On Top Of The Ups And Downs
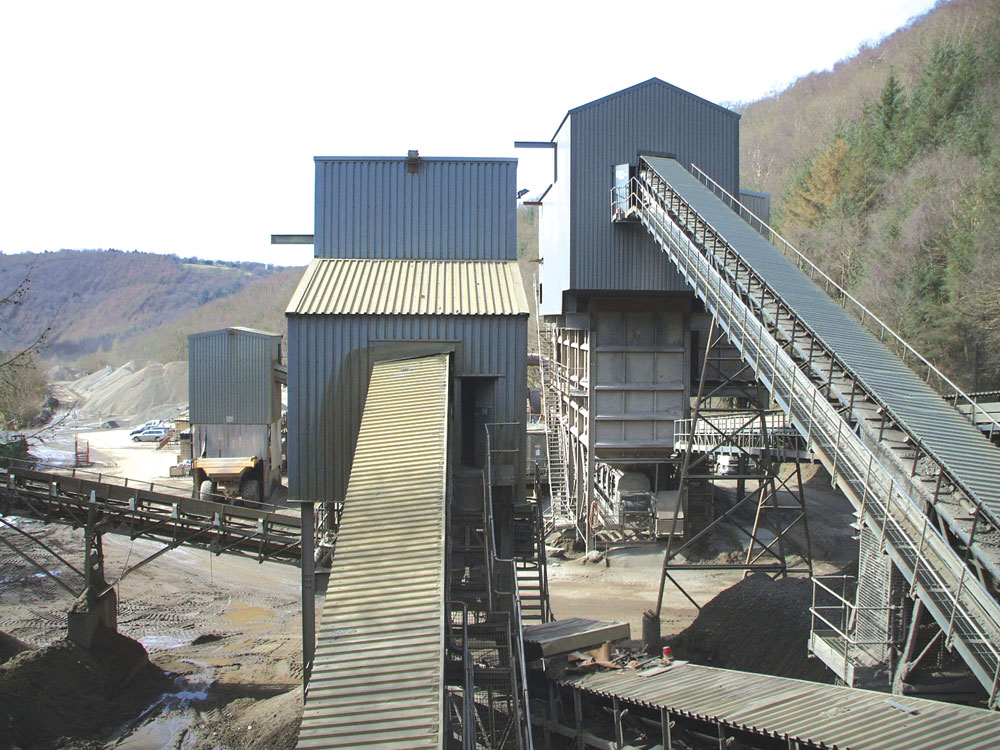
Innovative radio transmission level system controls the screen house bins at Hafod Quarry
An innovative six-point HyLink radio transmission level system, supplied by level measuring specialists Hycontrol, is providing crucial operational data on the contents of the screen house bins at Hafod Quarry, in South Wales. Level data from the bins are transmitted simultaneously to a receiver in the crusher control room and to robust portable receiver units in the cabs of two dumptrucks used to transport screened products around the site.
Owned and operated by Lafarge, Hafod Quarry produces over 250,000 tonnes of gritstone a year. Part of this production is used by the on-site bitumen coating plant, while the remainder is processed for sale as coated stone or aggregates. Maintaining optimum levels of material in the screen house bins is vital to ensure efficient and uninterrupted production across the site. If the bins become full or run short of product, various production activities are adversely affected until the situation is remedied.
However, in the harsh operating environment of a typical busy quarry, such as Hafod, providing level measurement on the bins only solves part of the problem; real-time data availability and accessibility for relevant personnel also needs to be a crucial part of any control system.
Hycontrol’s HyLink system, in conjunction with the company’s industry-proven level-measuring technologies, provides secure and robust transmission of data to critical parts of the Hafod operation, removing the need for extensive and vulnerable wiring. The 8m high bins contain screened product varying in size from dust up to oversize stone 80mm in diameter. The four bins containing sizes from 10mm diameter upwards are fitted with Hycontrol’s versatile Microflex LR two-wire, loop-powered ultrasonic units, which have a proven track record operating on storage bins and silos up to 60m in height.
The Microflex unit utilizes new lower-frequency ultrasonic technology, allowing it to operate successfully in difficult conditions. The unit’s proprietary advanced echo-extraction system automatically ignores false echoes from falling stone and averages out any uneven level patterns as the bin fills and empties. The unit can also be fitted with an optional GSM modem, allowing access for remote commissioning and service.
Meanwhile, the two bins containing 6mm stone and dust, respectively, are fitted with Hycontrol’s VF03 TDR guided-wave radar units. These units are unaffected by the high dust levels predominant in these bins and provide long-term accuracy over the full measuring range. Changes in pressure, temperature and density also have no affect on their performance. These instruments work on the principle of time domain reflectometry, commonly known as TDR, which was originally developed for checking and locating damage along sub-sea telecommunication cables. The units have replaceable 8mm diameter stainless steel wires that extend down through the product to the full depth of the bins. These act as the wave guides for low-power electromagnetic pulses. The units are fully calibrated prior to installation.
All the instruments at Hafod are powered by the six-point radio transmitter unit installed in the screen house. This re-transmits the level readings to the two separate portable receivers fitted in the dumptrucks and to the receiver located in the crusher control room. An additional receiver installed in the bitumen control room provides voltage level outputs for the site’s upgraded PLC system, which is currently being installed. Using standard external aerials, the radio system has a minimum working range of 200m, increasing to 500m with good line of sight, however this can be further upgraded using higher-power aerials.
Percentage level information is displayed simultaneously on the individual HYC3420 LED displays in the custom-built panel in the crusher control room and on the dumptruck cab displays. This dynamic real-time data availability across the site means that rapid decisions can be made by operators and drivers to optimize product availability to keep the plant running efficiently. If required, the system can be set up to display bin contents in tonnes, and optional output relays can be used to provide Hi-Lo alarms. A 12-point measuring system is also available for larger installations.
According to Hycontrol’s sales director, Nigel Allen, it is the integration of robust radio transmission technology with different level-measuring technologies that provides the ideal custom solution for this classic quarry operations problem.
‘We have developed a broad and diverse range of level-measuring technologies that allow us to select exactly the right product or products for any particular application,’ he said. ‘In some installations we may incorporate five or six different technologies depending on specific circumstances.’
‘In parallel, we have pioneered the development of proven communication technologies that can be integrated to provide the optimum system for such applications. Our in-house panel design and build capability means we can supply complete operational systems that can be either stand-alone or integrated with customers’ control systems and software.’
According to Mr Allen, the portable vehicle level receivers bring a new dimension to level measuring, ensuring real-time data can be used to best advantage at busy sites. ‘The units have an integral aerial and can operate off either their built-in rechargeable batteries or the vehicle’s standard auxiliary 12V power supply in the cab,’ he explained. ‘In the Hafod installation, the units can display all six bin levels at once in two columns, with the option to view one bin at a time or to scan to show all bins in rotation. If the level systems are configured to read in tonnes, the cab display can be used to monitor vehicle loading.’
Commenting on the installation of the Hycontrol wireless bin level system, Hafod’s quarry manager, Iain Ormrod, said the system had made the site a more efficient production unit. ‘Prior to this, the stocking dumper driver had to guesstimate when each bin was getting full and this could lead to the bin overfilling, contaminating the products in adjacent bins in the process,’ he explained.
He added that guesstimation had also led to bins running empty, forcing the bitumen coating plant to use material from stock. ‘Unfortunately, due to the renowned Welsh weather, this was often soaking wet, thereby increasing our drying costs on top of the cost of moving material twice,’ he said.
‘As an added bonus, knowing the level status of each bin means that the stocking dumper can be used for other tasks when the coating plant is busy, such as moving quarry waste, safe in the knowledge that the in-cab display will indicate when a screen bin is getting full.’
For further information, contact Hycontrol Ltd, Larchwood House, Orchard Street, Redditch B98 7DP; tel: (01527) 406800; fax: (01527) 406810; email: sales@hycontrol.com