Recycling At More Than 50%
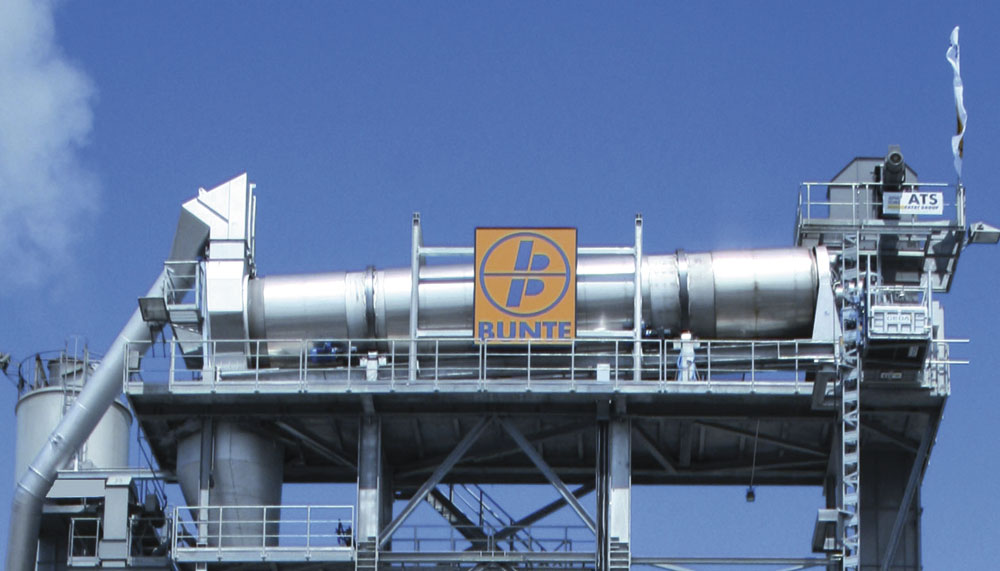
Fayat Group companies ATS and Marini develop double-drum solution for German road contractor
When German road contractors Johann Bunte sought to reduce their energy consumption in a bid to optimize their asphalt production, the company looked to meet this target by dramatically increasing the amount of RAP used in their asphalt mixes and by minimizing the electrical consumption of all major drives through the use of frequency inverters.
Two years ago the dryer on one of the company’s existing batch-mix plants, which was originally installed in 2005, was retrofitted with an ATS/Marini recycling ring to increase recycling rates. The existing RAP cold feed into the mixer was suitable for addition rates of up to 20%, but by retrofitting the recycling ring, this rate has been increased to 40% or more.
However, to achieve large production runs and higher rates of RAP addition, it was also necessary to install a powerful parallel dryer with a burner capable of running on gas oil or coal dust. ATS were awarded the contract to carry out this retrofit work, together with installation of frequency inverters for both dryer drums and the bag-filter exhaust system.
In addition, as the complex control procedures for the ATS burner system and RAP dryer could not be handled by the plant’s existing three-year-old control system, it was necessary to install the latest generation ATS/Marini plant control system, which allows all processes to be started, stopped, altered and supervised at the click of a mouse button, while the system’s batch log registers and records all parameters, consumption, events etc.
The newly developed ATS/Marini burner control system receives additional input from belt weighing scales indicating material flow into the drum. The system calculates any change in material flow and adjusts the burner settings accordingly and in due time to deliver product at a constant temperature. This offers additional energy savings and improvements in asphalt quality.
Highlights of the project included the delivery of:
- a parallel-flow RAP dryer drum with a nominal output of 180 tonnes/h and featuring variable rotation speed to achieve the correct RAP temperature of 140–160°C at the dryer discharge. The 14m long x 2.5m diameter drum is also designed to ensure that the exhaust fume temperature is no higher than 10–15K above product temperature
- a 32m high heavy-steel support structure for the new RAP drum, together with an insulated and electrically heated 26-tonne capacity buffer hopper, a 3-tonne capacity weigh hopper and a highly inclined mixer delivery chute equipped with special steel surfaces, heating and insulation, to avoid any sticking
- a dual-fuel burner suitable for use with coal dust or gas oil and featuring a carefully designed combustion area to allow effective transfer of the heat into the RAP material without overheating and damaging the bitumen content.
The ATS/Marini concept, developed in close co-operation with Johann Bunte, proved its performance capabilities during its first major production runs by achieving daily outputs of more than 2,500 tonnes and RAP recycling rates well in excess of 60%. Moreover, erection and commissioning of the new plant took place in less than two months without any major interruptions to the ongoing production of hot-mix asphalts.
Cormac Ltd, Unit 1, Burnhouse Industrial Estate, Whitburn, West Lothian EH47 0LQ; tel: (0141) 646 2066; fax: (0141) 646 2077; email: sales@cormac.co.uk