Reducing Emissions
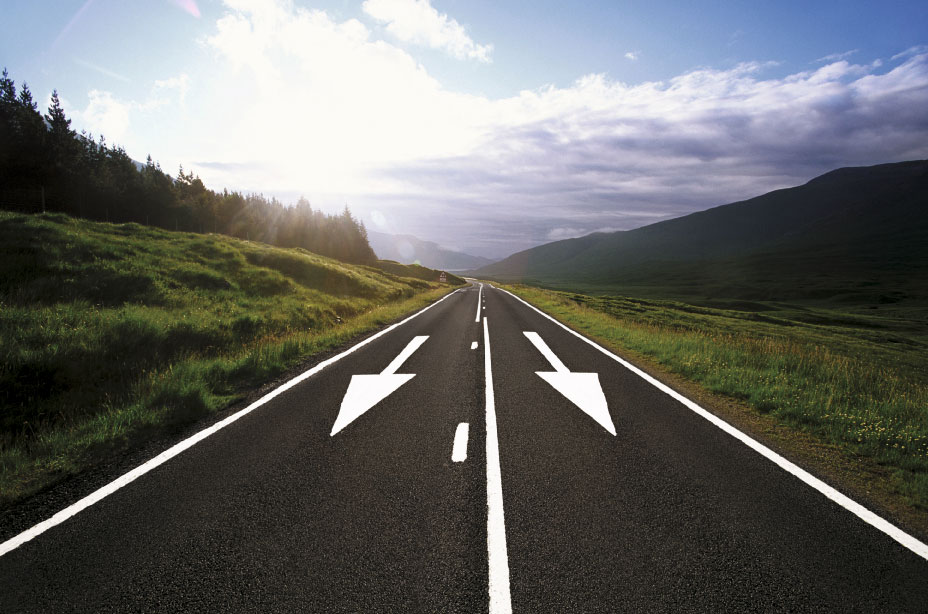
Producing asphalt at lower temperatures has become an important aim of material suppliers and Shell Bitumen think they have the solution – a ‘warm blend’ of bitumen binders
It is generally well known within road surfacing circles that reducing asphalt production temperatures provides environmental benefits with regards to emissions and energy consumption. To achieve this objective, however, material suppliers must not only demonstrate the environmental benefits, but also that their lower-temperature asphalt performs as well as traditional hot-mix products.
This is what has been achieved with the Shell WAM Foam process, a new way of manufacturing asphalt. Conventional hot-mix asphalt processes use one grade of bitumen at 170°C, whereas Shell WAM Foam uses two binders at lower temperatures. The combination of ‘hard’ and ‘soft’ components results in a bitumen blend and asphalt with the same properties as a standard hot mix, but one that can be produced and laid at significantly lower temperatures.
According to Shell, their WAM Foam process yields environmental benefits while producing high-quality asphalt. Traditionally, asphalt is heated to 160–170°C for workability. Asphalt manufactured by the Shell WAM Foam process is typically at 110–120°C.
‘Results from a site in Florence, Italy, show that this decrease in temperature offers a dramatically large reduction in emission of greenhouse gases and fumes, with up to 30% less energy consumed,’ said Shell Bitumen technical manager Michael Lecomte. ‘The figures refer to a study carried out by Italian contractor Conglobit during the production of their new asphalt mixture, Greenfalt, manufactured at low temperatures with the Shell-patented WAM Foam technology.’
Conglobit carried out a trial of Greenfalt with WAM Foam in Italy during October 2006. Measurements were made of fumes and pollutants emitted from the contractor’s asphalt plant, while the performance of the material and emissions were monitored on site on the Firenze to Livorno trunk road.
Around 900 tonnes of Greenfalt were mixed at Conglobit’s plant and laid on a 1.3km length of the Firenze-Livorno road near Florence. A single 3.5m width was laid in three layers. According to Shell, the air temperature varied between 19°C and 30°C during the day and the weather was recorded as cloudy with no wind – a good day for asphalt trials. Emission measurements were made during sample periods of 400mins, with Conglobit’s operatives wearing fume-collection devices to measure their exposure.
‘The results showed a 35% reduction in fuel consumption alone,’ said Mr Lecomte. ‘Emissions from the chimney were obtained at a production rate of 140 tonnes of asphalt per hour and showed that lowering the operating temperature from 180°C to around 125–130°C generated considerable reductions in the amount of gas and dust emitted.
‘The exposure data obtained on site was compared with Italian operational environmental limits and no measured values exceeded these limits.’
According to Mr Lecomte, WAM Foam technology has been proven to be significantly more environmentally friendly in terms of emissions of carbon dioxide, nitrous oxide, dust and organic aerosols. ‘This confirms the great potential of this solution for the environment,’ he said. ‘Over 30% reduction in greenhouse gases was recorded, with up to 55% reduction in fine dust and 30% less fume emissions during production. Energy savings were up to 30%.
‘The benefits of Shell WAM Foam have proven to be not only environmental,’ he added. ‘Unlike hot-mix asphalt, which is susceptible to weather conditions, asphalt with Shell WAM Foam offers greater workability and can therefore be stored for longer periods. The important workability window has been thrown wide open as mixes can be stored for longer and taken further.’
One year has passed since the Firenze-Livorno trial sections were laid, and while no report regarding field performance can be issued yet, indications are all positive that the road is performing well.
Since 1999, more than 60,000 tonnes of asphalt mixture using the WAM Foam process have been laid in other trials and commercial jobs throughout Norway and Sweden. In general, practical field experience demonstrates that WAM Foam mixtures give equivalent performance to hot-mix asphalt in different road categories and different climates.