Meeting The Challenge
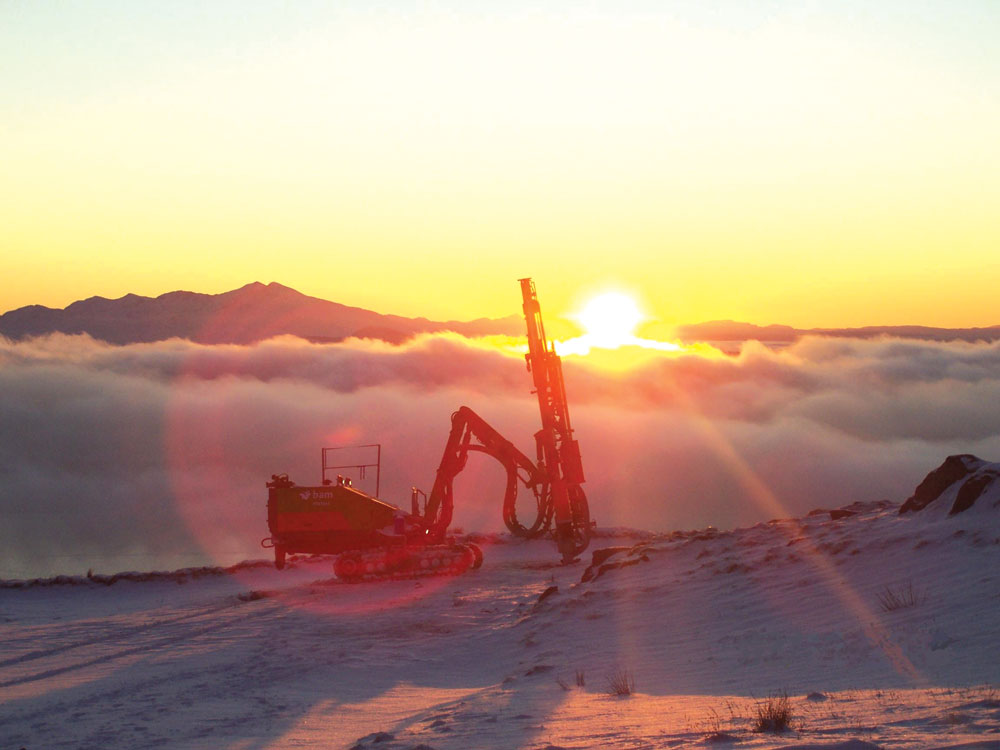
Drilling and blasting operations at Glensanda
By David Gibson, business development manager, BAM Ritchies
Situated in the West Highlands of Scotland on the north-west shore of Loch Linnhe is Glensanda, one of Europe’s largest granite quarries. The remote location of Glensanda means the site is only accessible by sea, the quarry extraction operations being carried out 500m above sea level.
These operations feed primary crushed rock down a 3.8m diameter x 300m deep shaft called the ‘glory hole’. The rock is then conveyed out of the mountain, via a mile-long tunnel conveyor, to a 500,000-tonne surge pile for further processing through the secondary and washing plants situated at sea level. All of the quarry’s products are transported by ship to UK and European markets, with occasional shipments made to the US.
Glensanda’s remote location and inaccessibility are not the only unique characteristics of the site; there are many other challenges and obstacles that have to be overcome to ensure successful blasting. During the winter months, arctic conditions are common in the quarry, with temperatures sometimes falling below –12°C. Snow drifts are a regular occurrence and, at times, wind speeds can achieve hurricane storm force 12.
When the quarry is not frozen, water can be an even greater challenge. The weather can change unpredictably and heavy showers are commonplace. The site averages 2.5m of rain per annum, and with very little storage area the run-off from the top of the mountain can increase into white water rapids as it descends the terrain. This has to be constantly planned for through development, as benches can easily be flooded.
Groundwater is a frequent problem when drilling and blasting at Glensanda as it can cause blastholes to collapse and sometimes makes charging even the good holes difficult, with large amounts of water present in the shot. Owing to the massive nature of the site, these problems can be compounded by variations in the local geology around the quarry. It is essential, therefore, that every drill hole is of consistent quality to ensure that they remain intact through the loading process.
The quarry itself, opened up and developed by Foster Yeoman over the past 25 years, is now operated as Yeoman Glensanda, following acquisition by Aggregate Industries, part of the Holcim Group, in 2006.
In November 2007 Aggregate Industries Ltd announced a contract with BAM Ritchies (a division of BAM Nuttall Ltd) for all drilling and blasting requirements at the site. The contract was procured under a comprehensive pre-qualification and tendering process, recognizing the importance of health and safety, quality and relevant experience in quarry drilling and blasting operations.
In shortlisting potential partners, Aggregate Industries interviewed BAM Ritchies and visited their offices and facilities to validate proposals contained in their tender submission. The selection of BAM Ritchies was based on value for money and their ability to meet the needs of an expanding operation at Glensanda that will grow over the coming years.
In particular, Aggregate Industries were seeking highly trained resources, modern equipment and technology and a commitment to work in a collaborative manner. BAM Ritchies demonstrated this commitment, which is expected to bring added value to the partnership at Glensanda over the five-year term of the multi-million-pound contract.
The awarding of the contract has also firmly established BAM Ritchies as the major drilling and blasting contractor in quarries in the UK, and represents the company’s largest contract of this type to date.
BAM Ritchies, whose principal office is located in Scotland, are now well established in providing this full drilling and blasting package at Glensanda for the five years from the contract’s commencement in December 2007. The operation complements the company’s other expanding quarry activities not only in Scotland, but also in England, Wales, the Isle of Man and overseas.
In 2007, BAM Ritchies reached the unsurpassed milestone of over 500 million tonnes of rock blasted since they started in business in 1966.
So, after the first 12 months of the new contract, how are the changes benefitting Glensanda? According to BAM Ritchies and Aggregate Industries, the changes have been notable and far reaching, resulting not only in increased production and reduced costs, but also leading to a significantly reduced carbon footprint brought about by fuel-efficient drill rigs and higher unit production outputs.
In addition, the use of modern rigs and methods, based upon industry-leading risk assessments and procedures, is helping BAM Ritchies’ commitment to eliminate incidents and accidents as part of their ground-breaking ‘Beyond Zero’ behavioural health and safety campaign, with its clear vision for the future.
The new developments and techniques cover all elements of the drilling and blasting operations.
Surveying and face profiling is carried out using MDL’s Quarryman Pro in conjunction with Quarry.4 from Co-Ordinated Survey Systems. Low cloud and heavy snow are common at Glensanda, with thick cloud sometimes lasting for days. This can have a significant impact on face profiling as a typical scan can take up to 45min to complete, due to the size of the faces being fired. Future improvements in technology and software will make this a much quicker and more efficient process, with the use of the fast-scan feature on the latest Quarryman Pro, combined with developments in the survey software, allowing profiles to be carried out in under 10min, thereby greatly reducing the time lost waiting for clouds to lift.
Traditionally, the site used in-house drilling with shotfiring operations carried out by Orica from an on-site bulk emulsion manufacturing plant. Drilling was carried out by two site-operated Ingersoll Rand DM-45E rigs, each drilling 168mm diameter holes, and four ECM 350 pneumatic rigs that were used for production and development blasting. A total of nine staff were employed, with the quarry regularly using contractors to ensure production targets were met. Production was approximately 6 million tonnes per annum.
Today, however, the quarry requires 7.5 million tonnes of blasted rock per annum (approximately 150,000 tonnes per week), which must be suitable for loading using Cat 992 loading shovels. This represents a drilling requirement of around 3,000m per week or 150,000m per year.
All of the drilling equipment previously used on site was decommissioned and replaced by rigs acquired by BAM Ritchies. The primary resource is two Atlas Copco L7 drill rigs fitted with COPROD systems, this being the only site in the UK to operate the COPROD system on L7 rigs. Both rigs are fitted with the COP 4050-series rock drill providing 40kW of energy at a frequency of 50Hz through the system’s special COPROD drill string, which comprises an outer guide tube and inner drill steel that carries the drill’s energy to the 127mm bit.
With the COPROD system the L7 is approximately 30% more fuel efficient in a drilling shift compared with a standard down-the-hole (DTH) machine of similar size. Having an average penetration rate in excess of 1.0m/min, the L7 has nearly twice the penetration rate of DTH machines, making the fuel economy per metre even greater.
Each L7 is capable of drilling 350m in a normal shift, drilling regulated benches on a varying staggered pattern dependant on the local geology of the quarry. It is necessary to present the blasted muckpile in a specific profile to allow it to be easily and safely worked by the loading shovels, and to ensure that the material ravels freely as it is dug.
The site also operates an Atlas Copco remote-controlled D9 rig fitted with a top hammer. BAM Ritchies own and operate the largest fleet of this kind of rig in the UK. The D9 rig is used for both production and development blasting and has the ability to drill in some of the most inaccessible areas of the quarry with little trouble. The operator is able to safely operate the rig using its remote control unit. In addition, the rig can be safely anchored using its built-in winch.
The site has its own bulk emulsion manufacturing plant, which is supplied and operated by Orica. An all-terrain bulk truck is used to deliver the product to the blast site. The current requirement is for approximately 2,000 tonnes of bulk emulsion per year. Excel initiation is used with a variety of timings to achieve the throw and fragmentation required to achieve optimum production. Other means of improving the blasting results are constantly being investigated and the use of Orica’s i-kon electronic initiation system has been trialled to allow greater control of the blast timings and to improve the resulting blast pile.
The key to ongoing success at Glensanda is ensuring that sufficient development work is carried out in line with normal production, much of which is only accessible by the D9 drill rig. These areas must be blasted and opened up to allow production drilling and the future development of the quarry to take place. In the coming years it will be necessary to blast the rock that surrounds the glory hole and to drop the level without affecting site production and while ensuring that no damage occurs to the site’s only shaft linking the extraction area with the processing area. Investigation of ground vibration during blasting will be used to minimize disruption to the glory hole and to ensure that no oversize material, which could potentially cause a blockage, is allowed to fall into the shaft.
All of the drilling and blasting work now carried out at Glensanda is done by seven BAM Ritchies personnel.
‘With a continually changing and an increasingly demanding production environment, it is essential that the drill and blast operations adapt to the needs of the quarry,’ commented Clive Allison, BAM Ritchies’ quarry engineer. ‘Staying ahead with advances in technology and improvements within the industry is key to the operation’s success. After a successful first year that has seen key changes and improvements, BAM Ritchies will endeavour to meet the challenges of the coming years.’