Avoiding Civil Works Overspend
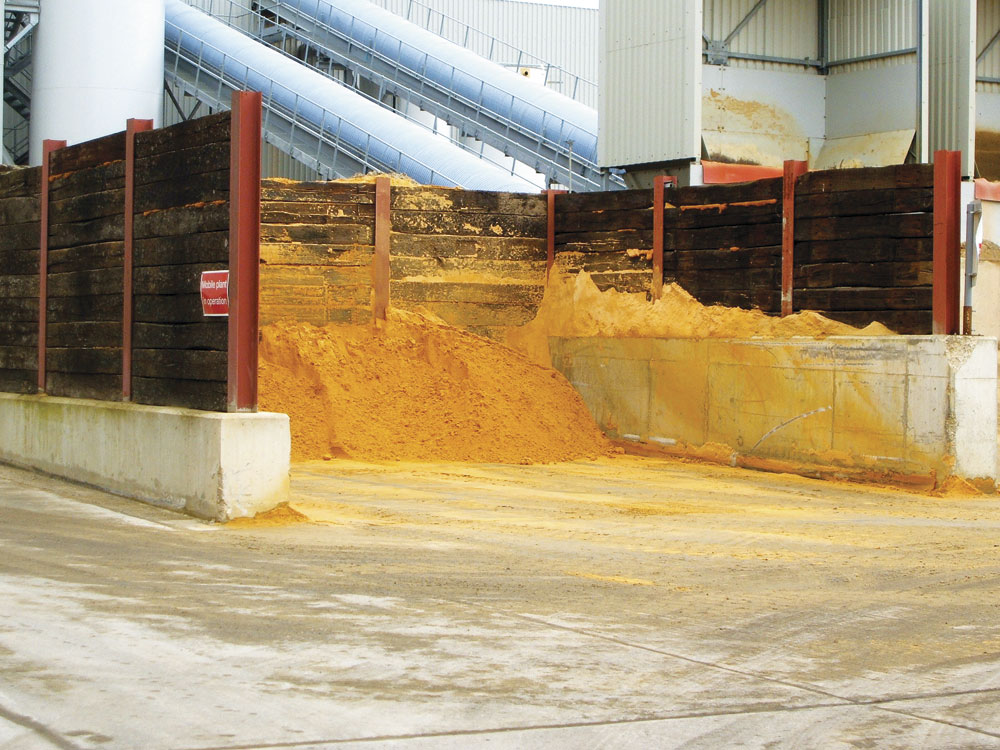
Budgeting headaches can be avoided if all the issues are considered at the right time, ie at the beginning, as Derrick Clarke of civil and structural engineering firm Clarke & Associates explains
It is only natural for purchasers of large process plants to focus on the key areas of output performance, capital and revenue costs, and the plant’s flexibility to accommodate varying materials and markets. However, when it comes to quarry process plants or asphalt and concrete/mortar plants, the capital element of the civil and structural works needed to enable the installation of the new plant and support its operability can represent anywhere between 15% and 50% of the total capital budget. To some, these high ‘non-core’ costs can seem horrendous and unjustifiable; so where do they come from? This article attempts to provide the answers using a typical ready-mixed concrete plant development as an example.
What is in a concrete plant?
Surely, all a plant needs is a few strips of concrete to support it and some paving to get vehicles to and from it, a few stockbays and some hardstanding around them, a batch cabin, a wedge pit or two, a drying bay, and possibly a reclaimer (plus further paving to all of those). All of these are needed, but so too are underground cables and freshwater pipes, tank foundations, additives bays, offices complete with a foul drainage connection (or biodisk) and access to comply with the Disability Discrimination Act (DDA), treatment of grey water discharge and yet more paving to accommodate vehicle circulation and wagon and drivers’ parking. Worst of all the potential costs is the disposal of muck off site, especially any material that is deemed to be contaminated.
Foundations
The plant will need robust foundations, and the engineer’s skill is in determining the optimum foundation solution in terms of both construction cost and muck-away cost.
If the site is suitable, the foundations need only be simple concrete footings, but they do need to be robust enough to support loads often equivalent to a four- or five-storey building. Furthermore, with the increasing sophistication of skip-transfer systems and weigh systems, they also need similarly tight limits on differential settlement. Differential settlements are becoming increasingly more complex to estimate as aggregate bin and cement silo capacities increase.
The daily variation in the actual load transmitted into the ground can also be significantly different to a normal building. Building codes require that the floors of buildings accommodate imposed (‘live’) loads which are rarely achieved in practice and certainly do not vary hugely on a regular basis. For example, a typical four- or five-storey building might only have a 5-tonne variation on a foundation load of 80 tonnes. Compare this with three 130-tonne cement silos, each weighing 10 tonnes, supported on a shared eight-column frame; here the inner columns are supporting 5 tonnes when the silos are empty and 70 tonnes when they are full – a change in load that can happen daily. If these silos are supported on an elevated frame, there may be only four columns beneath them with the foundation load varying from 7.5 tonnes up to 105 tonnes.
This means that it is necessary to look carefully at the total settlement figures for each part of the plant to ensure satisfactory relative displacements between key plant items of potentially differing load characteristics.
A simple set of pads or raft will only work if there are uniform natural ground conditions of adequate stiffness at a depth close enough to the surface beneath the entire length of the plant. If this is not the case, a variety of affordable techniques are available to extend the depth of the footings. However, abnormal foundations may be unavoidable on some sites. When creating foundations, great care needs to be taken, as all foundation work involves excavation and often disposal of muck off site. Excavation costs can bad enough, especially if the sides of the excavation need supporting, but muck-away costs can terminate a job if the excavations are too deep and/or the muck is contaminated.
If the site comprises ‘made ground’, then unless this has been ‘placed’ under engineering supervision, it is unlikely that it will be good enough without further improvement. This will involve specialist contractors, incurring yet more cost. To some, the worst-case scenario is a site where the ‘good’ ground is at too great a depth and piling is unavoidable.
More importantly, made ground is often contaminated and the chosen foundation solution will have to balance the construction cost against the disposal costs; ie a more expensive foundation could be offset by the saving in muck-away cost.
How does all this impact on the budget? Straightforward foundations for the key plant items may be around £45,000 on a good site, but this figure could easily double or even treble on a brownfield site with poor ground conditions.
Ramp or pit?
Aggregates are often delivered into a ground hopper (discharging on to a conveyor) or directly into the aggregate bins via a ramp.
If the ground hopper is in a pit, a practical mechanical and electrical supplier will use the walls of the pit to support the hopper. However, many hoppers stand on frames founded on the floor of the pit where the legs may corrode and eventually need replacement. Pits are relatively easy to cost, providing they do not extend below the water table or encounter contaminated ground, loose silts or other problems.
Ramps do at least offer the certainty of not encountering too many underground complications. Some plant suppliers even supply integral ramp-support walls. Often, purchasers will attempt to use these built-in walls of the aggregate bins to support the ends and sides of the ramp. This is acceptable for a temporary site plant, but modern safety standards are increasingly calling for near flat sections, 5 or 6m deep, at the top of a ramp and a maximum gradient of 1 in 6. This type of ramp can only be provided by using specially built walls, preferably in in-situ reinforced concrete, although timber posts and sleepers can be a reasonably effective and more-affordable alternative. Given that the wing walls have to extend above the running surface and the end walls should provide an effective wheelstop, precast walling units are not always the best solution since they tend to fracture excessively when hit.
Obviously, both ramps and pits can vary in terms of their size and cost. However, excluding surfacing, both methods are usually of similar overall cost, given that it is normal to pave under the delivery conveyor. However, pits become more risky where the ground conditions are of a more dubious nature.
Paving
Vehicle circulation is not cheap. Even a running surface comprising sub-base placed over good subsoil will involve the removal (and often export) of topsoil and the grading of the site to suit the vehicles’ capabilities. Asphaltic surfacing is often cited as the next most affordable type of paving, although some may question the robustness of modern mixes when exposed to loading shovels and tight-turning horizontal shear loads. That leaves concrete, which although becoming less costly as specialist fibre-reinforced mixes are developed, is still the most expensive option.
Using market rates for materials, costs are typically £25 to £70 per square metre, assuming clean muck for disposal off site and a reasonably stable formation. Obviously, poorer ground conditions will impact significantly on the paving cost.
But paving is not just used for vehicle circulation; it is a practical low-maintenance way of directing both storm water and grey water drainage to their appropriate wedge pits and for allowing access for loading shovels into those pits. There will also be a need to provide vehicle parking for the concrete wagons and the drivers’ own cars as well as for visitors, including, increasingly, a space for the disabled.
All this adds up. A paved area of 2,500–5,000m2 is not unusual for a modern concrete plant, at a cost of £150,000 or more.
Stockbays
All concrete plants need stockbays – a minimum of two, although four or even six are now considered desirable. The traditional post and sleeper solution (using second-hand railway sleepers) still has much to offer in terms of cost, robustness and ease of repair. Although if a shed is required over the dust and sand bays, a good, high, solid reinforced concrete wall provides the best support for the overhead steel-clad canopy. But what height should the shed be? At least 7m is needed to keep the roof steelwork above the reach of most loading shovels, although some would argue it should be higher. And what of the tipping height of delivery vehicle bodies? On several asphalt plants, 13m high sheds have been built over the dust and sand bays, but is 13m really affordable on a concrete plant?
There are some who will say the canopy can be built on the steel posts of the wall below. Perhaps so, but operators should remember that the height will be limited unless the steel posts are sized accordingly (and even then to little more than 7m), and the whole canopy structure will be vulnerable to the effects of ground-level impact damage from both the loading shovel and delivery wagons, which could have catastrophic effects on the canopy above.
What about stockbays with perimeter kerb around the bottom of the walls to provide a clean surface for the shovel to work against? These are fine, provided the £450–500 per metre cost can be found. For four 11m x 5.6m stockbays that amounts to some £33,000 plus another £17,000 or so for a decent floor/running surface. Add a canopy over two of the bays (fixed directly to the main wall posts), and the cost for the stockbays could easily reach £80,000, depending upon the chosen height.
Pits, reclaimers, tank and additive slabs, offices, underground services…
Space precludes further discussion of the multitude of costs that have to be included in the civils section of a project budget, but each of the above items (plus possibly many more depending on the type of plant) can impact on the budget. The issues of ground condition and contaminated materials impact on all of them to varying degrees, and the requirements of the Disability Discrimination Act could have huge impact on a two-storey site office where, potentially, a lift could be demanded by the local authority.
Conclusion
The cost of civil works can vary enormously. The old adage ‘if you can avoid going into the ground, then do’, is very true. A replacement concrete plant being installed on an existing site can be achieved for £140,000. An identical plant on a new site with only average problems can (and often does) cost three times that, and Clarke & Associates Ltd have been involved several large plants costing more than £1 million on civil works alone.
With potential costs of this magnitude, maximum value for money is essential. Aside from reviewing the site conditions to advise on suitable budgets for foundations, civil and structural consultants who are well experienced in the quarry products industry can look into a wide range of issues, including:
- laying out the mechanical and electrical contractor’s scheme effectively on the plan of the available site
- examining vehicle circulation to achieve workable vehicle movements, minimize surfacing and ensure efficient access into the various areas of the plant
- advising on the use of surface drainage and the optimization of groundworks to minimize the export of materials to tip
- using surface drainage to establish individual grey and storm water areas
- minimizing grey water discharge and its associated cost
- minimizing the use of mains water by harvesting storm water through the establishment of adequate surface drainage systems and storage pits and collection tanks
- ensuring disabled access to cabins, offices etc complies with legislation
- advising on the avoidance of ‘in-use’ damage to fixed plant by mobile plant, maintenance, cleaning etc, to avoid future repairs
- assisting with compilation of the project budget.
It is important, therefore, to seek the advice of a competent professional civil and structural engineering consultancy at an early stage in order to ensure that the same rigorous, value-added analysis that is generally applied to the mechanical and electrical installation, is also applied to the civil and structural enabling costs.
For further information, contact Derrick Clarke at Clarke & Associates Ltd on tel: (01925) 758811; or email: engineers@clarkeandassociates.co.uk