Effective Instrumentation
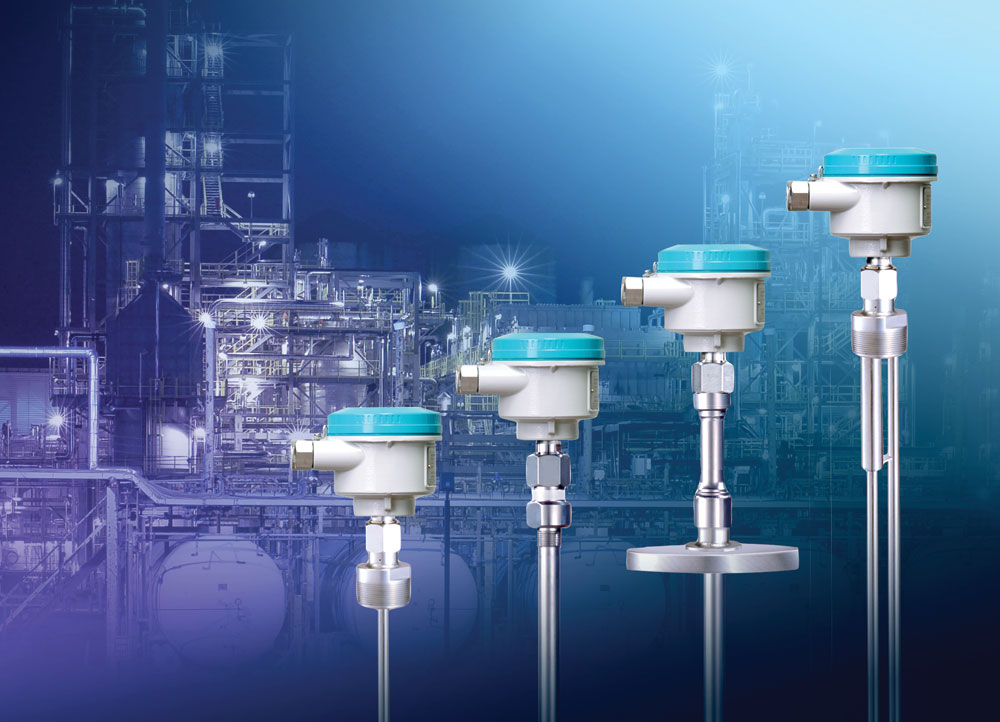
With the increasing threat of energy shortages and the major effects of global warming, instrumentation and control technology can offer some respite, in the form of energy savings and improved production. Stephen Howes, flow and level specialist at Siemens, discusses the relative merits of instrumentation equipment in the solids and bulk handling industries
The term ‘instrumentation’ is essentially the use of tools or instruments for the measurement/control of a given variable. Operating alongside effective controls, the partnership provides a valuable source of information in a variety of working environments.
In simple terms, in order for a site to be able to control a number of variables, it requires accurate and detailed measurements – gained through instrumentation equipment.
Depending on the industry, the variables to be measured could be anything from powders and liquids to solids, all of varying dielectric ranges. With this in mind, there are a number of different sensors available within the marketplace designed to meet the specific needs of each variable, and that take into account the challenges that may be experienced on site, such as moisture and dust generation.
It is possible that effective measurement and control at each stage of the production process, bearing in mind such obstacles, can increase availability, reduce waste, save time and increase output.
In the aggregates sector, for example, instrumentation equipment can be used throughout the production stage, from level and weighing measurements at the primary crusher, through to the screening process and then on to the secondary crusher and stockpiling stages.
Furthermore, one of the most common applications for industrial instrumentation is the measurement and control of the level of materials contained in storage and process vessels, such as bins, hoppers and silos. Using instrumentation equipment here can help reduce spillage and overflow, as well as providing quality control and inventory management.
Choosing the most suitable instrumentation technology for a site is dependent on a number of factors, such as the characteristics of the material to be measured, environmental conditions and the properties of the containers, as well as the specific needs of the customer in terms of cost, maintenance and accuracy.
There are a number of level measurement devices suitable for the solids and bulk handling industries:
Ultrasonic
Ultrasonic technology links a non-contacting transducer to a controller, offering a highly cost-effective solution suitable for harsh, rugged industrial environments, as transducers are impervious to moisture, corrosion and vibration, and are virtually maintenance-free.
Ultrasonic technology has been successfully used in many solid bulk material level applications, including aggregate stockpiles, and provide a cost-effective solution to overcome the challenges of multiple levels required in screen house applications.
Radar
Operational through electromagnetic waves, non-contacting radar is a low-maintenance technology unaffected by external processing conditions, such as extreme high temperatures and dust generation. The technology is appropriate for measuring liquids, slurries and solids, including fly ash, pulverized coal and cement.
With the decreasing price of radar measurement devices, many companies are standardizing on radar technology for all their measurement needs. One of the latest products to be introduced into the Siemens range is the Sitrans LR620, developed for use on virtually any stored solid medium, including aggregates and coal.
The two-wire continuous level radar-based transmitter can detect materials at distances up to 30m (98ft), even in environments with extreme dust load and temperatures of up to 200°C.
Guided wave radar
This technology uses pulses of electromagnetic energy to measure material levels. When a pulse reaches a dielectric discontinuity – created by the media surface – part of the energy is reflected. Therefore, the greater the dielectric difference, the greater the amplitude (strength) of the reflection.
As a contact device, guided-wave radar is not affected by changes in process conditions, high temperatures, pressure and steam, thus ensuring accurate measurement in level, volume and interface applications. The technology can automatically overcome obstructions and apply algorithms to raw echoes, so that accurate and reliable measurements are made.
This makes guided-wave radar devices suitable for the measurement of liquid/slurry applications involving corrosive vapours, foam, saturated steam, high viscosity, quick fill/empty rates and varying dielectrics and product densities (eg filler silo, fly ash etc).
Inverse frequency shift capacitance
This type of device incorporates a unique frequency-based approach to level measurement. The capacitance units monitor the effect of capacitance based on frequency change, given that the relationship between the capacitance and frequency is inverse.
The capacitance device has been widely used as a level point switch, offering reduced maintenance costs compared with conventional electro-mechanical units, particularly in applications with build-up.
Owing to the high accuracy and repeatability of the inverse frequency shift circuitry, capacitance probes are seeing a resurgence in the marketplace as a continual level measurement device. The technology is commonly used as a safety device for applications, such as blocked chutes and bitumen measurement.
Electro-mechanical
Electro-mechanical switches have traditionally been employed for simple level detection – the most common being the vibrating fork. A signal from the electronic circuit excites a crystal in the probe causing the fork to vibrate.
If the fork is covered by material, a change in vibration level is detected by the electronic circuitry, which subsequently changes the relay state after a one second delay. When the fork is free from material pressure, full vibration resumes and the relay reverts to its normal condition.
Electro-mechanical switches range from simple low-cost devices that detect liquid level to the more robust instruments used to measure dry bulk solids in bins, silos, hoppers and settled solids within liquids.
Overview
The concept of continuous level measurement for bulk solids is based predominantly on non-contact technologies that provide accurate and repeatable measurement of solids, liquids, slurries and foam in some of the harshest environments.
Siemens instruments are designed to work in such conditions, ensuring reliable and continuous level measurement despite the presence of extreme dust, moisture, corrosion, vibration, flooding and high temperatures, making them suitable for the solids and bulk handling industries.
Efficiency and good performance across the supply chain is achievable through effective control and instrumentation equipment. It can potentially make a real difference to a company’s annual performance and should, therefore, be an integral part of the continuing progress of the solids and bulk handling sectors.