Driving Down Carbon On Recycled Roads
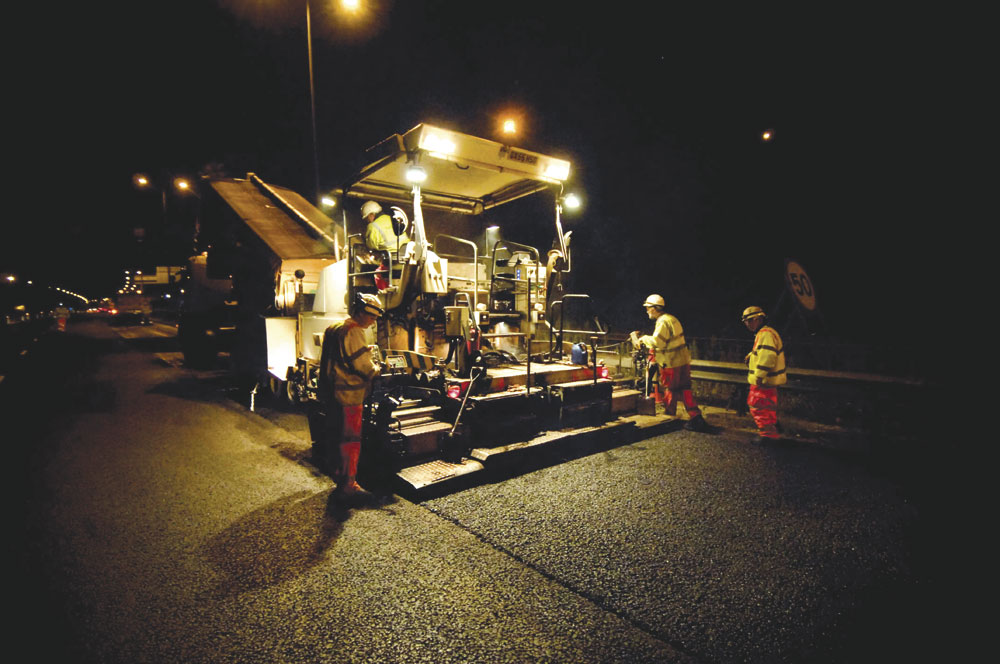
Delivering long-lasting roads and reducing environmental impacts
By Colin Loveday, Director of Technology and Quality at Tarmac
Highways industry efforts to cut the carbon emissions generated during the construction and resurfacing of UK roads often fail to tackle the real elephant in the room: embodied carbon in asphalt.
Material producers and contractors are bombarded with requests to report the same carbon information to different customers and clients in completely different formats, with different boundaries. Not only is this incredibly time-consuming, but, in the ensuing melee, it is possible for some of the bigger underlying principles to get lost among the bustle of turning off light bulbs and car sharing.
The highways industry, through the Mineral Products Association (MPA) and the Refined Bitumen Association (RBA), has been working with the major client bodies – such as the Highways Agency (HA) and ADEPT (a local authority Association of Directors of Environment, Economy, Planning and Transport) – in a collaborative project at the Transport Research Laboratory (TRL). This work has focused on developing a single footprinting protocol for asphalt that could be adapted for other pavement materials. This is called ‘asPECT’; the Asphalt Embodied Carbon Tool.
Embodied carbon (CO2e) in materials constitutes around 40% of the carbon footprint of road construction and maintenance. Recognizing this, the asphalt industry is working to standardize the calculation of asphalt-embodied carbon as the first step in systematically reducing it. While some of that reduction will come from new ‘low-carbon asphalts’, tackling the drying and heating energy consumption by switching to natural gas or adopting warm-mix technology, there are some simple ways in which big savings can be made.
Asphalt is made by combining around 95% dried and heated aggregate with around 5% liquid bitumen at a temperature of 150 to 170°C. Application of the asPECT embodied-carbon protocol involves calculating the carbon contribution of the following constituent key parts: the constituent production and transport; heating and drying; and mixing and delivery of the asphalt.
The biggest single factor in asphalt is the embodied carbon in the aggregate and binder, which comprises 44% of the total (see table 1). A major benefit of asphalt is that it can be 100% recycled into new asphalt, with the aggregate and binder being fully reused. Importantly, when the pavement or layer is eventually reconstructed, the asphalt can be recycled as asphalt, rather than being downgraded to an aggregate use. When this is done, the effect on the footprint of the new asphalt is that each 10% of reclaimed or recycled asphalt planings (RAP) added will save around 4% of total embodied carbon.
Tarmac’s latest plants are capable of incorporating RAP at 50% of the mix, giving a 20% carbon saving in a standard hot asphalt product. Moreover, that asphalt will still be recyclable at the end of the life of the road, giving further savings in the future. Managed properly, asphalt has the potential for a very long useful life, with multiple reincarnations of its constituent elements.
The second biggest factor that contributes to embodied carbon in asphalt is the heating and drying of the aggregate, which comprises 42% of the total. Various techniques are available to lower the mixing temperature, which reduces the carbon emission from the fuel consumption of the burner in the dryer. The savings that can be made in this way, while still ensuring a durable mixture, will be of the same order as for RAP.
The most important overall factor when looking at carbon in roads is consideration of the asphalt’s whole lifecycle of use, rather than just a simplistic initial ‘carbon today’ figure.
There is a particular danger, in this era of austerity and spending cuts, that measures to reduce cost will have a negative impact on the durability of road construction and maintenance. If this is allowed to happen, it will also increase the carbon impact of roads in the long term. If an asphalt with 50kg CO2e/tonne lasts in the road for 20 years, its effective footprint is 2.5kg CO2e/tonne/year. If, however, more care is taken and all best practice is adopted to extend the life to 40 years, this drops to 1.25kg CO2e/tonne/year. By ensuring that the asphalt is recycled at the end of use, this drops again to 0.7kg CO2e/tonne/year.
Extending the lifecycle of asphalt is not difficult, and not generally prohibitively expensive. The necessary measures are described in the recent TRL publication ‘Road Note 42’, which was prepared with input from across the asphalt sector. The connection has to be made that durable, long-life roads are generally carbon friendly and transient solutions are generally not.
Thus, alongside the evaluation of low-temperature asphalts, we should really be looking for low-carbon asphalts or rather low-carbon roads.
Recycling has a bigger part to play in the long-term carbon reduction of asphalt and roads than is often appreciated (see table 2). The UK has a mature road network, but within that asset, as a rough estimate, there must be in the order of 2 billion tonnes of asphalt. The carbon involved in the production of the bitumen and aggregate in that asphalt has already been expended. It would be a crime if that were allowed to go to waste.
In future maintenance of this road asset, plans must be made to rework the pool of embodied carbon, both to reduce the immediate carbon footprint and also to extend the life of the asset as far as possible. Realistically, that means systematic structural renewal of pavements over time to allow that reworking.
Until now, using RAP when resurfacing has been confined to sporadic ‘best practice’ projects. However, there is now genuine proof that high levels of RAP can be achieved in surface courses, at normal specifications of quality and safety. Last year, Tarmac set a new benchmark on an M25 resurfacing project, which saw the highest ever percentage (40%) of the surface course constituted by RAP.
Looking to the future, consistently higher percentages of roads recycling look set to become the norm, as they already have in some other European countries. Recycling and low temperatures are not the only routes to tackle embodied carbon. Designing roads to offer greater durability and extended life also must sit alongside. The premise for this is simple: doubling the life of any road will naturally halve resource consumption and carbon emissions. This is a challenging prospect at a time when all talk is of austerity, cuts and short-term expediency. It would be a shame if the green baby were thrown out with the bathwater of the recession.
The lifecycle carbon footprint of roads, their long-term durability and the importance of reusing existing materials when they do need to be resurfaced are inextricably linked. A move away from looking at these carbon-related elements in isolation will deliver longer-lasting roads, cut carbon and reduce their environmental impact.