Interview with Viv Russell
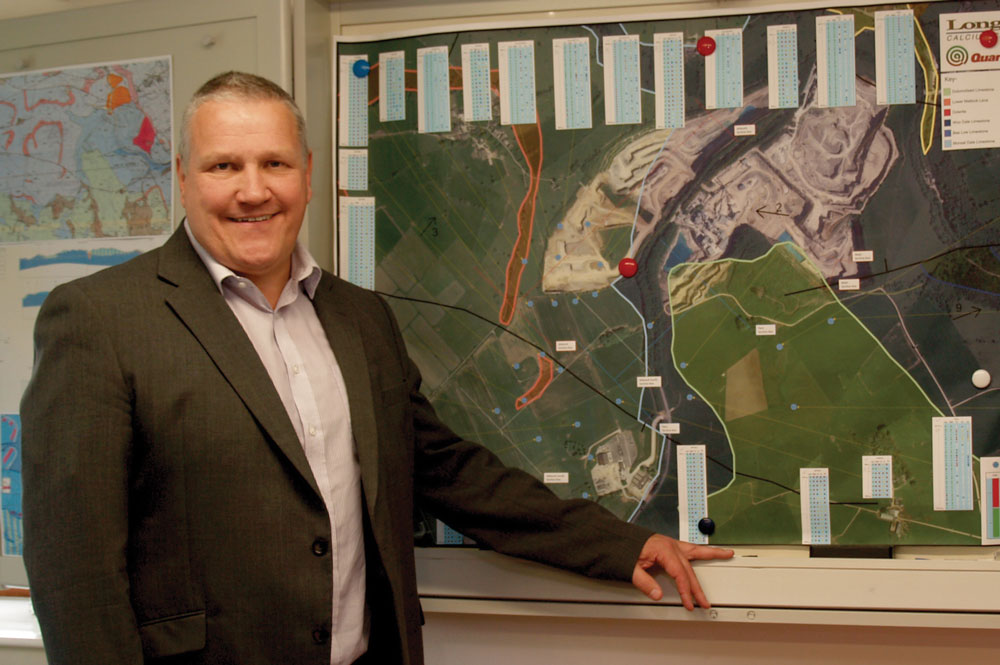
First published in the December 2018 issue of Quarry Management as A Positive Outlook
In April this year, Viv Russell, the new Deputy Chair of the Institute of Quarrying, became group managing director of one of the country’s largest independent operators: Longcliffe Group. After eight months in the job he spoke to QM about the reasons he chose to leave the corporate culture and about the opportunities as an independent.
For Viv Russell, the opportunity to join Longcliffe Group came through his good friend Andy Littler, who, as Longcliffe’s then managing director, was planning his retirement. However, Mr Russell says the decision to leave Tarmac CRH was very difficult. ‘I had 27 years of continuous service through a variety of corporate takeovers and the last two years of CRH ownership were by far the most enjoyable and rewarding. A personal regret is that I did not discover CRH 25 years earlier, as I have no doubt that I would have travelled the world with them. I would strongly recommend them to any young ambitious aspiring manager in the industry.’
So why did he choose to join Longcliffe? The answer, he says, is simple – ‘Not only is Longcliffe a fantastic, forward-thinking, community-focused company, but the job brings me back closer to the reason why I have enjoyed my 41 years in the industry: you can make a difference.’
According to Mr Russell, this difference is very well articulated in the four cornerstones of the Institute of Quarrying’s recently launched new strategy:
- Drive innovation and operational best practice;
- Support the industry in driving healthy, sustainable workplaces;
- Promote the positive impact of the industry and profession;
- Promote the IQ as a global leader in standards for the mineral extraction profession.
He says there is a great opportunity at Longcliffe for innovation and operational best practice. The company is always looking for new products and services and is actively involved in collaborations with other independent businesses. A core value of Longcliffe is their belief that this collaboration allows independents to compete on the same stage as the multinationals. A good example of this is the working relationship between Longcliffe and Alkali Solutions, whereby Longcliffe toll manufacture high solids milk of lime at a purpose-built hydrating plant.
The latest co-operative product is Longfloor, a liquid concrete self-levelling screed that is easy to pour and easy to use. Longcliffe supply the specialist powders content that independent concrete producers use to make the screed and have invested in a £500,000 blending plant to make the product. They are also now expanding into self-compacting concrete, again in collaboration with other independent companies. To support this Longcliffe employ their own experts in fields they consider to be part of their value stream and have recently recruited Darren Williams, an industrial expert in liquid screeds and self-levelling concrete. His background is with Marshalls and Lafarge.
To make sure the minerals extracted are what is required, dust from every blasthole drilled is analysed to find out exactly what it contains. This is being carried out in another collaboration – this time with geological consultants Geodesign – and involves employing geologists as 12-month interns over the next three years. After 12 months they have the option to continue as a trainee geologist with Geodesign or to join Longcliffe as a quarry management trainee. ‘This is a great way of sharing resources and introducing geology graduates to our industry,’ says Mr Russell. ‘Our first intern, Luke Hodson, who graduated from the University of Derby, has made a great start and is already contributing to the understanding of our geology and geochemistry.
‘I am also bringing some of my own ideas into the development of the workforce, introducing performance techniques to improve the business. One of the things we are implementing at the moment is ‘Operational Fundamentals’. It involves daily team meetings, lean manufacturing techniques such as 5S, root cause analysis (RCA), standard operating procedures (SOP) and process confirmations (the check part of Plan, Do, and Check).
‘We have put all 175 employees and key contractors through the Fundamentals and Mind Set training to allow everybody to use the language and techniques of ‘Win, Learn, Change’ to reframe issues as opportunities – if there’s an incident/breakdown there were probably two or three near misses beforehand. If you can get everybody to report and review these near misses you have an opportunity to learn and improve. This behaviour training is covered in the IQ Skills Wheel engagement fact sheets.’
Safety within the business is rapidly becoming an essential focus. Major capital projects such as a new entrance road have pedestrian/vehicle safety as a key part of their design. The company is also at the forefront in employee involvement by introducing a ‘Lifesaving Award’ for employees and contractors, which is one day’s additional holiday to spend with family and friends if they report/prevent a high potential near miss. There are also £20 Longcliffe Value Awards for employees and contractors, nominated by their peers and customers, who have demonstrated exceptional behaviours and promoted Longcliffe values. These awards and other news are incorporated in the employee-produced monthly newsletter called
Longcliffe Chatter. The newsletter also provides an opportunity to celebrate any successful projects and individual performances, both at work or at home. This can be raising money for charity or local sporting success.
The Longcliffe business was established in 1927 and represents a great example of a sustainable workplace. The sixth generation of the family, John Shields, is on the board of Longcliffe Group and the family are still very much involved. Whenever there is a long-service award to be presented, the chairman Robert Shields DL or his mother Rosemary will try to attend.
‘Longcliffe’s promotion of the industry and its professionalism, I believe, is second to none,’ says Mr Russell. ‘When Longcliffe wanted to erect two wind turbines on the edge of their Ryder Point Quarry there was, uniquely, not a single objection from any member of the public or statutory consultee. As John Shields said in The Parliamentary Review highlighting best practice this year, this is only possible ‘due to widespread local consultation and much local goodwill’.’
The company has a long-term approach to the business with every intention of passing it on down the generations, so it has a vested interest in sustainability. John Shields’ report in The Parliamentary Review says that since 2010, the company’s energy usage per tonne has fallen by 28% and with the addition of the two 2.5MW wind turbines, which are run as a separate business feeding the National Grid, on-site carbon intensity has halved. Last year the turbines generated 10.3 million kW/h of electricity.
Ongoing energy efficiency is enshrined in the company’s adoption of the energy management system ISO 50001, but this is just one of the many standards Longcliffe have achieved and maintain. Others include ISOs 9001 – Quality management systems; 14001 – Environmental management systems; 14021 – Self-certified environmental claims; OHSAS 18001 – Occupational health & safety management systems; BES 6001 – Framework for the responsible sourcing of construction products; FEMAS – Compliance with Feed Materials Assurance Scheme; TASCC – Trade Assurance Scheme for Combinable Crops (Transport Code of Practice); and BAA – Compliance with the British Aggregates Association Safe Quarry Scheme.
During the June heatwave more than 600 people visited the company’s Hoe Grange Quarry site and the BBC TV programme Countryfile went there to film. The site is a nature reserve run by Derbyshire Wildlife Trust, with Longcliffe paying for two retired people to be wardens. Peak Quarry is another restored site where Derbyshire Wildlife Trust have just taken on the management and recent surveys indicate it is proving a haven for rare species.
Longcliffe also own Vital Earth, a composting business in Ashbourne that takes brown bin waste from a number of councils and produces 55,000 tonnes of compost a year. The product is bagged and sold nationwide.
Of course, being good to the environment and being a good neighbour has its own rewards, but it is also good business sense for anyone working in an industry as sensitive and as regulated as quarrying that depends on being able to achieve and retain a licence to operate. ‘We have to earn that – and that’s Longcliffe’s real strength,’ says Mr Russell. ‘It has to be recognized too that the company is a major employer and contributor to the local economy in Derbyshire. It is the second largest private employer in Derbyshire Dales with 175 employees, six apprentices and
30–40 semi-permanent sub-contractors. In terms of annual financial contribution, it provides jobs with average P60 earnings of £36,000, £680,000 in NI contributions, £300,000 in business rates, £400,000 in corporation tax, £950,000 in vehicle excise duty and fuel duty, and £7 million spend in the local community.’
Still focusing on making a difference, Mr Russell believes the fourth cornerstone of the IQ strategy of promotion of the Institute as a global leader in standards for the mineral extraction profession is very important. ‘I believe I can contribute and support this in the next six years in my role as Deputy Chair, Chairman and President of the Institute of Quarrying,’ he says. ‘During my last two years with CRH, I was heavily involved in sharing good practice across the European and international lime industry and rapidly realized that there is a fantastic opportunity for the excellent IQ standards, membership benefits and education to be shared globally. I now have a great chance to promote the industry I love and hopefully give others the opportunities that I have enjoyed being a member of the Institute of Quarrying and a very proud quarrying professional.’
- Subscribe to Quarry Management, the monthly journal for the mineral products industry, to read articles before they appear on Agg-Net.com