Constant Communication
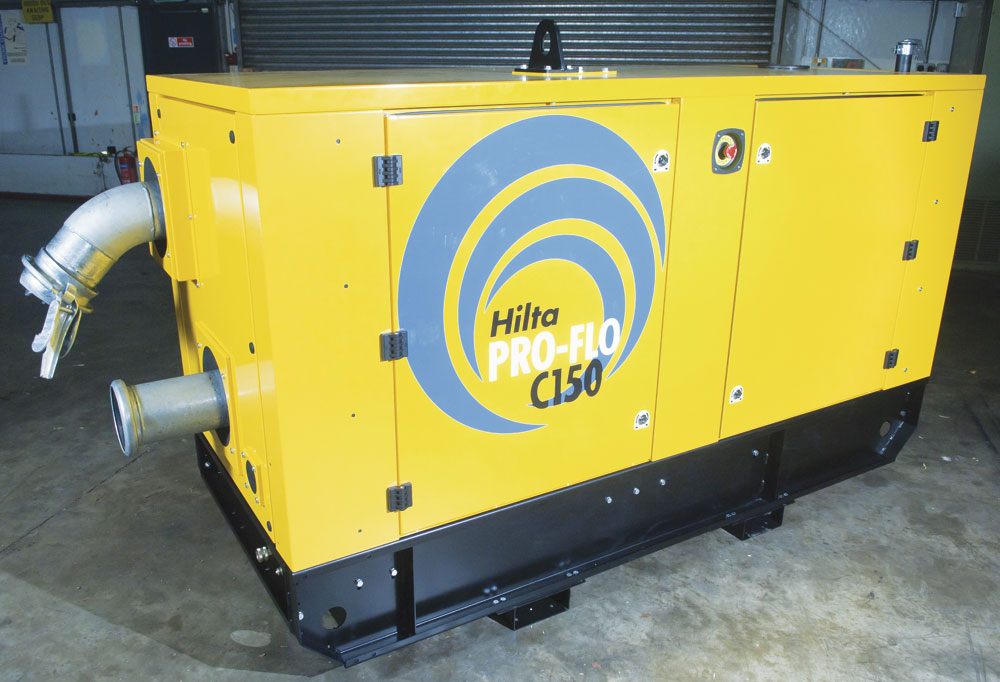
Bespoke telemetric solutions help make equipment work better and harder
Within the aggregates sector, some quarries have relatively limited lifespans and long-term investment in plant is not always viewed as the best economic choice. Many operators choose each piece of machinery locally on its merits with cost being the predominant factor. However, the shorter lifespan of some quarrying projects can also mean that there is less time to ensure decent profits, meaning that strict budgets have to be adhered to. As a result, companies are increasingly looking carefully at how they can ensure cost savings through more advanced technology and machinery, rather than settling for standard specifications.
Often required to function in remote, difficult and challenging environments, machines used in quarries and mines are faced with a unique set of conditions, meaning that new technologies are constantly at the forefront of the industry. Manufacturers are utilizing these new bespoke technological functions to find new and innovative ways to help quarriers save time, energy, and, most importantly, money by making their machinery work smarter and harder for them.
Pumps are among the most essential items of machinery found in a quarry – without the ability to remove excess water, work can grind to a halt and precious time and money can be lost. These days, contractors are becoming far more likely to invest budgets in new technologies, ignoring off-the-shelf solutions and working towards bespoke pump solutions that can meet the challenges set by quarrying conditions.
Commenting on the challenges facing the quarrying industry in particular, Martin Dickson, business development manager for pumps with ArcGen Hilta, one of the UK’s leading providers of hire equipment for the quarrying and mining industries, said: ‘Most of the hurdles faced by pumps in quarries and mines will not be found on any other job, and this means we have to constantly look at ways in which we can keep our pumps at the forefront of technology, making sure that our customers can find solutions that meet all of their individual requirements.
‘Functions such as float control mean that a lot of pumps can now be almost self-monitoring. With pumping of nuisance water taking place virtually 24h a day, seven days a week, float controls mean pumps can judge for themselves when the excess water has been removed and then turn themselves off when appropriate. This obviously saves wear and tear on a pump due to overuse, but most importantly, it saves fuel and, therefore, money for the user.
‘Technology is now progressing at such a rate that pumps can almost take care of themselves. One of the bespoke options that ArcGen Hilta have started to offer on their latest pump models is telemetrics, which, when combined with functions such as float controls and external fuel bowsers, can practically run a pump for you on a day-to-day basis.’
Telemetrics is a technology that involves the automatic measurement and transmission of data from remote sources. Sensors at the source measure either electrical data (such as voltage or current) or physical data (such as temperature or pressure). These data are then collated, transmitted and processed according to user specifications, allowing constant monitoring of machinery output and functionality.
As little as 10–15 years ago, remotely connecting a pump to a central database to provide continuous data was a difficult and often expensive task. A plethora of battery-powered GSM data-loggers appeared on the market but, in general, they only provided data once per day, which offered little or no advantages if a machine malfunctioned. Over the past few years, however, telemetry has advanced greatly and remote data-logging can now be used to send data continuously without the need to replace batteries every few months or to provide mains power.
Modern-day telemetrics function mainly via wireless communication, meaning that machines in remote, hard-to-reach locations can be monitored via a variety of communication devices. Constant monitoring can be undertaken via computers and laptops, and alerts can be sent to mobile phones in the case of a malfunction or breakdown, or even more minor issues.
As a result, technology of this kind is now beginning to infiltrate all markets where remote machinery is used, including, quarrying and mining. Telemetry options are now being offered on many pumps built for these industries, offering a wide variety of time and cost savings for users.
One of the main user benefits to be gained through the use of telemetry is a reduction in the manpower needed to keep a pump functioning. Using telemetrics to monitor the pump means it can be left to its own devices and monitored remotely – this means fewer checks and far fewer trips to the location of the pump to ascertain that all is running smoothly.
There are also significant environmental benefits. With an increasing amount of environmental legislation in the UK, there is a growing need for a more central approach to monitoring. By effectively managing and monitoring all of their processes, companies can use the information gleaned to implement environmental best practice wherever possible.
However, the biggest advantage for users of telemetrics is the reduction in downtime. For example, with the pumping of nuisance water often taking place overnight, a broken pump can mean that work is delayed by several hours or even days. Thanks to the use of telemetrics, when a problem arises, no matter what time of day or night, a warning message can be sent directly to computers and mobile phones, alerting project managers to the issue. With 24h support from machinery providers, this means that the problem can be fixed as soon as possible, reducing wasted hours and, therefore, wasted money.
Commenting on the telemetric system, Martin Dickson said: ‘Telemetrics may have been around for a number of years, but with benefits such as these, the technology has really started to increase in popularity over the past couple of years. We are experiencing an increasing number of enquiries about these systems, especially for our new pumps, and quarry operators are now beginning to see how bespoke options such as these can really help them meet their time and budget targets.’
An initial cost outlay to have bespoke options and functions, such as telemetry, fitted to plant and machinery for quarrying and mining projects, especially bigger projects, can offer substantial cost benefits in the long term. Broken or malfunctioning machinery, especially pumps, cannot be allowed to run the risk of bringing a project to a standstill, so there must be a reliable and effective way of monitoring machinery to ensure constant operation and progression in the face of financial constraints.
Companies should not shy away from paying extra for additional functions to be added to the machines they invest in for their projects, as the smooth running and correct functioning of these machines can make or break a job.