Seismograph Calibration
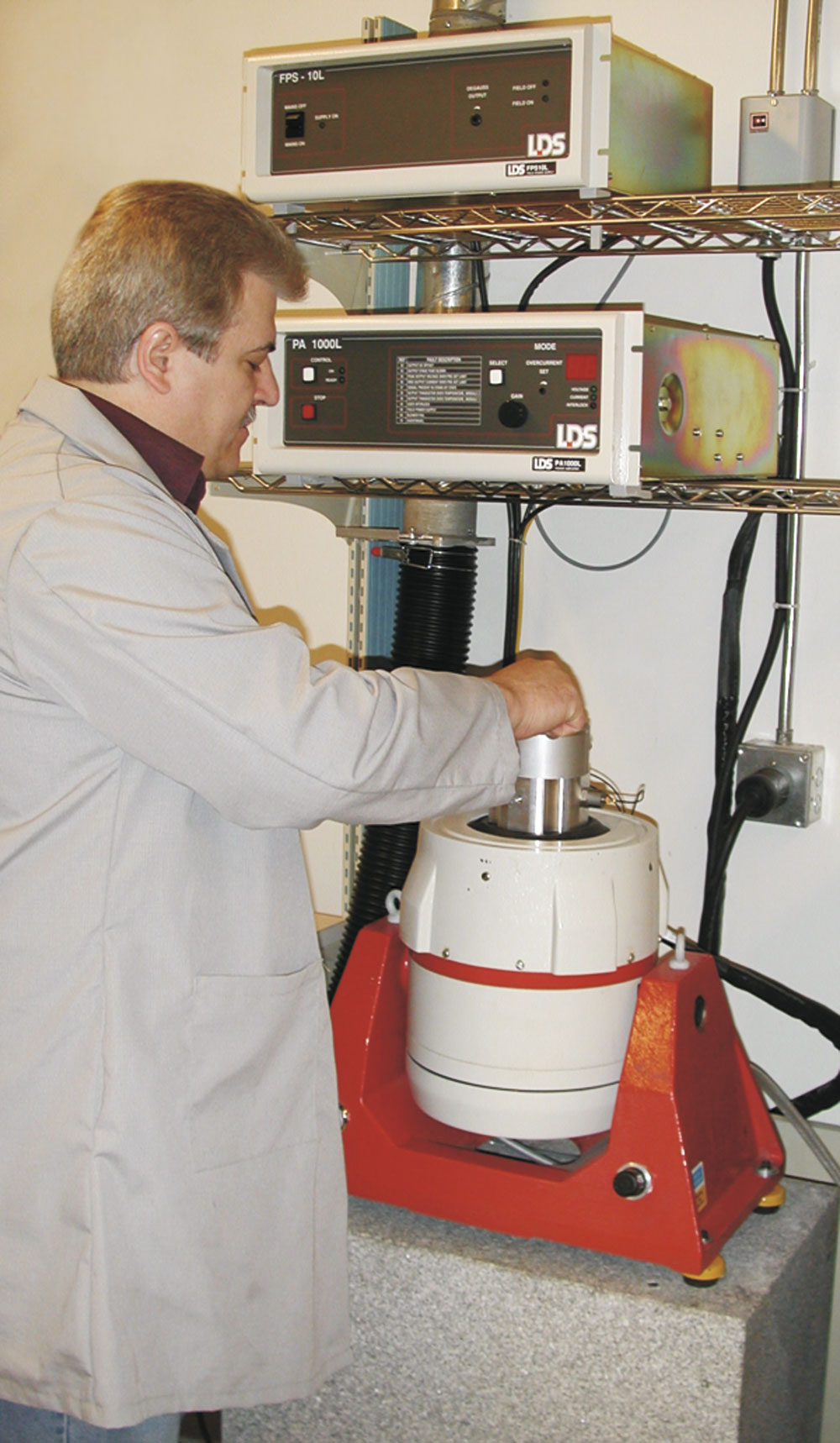
What the user should know
The dictionary definition of calibration is: to determine by measurement or comparison with a standard, the correct value for each scale reading on a device1. Blast consultants and blasting contractors assess risks every day, but how often do they consider the importance of, and the risks associated with, the calibration of their seismographs and the accuracy that they provide? Can the calibration provider back up the seismograph user in times of trouble and provide documented evidence that the equipment was functioning within specification? Can their calibration procedures withstand independent scrutiny and be shown to be traceable to a national standard for accuracy of measurement? These are important documents that, in a court of law, provide tremendous support in showing that blasting and monitoring activities are being conducted professionally and competently.
Why calibration is important
The recommended interval for the calibration of most types of measuring equipment, including seismographs, is one year. Across most of North America and many parts of Europe regulatory authorities actually require seismographs to be calibrated on an annual basis. This requirement has been, or is being, adopted by several other countries around the world and some specific projects even require that seismographs be calibrated every three or six months. Calibration is important to ensure that the instrument is performing as it was designed to, and measuring accurately the true ground vibration and airblast. Although seismographs are designed to be used in rugged environments, they are still a sophisticated electronic monitoring devices. Preventative maintenance, therefore, becomes an important part of the annual calibration process. Many manufacturers and their authorized calibration facilities will perform upgrades and preventative maintenance, often free of charge, provided the units are regularly serviced. The upgrades often include product enhancements of both hardware and software and result in expansion of the functionality of the equipment.
How a seismograph is calibrated
During the calibration process the geophones are mounted on a shake table with a reference sensor and excited at a specific frequency and amplitude. At this point the sensors are checked for the ‘as found’ condition of each channel. This must be performed before any adjustments are made. These results will allow the user to assess all of the vibration records that have been recorded since the last time the seismograph was calibrated and determine the impact, if any, on these records. The seismograph is then adjusted to match the level being recorded by the reference sensor and the geophones are checked to ensure they are within specification across the required frequency range of the equipment. Microphones are calibrated in a similar manner. They are exposed to a sound source at a specific frequency and sound pressure level and the ‘as found’ conditions are recorded. The microphones are then adjusted to match a reference microphone and, like the geophones, checked to ensure they meet the specifications for the required frequency range.
To ensure compliance, it is very important that all sensors are tested at several frequencies within their required range. For example, if a calibration service provider uses a device called a piston phone to calibrate the microphones, the microphones are only checked at one frequency and one pressure level. This frequency is typically about 250Hz and is at the high end of most seismographs’ frequency response. This is not a valid procedure because single-point calibration does not provide any indication of the response at other frequencies. The seismograph may be reading high, low or nothing at all at other frequencies within its specified frequency range.
Some seismographs are meant to have the geophone, microphone and data-acquisition unit calibrated as a system. Generally, this allows the entire system to be calibrated more accurately. However, a limitation of instruments that are calibrated in this way is that the geophone and the microphone are matched to the acquisition unit and may not be interchangeable with other instruments, even if they are of the same model from the same manufacturer, without a decrease in overall accuracy. Other seismographs may require the geophone, microphone and data-acquisition unit to be calibrated as independent assemblies. This type of seismograph should maintain its accuracy when sensors from compatible models are interchanged.
To help maintain the integrity of the recorded data, most seismographs have a sensor-checking function. Some users confuse the purpose of this function with that of the yearly calibration. The sensor check can provide valuable information about the sensors and their set-up. If a sensor has not been installed or connected properly, the sensor-check function will provide some indication of a failure. In general, the sensor check will induce an electrical pulse into the sensor that will cause the mechanical components within it to move. The seismograph in turn measures this movement, as if it were a true vibration, and the response is recorded. This response is then analyzed to make sure the sensors are operating within an acceptable range. This provides a very good indication that the sensors and unit are working properly, however the sensor check is not a calibration check and cannot replace the annual calibration process. The sensor check does not compare the measured result against an external traceable reference sensor, nor does it test all the electronic circuits that are integral to the geophone response.
What the calibration certificate means
When a seismograph is calibrated by an authorized calibration facility, the facility will issue a Calibration Certificate. This provides a list of reference equipment used in the calibration process. In order for the calibration to have any validity, the reference equipment must be more accurate than the equipment being calibrated, and must itself be calibrated by equipment of even greater accuracy which is traceable to a nationally recognized standard, such as the National Institute of Standards and Technology (NIST) in the United States. Needless to say, the agency performing the calibration must be qualified to do so. The Calibration Certificate should also contain details of the model, serial number, date the instrument was calibrated and who performed the calibration. Should an authority question a user’s seismograph records, this certificate provides documentary proof of professional calibration.
Importance of manufacturer-certified calibration
There are individuals and companies worldwide who are not certified by the manufacturer to perform seismograph calibration, yet continue to do so. It is in a user’s best interests to have their seismograph calibrated by the original manufacturer or an authorized agent.
The key factor here is the integrity of the measured record should it ever be called as evidence in a court of law. Using a manufacturer-certified facility ensures that proper procedures are followed when the seismograph is calibrated. This removes any uncertainty associated with the reliability and measurement accuracy of the seismograph. The use of unauthorized calibration facilities may cause problems in court if the reference equipment is not traceable, or if the certification documents are incomplete. In some instances, unauthorized facilities have even been known to calibrate equipment without ever updating the calibration date within the instrument. If an improper calibration date is printed on vibration records, it may call into question the validity of the report itself.
Moreover, if a seismograph ever requires repair, the manufacturer has the best experience and knowledge to find and fix the problem. They will also ensure that any replacement parts meet the specifications for the equipment. Unauthorized facilities do not have access to test specifications, procedures or parts lists and some of these facilities may use substitute parts that do not meet the functional requirements, which can lead to inaccurate vibration levels being reported.
Calibration service providers should always:
- be authorized and trained by the manufacturer
- have reference equipment calibrated to a traceable standard
- provide copies of the Calibration Certificates for reference equipment
- record the ‘as found’ condition as part of the calibration procedure
- test the microphone and geophone sensors at multiple points within their stated frequency range.
Conclusion
When a seismograph is sent for its annual calibration the user should remember to manage the associated risk. The factors listed above will help to lower this risk and provide assurances to the regulatory authority that vibration levels are being proactively monitored.
Reference
1. Dictionary of Scientific and Technical Terms, 5th Edition, McGraw-Hill.