases to potentially penetrate deeper into the micro-fractures of the rock mass, thus increasing fragmentation before the gas pressure head is dramatically reduced with burden movement.
Following each blast the resulting rock pile dimensions were documented and an optical fragmentation analysis was conducted throughout the excavation of the shot rock. The primary crusher throughput was also monitored during the excavation of each blast. Previous studies have demonstrated a direct correlation between improved fragmentation and increased productivity.
Field Controls
Throughout the study close attention was paid to maintain a high level of field controls. These field controls were monitored and applied as they related to bench preparation, pattern layout, blasthole drilling, blasthole loading procedures and post-blast data collection.
The implemented blast design during these test blasts used a 63?4in blasthole drilled to a bench depth of 55–60ft. Four rows of holes were drilled on a 15ft x 20ft staggered pattern. In order to ensure proper toe burden dimensions, set-back markers were placed prior to the detonation of each blast to ensure the correct placement of the following blast’s face row holes.
The production blasts were loaded using an Iremix 40% emulsion blend. A 40lb high-energy toe load of SEC Sluran-600 was placed at the bottom of each hole prior to the bulk loading of the emulsion product. Prior to the blasthole loading each of the holes was again measured to verify the correct depth and the presence of water. If water was encountered the hole was pumped before explosives were introduced.
The holes in the front row of each blast were stemmed with 9ft of crushed rock. The holes in the second, third and fourth rows were stemmed with 6ft of crushed rock. In the blasts that used the Vari-Stem plug, 3–4in of stemming buffer (drill cuttings) were loaded on top of the powder column prior to the insertion of the plug. Crushed rock stemming was then added to the top of the hole.
The explosive column rise was carefully monitored at each blasthole to ensure the proper explosive column height and the designed amount of stemming material were used.
Fragmentation
The fragmentation data during this study was processed using a digital image analysis system. The images were gathered using a Sony TRV-900 digital video recorder and a Sony Mavica CD-400 high-resolution digital camera, transferred to disk and loaded into an image processor for delineation and size-distribution analysis.
To ensure that the resulting merged material would be representative of the true level of blast-induced fragmentation, images were taken at the primary crusher as each haul truck emptied its load into the hopper.
Analysis of the merged fragmentation data yields showed that the post-blast rock piles from the tests that utilized the Vari-Stem plugs were composed of a higher degree of fragmented rock with a uniform size distribution than those without stemming plugs.
Table 1 contains the fragmentation data from the individual blasts and the combined analysis of the plugged and non-plugged blasts. The chart includes the mean size, D90 and D75 passing sizes.
The merged analysis of the Vari-Stem plugged blasts resulted in a 27% reduction in the average mean size of rock and a 26% decrease in the D90 (90% passing) screen size from the combined no-plug result of 12.19in to 8.96in. There was also a 24% decrease in the D75 size from 8.22in to 6.22in.
These numbers can typically be directly related to reductions in excavation and crushing costs.
Blast Control
The high-speed filming of the surface swell above the opening hole indicated that the stemming plugs effectively contained the expanding gases roughly three times longer than the non-plugged holes using only crushed stone as the stemming material.
Productivity
The primary performance parameter monitored in this study was the crusher throughput. During shifts when the primary crusher was operating, records were kept regarding the source and the total tonnage of the stone delivered to the primary crusher during each shift.
The average throughput of baseline blasts loaded without stemming plugs was 851 tons/h. The average primary crusher throughput of stone from the Vari-Stem plugged blasts was 879 tons/h, representing a 3% increase in stone throughput at the primary crusher.
Conclusions
The Vari-Stem stemming plug trials at Rich Hill Quarry resulted in performance benefits in terms of fragmentation and increased primary crusher productivity. The findings during the study provide evidence quantifying the benefits of stemming plugs in terms of improved blast performance, as represented by a 27% decrease in the mean size of rock in the post-blast rock pile from 7.89in to 5.69in, and a 3% increase in the tonnage throughput at the primary crusher.
Testing was conducted in such a manner as to demonstrate the potential productivity increase and downstream savings stemming plugs can provide. Similar test results could possibly be obtained conducting the same test procedures using pyrotechnic initiation systems in place of electronic detonators. The use of electronic detonators to eliminate timing scatter significantly increases the reliability of the study findings and can be directly related to the effectiveness of the stemming plug.
Stemming plugs are a valuable tool. It pays to be open-minded and to evaluate new technologies.