Microwaves For Level Measurement
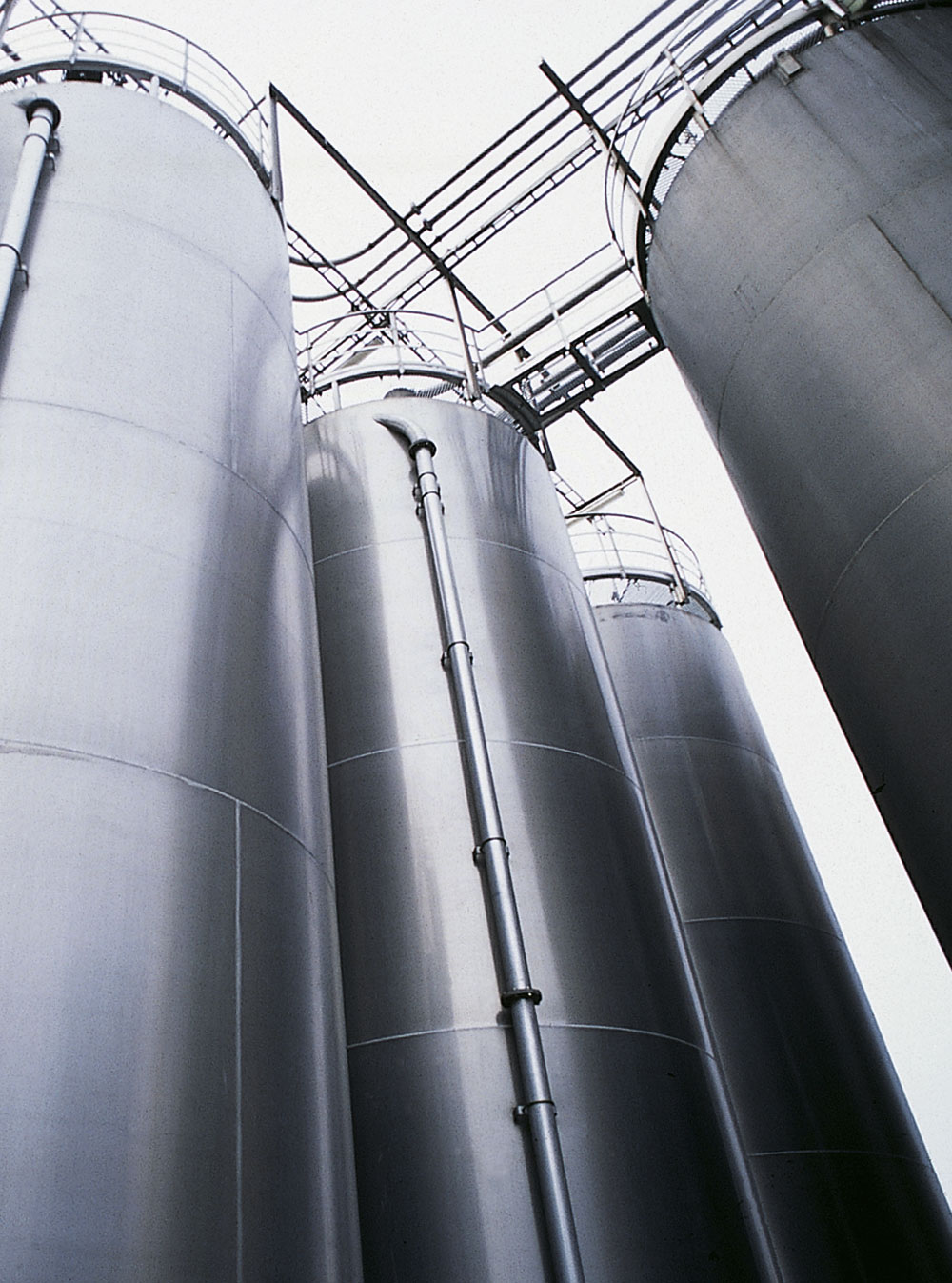
The benefits of using microwave-based technology for level measurement
This article has been adapted and translated by Doug Anderson of Vega Controls UK Ltd from an original by Jurgen Skowaisa, product manager, Microwave and Ultrasonic Department, Vega
Level measurement has always played a key role in the quarrying industry and today it has even more significance with demands for de-manning, automation, and inventory control, as well as for safety and environmental reasons. The challenges for a reliable solution are numerous. For solids these include: dust, product build-up, abrasive products, and uneven surface levels. In general, liquids are easier to deal with, although bitumen requires particular solutions, however it is also important to avoid spillage and contamination by liquids. The working environment for all devices is harsh as vibration, noise, weather and impacts from falling materials are common.
To meet many of these needs, microwave-based technology has now become firmly established in a broad range of quarrying applications. With reducing costs, higher performance and special variants, could it be a question of when, not if, it can replace ultrasonic transmitters for the majority of applications?
The benefits of using microwaves for level measurement are clear. Practically uninfluenced by process variables such as temperature, pressure, vapours, dust or gas composition in the vessel air space, they are suitable for a wide range of applications. The development of new radar and guided-microwave (or TDR) sensors, optimized for applications in bulk materials, brings the goal of a ‘universally applicable’ sensor a step closer. The use of microwaves, however, offers a ‘universal technology’ now.
This article seeks mainly to compare the two microwave-based principles of ‘non-contact’ radar and ‘contact’ TDR and to explore the technology, choices and application types. There is no attempt to make any accuracy claims over weighing systems; they are still the best solution for many applications. Sometimes, however, weighing is not suitable or effective for a number of reasons such as structure, cost, environment, changing product density or build-up.
LEVEL TECHNOLOGIES FOR BULK SOLIDS
The level measurement of bulk solids has a broad scope and ranges from the contents measurement of very fine powders to the monitoring of boulders in crushers. The requirements of each application dictate the measurement principle chosen.
In general, traditional methods range from electromechanical ‘plumb-bob’ devices to capacitive level probes as contact devices, with ultrasonic sensors the usual non-contact principle. A universal transmitter for the varying level-measuring tasks required for bulk solids and liquids is not yet available, as the differing needs are too broad.
EXISTING TECHNIQUES
Capacitive/admittance probes have been used for decades for measuring the level of bulk materials. They rely on the measurement of a change in capacitance proportional to a change in the amount of a product. This assumes a constant electrical conductivity (dielectric constant or DK). The measurement is made between the silo wall and an electrode suspended from the top to the bottom. If the DK value shifts, however, for example due to condensation or the ingress of rainwater into a dry product, a change in the capacitance value can develop with the same product level; this is a particular problem with wet to dry aggregates.
Other considerations include filling and emptying to calibrate, as well as loading and wear on the electrode. Capacitance/ admittance probes are still very effective, however, in some applications, for example ‘hot-stone’ bin levels where awkward installations and shapes can be accommodated by contouring a ‘replaceable’ electrode to suit. The product is also preheated to drive out moisture, which keeps the all important DK value stable.
Ultrasonic sensors are the traditional devices for non-contact level measurement of bulk materials. They reflect a sound wave off a (near horizontal) product surface to measure distance/level. The environment in solids storage, however, nearly always involves dust formation, which can significantly dampen a sound pulse. When pneumatically filling a silo, the combination of dust, airflow and pressure will weaken the signal return from the product, the acoustic waves can be completely dissipated or the sensor can lock on to the wrong echo. A large, high-power transducer can sometimes overcome these issues, but this also makes installation more difficult and result in a bigger ‘dead band’ at the top end of the range in which it cannot measure. Moreover, solids often do not lie flat either, and the lower frequency signals used for higher power can be deflected sideways, giving a misread of the level (distance). High product temperatures (and vapours seen mainly with liquids) can substantially change the speed of the sound too, which can also lead to measuring errors.
When all else fails, many people revert to an electromechanical plumb-bob device for silo levels. But this method is slow, prone to cable breakage, loss of sensing weight and provides no readings during filling. This, combined with high maintenance costs, make this a last-resort solution and one that is generally being replaced.
MICROWAVE TECHNOLOGIES
The main reason for measuring with microwaves is that the changing conditions outlined above, such as variations in conductivity, density, temperature, air movement, pressure, dust, gas, vapours and angle of repose, have practically no effect. They are also easy to set up. New intuitive software means that to calibrate they generally only need the input of ‘full’ and ‘empty’ levels/distances.
Guided microwave (TDR)
The rapidly growing number of contact TDR sensors successfully installed in the past five years in a range of industries shows that they are now being accepted. Like a capacitance device, they utilise a high-strength cable or rod suspended down to the vessel bottom but, unlike capacitance, changing material characteristics have no effect.
TDR has a proven track record for reliability in solids level measurement. Pulses of microwaves (around 300mm in diameter) are guided down a rod/cable over lengths of up to 60m, depending on the bulk density of the product. The cable can also be positioned to avoid container obstructions, side walls/ welded joints or material inflow. Levels can still be measured reliably regardless of surface angle, build-up, dust or air movement. A small connection size, from 3/4in BSP, and very simple start-up (range is determind by the cable length, which may be cut to suit on site) make them easy to apply. There are some applications, however, where a non-contact option is preferred.
Non-contact radar
Non-contact measurement still offers substantial advantages in some applications, particularly where contamination, roof loading, abrasion/impact, corrosion, extreme build-up/ adhesion and high forces during filling or emptying may cause concern. But ultrasonic devices have not always proved the best solution.
The latest radar devices use a focused high-frequency (26GHz) beam. Microwaves simply do not see dust and, as for surface angles (of repose), this ultra-high frequency can reflect back from even the smallest surface particles, rather than deflecting, as may be the case with some ultrasonic sensors.
Radar devices now offer reliable non-contact measurement, which is essential, particularly with dusty, abrasive and heavy media such as stone, aggregates, ores and cement, or over large measuring ranges. Even extreme applications can be realized, such as the level measurement of a cooler bed, a furnace or even glowing coke for steel production. By cooling and cleaning the antenna systems it is possible to use them at temperatures well over 1,000°C, applications far beyond the capability of ultrasonic sensors.
COMPETITION OR IDEAL ADDITION?
The different characteristics of the two microwave measuring procedures outlined above mean the user can choose the most suitable solution for a measuring task. The following are some applications where the advantages of one or the other measurement principle can be seen, showing how the two options complement each other.
Applications of microwave level devices
Crusher levels
The environment inside a crusher box is very harsh and there are few technologies for level and blockage detection. One of the most reliable is a totally non-contact nucleonic system, mounted outside the application. This is highly reliable and needs only scheduled maintenance checks of the gamma source.
Feed control and blockage detection in open (primary) crushers and feed chutes, however, have space above to mount a downward looking non-contact sensor. An ultrasonic device can be used but these can sometimes be affected by the volume of noise as they also use sound waves. A radar device has a narrow beam, which is unaffected by dust or noise. With a safe, low-output level means it can be used even with personnel in the area (but check the manufacturer’s guidelines first).
Cement storage
With cable lengths up to 25–30m for cement, a TDR device is suitable for level measurement in silos and is designed to comfort-ably withstand the emptying forces. In very tall silos or with abrasive coarse-grained ‘meals’ and clinker, however, a contact-free measurement using radar avoids the potential for heavy loads on silo tops and damage to the cable. A swivel mounting allows easy sensor alignment and with air-cooling high temperatures can be handled, even on clinker cooler beds over 1,200°C.
Filler silos
These are often very tall and narrow and TDR is the most commonly used method for level measurement as the signal guidance eliminates possible reflections from the silo wall, filling or internal structures. In some applications a non-contact measurement may be preferred, possibly due to roof loading. Even if the silo has a pneumatic fill system causing dust and air movement, microwave technology follows the level reliably.
Coal in its raw form is made up of various-sized pieces. It is then normally milled into pulverized powder and stored in silos ready for combustion. The potential for strong forces and damage to a cable when handling the raw coal in bunkers means that non-contact measurement is often recommend- ed. Previously, high-performance ultrasonic sensors had varying reliability due to substantial dust combined with condensation on the transducer. To overcome the effects of heavy build-up on the sensor, radar can have an integral high-pressure air purge. A TDR is virtually unaffected, even during the pneumatic filling of pulverized coal silos, ensuring a reliable measurement is made.
Liquids in the aggregates industry
In this area more attention and scrutiny is being paid to the safe handling of fuels, fluxes and bitumen by bodies such as the Health and Safety Executive, the Environment Agency and the Refined Bitumen Association.
For liquids, top-mounted level systems are preferred as they provide easier access and there is less possibility of leaks. Moreover, a bottom-mounted level transmitter can be damaged if the bund is flooded. Free-flowing liquids are easily handled using a number of systems. An old method is the ‘cat and mouse’ — a float and pulley system to indicate an inverted level in a vessel. These are prone to sticking, however, giving false readings and are generally being replaced. Ultrasonic systems are suitable for non-fuming products and products at ambient temperatures, while top-mounted hydrostatic transmitters measure liquid head pressure as long as material compatibility is satisfactory and density changes are not expected.
Some fuels can give off fumes and vapours in the head space, which can affect the accuracy of an ultrasound signal. Radar and TDR devices are unaffected by vapours or temperature and are therefore suitable for these types of liquids. The devices can be employed as a universal solution across a number of tanks — with only one spare needed — or in combination with other sensor types.
Bitumen storage
Of all the liquids in the industry, bitumen is one of the most difficult to handle. Microwaves are unaffected by the temperature, vapours and changing density (different PEN values and polymer additives will affect this) of bitumen and so are suitable for measuring this problematic product. Both non-contact radar and contact TDR radar devices work equally well in this application. The customer can choose their preferred option to suit the needs of the application. The main advantages are shown in table 1.
Coated stone
Some sites store finished bitumen-coated stone/polymer products in heated bins ready for dispatch. This type of product is very adhesive and radar avoids any contact. There is no ‘pulling’ force on a cable to be concerned about, radar copes with the high temperatures and fumes, and the focused beam avoids obstructions and any build-up on vessel walls.
CONCLUSION
The development of sensors has opened up a range of applications within many solids- and liquid-handling industries for microwave level technology; further developments will surely follow. In most cases a non-contact radar measurement principle is preferred as it provides lower maintenance costs, installation is generally easier and there is less concern about materials and mechanical loadings. TDR technologies are popular too, as they are often easier to set up and may have cost advantages. All the technologies mentioned above remain in use, however, whether through preference, niche or economical reasons, and manufacturers still need to offer choice backed up by sound advice.