Benefiting From Automation
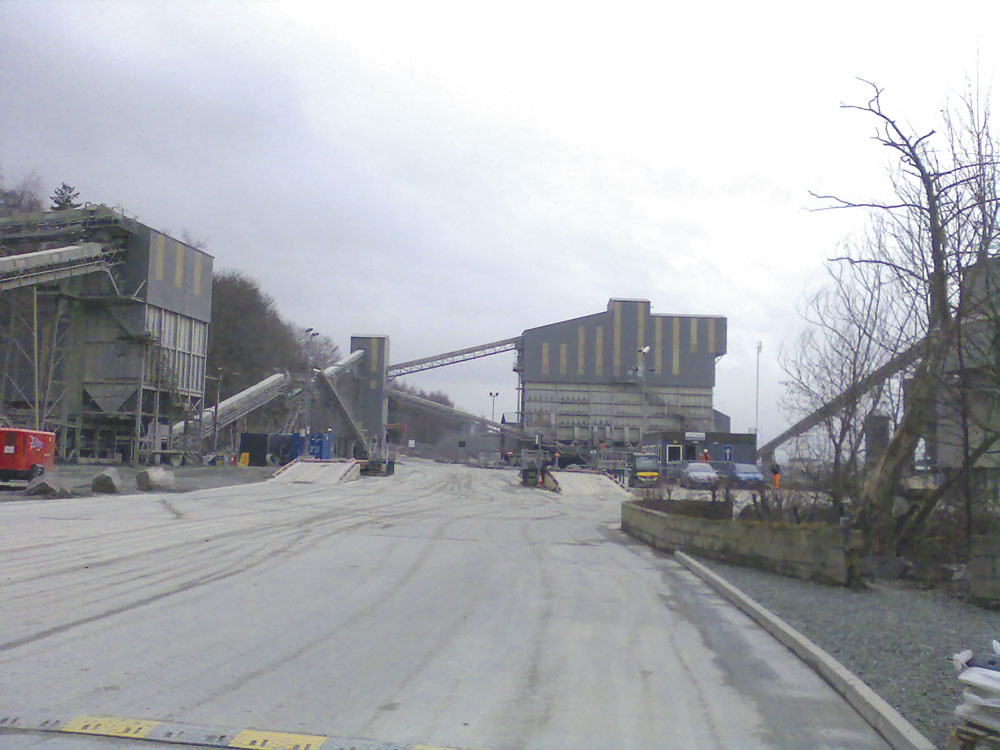
New approach to automation at Criggion Quarry exceeds expectations
The metsoDNA automation system installed during 2008 at Hanson’s Criggion Quarry has now been in operation for more than a year and results show that it has brought greater benefits than expected. The system has provided a truly integrated quarry-wide control and management information system resulting in a significant reduction in manpower, efficient daily operation, increased flexibility of production and, importantly for Hanson, improved customer service.
It was during 2007 that the management of Criggion Quarry, near Shrewsbury, decided to replace their existing control system. In many ways, the system that was replaced (based on an obsolete GEM 80 control system) was ahead of its time, as it was one of the first quarry control systems in the UK to feature a centralized control room. However, the reduction in manning levels achieved through the successful introduction of the metsoDNA DCS (Distributed Control System) constitutes a significant landmark.
The metsoDNA automation system controls all aspects of both the crushing plant and a dual-batch asphalt plant. In addition, Metso were responsible for the supply of a production–delivery management system linking customer orders to production planning, vehicle access and management (through the use of RFID tags, traffic lights and entry/exit barriers), as well as the supply of a new weighbridge. A new CCTV system and the establishment of wireless communications around the quarry facilitated the necessary infrastructure to provide a fully integrated solution.
The entire metsoDNA automation system was installed in parallel with the existing GEM 80 system. At no time during the project changeover was quarry production at risk as individual items of plant could be controlled by either system during the entire process. This lack of risk contributed greatly to the acceptance of the system by both operators and management.
Integrated crusher control system
The new plan was to have a single automation system that would control secondary, tertiary and quaternary crushing, as well as the screening and asphalt plants and lorry load out. To achieve this, it was necessary that such a system should be able to integrate the controls of the site’s existing Svedala ASR cone crushers.
Utilizing crusher automation experts from within Metso Minerals, Metso Automation were able to integrate the five existing Svedala crushers directly within the metsoDNA automation system. This resulted in significant cost savings as it negated the need to replace a number of obsolete dedicated crusher controllers.
According to David Richardson, sales manager at Metso Automation UK, the integration of third party crushers into the new quarry control system was only possible due to the expertise in crusher know-how available from the combination of Metso Automation and Metso Minerals. When combined with the control of the asphalt plant, screen and asphalt load out, the centralized control room efficiently integrates all aspects of Criggion’s production and reporting requirements.
Many benefits
The new metsoDNA automation system controls secondary, tertiary and quaternary crushing as well as the screening and asphalt plants and lorry load out. In addition, the new weighbridge connected to the metsoDNA system performs control and reporting functions. The vehicle tagging system totally automates the loading of trucks from the dry stone and asphalt plants, and from stockpiles, by means of a wireless tablet PC installed in the driver’s cabin of the truck loader. A management display panel linked to the vehicle-tagging system informs the driver where to collect his load.
According to Howard Sant, quarry manager at Criggion, the new metsoDNA automation system has produced many benefits. ‘Basically, the system looks after itself and monitoring is now continuous, rather than the ‘stop and start’ operation we had before. Control of the crushing process is significantly more precise, and much more information is readily on hand for management,’ he explained.
‘For operators, the system is really user-friendly; it is easy to understand and can be learned in a week. In the past, crusher controls were alongside the machines in a dirty, dusty atmosphere and we had to set each machine individually. Now all the controls are in a single clean control room and it is a clean and easy job to reset them as often as we like to optimize stone sizes.
‘As far as liaison and training were concerned, I went over to Metso Finland for a week with one of our operators to work with their experts in fine-tuning the system to meet our specific requirements. We found Metso good to work with and they offered us a competitive price. The engineers who came over to Criggion from Finland were first class.’
No downtime during system change over
Mr Sant added that the changeover from the GEM 80 to the new Metso system was very straightforward with no disruption. ‘By using disconnection terminals, which isolated sections of the old system, the new system was installed stage by stage. However, we were able to run the old system until the new one was completed. The whole operation took approximately 12 months.
‘We had originally planned for a reduction of three in quarry personnel. However we have found that five fewer members of staff are required. Customer service has seen a great improvement, and there are far fewer complaints from customers because the whole operation runs more smoothly.’
Expanding the system
metsoDNA is a modular automation system that can be easily expanded. Its powerful computational abilities allow it to perform a number of advanced functions. Considerable work has been conducted into the optimization of the crushing and asphalt plants, where both energy efficiencies and increased productivity have been addressed. The recent introduction of continuous, real-time condition monitoring to the DNA platform offers an extremely cost-effective and informative condition-monitoring solution.
‘We are seriously considering the possibility of adding condition monitoring to our system at Criggion,’ concluded Mr Sant. ‘We can see the advantages – for example, the ability to monitor frequency and friction in bearings, to continuously monitor wear on all the parts and to have predictive maintenance. In addition, we’re also thinking about having regular updates to the software, so that we can keep up to date with all the latest developments.’
For further information contact David Richard at Metso Automation UK on tel: (0870) 6061478; or visit: www.metsoautomation.com