Potential Dangers From Heated Fuel Systems
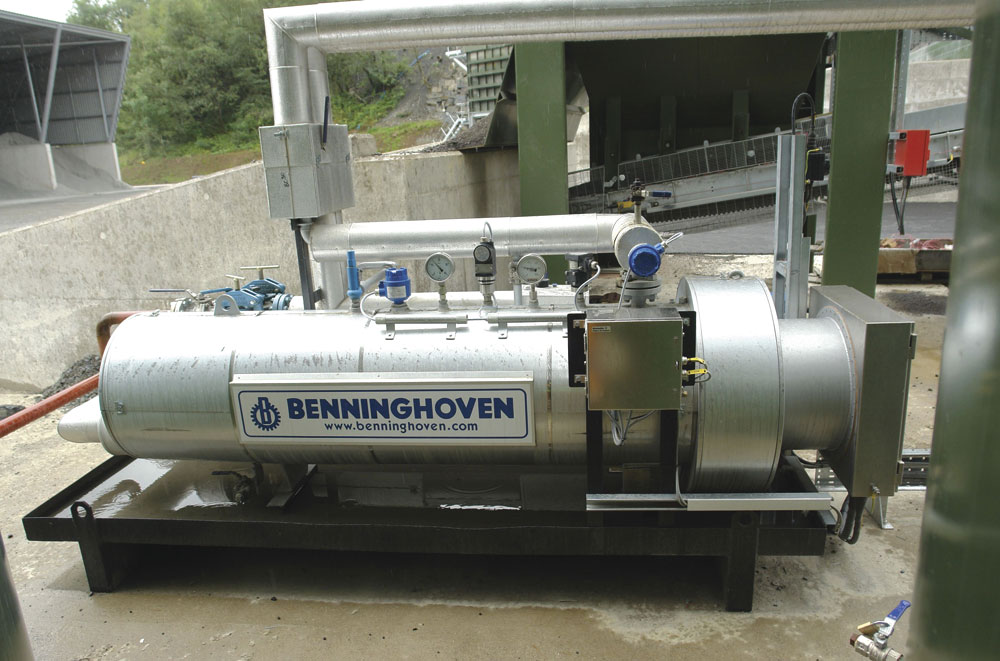
Baseefa have recently been involved in a review of the use of recycled fuel oil (RFO) heating systems to establish whether such plant and associated equipment falls within the scope of the ATEX Product Directive. In this article Andrew Dickinson, Baseefa certification engineer, details the issues and recommends action that should be taken by those responsible for such plant.
RFO heating systems are commonly used in quarries for asphalt production. They typically consist of an outdoor fuel-oil storage facility where fuel is stored at the local ambient temperature, from which the oil is pumped at pressure through a heating skid (often electrically heated) equipped with necessary controls, such as regulators, valves and associated filters, to supply heated oil to burners.
In the case of asphalt production, the RFO is typically raised to temperatures of around 75°C, before being pumped to burners used in the production process. The RFO is pumped around a ring main in order to maintain consistent output temperature and pressure.
Typical systems may run at pressures of around 13 bar, with overpressure detection and relief systems typically set to give a 50% safety margin (ie operating at about 20 bar), in addition to over-temperature detection and mitigation systems.
Ideally, the temperature of the RFO, or any fuel which may be used, would never be raised to its flash point within the heating system. However, it is important from an environmental and commercial standpoint that the fuel temperature be raised sufficiently to achieve efficient and clean combustion. Also, the required temperature will be dependent on the fuel’s viscosity – a basic physical characteristic which may vary, even between suppliers of nominally the same fuel, and which may require the fuel to be raised above its flash point.
Additionally, any variability in the flash point of batches of RFO may lead to the flash point being exceeded. The oil passing through the heating skid may vary considerably in its flash point due to the use of a wide range of recycled fuel oils. Some evidence suggests that variations in the content of RFO – such as the presence of unleaded petrol in some batches – may reduce the flashpoint of RFO to values as low as 25°C.
Also, as there are several different methods of measuring the flash point of a flammable substance, it is not always possible to directly compare flash points which are obtained from different sources.
It is, therefore, reasonable to consider that at least some of the oil passing through the heating system will be raised above its flash point, either under normal operation or as a result of malfunction.
As the system operates at pressure, the release of RFO mists is another possibility in the event of faults and, as mists may ignite at temperatures below the flashpoint of the bulk fluid, this also needs to be considered. Incidents have occurred where significant amounts of explosive vapour have been released. Consequently, it is considered that potentially explosive atmospheres could develop in the vicinity of such systems.
Scope of ATEX
The ATEX Directive 94/9/EC, enacted in the UK by The Equipment and Protective Systems Regulations 1996, could be summarized as: ‘ensuring that no effective ignition sources are present on ATEX-compliant equipment’. Critically, the Directive considers the use of equipment in line with its ‘intended use’, including the potential for its misuse and malfunction. The level to which this is taken is dependent on the zone of use.
From the earlier consideration of RFO heating systems, it can be seen that it is possible that batches of RFO with lower than expected flashpoints may be received. This is borne out by evidence from within the industry. Therefore, in line with the notion of ‘intended use’ and foreseeable misuse, all such equipment appears to fall within the scope of the ATEX Directive.
The collection of equipment creating the oil-heater skid will, therefore, constitute an assembly under the ATEX Product Directive. Consequently, the appropriate Conformity Assessment Procedures described in the ATEX Directive will need to be applied.
Depending on the zone of use, the involvement of an independent third party, known officially as an ATEX Notified Body, such as Baseefa (commonly known as a ‘certification body’), may or may not be required. However, even if the services of an ATEX Notified Body are not mandatory, it is quite common to involve notified bodies on a voluntary basis to provide independent reviews and guidance, with the intention of providing additional assurance to both the manufacturer and the end-user of the equipment.
While the ATEX ‘Product’ Directive places responsibilities on the manufacturers of equipment designed for use in potentially explosive atmospheres, the ATEX ‘User’ Directive also places responsibilities on users and site owners where there is a potentially explosive atmosphere. This is the ATEX ‘User’ Directive, as enacted in the UK under the DSEAR Regulations. Some exclusions are stated in the DSEAR Regulations for the mining and quarrying industries to which the Mines and Quarries Act 1954 and the Quarries Regulations 1999 apply. However, some of the Regulations under DSEAR remain. It is recommended, therefore, that while DSEAR may not be mandated in full by regulation in the quarrying and mining industries, the avoidance of potential fires or explosions remains a priority under other legislation (including the Health and Safety at Work Act 1974). The use of ATEX-compliant equipment achieves a great deal in addressing this need.
While there has not been space in this article to explain the requirements of all the applicable regulations in full, clearly the onus is on both the end-users of equipment in potentially explosive atmospheres, and the manufacturers of equipment designed for use in potentially explosive atmospheres, to work together to achieve safety. The case of RFO heating systems illustrates this particularly clearly.
Acknowledgement
The author wishes to acknowledge the assistance of Benninghoven UK Ltd in the preparation of this article.
References
Baseefa website: www.baseefa.com
Guidance on ATEX is available from the HSE at: www.hse.gov.uk/electricity/atex/issues.htm
Guidance on DSEAR is available from the HSE at: www.hse.gov.uk/fireandexplosion/dsear/background.htm
EU guidance: ec.europa.eu/enterprise/atex/guide/index.htm
LETTER TO THE EDITOR
Heated Fuel Systems
Sir, — The October issue of Quarry Management contained an article written by Andrew Dickinson of Baseefa regarding the potential dangers from heated fuel systems, which I have to say alarms me.
Having worked in the oil industry for 43 years, and in the waste oil industry for 30 years, I believe the item is misleading, inaccurate and does nothing to promote the use of this type of fuel. Mr Dickinson appears to have received most of his information from a single manufacturer trying to promote its new heating system.
There are many companies who manufacture these types of systems (eg Midland Combustion, Ammann and M&Q, to name but three), and all produce quality systems that work within the permitted regulations.
Mr Dickinson also refers to RFO, which is a product that is no longer used within the roadstone industry, as only plants that meet the conditions of WID are allowed to do so. The generic term for the product that can be used is PFO and this is produced to a very tight interim specification, under guidance from the Environment Agency. Within the next few months this specification will be altered again once it has been agreed with the EU.
Mr Dickinson also states that the product is heated to temperatures of around 75°C, which is incorrect; the usual figure is around 45–50°C, although this may be increased slightly in winter months. Moreover, flashpoints are carefully monitored and any low-flashpoint material is put to one side for safe disposal.
There are now only around eight producers of this type of material, all of whom are members of the Oil Recycling Association, and I can assure QM readers that they all take a responsible view and produce fuel that meets the legal requirements.
Yours etc,
MICHAEL A. DICKIE,
Marketing Director, Eco Oil Ltd.
Baseefa response
Mr Dickie, — I am sorry that you felt that the article was misleading but, in my view, it is quite specifically related to RFO and I believe that in this respect the content represents the true situation. We wrote the article on the basis that we were then currently involved in a technical evaluation of a system which had been described to us as an RFO system and, therefore, had no reason to doubt that RFO was actually in use.
Clearly, from your own information, we conclude that the potential for mandating the use of PFO rather than RFO is fairly recent, as you say that the actual legislation is still awaited. We always write from a European perspective although, where relevant, mentioning the UK transposition of the European Directives.
Also, as part of our DSEAR services to users, we have been involved in inspecting three sites within the last year where the use of RFO or a similar material is an issue and where we have had to make recommendations to mitigate the risk. We must also bear in mind the recent incident involving a fire related to an RFO plant.
The safety record of equipment designed and manufactured to meet the ATEX Product Directive 94/9/EC, and correctly selected, installed, inspected, maintained and repaired in accordance with the ATEX User Directive 1999/92/EC, is enviable. Fires and explosions are almost always connected with incorrect installation or maintenance, but having the correct equipment to install is the start of the safety process.
If, as you say, PFO is carefully monitored to ensure a flashpoint well below ambient temperature, there still remains the issue of a high-pressure release leading to a mist, which can be ignited at temperatures well below the flashpoint. I am not in a position to comment on the probability of such a release for any particular bit of equipment, but until someone has actually completed this zoning exercise, it would be unwise to rule it out. It should not be forgotten that the mist element of the cloud at Buncefield was a major factor in causing so much destruction.
Yours etc,
RON SINCLAIR,
Managing Director, Baseefa.
Letter to Editor
Sir, – I am writing in response to the article ‘Potential Dangers from Heated Fuel Systems’ published in the October issue of QM, which I consider contains several statements that are misleading.
In recent years, regulation and regular monitoring by the Environment Agency and compliance with the European ‘Waste Incineration Directive’ have significantly improved the consistency and quality of RFO. Today’s RFO bears little comparison to that supplied prior to 2002 and is now known as either CFO or PFO. The oil is heated simply to reduce its viscosity, to bring it closer to that of gas oil and, hence, ensure clean and efficient combustion at the burner. Owing to the more stable properties of the fuel, it is only necessary to preheat the oil to a temperature of around 50–55ºC, not 75ºC as stated by the author. It would not be safe practice to preheat RFO to this temperature.
To consider the flash point of RFO, it is first necessary define the meaning of the term, ie ‘the temperature at which the fuel releases enough vapour to produce a vapour/air mixture that will ignite when a flame or other source of ignition is applied’. The mixture cannot and will not burn unless oxygen (in air) is present in sufficient quantity. In a typical RFO installation, the fuel is only in contact with air in the vented storage tank, where it is at ambient temperature, and when it leaves the burner nozzle, where it mixes with the combustion air and ignites to form a flame. The RFO heating system operates at a controlled pressure and is completely closed; no air is present within the pumping and heating equipment. Occasionally, and usually due to poor maintenance, a little air may enter the system but this is insufficient to support combustion.
The author creates more confusion with reference to ‘zones of use’. EU Directive 94/9/EC relating to ATEX certification came into force on 1 July 2003 and sets out the requirements for manufacturers of equipment and components intended for use in potentially explosive atmospheres of gas, dust, mist or vapour. The definition of a potentially explosive atmosphere is clearly stated in the interpretation of the ‘Dangerous Substances and Explosive Atmospheres Regulations’, 2002 (S.I. 2002 No. 2776) (DSEAR), as ‘a mixture under atmospheric conditions, of air and one or more dangerous substances in the form of gases, vapours, mists or dusts in which after ignition has occurred, combustion spreads to the entire mixture’ – in short, an explosion.
RFO systems are not installed to operate within potentially explosive atmospheres. If they were, and it would be folly to do so, than I would agree with the author that ATEX certification would be required. If we were to consider that a typical RFO pumping and heating installation on an asphalt plant is within a potentially explosive atmosphere, then ATEX certification would need to be extended to include the gas oil and binder storage systems, trace heating and other equipment, the burner controls and all electrically operated equipment etc installed in the immediate vicinity. There would also be also the problem of how prevent the naked burner flame from igniting the explosive mixture ingested via the combustion air intake. However, as RFO equipment is usually installed near to the burner, the immediate area is well ventilated by the large volumes of air induced into the dryer by the main exhaust fan.
The potential danger from pressure leaks releasing fuel vapour must also be recognized. This was the cause of the Buncefield tank farm incident in December 2005, which resulted from external ignition of vapourized motor spirit (flash point c. –40ºC) arising from a large spillage. The ignition source was not positively identified but may have occurred when the vapour cloud overflowed into an adjacent car park. A pressure leak from heated RFO will cool quite rapidly, thus preventing the formation of a vapour cloud.
Returning to the flash point, it is recognized that RFO sourced from used lubricating oil from internal combustion (IC) engines can contain a small amount of petrol or diesel fuel, which can reduce the flash point. The author suggests this ‘may be as low as 25ºC’, but does not support his claim. The H&S circular SPC/Technical/LD1-4/06 gives a lowest flash point of 32ºC when petrol constitutes 1.5% of RFO. The circular also defines the method of measuring the flash point. A large proportion of RFO is sourced from engines fuelled by diesel which has a flash point close to 70ºC. Paradoxically, most IC engines are designed and controlled to operate efficiently and safely at a temperature of 90ºC where the lubricating oil (containing a small proportion of fuel) is in contact with air via the sump breather. I suggest more work is required to substantiate this claim.
High flash points are usually resolved by the RFO supplier who samples the raw fuel and applies control methods to stabilize the fuel properties. This is good practice but should not encourage complacency, as oil in any form is highly combustible and, therefore, potentially dangerous. The basic techniques of a selecting a responsible fuel supplier, good housekeeping, and regular inspection and maintenance of the RFO installation and equipment are essential in preventing failure and hazardous incidents.
Yours etc,
TERRY HENSHAW FIQ.