Runway Success
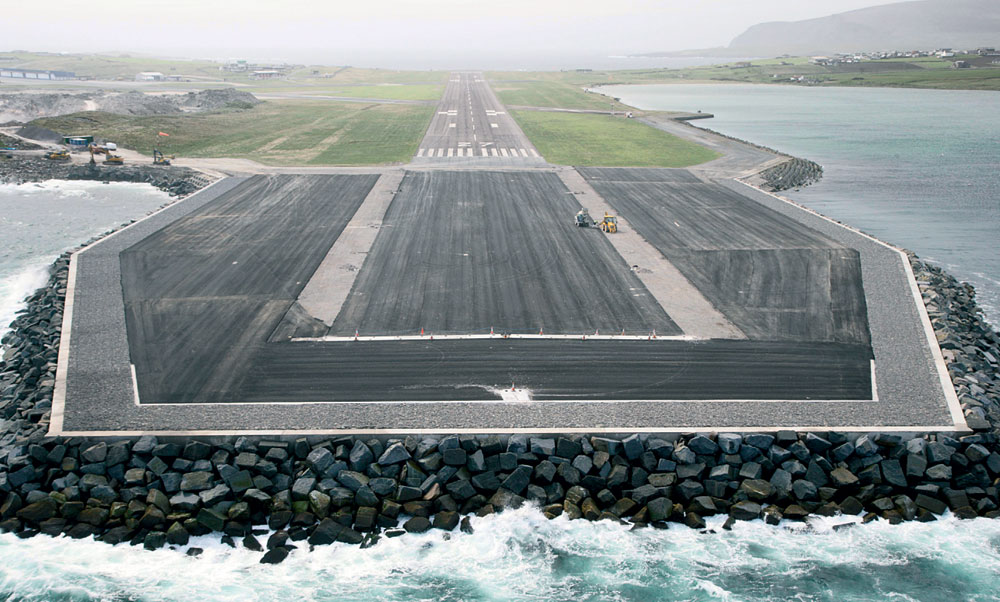
Sumburgh Airport in the Shetlands becomes the first UK airfield to benefit from Colas’s European airport surfacing materials
By Carl Fergusson, business manager – Airfields Division, Colas Ltd, and Steve Cant, technical manger, Colas Ltd
The recent contract for Highland and Islands Airports Ltd (HIAL) to extend and upgrade the runway at Sumburgh Airport in the Shetland Islands, the UK’s most northerly gateway, was a notable project for a number of reasons. Not least was that Colas Ltd became the first contractors to successfully utilize European airport surfacing materials within the UK’s airfields industry, coupled with the logistical problems posed by Sumburgh’s remote location, some 150 miles from the Scottish mainland. Working as specialist subcontractors to Balfour Beatty Civil Engineering Ltd, as part of an overall £9.75m redevelopment project, Colas undertook the £1.8m resurfacing and grooving of the existing runway and newly constructed runway extensions.
To ensure an efficient, cost-effective programme of works, Colas worked closely with Balfour Beatty and HIAL and, by drawing on the airport expertise of their parent company, Colas SA, were able to offer various innovative solutions during initial project investigations. These included sourcing the required aggregate from a temporary quarry (Wilsness Hill) inside the airfield perimeter and using their own on-site high-output mobile asphalt plant.
Specification
Designed and project-managed by the Capital Programme Service of Shetland Islands Council, the project introduced into the UK for the first time an advanced, high-performance airfield surfacing material, developed by Colas SA in France. Known as Betoflex, it meets the French Beton Bitumeux Aeronautique (BBA) standard NF P98-131 and has been widely used on airfields across Europe. The Airfields Division of Colas Ltd was the first contractor to use it in the UK. Uniquely in the UK, the French material standard was adopted as the job specification for the asphalt element of the works and, correspondingly, all physical and mechanical properties of the mix constituents had to meet French standards.
Unlike typical UK standards, NF P98-131 does not provide grading or binder content specification envelopes. Instead, mechanical performance targets for laboratory mixtures are defined and end-product performance characteristics specified, which the producer is required to meet. In this way, three classes of mixture are defined by the standard. The class required for a particular contract is determined from a pavement design process that brings into play the type and mass of aircraft, frequency of use, and aircraft tyre pressure. Once a satisfactory design has been produced the appropriate class of BBA may be selected together with an appropriate aggregate size and grading (continuous or gap-graded) and appropriate aggregate requirements (related to the layer and type of airfield). Thus, for Sumburgh Airport the design produced required a Class 2 BBA 0/10D with aggregate of Class BIIIa laid to a depth of 45mm. Requirements for the mechanical performance targets of the Sumburgh laboratory mixture are shown in table 1.
Betoflex provides numerous benefits compared with more expensive traditional airfield paving materials, not least in terms of whole-life cost, and can be manufactured and laid more quickly, which meant some 200 linear metres of runway could be laid each night at Sumburgh. Installation is not constrained by the grooving process and, at most European airports, due to its enhanced texture and higher friction value, it is used without being grooved. However, by grooving runway 09/27 at Sumburgh, aircraft are able to stop over shorter distances in the wet, allowing the runway extension to be significantly shorter than it would otherwise have been, saving the client a considerable amount of time and money. In addition, when compared with Marshall Asphalt, Betoflex has been shown to have greater load-spreading ability, reduced temperature susceptibility, increased resistance to age hardening, increased resistance to permanent deformation, comparable levels of fatigue resistance and no susceptibility to moisture damage, providing significant whole-life cost benefits.
Pre-works testing and mix design
Aggregates
Clearly, transporting the required 22,200 tonnes of aggregates from the mainland would have been extremely expensive, therefore Colas identified Wilsness Hill, within the airport perimeter, as a suitable source of aggregate for all asphalt production. Thus both time and costs were reduced by using local aggregate and manufacturing the asphalt on site. A comprehensive study of the aggregate source was undertaken, starting with an examination of the geology by Colas’s in-house geologist. There followed a series of tests looking at the mechanical and physical properties of aggregates produced from Wilsness Hill, conducted both by independent test houses in the UK and by Colas’s own Campus for Science and Techniques facility at Magny-les-Hameaux, near Paris. The work in France focused on the relationship between LA, MDE and FI and resulted in a more stringent shape requirement for aggregate for use in the BBA 0/10 D surface course. This in turn required additional processing of the Wilsness Hill aggregate, which was composed of Old Red Sandstone, to ensure this shape requirement was met, as well as a more stringent test regime.
Aggregate characteristics required by NF P98-131 are summarized in table 2.The use of local material and on-site production meant greater control over quality and supplies. It also minimized airport disruption and was environmentally and socially beneficial as it avoided the impact of some 1,100 lorry movements on local roads.
Mix design
The mix design process follows a staged approach. Provided the mix meets each stage of the process, it proceeds to the next stage or level of test. If not, adjustments are made and the process repeated until a satisfactory mixture is achieved. For the Sumburgh contract three levels of test were deemed necessary, each building upon the previous level (NF P98-131 has four levels of test available). The first level is mandatory and involves designing the target PSD to achieve the desired air voids under compaction in the PCG Gyratory Compactor NF P98-252). Once this is satisfactory, the Duriez Test is performed (NF P98-251-1) to assess the water sensitivity of the mixture. The mixture then proceeds to level-two testing where resistance to rutting is assessed (NF P98-253-1) and then to level three for assessment of complex modulus (NF P98-260-2).
The choice of binder is left to the producer who must decide which type and grade to use to achieve the required mixture characteristics and mechanical performance at the design binder content. The design team at Colas SA suggested penetration grade 40/60 bitumen would be sufficient to achieve the required mechanical performance properties of Class 2.The choice of binder in this instance was also influenced by the logistics of getting the binder to the island.
Production and control
Colas’s mobile asphalt plant, which had been transported to the Shetlands from Birmingham, was sited a short distance from the entrance to the terminal building. One of the few truly mobile asphalt plants in the UK, and certainly one of the largest with a production capacity of 225 tonnes/h, the plant was central to the efficient handling of the contract. The Ermont TSM 225 plant, which requires no foundations, was erected and commissioned within 10 days of its arrival on site. The surface course was laid by two Vogele pavers laying in echelon and compacted by two Bomag 161 rollers, with a Hamm HW90 deadweight following each paver. With no reliance on external asphalt supplies, work on the 100,000m2 resurfacing project, including 43,000m2 of runway extension, could be closely monitored and controlled. The presence of Colas’s fully equipped mobile site laboratory and experienced staff allowed quality control to be established in accordance with the requirements of Sector Scheme 14, and the plant was accredited to ISO 9001 while on this contract as a result of this. In addition, a 50-tonne capacity weighbridge was shipped from the mainland to the site. A comprehensive quality plan for sampling and testing was established, which included the usual minimum compositional analysis test rates required by Sector Scheme 14, based on Q level. At the outset these were onerous because the plant was operating at Qx until 30 results were available to establish a Q level, and production at the beginning of the contract was in excess of 1,400 tonnes per shift. Basecourse and binder course compaction was monitored by NDM and confirmed by PRD on cores taken every 500 lane metres. During installation of the surface course, compaction was monitored by an NDM suitable for use with thin layers, and in-situ air voids were confirmed on extracted cores taken every 1,000m2 installed. Production was carefully co-ordinated with the supply of 1,080 tonnes of bitumen, which was shipped by Colas from the mainland in 54 loads along with the bond coat (Colbond 65) to meet site demands.
Operation
Being a significant component of the island’s transport infrastructure, it was essential that the runway remained fully operational throughout the duration of the project. This meant that all equipment had to be withdrawn to safe zones during daytime aircraft movements. Furthermore, the A970, which runs across the west end of the runway, was to remain open at all times. For the final runway surfacing, which involved milling and removing the existing surface, all work was carried out at night. Possession of the runway was given to Colas at 10pm and work was completed by 4.30am the following morning, allowing plenty of time before the handover at 7am, by which time the runway had to be clear and operational. The use of Betoflex reduced construction times, an important factor at any busy airport where shorter nightworking periods restrict the amount of surfacing that can be completed in any shift. This required a close co-operative partnership with main contractor, Balfour Beatty, and the establishment of clear communication protocols and working procedures with HIAL and the airport management.
Although the location of the site posed certain logistical problems in terms of the transportation of plant, equipment and materials, Colas have particular expertise both in airfield work and in operating in remote island locations, having previously undertaken contracts at airports on the islands of Jersey, Islay and even the Falklands. Based in Birmingham, the mobile asphalt plant, paving machinery and site laboratory made the 450-mile trip by road to Aberdeen, followed by a 14h boat journey to the Shetland
Islands. They were accompanied on site by around 40 skilled and experienced Colas staff from Birmingham and support staff from France, together with local Shetland-based resources.
Acknowledgement
The speed and success of the project – completed in just 28 days – was made possible by the integrated approach adopted by Colas, Balfour Beatty and HIAL, which allowed the various parties to develop technical solutions leading to time- and cost-savings, both before and during the contract period.
To ensure that the proposed developments posed minimal environmental impact, all activities were organized and managed under the Colas environmental management system, which has been developed in accordance with the ISO 14001 environmental standard.
This article first appeared in Asphalt Professional magazine and is reprinted here by kind permission of the Institute of Asphalt Technology.