Tackling Tiree
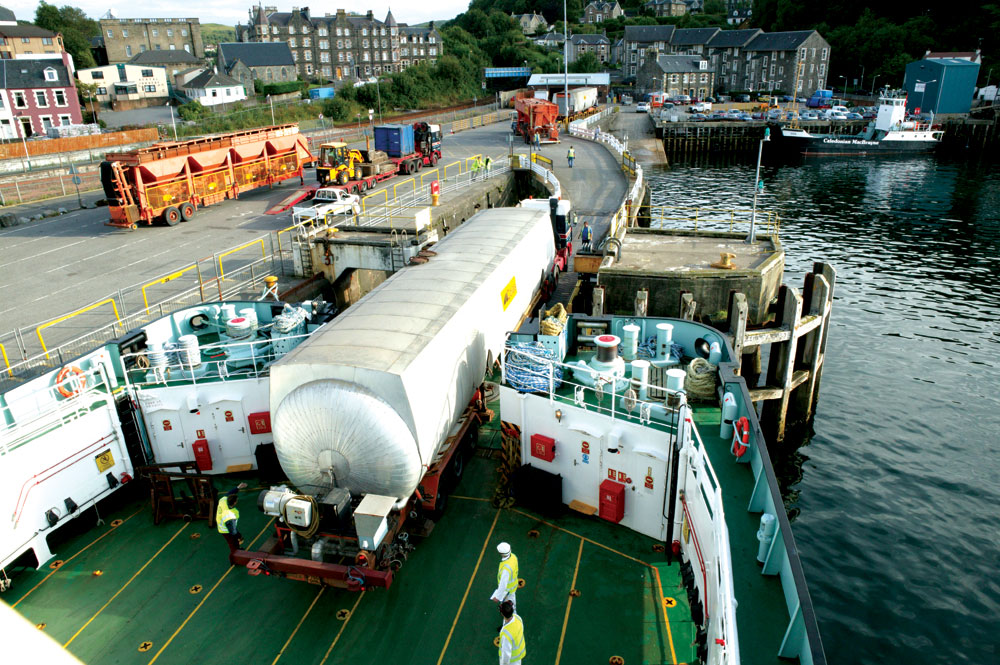
Colas have been furthering the use of more productive and durable materials for surfacing runways on the island of Tiree and attracting wide interest from the UK airfields sector
Airport operators have been showing great interest in Colas’s runway resurfacing work with asphalt developed to French standards; most recently on Tiree in the Inner Hebrides. BAA has visited Tiree to review the results, which represent confirmation of a considerable advance in materials technology for UK airfield surfacing.
The Tiree project has continued Colas’s work at Sumburgh on the Shetland Islands in 2006, when the company first introduced to the UK asphalt developed to the French BBA (Beton Bitumeux Aeronautique) standard. Colas have found BBA materials to be more productive in terms of manufacture and laying than the Marshall Asphalt traditionally used on UK runways. And BBA asphalt will also generally last longer, according to an independent study by consultants Scott Wilson.
According to Colas, it is continuation of the use of BBA material on Tiree that has grabbed the attention of other operators. HIAL (Highlands & Islands Airports Ltd), who operate Sumburgh and Tiree airports, were sufficiently impressed with the former to ask for a repeat on Tiree in 2007 – a decision that would mean extensive and detailed planning in order to get Colas’s high-capacity Ermont TSM 225 mobile asphalt plant to Tiree and to maintain the supply of constituent raw materials (see below).
Colas first had to select suitable aggregates and bitumen binder and take these to their laboratories in France for development and testing of the asphalt mix. The BBA standard is less conservative than the Marshall mix recipe approach. BBA asphalts are specified in terms of their required performance in use; allowing more use of modern polymer-modified constituents and variation of mix design to withstand particular frequencies and weight of traffic. Nevertheless, individual mixes have to be designed with the exact characteristics of the constituent materials taken into account, with laboratory tests carried out to prove the mix will perform.
‘Only aggregates that exhibit particular mechanical properties and are of high quality can be used in BBA mixes,’ said Colas’s business manager for airfields, Carl Fergusson. ‘The proximity to Tiree of the west of Scotland and the north-east of Ireland opened up possibilities for the supply of good-quality stone and bitumen from there by boat.’
The BBA asphalt mixes were designed and developed at Colas’s Paris technical center, using selected aggregates from Cashel in southern Ireland and Bonawe on the west of Scotland, with a binder to be supplied from Nynas Bitumen’s Dundee refinery. Evidence of mix testing was produced to satisfy HIAL that the design met the BBA standard, and Colas arrived on Tiree in August last year, ahead of surfacing during September.
In total, 20,000 tonnes of BBA asphalt were laid as a 100mm overlay on Tiree’s main runway (the airport has three runways on different alignments to suit wind direction), but only 21 surfacing days were needed. ‘The Ermont plant has a production capacity of 225 tonnes/h and enough bitumen and fuel storage to keep it running continuously for several days, which is particularly important when reliant upon difficult supply chain logistics,’ said Mr Fergusson. ‘With the better workability of BBA asphalt, we could lay 1,000 tonnes and more than 300m of the overlay between scheduled flights.’
An extra 20m by 50m aircraft parking apron was also built, and a considerable amount of ‘delethalisation’ work was carried out. This latter task involved the building of ramps to eliminate below-surface slab edges where the main runway meets taxiways, so as not to snag the undercarriage of any plane in the unlikely event of one skidding off the runway.
According to Mr Fergusson, HIAL needed an ‘affordable solution’; tendering an NEC Option C target cost contract with Scott Wilson Airfields as its consultant. ‘As at Sumburgh, we operated with open-book transparency and with a laboratory made available for the client to use at the Tiree site.’
Between the Sumburgh and Tiree projects, Colas commissioned Scott Wilson Pavement Engineering to carry out an extensive technical study of BBA materials for UK use in comparison with traditional Marshall Asphalt. The findings, published in a full report, came out very much in favour of BBA, which can typically reduce the required layer thickness by15%, says the report. Other benefits include greater recyclability and sustainability, and lower whole-life cost due to the reduced thickness and greater durability.
This confirms Colas’s view and adds to the company’s recent experience, which has shown BBA to be a more productive material in use. Generally, far more can be laid in a given time because the material is less difficult to mix and lay. This is well known in France, where the BBA specification is that to which asphalt has been produced for many of the country’s largest and busiest runways, including those of Paris–Charles de Gaulle Airport.
‘The results of the study provide independent validation of our own findings,’ added Mr Fergusson. ‘BBA asphalt also provides greater levels of grip and so is more versatile because the surface does not have to be grooved, although the Tiree runway was grooved to give HIAL absolute confidence. Critically, BBA has superior physical and mechanical properties, leading to savings in whole-life cost for airport operators due to less maintenance intervention and disruption.’
Planning key for production
Detailed planning of deliveries and transport had to be conducted before Colas embarked for Tiree – not least, for working out how and if Colas could get their mobile plant to the island’s airport.
‘A lot of planning went into that,’ said Colas’s business manager for airfields, Carl Fergusson. ‘A detailed storage plan was produced to show the plant could be stowed to maritime rules, with each trailer reversed on to the ferry so that they came off in the right direction at Tiree. Even then, we had only one day available for the trip in the month, because the plant could only be disembarked on the highest tide.’
Before leaving for Tiree in August last year, Colas practised the necessary manoeuvres of the 13 trailers of the Ermont plant in their Birmingham yard, with cones marking out the limits of the Scottish port at Oban, Tiree’s jetty and the island’s B-classified roads. The practice runs showed that road junctions on Tiree would have to be modified to accommodate the long trailers and that great care would be needed when they arrived. ‘There were centimetres to spare in places,’ said Mr Fergusson. ‘But once on the island we were up and running in less than a week. The next challenge was keeping the vital supply operation going.’
Colas sent something across on the 4h ferry crossing from Oban every day during September last year. At the peak of production, bitumen was arriving daily from Dundee while aggregate arrived every third day from Bonawe, near Oban, or Cashel in southern Ireland.
‘Precise timing was needed to maintain deliveries and asphalt production,’ said Mr Fergusson. ‘No-one was holding the ferry for us and it only hangs around in each port for about 20min. Missing the boat would mean a 24h delay, so good planning was vital in order to keep to the surfacing programme.’