New Bomags to be Hillhead highlights
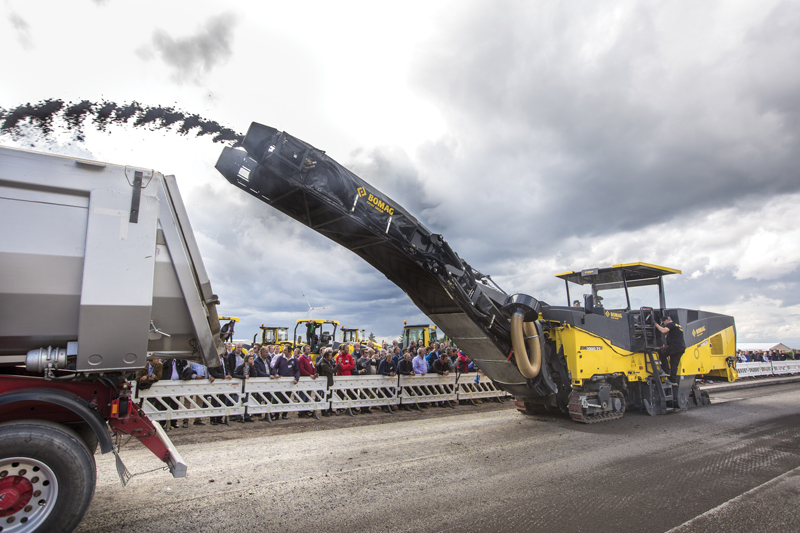
First published in the January 2016 issue of Quarry Management
Nick Johnson reports from Germany on new Bomag machines destined to make their UK exhibition debut at Hillhead 2016
Get ready for two good exhibitions this year. April will see the big Bauma show in Munich and two months later it will be Hillhead 2016. And already some of the major machine makers are revealing some of the new products they will be featuring.
Bomag are best known for their compaction products but their product portfolio also includes cold planers and asphalt pavers. And, during a customer event at their headquarters in Boppard, Germany, last autumn, the company showed the production version of its new 2.0m planer and the latest larger models in its Dash-5 series of self-propelled single-drum vibrating rollers.
The prototype of the new BM2000/75 planer was actually first seen at the Intermat exhibition in Paris last year. Now, after a rigorous test programme, the machine is in production at Boppard and will feature prominently on Bomag’s big Bauma stand. Subsequently, the planer will get its UK exhibition debut at Hillhead.
Planers and pavers joined the Bomag range after the company was bought by the Fayat Group 10 years ago. Fayat already owned the Italian company Marini and they now concentrate on asphalt plants with their pavers and planers being rebadged as Bomag.
To counter the dominance of their competitor Wirtgen in the world market for cold planers, Bomag decided to invest heavily in a new generation of machines in order to provide a good alternative. It put together a team of planer experts and gave them a clean sheet of paper to design a new range. After three years’ work they delivered the 1.0m milling width BM1000/35 (along with 1.2m and 1.3m versions) and now their next machine is the BM2000/75 with a 2.0m wide milling drum that cuts down to a maximum depth of 330mm.
BM2000/75 cold planer
The BM2000/75 tips the scales at between 32 and 37 tonnes and it rides on four extended-length crawler tracks to enhance traction and stability. The machine’s main engine is an emissions-compliant 552kW (750hp) Mercedes MTU engine. To provide back-up there is a small Hatz engine which can move the planer out of the cut in the event of a main engine failure. A secondary wiring loom is also provided as standard.
Other features of the new-generation BM2000/75 include a vibration-isolated operator’s compartment (with swivel seat), an integrated dust-extraction system, on-demand fans, a large water tank and a hydraulically folded front discharge conveyor (that swings through 120°). Particularly novel is the ability of the machine’s engine canopy to be angled down sideways to provide a safe working platform for service technicians.
To increase operational versatility, the BM2000/75 can be fitted with different milling drums. There is a choice of a standard drum with 162 cutting tools (picks), a fine milling drum with 274 tools or a Powerdrum with 124 cutting tools. Both the standard drum and Powerdrum can mill down to a maximum depth of 330mm, whilst the fine drum is for surface work down to 50mm.
As part of their new approach to cold planer design, the Bomag engineers revaluated the design of the milling drums, the positioning of the tool holders and the fixing of the cutting tools. Particular priority was given to maximizing cutting tool life and making it quicker and easier to replace a set of cutting tools.
The engineers devised a new interchangeable tool-holder system which has been designated the BMS 15. Claimed to reduce the time needed to change cutting tools by up to as much as a quarter, the cutting tools are easily fitted into the drum using the new design of tool holder.
Each cutting tool simply slots into the detachable top section of a tool holder that is secured by means of a single bolt. This bolt only needs a low torque setting of 100Nm. Once this bolt is removed, worn tools can be replaced quickly by tapping them out from behind ready for a replacement to be fitted.
The milling drums for the new-generation planers are made by Bomag in their new drum shop, which opened in 2013 at the Boppard factory. This 12,000m2 facility has doubled Bomag’s capability to make both planer and roller drums. It has rolling machines – that can shape steel plate up to 60mm thick – together with robot welders and dry turning machines.
There will also be a version of the BM2000/75 with a 2.2m wide milling drum that will be designated as the BM2220/75. As they ramp up production of their latest planers at Boppard, Bomag have stated that their goal is to become the clear number two in the global milling machine market by providing a credible, long-term alternative to the well-established market leader.
New Series-5 single-drum rollers
Meanwhile, Bomag are intent on maintaining their position as a leading maker of single-drum self-propelled vibrating rollers. To this end, they have now officially launched more new Series-5 machines. Fitted with the latest Stage IV low-emission engines, the newcomers have operating weights from 11 tonnes up to 26 tonnes. Whilst the lighter-weight Bomag single-drum rollers have Kubota engines with a DPF (diesel particulate filter), the larger rollers (over 11 tonnes) are Deutz powered and feature SCR (selective catalytic reduction) using AdBlue and a DPF. Despite the need for an AdBlue tank, the size of the main diesel tank has not been reduced.
The vast majority of the self-propelled single-drum vibrating rollers supplied by Bomag in the UK are the ‘high climb’ DH versions. Now fitted with a new Sauer double-pump hydraulic system, their gradeability is up to 60% to cope with steep batters.
The new Series-5 machines likely to be most popular in the UK are the BW213DH-5, BW216DH-5, BW219DH-5 and BW226DH-5. Each with a drum width of 2,130mm, they weigh between 12.72 tonnes and 26.71 tonnes. Most machines sold in the UK have smooth drums but padfoot drums and padfoot shells (which bolt over a smooth drum), as well as more specialized rock-crushing and high-impact polygonal drums, are also available.
All these new Series-5 single-drum rollers have electronically controlled engines with an Ecomode which is claimed to reduce fuel consumption by up to 30%, whilst delivering the same compaction performance. An optional Ecostop automatic engine shut-off function provides extra fuel savings whilst also reducing engine wear.
A big feature of all the new-generation Bomag single-drum rollers is their totally new cab that provides 30% more internal volume. Made in house at Boppard, this cab has a deeper back screen to provide better vision to the rear. There is a new, more user-friendly dashboard and other features include a clever-shaped, small-size, adjustable steering wheel and an optional rear-view camera.
The new Series-5 single-drum rollers have a sturdy, maintenance-free articulation joint and very neat, colour-coded electrical wiring. Usefully, in this increasingly technological age, they can be fitted with different compaction operation, control, measuring, indication and documenting systems. These include Variocontrol, the Terrameter and different levels of BCM (Bomag Compaction Management).
Control technology
The latest Variocontrol system for the models BW213-5, BW219-5 and BW226-5 has been made easier to use. Now, just one rotary switch integrated into the arm of the seat is needed for all Variocontrol settings. In manual mode, the operator chooses the required amplitude; in automatic mode, he can specify EVIB values and Variocontrol takes over control of the amplitude.
Variocontrol auto-matically ensures that energy is constantly transmitted at the optimum level. This prevents over-compaction and minimizes the number of passes required, which, in turn, increases productivity and the quality of compaction performance. A few Bomag Series-4 single-drum Bomag rollers in the UK have Variocontrol – notably some BW226DH machines on the Hinckley Point C nuclear power station site.
At the recent CPA (Construction Plant-hire Association) Conference, a speaker from Highways England highlighted the need to adopt ‘black box’ technology on machines in the future. This enlightened attitude to new technology should help hasten the greater adoption of intelligent compaction systems on this side of the Channel.
Another clear message from the CPA Conference was that more intelligent, remotely connected machines will increasingly be required as more sites fully embrace the digital age. So, roller buyers should now be evaluating the full capability of the clever systems that are available from companies such as Bomag.
Telematics can not only aid the contractor by allowing more efficient connected machine operation on site, but also bring management benefits to the roller owner. Bomag offer an add-on to their BCM 05 compaction measuring technology called BCM Net, which can relay real-time data from multiple rollers working together on a major compaction job.
Remotely knowing all about a machine and its operation offers tremendous benefits, but mixed-fleet operators have been frustrated by all the different telematics systems. Thankfully, a common application programming interface (API) has now been developed by the AEMP (Association of Equipment Management Professionals) in the US. Bomag are able to utilize this new interface, giving operators all the more reason to check out the new Series-5 rollers and all their smart technology at Hillhead 2016.
For more information visit: www.bomag.com
- Subscribe to Quarry Management, the monthly journal for the mineral products industry, to read articles before they appear on Agg-Net.com