Simple Rules For Safe Bitumen Storage
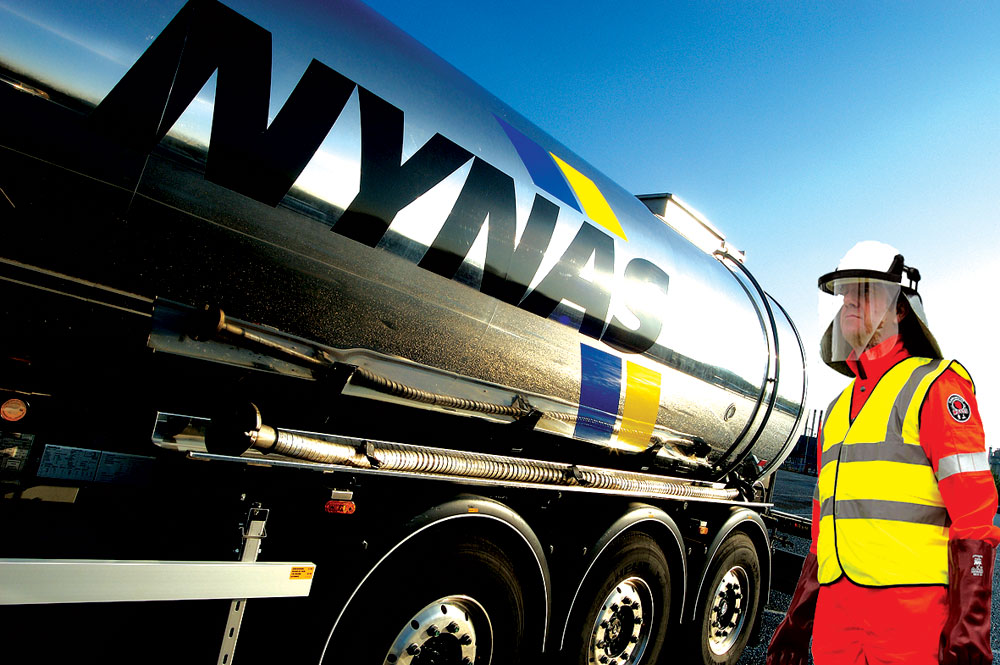
Regular maintenance and adherence to some basic rules should be enough to ensure that bitumen is safely stored at quarries and roadstone facilities. Ian Lancaster and Paul Lamb of Nynas Bitumen explain some of the pitfalls
The simplest way to ensure that on-site bitumen storage tanks are safe is to comply with the relevant codes of practice. Any tanks that are used for storing bitumen should be manufactured in accordance with the appropriate British Standard, so operators should check this with the manufacturer before they buy.
The Refined Bitumen Association (RBA)’s Code of Practice for the Delivery of Bitumen Products (revised 2001) sets the industry benchmark for the delivery, receipt and storage of bitumen products, and defines best practice and minimum standards. The code of practice covers all aspects of delivery, and the RBA also publishes guidance on safe bitumen tank management. Additional guidance can be found in the Energy Institute’s ‘Bitumen Safety Code’, which covers every aspect of bitumen delivery, storage and handling, including health and environmental management and fire prevention.
Problems with bitumen tanks may occur due to infrequent maintenance. At Nynas’ own facilities, where high-performance materials are manufactured and stored, the company employ a regular maintenance regime that includes tank cleaning. Many asphalt plant managers do not have this luxury, but in the long term regular maintenance pays dividends.
If a tank is coil heated, for example, over time it is possible that coke will build up on the coils, making the coil less efficient and having a knock-on effect on energy consumption. Taking the time to empty the tank and clean off any coke build-up could improve efficiency dramatically.
Even tanks that are externally heated can be subject to coke build-up or carbonization. Hot spots in the tank are created where the heating pads touch the wall of the tank, and this is where carbonization can occur.
Efficiency can also be compromised by the build-up of bitumen deposits on the cross-members of square tanks. Over time, if this goes unchecked, these deposits will build up to such an extent that the storage capacity of the tank is severely compromised. While this may not be a safety issue, it is an important issue when it comes to cost and effective working, and is one that could be avoided by good practice and regular maintenance.
Some maintenance issues, however, do have serious safety consequences, the most worrying being the potential for fire or explosion. While Nynas do advocate regular tank maintenance and cleaning, if a tank is taken out of service, it must be completely dry when it goes back into commission. Any water left in the tank when the bitumen is delivered will be immediately turned into steam and expand significantly, presenting a real risk of explosion. A guide on returning bitumen tanks to service is published by the RBA.
As bitumen is a hydrocarbon, the potential for fires cannot be ignored. When fires do occur, they may be reported as having been in the tank itself, but this may not be the case: fires can also occur in the tank insulation. Fires in the insulation can occur in two ways – through spillages or through migration. Storage tanks tend to be insulated by Rockwool-type products, and a spillage of bitumen into a rockwool system can ultimately lead to a fire.
Even without spillages, however, fires can still occur in the insulation as, over a prolonged period of time, some of the lighter materials within the bitumen can migrate and find their way into the tank insulation. This tends to be more of an issue with old tanks, and particularly those that are electrically heated using pads on the outside, as hot spots encourage this sort of migration.
Again, regular emptying of the tank and replacing worn insulation – especially where bitumen has been spilled or migrated – can go a long way to preventing fires.
It is crucial that everything possible is done to reduce spillages. Section 4 of the RBA code of practice for the safe delivery of bitumen products details the requirements that tank owners need to have in place to prevent spillages occurring when bitumen is being delivered, including high-level alarms and well-calibrated gauges.
Data from the RBA’s Health, Safety and Environment committee shows that 90% of spillages at the delivery stage are caused by customers misunderstanding the safe working capacity of their storage tanks. The code stipulates that customers should leave a 10% clearance in their tanks after every bitumen delivery, but there is a tendency for some to fill the tanks as much as they can. Properly fitted and working high-level alarm systems should prevent this from happening.
Problems can also occur at the delivery stage if the inlet pipes are not sufficiently warm. In the past customers have complained to Nynas that their bitumen supply is too cold and is blocking up the pipes, but what the company often finds is that the location where the delivery tanker offloads is some distance from the storage tank. This means that the new bitumen has a long piece of pipe to get through, and if this is not lagged or trace heated, when the bitumen starts to discharge the first thing it comes into contact with is very cold metal pipe, so it cools down and solidifies.
To avoid this, inlet pipes should be as short as practically possible, they should be lagged and – if distance cannot be avoided – they should have trace-heating elements fitted. It is important to remember to switch the trace heating on well before the delivery tanker is due to arrive, to give the pipe time to warm up, and also to switch it off again once the delivery is finished to prevent coke build-up on the element.
Top tips
- Follow the principles outlined in the RBA code of practice
- Fit tank gauges and regularly check to make sure they are working
- Fit high-level alarms and regularly check to make sure they are working
- Clean and maintain tanks regularly
- Build effective bunds around tanks so any spillages will be contained
- Make sure vent pipes are maintained and clear
- Check tank lagging and replace it after any spillages or bitumen migration