Rock On Ground
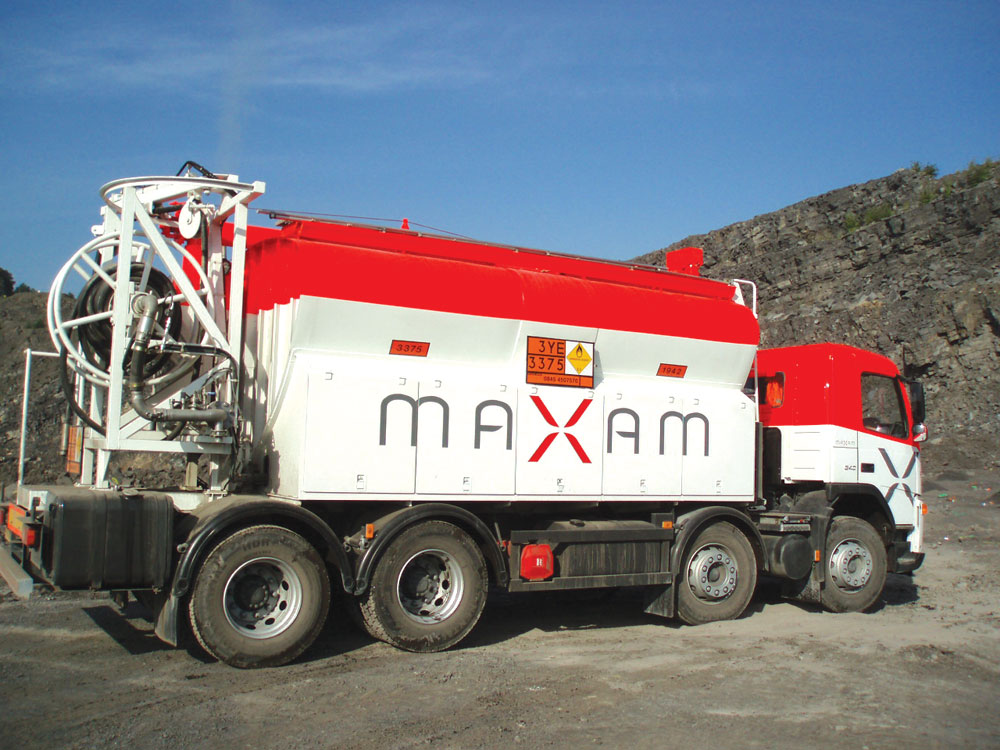
Steve Gilmartin, commercial manager with Maxam Explosives, discusses a number of important considerations for drillers and blasters
This paper looks at quarry drilling and blasting and considers some of the actions that can be taken by quarry operators and their staff, and rock-on-ground (ROG) contractors, that will lead to an overall reduction in the cost of providing broken rock as well as the cost of downstream operations.
A number of elements require consideration and action to achieve the successful, cost-effective provision of broken rock at a quarry face, each of which will be discussed in turn. They are:
- Competent drilling, blasting and surveying staff
- Efficient and effective equipment
- Explosives and initiation systems suitable for site conditions (packaged, bulk, ANFO)
- Flexible working hours and conditions
- Co-operative management team
Competent drilling, blasting and surveying staff
For safe, successful operations, today’s shotfiring teams need good knowledge of products and techniques, and an awareness of the consequences of incorrect blast design and drilling errors, typically:
- too big a burden and the explosive cannot do its job
- too small a burden and there is potential for fly-rock
- wrong hole angles can increase or decrease the burden
- wrong hole depths result in poor floor conditions
- incorrect azimuth can lead to excessive concentrations of explosive, resulting the risk of fly-rock or not enough explosive in the right place, thereby causing toes
- if the drilled holes are not satisfactory they should be put right. If this is not possible, steps should be taken to ensure the same problem is not repeated on the next shot.
The shotfiring team need to have knowledge of the tools at their disposal to assist in maximizing fragmentation; minimizing oversize, vibration and air overpressure; and dealing with water (both static and dynamic). They should be willing to embrace new, and sometimes radical, techniques and understand the basic concept of ‘mine-to-mill’ operations.
It is a fact that small additional costs at the quarry face, coupled with close co-operation between the blasting team and the face operations team, can often result in extensive downstream savings in plant wear and tear and power consumption, in addition to increased throughput at the primary crusher.
The driller, his drill rig and his knowledge are the key to good blasts. He must always follow the drilling plan but also be ready to make informed changes when the situation dictates. For instance, in poor ground he may need to move the start of the hole to a different position to the design. Once noted on the drill log, the blast designer can then make the necessary adjustments to the blasting specification.
Holes that are drilled too deep, too short or at the wrong angle/direction will either diminish the effectiveness of the blasting process or increase the risk of a dangerous occurrence. In today’s enlightened times, there is no reason why holes should not be drilled to the correct depth and at the planned angle. The trend towards lower bench heights and reduced face angles mean azimuth errors should occur infrequently, if at all.
If the drilled hole is in the correct location and to the correct depth, angle and azimuth, the job is half done. But if the hole is too deep, too short or at the wrong angle and/or azimuth, there is the probability of:
- toes and/or hard digging
- poor floor conditions
- increased vibration
- difficult drilling on the next level.
Blast personnel should be well aware of these problems and take the necessary action, eg backfill holes that are too deep and/or get the driller back to re-drill short holes. If the inclination or azimuth is consistently wrong, retrain or change the driller.
Use the right explosive to do the job. A primer and ANFO will work in many short-bedded Carboniferous limestone quarries but, if conditions dictate, use a high-energy explosive base charge to break out the toe. Use bulk emulsion or cartridge explosives where water is present. Use the correct sub-drill depth and position the primer correctly. If there is a consistent need to drill toe holes, if quarry waste is required to level the floor adjacent to the face, or if the burdens on subsequent blasts are too great, something is wrong.
The role of surveying personnel has taken on much greater importance over the last 20 years since the requirement to profile faces came into force in the 1989 Regulations, and both software and hardware have become increasingly sophisticated. However, relevant training has not always kept pace with these developments. Many ‘surveyors’ have received their knowledge having had it ‘passed down the line’. Given the decisions that are taken based on the survey, it is essential that all surveyors have the necessary qualifications, training and experience.
Efficient and effective equipment
The majority of quarries and all blasting contractors have access to quality surveying hardware and software. The use of this equipment, the correct interpretation of the results and the subsequent blast design all play a major part in the quality of the shot rock profile.
Surveying the face prior to drilling the set of holes is preferable, as this will give the blast designer the opportunity to place the front row of holes in such a way that any heavy or light burdens can be taken into account.
The drill rig is still only as good as the operator but a well maintained, modern rig with a competent operator will consistently deliver accurate blast blastholes. Most modern rigs now have automatic depth indicators and azimuth control devices, and looking to the near future it is likely that the position of the drill on the holes will be automatically set using GPS.
Site radios, well maintained shotfiring equipment and a stock of accessories, such as gasbags, Aquaplugs, layflat tubing and Rockloks, can all help in making the loading process run smoothly. Gasbags can be used to block off holes where water and cavities are present, Aquaplugs will seal off small amounts of static ground water and are invaluable when using ANFO if no packaged explosive is available, and layflat tubing will prevent ANFO running away in fissured ground.
Explosives and initiation systems
The type of explosive used is determined by the blast designer (or specified by the client). It will depend on many factors but primarily on the type of rock being blasted and whether any water is present.
While it is important to use a consistent, high-quality explosive, this factor is secondary to getting the geometry and design of the shot right. Any explosive will create broken rock; it is the way it is used that will determine the results. If the explosive is weak or of poor quality, the shot should be designed to suit. Likewise, if the explosive delivers high energy and gas volume, the shot should be designed accordingly. Patterns can be altered and explosive distribution, either throughout the hole or the shot, can be changed.
Flexible working hours and conditions
Explosive delivery trucks and pumped explosives now account for approximately 70% of the explosives used in the UK. Although this method of delivery has been around for a long time and has radically changed blasting procedures, the attitude of many quarries has hardly changed at all – the explosive is required first thing in the morning and, in the main, nothing else is acceptable.
Similarly, many quarries have ceased to hold explosives in their stores or have dispensed with the store altogether, expecting deliveries to be made on the day of the blast. Once again, if the delivery cannot be first thing in the morning it is regarded as unacceptable.
Flexibility with respect to delivery times and firing times means the explosives suppliers can arrange their delivery schedules in a more cost-effective way, resulting fewer truck movements and, hence, lower delivery charges. The reason often given for early deliveries is that it leaves plenty of time should something go wrong – but how often does this happen? If more rigorous controls were placed on pre-loading operations (profiling, drilling, hole management etc), the chance of a problem is diminished. All too often a shot is loaded and ready to fire by tea break, but is then left until lunchtime for firing. Quarries should consider firing two shots in one day with one truck as, once again, the more tonnes delivered the lower the price.
Co-operative management teams
For the use of contractors to work there has to be flexibility on both sides.
The quarry, quite rightly, expects stone to be available at all times in a well-fragmented rock pile offering easy digging for their face loader. They want the best-possible price and the least disruption to their day-to-day operations. They expect the contractor to provide a competent, qualified team of operators, from drillers to blasting supervisors, who will fit in with quarry opening times, firing times, rules and regulations and SHE requirements.
The contractor, on the other hand, has to make a profit, so time is money; he wants to drill and blast as much stone in one visit as possible, maximizing the use of his drill rig and shotfiring team. He wants to get as much stone per kilogram of explosive as possible (highest blast ratio), and he wants the site manager to tell him which way the quarry is going to work, then let him get on with the job. Within reason, he wants to carry out his operation to suit his own timings.
In an ideal world the above points would come together, but breakdowns, transport problems, difficult drilling etc, all mean that extended time on one site will inevitably impact on arrival time at the next, putting pressure on all concerned.
The incidence of breakdown can be limited by carrying out planned preventative maintenance, and transport can be arranged at night so there is no impact on daytime work. Difficult drilling will always be a problem, but even here it is possible to not add to the geological conditions by over-drilling upper benches and impacting on the next bench down.
The site can help by making sure benches are cleaned off and ready for the drill rig to start, and that access roads are clear for the rig to tram to the blast site, shot piles are dug out in a timely fashion and the faces left clean for the profiler to conduct his survey.
With good relations and understanding between the site management and the contractor, the operation will go smoothly and the final result will suit everybody.
Whether carrying out in-house drilling and blasting or using a contractor, this is one of the most crucial parts of the whole extraction operation. Time, experience and dedication need to be devoted to it because, if the blasting is right, in the main the rest will follow.