Resisting Fuel At Bristol Airport
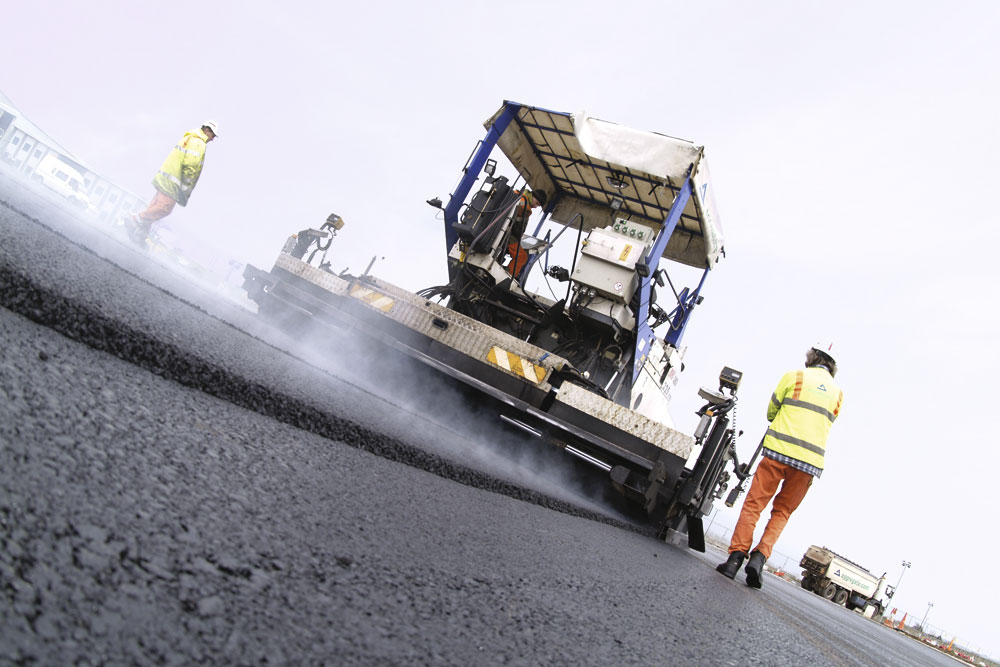
Fuel-resisting asphalt has been designed for two former military runways at Bristol International Airport, surfaced as part of an ambitious programme to expand aircraft operations. Mike Walter reports.
Pressure to extend commercial services has led Bristol International Airport to rejuvenate two redundant runways and relocate private planes to a new facility away from the main terminal. The former runway areas will now provide two new taxiways, light-aircraft parking, a new southern apron and two refuelling areas.
Both refuelling areas have been surfaced using a fuel-resisting asphalt and mark the first use of the material on an airfield. The asphalt material is based on a product known as Bardon 10mm Forpave and has been produced using a fuel-resisting binder known as Nyguard, designed by materials specialists Nynas Bitumen. The binder is often used in asphalt designed to resurface motorway service areas and bus depots, where the potential for fuel spillages is greater.
Bardon Aggregates’ regional technical manager, Chris Mellor, said: ‘We have specifically designed a material here that not only resists fuel-spillage damage, but is also highly durable and provides excellent deformation resistance.’
The binder’s ability to resist fuel lies in a special blend of polymer-modified ingredients, which also help to give the asphalt added strength when it is put under pressure. Nynas Bitumen senior chemist Dr Ian Lancaster explained: ‘A high level of stiffness is afforded to asphalt containing Nyguard, which remains unaffected should fuel be spilled. The binder was first developed about five years ago and can withstand the enormous point loads exerted on an airfield by aircraft tyres.’
The Nyguard binder specified for the airport surfacing was mixed with a durable crushed-quartzite aggregate at Bardon’s Westleigh asphalt plant in Devon. In total, 240 tonnes of the fuel-resisting asphalt were laid at Bristol, to a depth of 30mm, by Bardon Contracting. The material represented a fairly small yet highly significant part of a larger surfacing operation, which involved laying nearly 7,000 tonnes of asphalt.
The airport’s advisors, Bristol Engineering Consultancy, requested that three further types of surfacing material were specified for the airfield. The taxiways measure 500m and 300m in length respectively; one was resurfaced with Bardon 6mm Smatex, the other with Bardon 10mm Smatex. Both stone-mastic asphalt materials were produced using standard 50-penetration binder. Part of the new southern apron not designated for aircraft refuelling was surfaced using Bardon 10mm Smatex industrial surfacing, again produced with a straight-run bitumen. Surfacing took place largely during the day, with night works required to tie in to the runway.
The two former runways now rejuvenated into taxiways, aprons and refuelling areas were used by fighter aircraft during the Second World War but later fell into disrepair and have largely been unused ever since. Reinstatement and repairs were carried out to sections of the runways prior to them being resurfaced and extra carriageway strength was provided through the use of a glass geomembrane rolled out beneath the binder course.
Resurfacing of the former runways has been carried out as part of a larger scheme, headed by main contractors Nuttall, to develop airport facilities including a new light-aircraft hanger and offices for the Bristol Flying Club on the south side of the airport.
Nuttall site agent John Hutton said: ‘The old runways were of very thin construction and unusable. We filled the potholes and carried out patch repairs and strengthening before overlaying the existing construction with a 20mm sealing layer. Glassmat geomembrane was than placed, after which binder and various surface courses were laid.’