Modified Bitumen For Road Paving
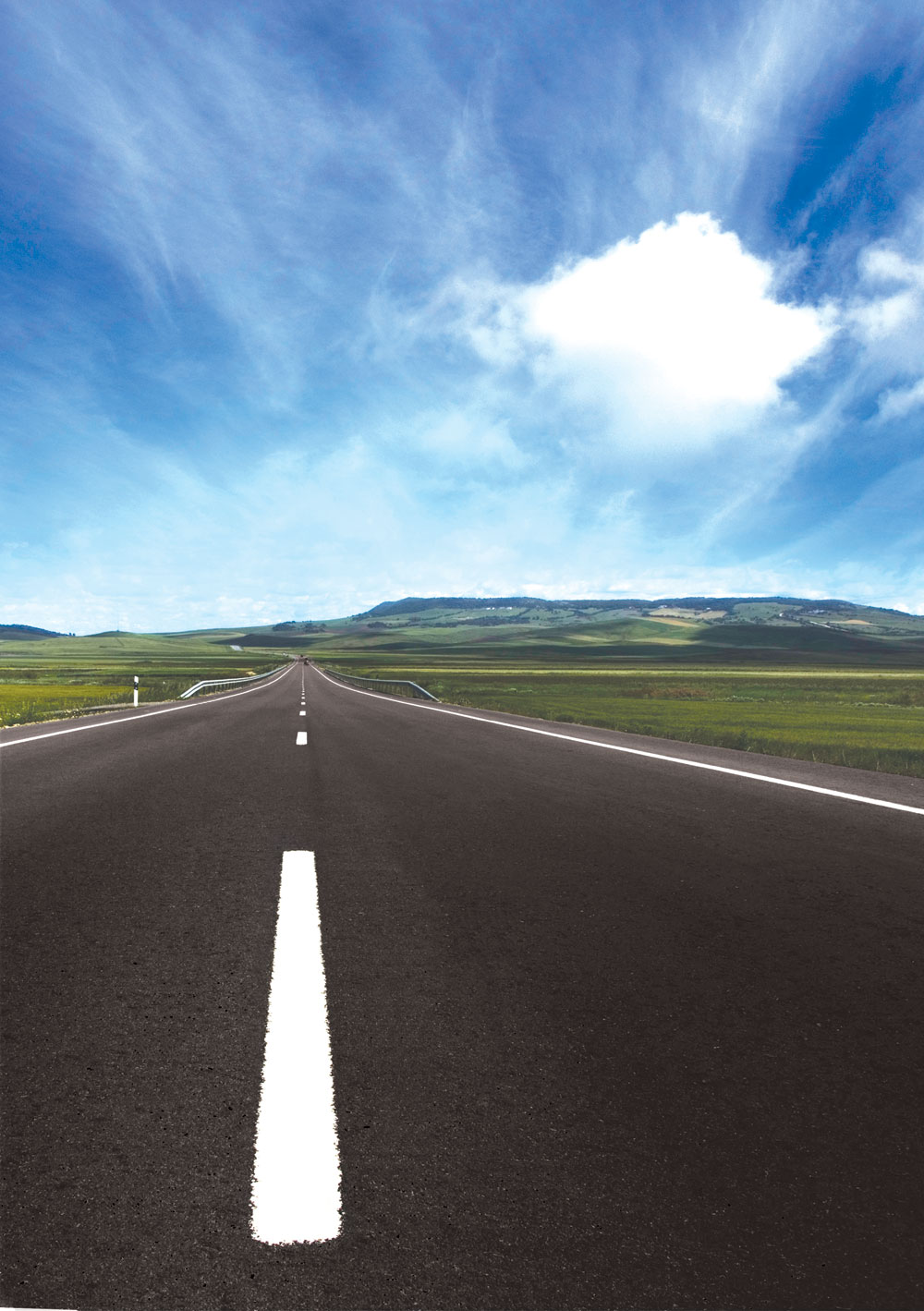
The performance and sustainability benefits
Polymer-modified bitumens (PMBs) are often hailed as the universal panacea to all pavement problems, but this is a fallacy in the same way that supercars are automatically considered the best cars in the world. PMBs will address many of the problems of the road but not all, just as a supercar is great on high-speed straights and corners but not as a family car for taking the children to school – the product must meet the requirements for which it is to be used.
In order to extract the maximum value out of any PMB, the lower layers of the road must be properly constructed, compacted and drained, and the traffic loading, climate and desired life of the pavement fully understood. Once all these factors have been ensured, the choice of PMB can then be made. In choosing a PMB, many clients/contractors ask the following:
- How can you claim that the use of PMBs is more sustainable?
- Why should I pay more for some products, are they not all the same?
- What has changed so that I now need to use a PMB rather than penetration grades?
- Have you any proof that PMBs provide the benefits you claim?
- If PMBs are so great, why are they not specified for all wearing courses?
- What is the next step after PMBs?
PMBs, such as the Shell Cariphalte range, are more sustainable in that, if they are properly designed into the overall structure, pavement life can be significantly extended, saving money in whole-life terms, reducing the amount of construction materials used, reducing energy consumption and reducing the number of vehicle movements associated with construction and maintenance (ie thinner structures and longer maintenance periods).
Added to this must be a consideration of which PMB to use, as they are not all the same. The PMB supplier must be able to clearly demonstrate which mechanical properties of the PMB, and therefore the asphalt, are improved by the modification. This necessitates the use of a PMB supplier who can demonstrate this type of information, provide technical support as required, develop fit-for-purpose solutions at short notice (there will always be occasions when the end application has not been designed for previously) and demonstrate a long track record. Shell, for example, have been supplying PMBs for over 30 years.
Proof that PMBs really work is always difficult to find, as it is rare that a modified and unmodified section of road are laid together so that they experience exactly the same conditions. However, recently the Asphalt Institute in the US produced a book entitled, ‘Quantifying the Effects of PMA (Polymer Modified Asphalt) for Reducing Pavement Distress’, which provides a lot of convincing independent evidence to this effect. Additionally, there are many instances around the world where PMBs have been used because other solutions have failed, and the PMBs have stood up to the onerous conditions.
The need for PMBs is increasing all the time in line with increasing traffic volumes, axle loads, tyre pressures and temperatures, all of which have a detrimental effect on the pavement, as well as with the environmental drive towards all industries being sustainable. In the long term, it is entirely feasible that there will be a move towards PMBs not just in all surface courses, but in all bound layers of the road to ensure maximum performance with minimum thickness and reduced disruption due to maintenance.
Today, the use of PMBs is becoming widespread, with developing nations using them to build their infrastructures and developed nations using them for maintenance. This leads to the question of what next? The next generation of PMBs adds functionality beyond improved mechanical properties; an example of this is Shell Cariphalte Fuel Resisting, a PMB designed to provide all the benefits of a traditional PMB, such as resistance to permanent deformation (rutting) and fatigue cracking, as well as significantly increased resistance to damage by fuel, which is particularly important in areas such as airports, where loose material, caused by a fuel spillage, could cause foreign-object damage to aircraft.
Beyond this next generation of multi-functional PMBs, Shell are beginning to ask what else can they make a road do beyond simply carrying goods and vehicles from A to B. The answer to this question forms the basis of the company’s extensive research and development programme for the next five years, and will involve more than 100 bitumen, asphalt and pavement experts working with Shell customers to find the sustainable solutions of tomorrow.
Shell Bitumen, Shell UK Oil Products Ltd, Rowlandsway House, Rowlandsway, Wythenshawe, Manchester M22 5SB; tel: (0870) 201 7777; fax: (0870) 201 8888