New Pump Drive For Linhay Hill Quarry
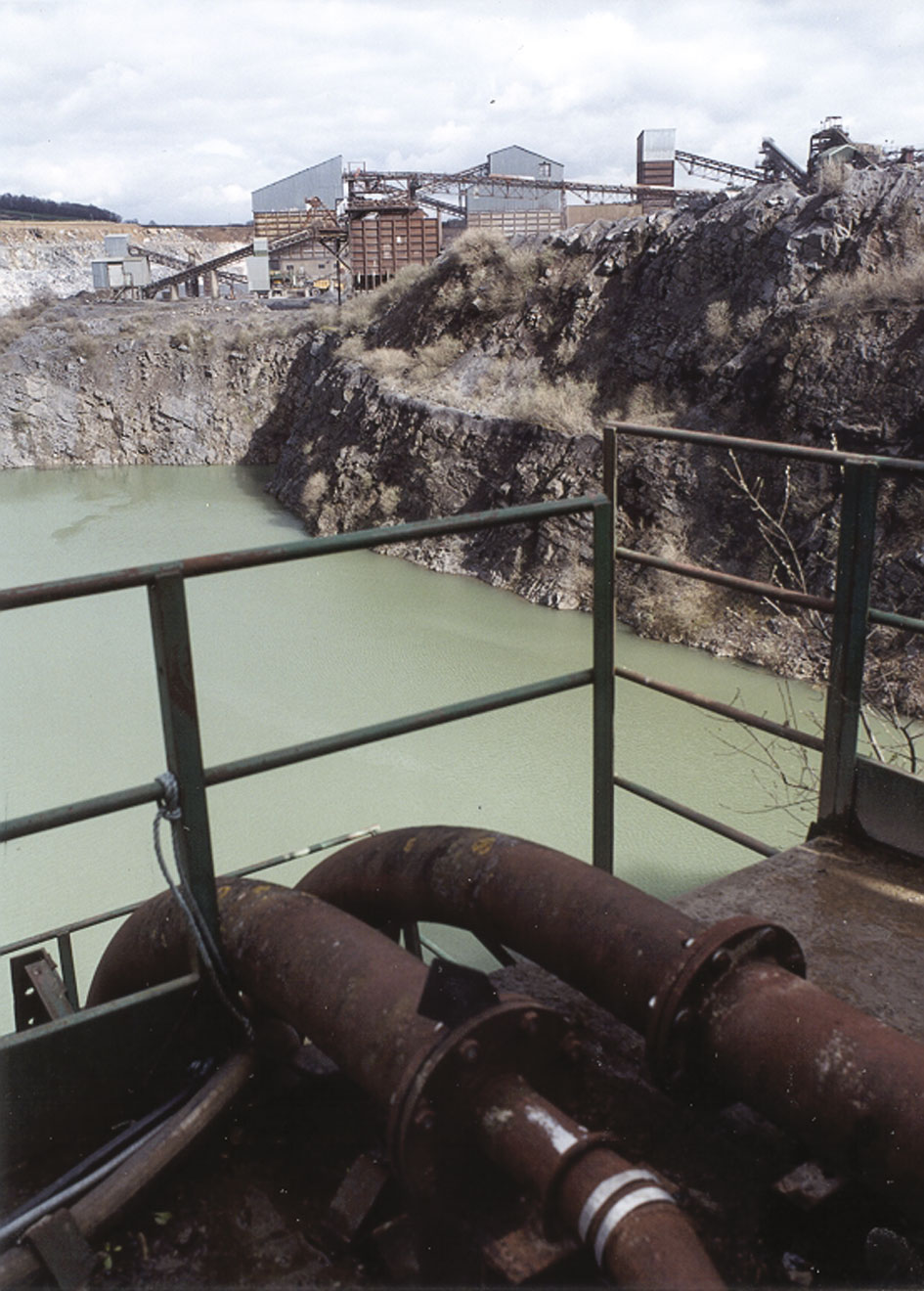
Variable-speed drive provides flexibility and halves energy costs
Projects with short payback times are relatively unusual in the quarrying industry, so when Rockwell Automation calculated that the cost of installing an Allen-Bradley drive to control a 150kW pump would be covered by the resulting energy savings in just one year, engineers at Glendinning’s Linhay Hill Quarry, near Ashburton, Devon, were impressed. Despite some initial caution about such a short payback time, the projected energy savings have since been proven in operation.
Linhay Hill Quarry produces over 600,000 tonnes of limestone annually, with products ranging from aggregates for coated materials and ready-mixed concrete to building blocks, decorative and industrial paving, as well as hardcore, agricultural lime and walling stone.
Large amounts of water are used throughout the quarry to wash crushed stone and to clean plant and equipment. Glendinning make use of the water that collects naturally in an on-site lagoon and move it to where it is needed using a high-output 150kW centrifugal pump rated at 5,000 litres/min.
An Allen-Bradley 1336 PLUS II drive was installed on this pump to improve flow control and to reduce energy costs. Before it was installed the typical average energy consumption for the pump was 124kW; this has now been more than halved to 59kW without affecting its usage.
The new drive replaced a traditional star-delta starter that, although operating correctly, did not provide any control over the volume of water delivered. At times of low demand the flow could be reduced only by using a mechanical throttle valve or by releasing the water into a stream off site or back into the lagoon.
Running such a large pump at full speed is expensive, costing over £8.00 an hour, but controlling its speed with an AC inverter drive allows the pump’s output to be matched to demand, thereby saving energy and reducing wear and tear on the pump itself.
Dennis Smith, group electrical manager with Glendinning, said, ‘We knew there were better ways of controlling this pump so we visited the Drives and Controls Show to discuss alternative ideas with some of the exhibitors. We looked at the Rockwell Automation stand and were impressed with the Allen-Bradley products. As a result we arranged for a site visit to discuss the potential energy savings and estimate the installation costs.’
Based on these potential savings, the order for the control panel containing the Allen-Bradley drive was placed with Switchgear Services in Honiton, Devon, and a new control room was built to house it. This was positioned on the rim of the quarry together with the associated pipework, about 30m above the water level.
The Allen-Bradley 1336 PLUS II series comprises a range of sensor-less vector control drives rated from 7.5kW to 400kW. The range provides 250% acceleration torque and a wide (120:1) speed range, with high levels of dynamic response and full torque down to 15 rev/min.
Robust and reliable and designed to tackle the most challenging applications, the 1336 PLUS II drive is well suited to use in the quarry environment. The drive was supplied as an IP20 open unit and built into the control panel by Switchgear Services, who supplied the door-interlocked isolator and panel-mounted controls. These include operator push-buttons and an Allen-Bradley Human Interface Module (HIM) rated to IP66.
The HIM is a push-button unit with a built-in LCD that provides text facilities for local operator set-up and a read-out of system status. Glendinning use the digital speed-control option, but the option of potentiometer control as well as start/stop, direction and jog is also available. The panel-mounted HIM allows drive parameters including speed, frequency, voltage and power to be displayed. It also alerts the operator to any alarm conditions with warnings being given before a trip occurs.
The drive has a high operating efficiency (97.5%) and features a built-in auto-economizer. This is a particularly useful feature for pump applications, whereby the voltage is automatically adjusted to match the torque required. Motor flux is optimized, providing the highest efficiencies and lowest energy consumption. In addition, although not being used at present, the drive has the facility for a built-in PI, which could be used with a pressure sensor on the output pipe. With rising or falling pressure, the drive would automatically compensate for any reduction or increase in demand.
The centrifugal pump itself is suspended from a pontoon in the centre of a lagoon in a disused working. It is positioned just below the surface of the water and a flexible pipe connects the output from the pump to a 200mm diameter steel pipe. This rises from the edge of the lagoon and up the side of the quarry to the control room — a lift of about 30m.
The control room houses the drive control panel and control valves for the pipework. From this point the water is distributed to the vehicle-washing, storage and concrete products production areas as well as the scrubbing plant where the crushed stone is washed. This requires the water to be lifted a further 50m.
The water level in the lagoon varies with the seasons, weather and demand for water. Moderate changes are accommodated by the flexible link, while larger changes require lengths of fixed piping to be added or removed. A specially protected cable, rated for quarry duties, supplies power from the drive to the pump.
Access to the pontoon for maintenance or inspection of the pump is by means of a small boat, with a cable between the shore and the pontoon allowing the engineer to pull the boat across the water. Clearly, therefore, the reliability of the motor and pump is critical.
The Allen-Bradley drive provides a high level of protection to the motor including over- and under-voltage protection, short circuit, phase-to-phase and phase-to-neutral fault protection. In addition, the drive’s fast processor and large memory provide quick set-up and class-leading diagnostics.
Adam Smith, electrical engineer with Glendinning, said, ‘Rockwell Automation have been very helpful. Their knowledgeable application engineers were able to suggest how new technologies could be applied to save us money and we have now standardized on Allen-Bradley products throughout our plant.
‘This includes a further 1336 Plus II drive installed on a 260kW rock crusher and DeviceNet and SLC 5/05 programmable controllers on the quarry’s slab and block-moulding line.’
Mr Smith added: ‘We have a number of remote sites and our ultimate goal is to be able to access data at these sites using an Ethernet network with remote access via modem links.
Rockwell Automation can supply all the products we need to be able to complete this.’